Media | Articles
The Fire Wrench
Last week I promised (threatened?) to write about removal of the mousy heater box from newly purchased 1969 Lotus Elan +2. I’m not quite finished, so instead we’re going to talk about something near and dear to my heart but misunderstood—why you sometimes need to use a torch to remove stuck bolts, and why that method works.
The 2008 Nissan Armada I bought last December had sat unregistered for about a year before I bought it. Cars that sit outside have rust form on the surfaces of the brake rotors. If a vehicle hasn’t sat too long, hitting the brakes hard a few times typically wipes the rust off, but if it had a long period of disuse, there’s often an area of deposits where the pads were stuck to the rotors. Like the surface rust, these may completely wipe off with repeated braking, but if they don’t, it creates a pulsing brake pedal, and, if the deposits are on the front rotors, a shuddering steering wheel. These same symptoms are also said to be caused by “warped rotors.” We can get into a technical debate on whether brake rotors on street cars ever actually “warp” from heat, or whether pedal pulsation is always due to deposits on the rotors, or by the rotors not being installed on a clean, flat hub face. Nonetheless, the solution is the same—replace the rotors and make sure the hub face is clean when they’re installed.
Of course, I didn’t replace them when I bought the Armada, as it was so needy that the functioning but pulsating brakes fell to the bottom of the punch list. However, after using the truck to tow home the needy BMW E30 in August and the Lotus in October, it became clear to me that I was pushing the boundaries of sanity. I bought a set of Detroit Axle front and rear rotors and pads on eBay that, with both a coupon and an offer sent by the seller/manufacturer, came to the ridiculously low price of $234 shipped. I pity the FedEx driver who had to deliver the 101-pound package the last 20 feet. My 66-year-old back and I unpacked the box and moved its contents one rotor at a time.
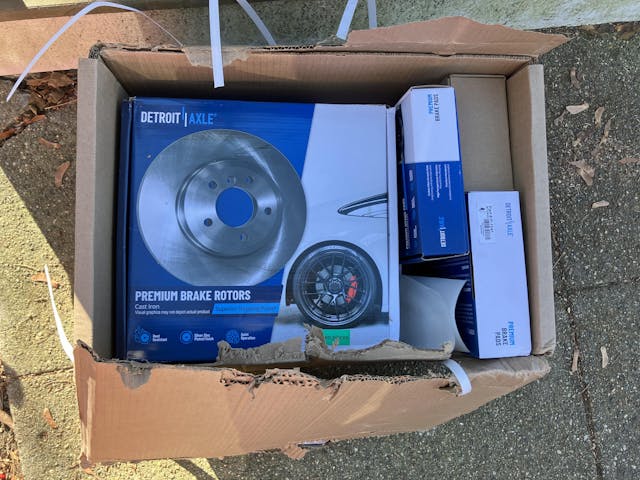
As I’ve written before, working on the Armada is challenging. It doesn’t wholly fit in my garage unless I kick two other cars outside, and I couldn’t do that as I’d already begun tearing the Lotus Elan apart. I saw that we had a few days of 60-degree weather coming up, so I staged the car in the driveway using aluminum sheets under both the floor jack and the stands so they didn’t sink into the asphalt.
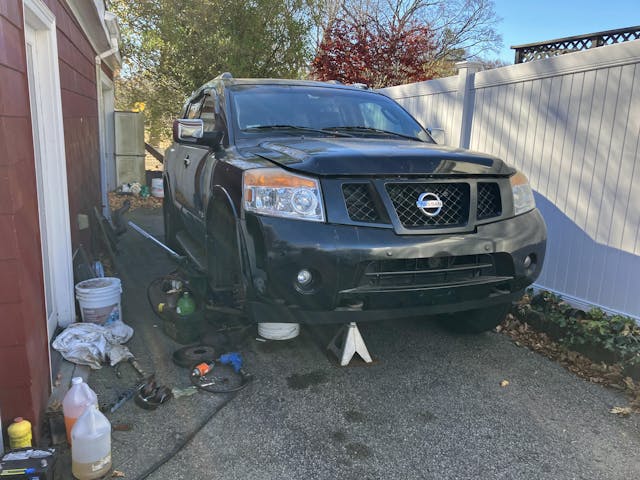
Like most modern cars, the Armada has “floating” calipers that slide on a bracket. The bracket is attached to the steering knuckle with beefy bolts and doesn’t need to come off unless the rotor needs to be replaced. The caliper is bolted to the bracket with smaller bolts that slide in rubber bellows. This setup enables the caliper to have its piston(s) on only one side, and for the brake pads to be replaced fairly easily. Since I was replacing pads and rotors, the bracket had to be removed, so I fired up my compressor, stretched the air hose out to the driveway, snapped the 18mm six-point Snap-On impact socket (a set of half-inch impact sockets is one of only two Snap-On tools I own) onto the impact wrench, and did the whacketa-whacketa thing on the first bolt. The joy of owning an impact wrench is hearing that sound quickly transition into whacketa-whacketa-WHEEE as the bolt spins out.
Marketplace
Buy and sell classics with confidence
Except it didn’t. I tried the second bolt—same thing. I waited until the compressor cycled so its pressure was at a maximum and tried it again. No WHEEE. On a caliper bolt. It was surprising; even up here in the rust belt, I don’t think of caliper bolts as rusty, never-have-been-removed troublemakers like, say, control arm bolts.
Now, my Craftsman 2.5-hp, 20-gallon compressor is older than my firstborn child, and he’s 36. It probably hasn’t had its oil changed in several presidential administrations, and like myself, it doesn’t put out the force that it once did. With regard to stuck bolts, that’s actually not a bad thing. You can always put a four-foot pipe on the end of a wrench or breaker bar to deliver big torque to a stuck fastener, but when you do that, you run the risk of snapping off the fastener. Having the compressor and impact wrench torque-limited (in my case, by the compressor’s age) can actually be a valuable safety gate on the whole “any 15-minute repair is one broken bolt away from being an eight-hour ordeal” thing. But even with this quasi-intentional limit and the high-quality Snap-On six-sided impact socket, I could see that the corners on the bolt were beginning to round off.
It occurred to me that it was possible that the bracket bolts were installed at the factory with Loctite on the threads. I checked on the Armada forum, found that this was true, and saw numerous posts of people who’d descended into the hell of rounded-off corners or snapped-off bolt heads.
There’s a chapter on dealing with stuck fasteners in my first book. Hopefully by now you know that WD40 is a light lubricant, not a penetrating oil, and it is never going to loosen any badly stuck fastener. I like SiliKroil and/or wax. Others use PB Blaster or a mix of acetone and transmission fluid. But any kind of penetrating oil has to be able to get into the threads, and in the case of the bracket bolts, the threads were inaccessible.
In a larger context, when I encounter a situation like this, I stop and get some Hack Mechanic situational awareness. That is, I look at how bad the situation will be if I snap off a bolt. If the bolt goes into some other inexpensive and easily replaceable part, or if you know that the other part is junk anyway, as it often is when replacing exhausts, sometimes the thing to do is just go for it; but if you know you’ll deeply regret it when you feel that sickening sensation of having the bolt twist but not hearing the threads crack (which indicates that it’s snapped rather than unthreaded), the thing to do is preemptively go for the heat. A small propane torch usually isn’t hot enough. MAPP gas can get small fasteners cherry-red. But for big stuck fasteners, you need an oxy-acetylene torch. Or as it’s affectionately known in the repair world, The Fire Wrench.
You’ve all likely seen this meme:
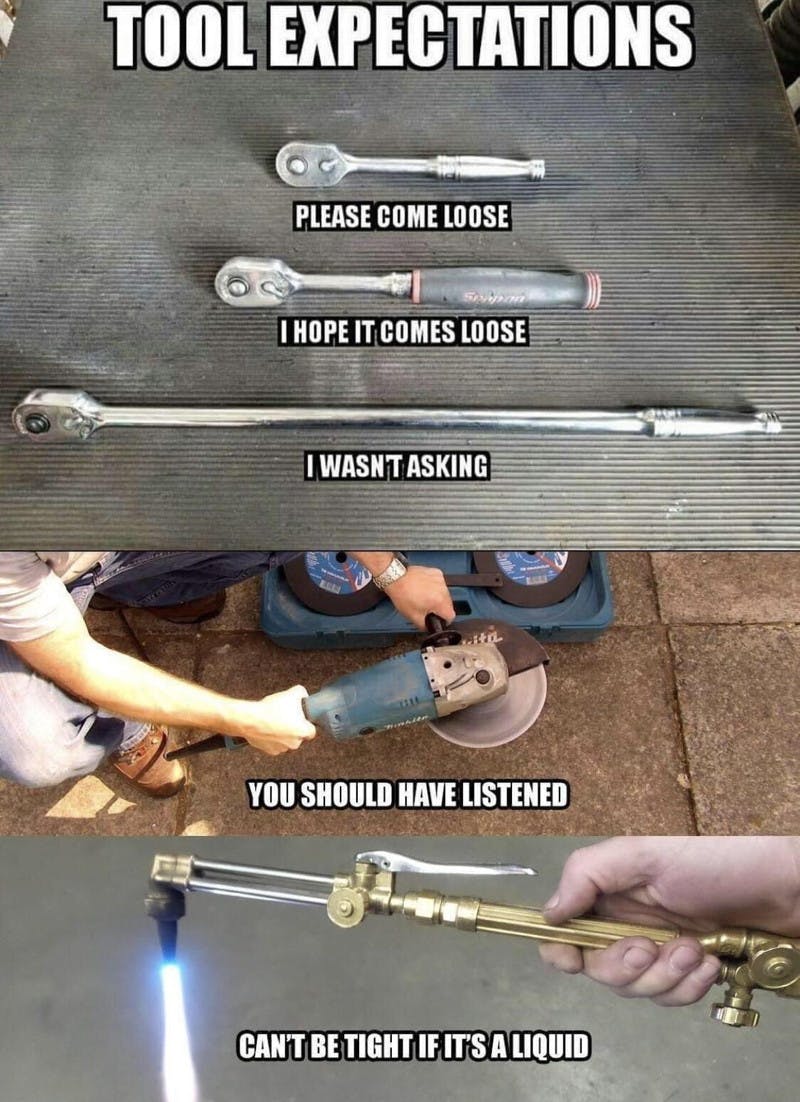
While it’s funny, the meme is more than a bit misleading. The torch attachment shown in the meme has a lever on it, which means it’s a blowtorch, which is meant for cutting metal by melting it. When faced with a stuck fastener, you don’t usually want to melt metal, and if you melt it in the wrong way, you’ll cry.
Let me back up. There are three different truths that can come into play when you apply heat to a stuck fastener. The one that’s most often referred to is that metal expands when it’s heated, so if you have a nut on a stud, you heat the nut to release the death grip it has on the threads of the stud. Similarly, if you’re trying to remove a stud from an engine block or head, you should heat the area around the stud, not the stud itself. You can do your own research on the different expansion rates of iron, steel, and aluminum to judge whether or not you think that this is the primary mechanism by which heat unsticks things.
Personally, I’m a bigger believer in the second truth—that heat helps break the bond of corrosion or other binding factors in the threads. In the case of my caliper bracket bolts that were Loctited at the factory, that’s exactly why I wanted heat. I wanted to literally melt the old Loctite.
To be absolutely clear, when you break out the torch, you don’t really care what percentage of the loosening is expansion of metal versus what portion is corrosion-breaking or Loctite-melting. It’s largely an academic question. If you’re dealing with a nut on a stud or bolt, you heat the nut up cherry-red, it comes off easily, and you’re thrilled. (Although, if you’re removing a stud, I’d still concentrate the heat at the area around the base rather than heating the top of the stud.)
But the third truth— the “can’t be tight if it’s a liquid” thing—is different, and it’s something you need to be very careful about. This approach is totally the right one if you have a stud with splines on the sides that are an interference fit into a hole in a flange on something like an exhaust manifold that holds a headpipe or catalytic converter, and the threaded top of the bolt has snapped off. Heat that remaining little stub until it’s as orange and malleable as lava, then smack it with a punch. It acts like it’s Play-Doh, deforms in the middle, shrinks a bit in diameter, and pops out. It’s awesome. You’re never so happy to own a tool in your life.
The Armada’s caliper bracket bolt is about two inches long. Its cap was easily accessible, but that wasn’t the part that was seized. About an inch of the bolt goes through a non-threaded hole in the steering knuckle. That wasn’t the seized part, either. It was the remaining inch that was threaded into the bracket. In this situation, heating the cap of the bolt to near-melting temperature would be the worst thing you could do, because when you put torque on it, it’s just going to twist off like warm taffy and leave the part that’s stuck in the threads.
The other thing about The Fire Wrench you need to be aware of is that an oxy-acetylene torch is not a scalpel. The flame tongue is about eight inches long. It is very easy to melt nearby wires or rubber boots, or to cook the grease out of bearings. Ask me how I know.
So, with all that explained, you can see that the thing to do was to use the torch to heat not the bolt cap but the part of the bracket into which the bolt was threaded. Multiple heatings and test whacketas with the impact wrench were required, but eventually the bolts began to budge. Once there were some exposed threads, I goosed them with SiliKroil, waited a few minutes, then whacketa-WHEEE’d the bolts all the way out.
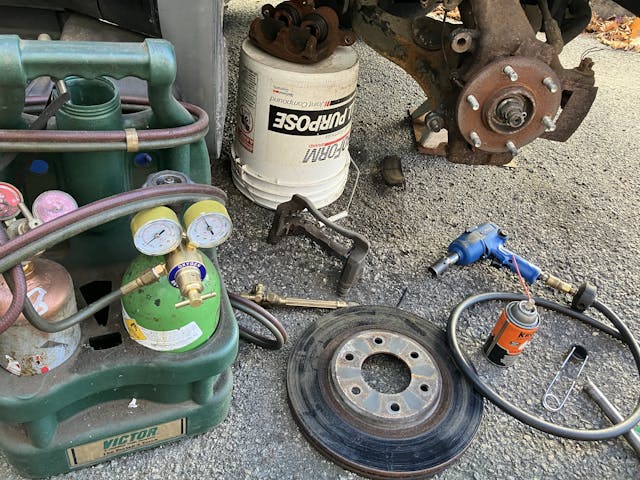

With the bolts out, I could see how rounded the corners of the caps had gotten, even with the use of heat and a high-quality six-pointed socket. I’d never had anything even close to this happen on the vintage BMWs I usually work on—I re-use those caliper bolts without a second thought. With the Armada’s, I didn’t feel right putting them back in. And it wasn’t an altruistic “do the right thing for the next owner” thing—it was an entirely self-interested desire to not get shot at some later point by the bullet I’d just dodged.
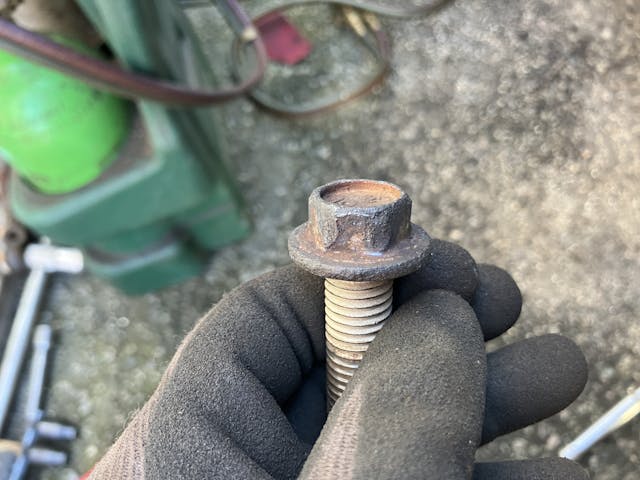
Sourcing replacement caliper bolts was surprisingly challenging. I couldn’t find them in the online Nissan parts diagrams, and the part numbers listed on the Armada forum seemed to be for bolts for the heat shield, not the caliper bracket. I normally don’t pay as much attention to bolt grade as I probably should and usually would substitute any available M14x2.0 bolt that’s about the same length. Last week I mentioned doing exactly that for a caliper bolt on the Lotus Elan +2, but that’s a featherweight car. The Armada is a 5600-pound truck that I use to tow. I wanted the correct grade 10.9 flared-head bolts. Fortunately, my local True Value hardware store has a fabulous selection of fasteners, including these. They were $5.80 each, and I was glad to pay it.
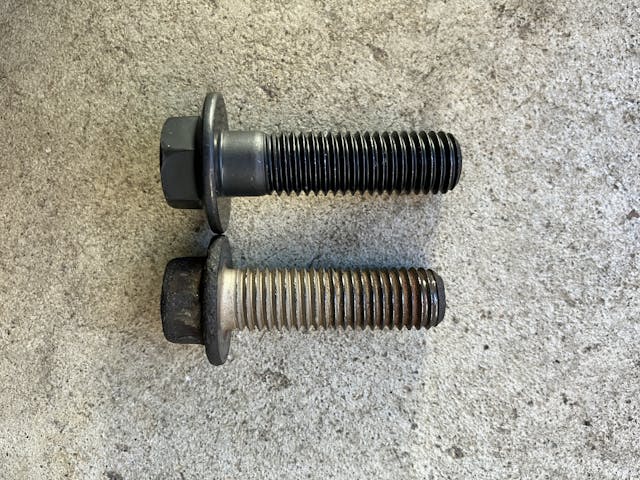

The Armada now stops great and doesn’t shudder while doing so, and The Fire Wrench was an absolutely indispensable part of the repair. But not because it liquified metal—because it liquified Loctite and broke the bond of corrosion.
There. I fixed the last part of the meme.
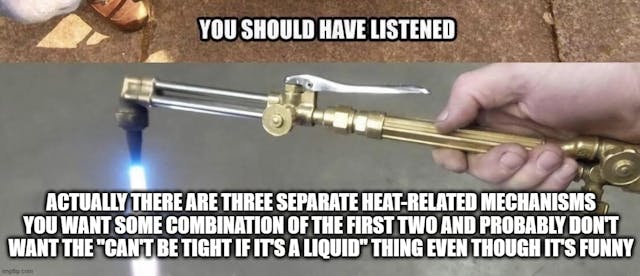
***
Rob’s latest book, The Best Of The Hack Mechanic™: 35 years of hacks, kluges, and assorted automotive mayhem, is available on Amazon here. His other seven books are available here on Amazon, or you can order personally inscribed copies from Rob’s website, www.robsiegel.com.
Also the Blue Knife.
The horribly rounded hex on that bolt sure looks like from the wrong socket size, or one of those gimmicky sockets with rounded corners that’s supposed to work on the flats.
I wasn’t going to add this but the Semantic Man in me won out, so I apologize in advance: they’re not flare bolts, but flange bolts.
You are correct on “flange.” Not sure why my brain plucked out the wrong word there. Socket was a correctly-sized six-point Snap-on socket.
A related trick is using an arc welder to heat the bolt by “sticking” the electrode to the bolt and the ground to the offending nut,bracket,block etc. The current heats the bolt and since resistance = heat, the heat is concentrated in the mating surfaces. Beware of stray currents and delicate electronics,,,,
Every week you describe my life with incredible accuracy.
When I worked at Bankhead Welding, the torch shown in the photo was called a “cutting torch.” A blowtorch is a different animal.
You have TWO Loti and you’re just now pushing the boundaries of sanity?
I recently bought new tires for my 14 year old pickup truck. Having them installed at the tire store is akin to taking a family member to a surgeon in a low rent strip mall. They were unable to remove the six lugnuts of the right rear wheel. None of their impact guns would do it, and the “lead technician” with a torque wrench as a breaker bar( I’m not making this up) couldn’t remove them either. I wound up taking my truck home with 3 new and 1 old tire. My impact gun never let me down on any project, but it too failed. I broke out my new 1/2″ Milwaukee battery impact, a 4 pound maul, and got to work. I put the proper size deep well impact socket on the lugnut, and whaled on it with the maul. Think of hitting the end of the socket as if you’re driving a nail. 45 minutes of this, and believe it or not, that battery powered impact gun broke all six lugs loose. There wasn’t a rust issue, the truck has aluminum wheels and those nice stainless looking lugnuts. It was a phenomenon of the steel lugnut fusing into the aluminum not so much with corrosion, but somehow frictionally. I had to buy new lugnuts, but I did go back to get my last tire installed.
And this was a national tire store by the way, you would have to add up the ages of 3 of their techs to equal my age. I’m 56.
Two more thoughts on the article, one- there is NEVER a reason to use loctite on the small bolts that attach the caliper to the caliper bracket. The bolts do not provide any service other than keeping the caliper from falling off the car. The way the caliper fits into the bracket is what absorbs the rotational stresses of vehicle braking.
Two: those bolts that you struggled to remove looked like they had maybe been previously damaged by someone trying to remove them with perhaps the wrong size socket?
Amen to both points.
Sorry but the cheap rotors will warp pretty quickly especially if you have to panic stop once or twice. Back in the day you could bring “good” rotors to a garage to be “turned” for a fraction of the cost of new.