Media | Articles
The Exhaust Problem (Part 2)
Last week, I wrote about discovering that the exhaust in my just-purchased 182,000-mile 2008 Nissan Armada was leaking in three places—large leaks from a laughably bad weld between the tailpipe and the muffler and from the seam on the top of the muffler, and a small leak at the rear flange of one of the four catalytic converters. I shoveled muffler putty into and around the first two leaks, ignored the third, took it in for inspection, and failed. So now, instead of a useful vehicle, I had a big red “R” sticker on the windshield that could land me a moving violation and add points on my license, and an exhaust whose proper repair was the definition of a slippery slope. Great. Just great.
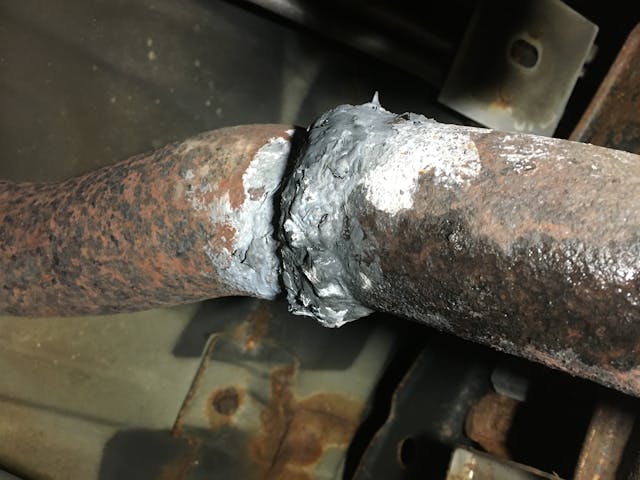
In addition to the specifics of the vehicle and its exhaust, there’s, well, me. I’ve long said that I have no idea how anyone can afford to own any older high-mileage car, much less a vintage car, if they need to pay someone to fix it. Multiply that by 13 for the number of vehicles I own (shut up), and you can see why none of the cars I own ever gets everything it needs. The day I stop doing all my own work is the day I decide that I need to shed vehicles. Although that day is not today or next week, this is getting more challenging as I get older. I still think of myself as 25 years old, but I turned 65 last summer, have back issues that get triggered by lifting and bending, and have a garage situation where the Armada appeared to be too big to fit without kicking out not one but two of my cars. I do have a mid-rise lift in the garage, but the Armada’s weight is close to the lift’s 6000-pound limit, it’s so wide that I don’t think the swing arms will even reach the jack points on the sills, and the geometry of the truck and the lift make it challenging to get the jack pads somewhere more inboard, like the under frame. For these reasons, any under-truck work likely needs to be done on the garage floor, and even then, figuring out how to get the truck in there so I could close the door and turn the heat on and not freeze my old bones was challenging.
My 38-year-owned ’73 BMW 3.0CSi, 1999 M Coupe, and 49,000-mile ’73 2002 are here in the garage over the winter, with four other vintage BMWs and the Lotus in warehouse storage. The CSi is the definition of a pampered car. With its Karmann-built body, it is never going to sit outside (to repeat the best automotive joke in the world: Karmann invented rust, then licensed the process to the Italians). In contrast, the M Coupe is a modern car that can sit in the driveway for weeks if necessary. The low-mileage 2002 is somewhere between the two. I don’t necessarily think it’s an act of violence to move it outside for a few days, but if the weather turns and it sits in rain or snow while I’ve taken the Armada “down” and rendered it immobile while waiting for parts, I will have made the wrong call.
My garage is 31-feet long, so it easily fits two small cars nose-to-tail. After I bought the mid-rise lift, I discovered that an unintended benefit is that I can put a car on it, lift it, and be able to tuck the nose of another car under it. I didn’t think that would work with the Armada, as its nose is tall enough that I’d need to raise the 2002 so high that I was concerned I’d dent the roof against the ceiling. Plus, a while back I found that one of the lift’s hydraulic cylinders leaks when raising it to the upper position.
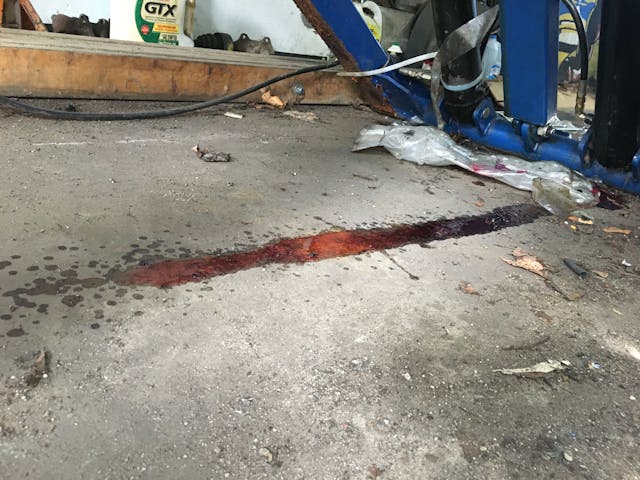
I went for it anyway. The cylinder shot out a stream of red fluid, but it got to where I could lower it into the lock-stopped upper position. Hopefully come spring I’ll be able to get the 2002 back down.
Marketplace
Buy and sell classics with confidence
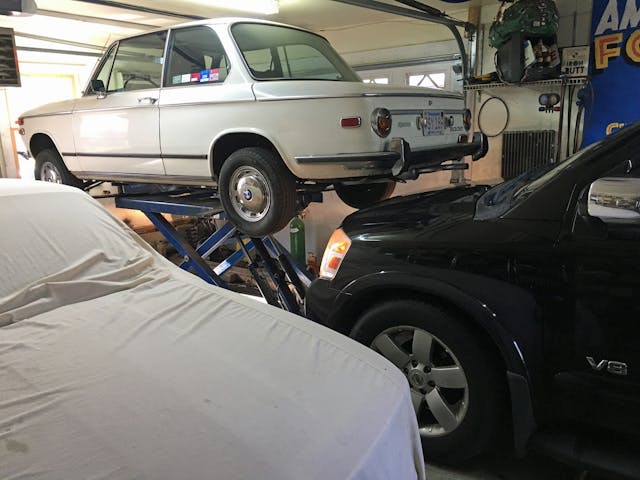
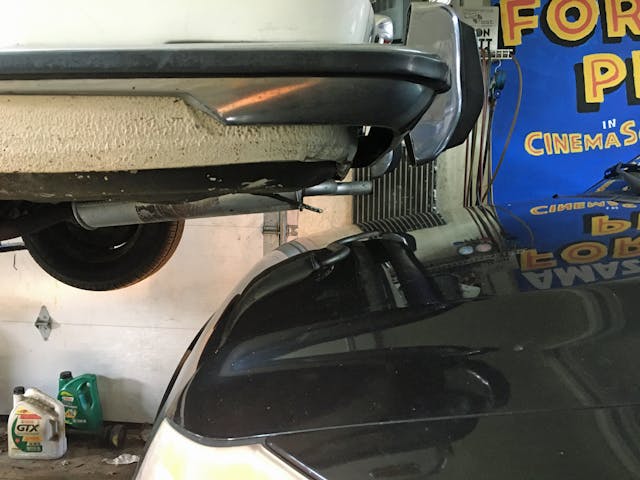
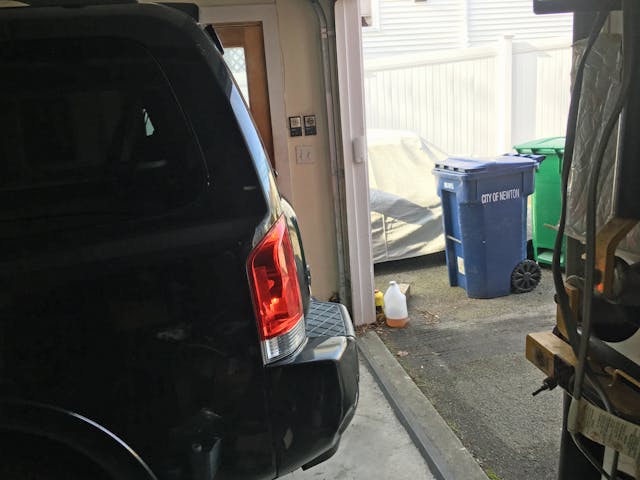
So, I had the truck inside the heated garage. I could lift the back end if I needed to, but I had no room to lift the nose. This meant that I could get to the tailpipe, maybe the muffler, but I wouldn’t be able to access the slightly-leaky flange behind the right-hand secondary cat.
I looked on RockAuto and found that there were three aftermarket cat-back exhausts, each less than $200 delivered. One was an ANSA that had an OEM-style muffler with long inlet tubes, one of which bolted directly to the leaky flange.

The other two exhausts—AP (which apparently now owns ANSA) and Walker—both had a muffler with short inlets that are meant to be clamped or welded to intermediate pipes. The Walker was appealing because it’s stainless, but reviews on Amazon reported that it uses 2-inch pipes rather than the stock 2.25-inch, requiring adapters if you want to try to splice a new muffler into the existing pipes. The AP exhaust appeared to have 2.25-inch muffler inlets, however.

I began to formulate an approach—order an AP muffler and tailpipe, cut the old muffler off with a Sawzall, and splice the new one to the existing pipes with butt-joint-style band clamps. If it worked (meaning if it sealed well enough to pass inspection), done (at least for now), but if it didn’t, I could still order the other pieces of the AP exhaust kit and replace everything behind the cats, and a cost comparison showed that there wasn’t a big discount buying the whole exhaust kit as opposed to ordering the pieces a la carte anyway. If the paper-thin leaky cat flange self-destructed when I tried to take it apart, then I’d need to replace the cat, which was another $125. Hopefully the joint between the primary and secondary cats would cooperate.
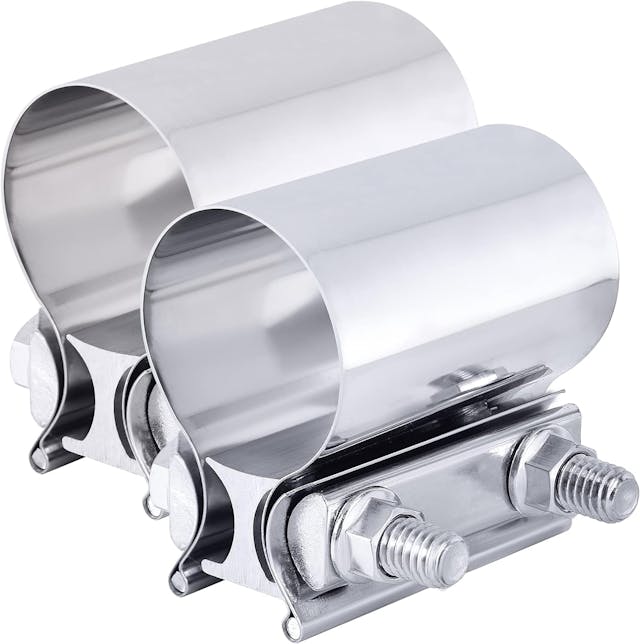
Before I ordered parts, I wanted to see if this repair could be accomplished with the Armada shoehorned in the garage the way it was. I took my Sawzall, shimmied under the back of the truck, tried to get to the front of the muffler where I’d need to cut the pipes, and found that there wasn’t enough clearance to do it. I’d need to raise the front of the Armada, and there was no way to do that with it stuffed under the tail of the 2002 on the lift. I’d either have to take the 2002 down and give the Armada the entire right side of the garage, or do the repair with the Armada’s butt hanging out of the garage, leaving the place open to the elements.
I checked the weather. There was a Nor’easter predicted to drop about 10 inches of snow two days hence.
Dukes.
I thought about it carefully, and realized that I hadn’t tried to find the exact reason why the exhaust had failed inspection. I clamped a rubber glove back over the tailpipe, started the truck, and did my best to feel along the exhaust for leaks. To my surprise, my patch along the upper seam of the muffler appeared to be holding. The leak from the cat flange was minor. The motherlode was coming from my unsuccessful attempt to seal up the booged weld attaching the tailpipe to the muffler. I was unable to fix it with the soup-can-and-hose-clamps method because the weld (and my putty) created a gall like a walnut inside a garden hose, around which a clamped can had zero hope of sealing.
I thought “What if I cut the lump out with a Sawzall? Couldn’t I then just mate the two sections with a butt-joint band clamp like I was planning on doing to the muffler?”
Hmmmmn.
I crawled under the rear of the car again with the Sawzall. But this time I found that, unlike the front of the muffler, there was ample space to get the Sawzall positioned on the tailpipe, as it was located up in the recess where the spare tire is.
I used my vernier calipers to take some careful measurements of the pipes so I could order the correct band clamp and laughed out loud when I found that the outlet pipe of the muffler was 2.25 inches, but the tailpipe was 2.5. No wonder the thing didn’t seal.
So what I needed wasn’t a butt-joint clamp. I needed a 2.5-to-2.25-inch reducer adapter.
Mindful of the impending Nor’easter and really wanting to get the repair completed before a foot of snow stranded the Armada inside the garage, I drove to five local auto parts stores, but none of them had a 2.5-to-2.25-inch reducer. I looked on Amazon, found one that appeared to fit the bill (2.5-inch inner diameter to 2.25-inch outer diameter) with next-day delivery, clicked, and waited. In the interim, I cut the “walnut” out of the exhaust pipe. It was laughable how misaligned the two different-sized pieces were.
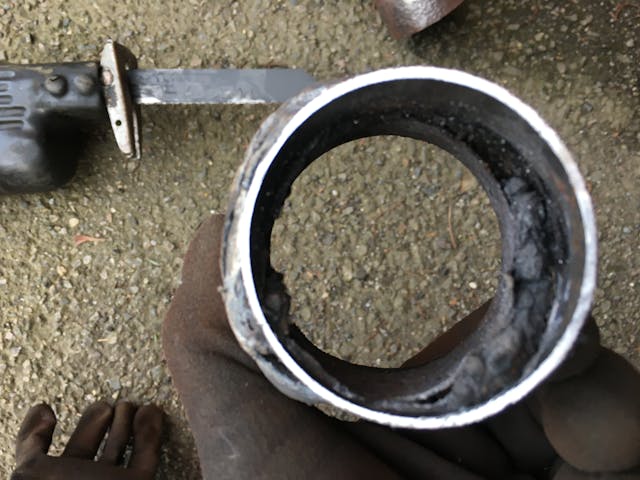
The reducer arrived at about 7 p.m. the night before the snowstorm was predicted to hit. I’d already wire-brushed and sanded the cut ends of the muffler and tailpipe, so I thought all I needed to do was goop up the reducer with muffler cement, slide it on, and clamp it down, but I found that while the 2.5-inch end fit the tailpipe perfectly, the 2.25-inch end was not an inner-diameter fit to the back of the muffler—it was exactly the same size as the back of the muffler. I hightailed it to the O’Reilly Auto Parts a few miles from me before closing time and grabbed a 2.25-to-2.25 adapter and another clamp.
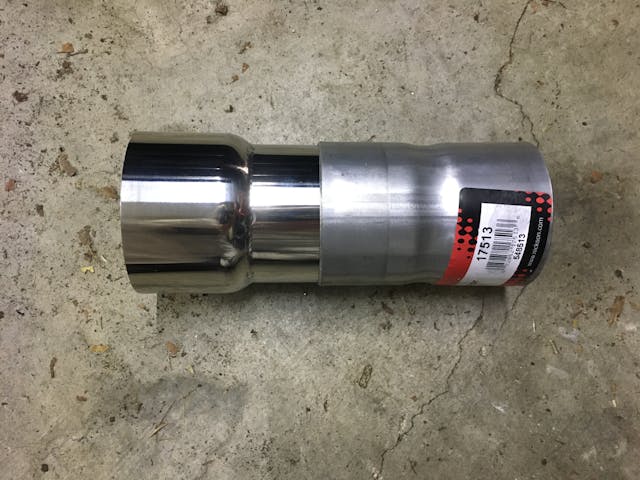
I emptied a good portion of a tube of J-B Weld muffler cement into the three slip-in joints, clamped everything down, backed the truck out of the garage, and drove the M Coupe back in. I had beaten the impending snowstorm, but when I’d be able to get the truck inspected remained to be seen. I also was well aware that between the adapters, the clamps, and the muffler cement, I’d just dropped 50 bucks on a very, um, hacky solution when $200 would’ve bought me something permanent.
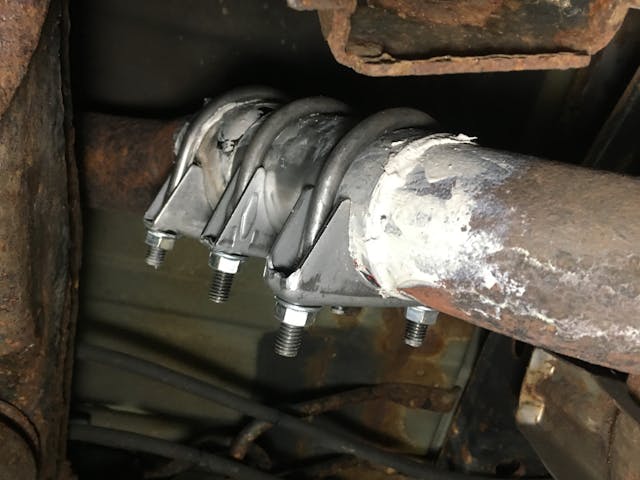
In the morning, I was surprised to find that the big Nor’Easter had fizzled. Overnight the meteorologists had massively rolled back the snow prediction. I looked out the window and saw only rain. I started the truck, put a gloved hand over the tailpipe, the exhaust felt tight to me, so I beat it on down to get it re-inspected. As this was a re-test for a failure due to an exhaust leak, I heard them rev it up and down several times as they checked, but it passed.

I have little doubt that I’ll probably need to do a more proper stem-to-stern exhaust replacement sooner rather than later, but damn it’s awfully satisfying to dig the ice axe and the crampons in and say, “Slippery slope? Not today.”
***
Rob’s latest book, The Best Of The Hack Mechanic™: 35 years of hacks, kluges, and assorted automotive mayhem is available on Amazon here. His other seven books are available here on Amazon, or you can order personally-inscribed copies from Rob’s website, www.robsiegel.com.
Check out the Hagerty Media homepage so you don’t miss a single story, or better yet, bookmark it. To get our best stories delivered right to your inbox, subscribe to our newsletters.
Rob – I would have thought that a yard or two of muffler bandage would have been what you would have needed to take care of this to pass inspection? Am I missing something?
Maybe. I’ve never had good luck with muffler bandages unless they can seal against clean smooth metal, and that wasn’t the case here.
Having lived in the Berkshires (and worked for the NYS Thruway) for a long time when I was a youngster and knowing what that climate does to a vehicle, I would shy away from anything from that area. By the time you go through repairing everything because it is either rusted or breaks when taking off because of corrosion you could have had a nice vacation trip down south and found a rust free vehicle. However, if that was the case we would not have a lot of the stories you write.
Excellent article!!! I was laughing out loud while reading it. It sounded so much like something I’ve done so many times!! Thanks for the laughs.
(I enjoy reading your articles and am a fellow Massachusetts “residential garage mechanic”.
Rob. Please don’t stop doing your own work and telling wannabees like me about it! But do not consider it a failure to prioritize your projects. I’ll bet you if you chose 9 of your 13 vehicles and disposed of the other four, in a year you would still not have them all fixed. Think about how much easier it will be with all that extra room and parts money from selling those four classics.
I feel good. I sold a car last year and another last week. I’m down to 8 and 4 are actually licensed, insured, and roadworthy. The same amount of time to spend on fewer projects means another one on the road this year.
Why so many negative comments? Did you not read his title of “Hack Mechanic “. Personally the one thing I would do differently is sell the crappiest car in the fleet and purchase a 110 mig welder. Or 220 rig if you have the power source and funds. I just upgraded to 220 unit and gave my old 110 unit to my son. Had the Lincoln 110 for 25 plus years and it got used regularly. Only drawback was it could only weld up to about 3/16” thick metal if you cranked it up and slowed wire speed
My only comment Rob, is the first photo – the van in the garage. Either the photo doesn’t show properly, or by my eye you had another 6 inches clearance to drive forward – easy. 🙂
If you’re gonna bodge, bodge all the way!
My only comment Rob, is the first photo – the van in the garage. Either the photo doesn’t show properly, or by my eye you had another 6 inches clearance to drive forward – easy. 🙂
If you’re gonna work in a garage like that, then you gotta be willing to go for it! (you should see my ‘working space’ in my garage).
Good job Rob! We both know that hack repair will still be on there 5 years from now when the trans grenades.