Media | Articles
Safety requirements (not just tips) when using floor jacks and jack stands
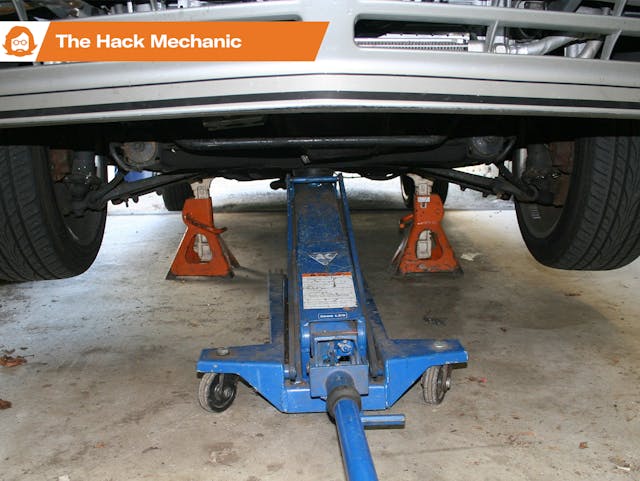
After a ratchet-and-socket set, box-end wrenches, and screwdrivers, the most commonly used automotive DIY tools are probably a floor jack and a set of jack stands. Whether you’re changing a flat tire, replacing brake pads and rotors, or performing work under the vehicle that requires it to be raised for clearance or comfort, it’s important to understand that the functions of floor jack and jack stands are tightly intertwined.
That is, you use a floor jack to lift the nose or tail of a car (or, possibly, just one wheel), then you set it on jack stands to keep it safely in the air.
Last year, low-priced tool giant Harbor Freight recalled several of its jack stands due to instances of the stands slipping under a shifting load. It pushed the issue of jack stand safety to the automotive media’s front burner, which is certainly a positive thing. I thought I’d give you my common-sense perspective on floor jack and jack stand safety.
The old stamped metal-pinned tubular jack stand design
Before I delve into the mechanics of the slippage of the Harbor Freight stands, we need to jump into the Wayback Machine. If you wrenched 30 years ago, the jack stands you likely used had a design consisting of two sliding stamped metal tubes like the ones pictured below. The bottom of the outer tube was slit in three places, and the resulting sections were bent outward to create three legs which had metal bands welded to the bottoms to secure them against splaying apart further under load.
The inner height-adjustable tube had a cradle on the top to hold whatever part of the car it was under, as well as several holes that could be aligned with a hole in the outer tube and locked with a metal pin that was the diameter of a pencil. Stands like this were inexpensive and lightweight, but the stamped metal was fairly thin, the increment of height adjustment with the holes was usually pretty coarse, and using the stands meant putting them under your jacked-up car, raising the inner tubes, lowering them until one hole aligned with the hole in the outer tubes, and manually sliding the pins through. The pins actually performed three separate functions—selecting a height, locking that height in place, and supporting the weight of the car—but this wasn’t really trumpeted as an advantage.
Marketplace
Buy and sell classics with confidence

The newer ratcheting jack stand design
The stamped metal-pinned tubular jack stand was gradually replaced by a welded ratcheting design. Instead of having two sliding stamped-metal tubes with their location fixed by a pin, the ratcheting design has a post with teeth, which slides up and out of the middle. This ratchet works like the familiar ratchet in a wrench, except it’s linear instead of circular. Teeth on the post are a right-triangle sawtooth shape with the short edge parallel to the ground. As the post is lifted up, a “pawl”—a curved eyebrow-shaped bar—has one end that pivots, and another end that slides under the part of the tooth that’s parallel to the ground, making it so the post can be pulled upward but can’t be lowered without flipping the release bracket. It’s a bit quicker to deploy beneath a jacked-up car than a pinned stand.

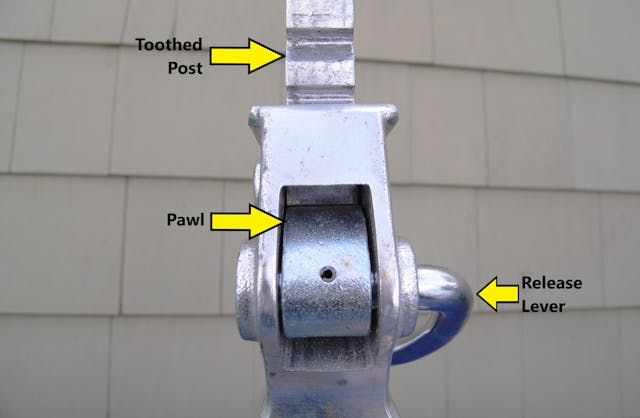
In addition to the ratchet itself, the construction of a ratcheting stand is heavier and thicker than the pinned stamped-metal tubular one. Typically, a thick metal plate is bent into a four-legged shape, welded onto itself at a seam, and welded at the top to the central body that receives the toothed post. If you accidentally run over a stamped-metal tubular stand, odds are you’ll flatten it, or at least bend the legs. In contrast, if you accidentally run over a ratcheting jack stand, odds are you’ll damage the undercarriage of the car.


And with that background, let’s talk about …
The Harbor Freight jack stand recall
In May 2020, low-priced tool giant Harbor Freight recalled 1.7 million of its Pittsburg-brand three-ton jack stands (items 56371) and six-ton stands (items 61196 and 61197) due to reported instances of the stands slipping while under load. You can find videos on YouTube where people demonstrate this under controlled conditions. This video of a disassembled jack stand does a pretty good job of showing the mechanics of the problem—the end of the pawl not fitting as securely under the teeth as it should. And on this website, you can see photos in which someone put white paint on the pawl, and a surprisingly small amount of paint transferred onto one of the teeth on the shaft, which demonstrates the small amount of overlap of the pawl under the teeth.
The root cause of the problem was reportedly traced to aging tooling at one factory run by the manufacturer, the Jiaxang Golden Roc Tool Company, affecting reportedly about 5 percent of the jack stands manufactured there. There were reportedly 11 injuries caused by the problem, none of them life threatening.
Unfortunately, Harbor Freight’s replacements for the recalled three-ton stands (item 56373) had a different problem—instances of the seam weld cracking when under load. These were recalled as well. You can find videos of this “zipper failure” of the seam weld on YouTube. Together, the recalls created the impression that any Harbor Freight jack stand was going to kill you.
The reaction
An unintended but completely reasonable response to the Harbor Freight jack stand debacle was a sharp resurgence in interest in tubular jack stands, where a thick and plainly-visible pin is used to set the height, lock the stand, and support the car’s weight. Although the cheap lightweight stamped metal design is a thing of the past (and rightly so), sales of pinned-design jack stands such as this Torin T43004, with two sliding aluminum tubes and a screw-on aluminum base, soared. In addition to having a locking pin instead of a pawl, the screw-on base means that this particular design is even free of the kind of weld that failed in the second Harbor Freight recall.
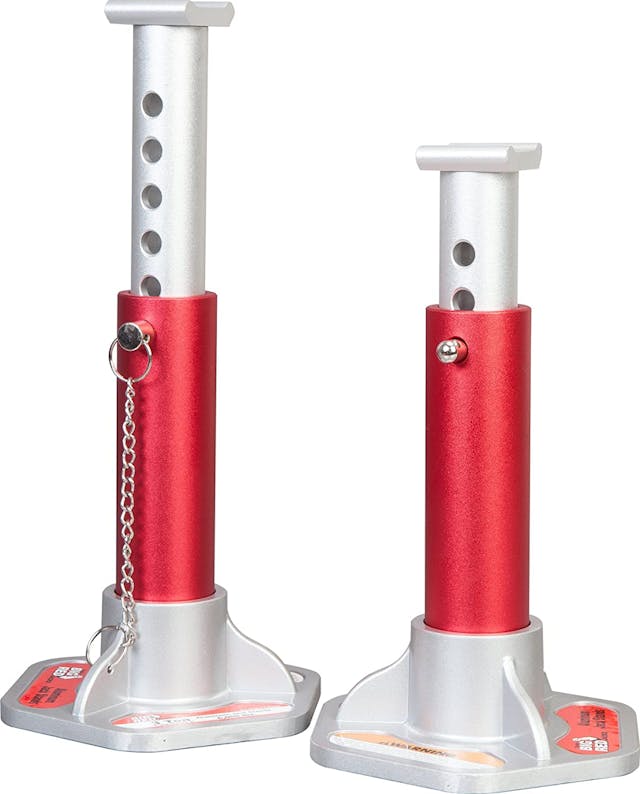
Ratcheting jack stands, however, have not gone away. Far from it. In fact, many if not most new ratcheting stands have had a makeover, receiving a manually-insertable safety pin that provides redundant load bearing to the ratchet pawl. If you want to buy new ratcheting stands, you’d probably need to go out of your way to find one that doesn’t have this “double-locking” feature.

The REAL safety issues
Obviously, the Harbor Freight jack stand recalls are a very serious issue, and if you have Harbor Freight jack stands from one of the recalled batches, you should return them. But should you toss your current ratcheting jack stands in the recycle bin and pony up for one of the newer pinned-tubular stands or a ratcheting stand with a redundant pin? If you’ll never feel safe working under a car unless you do, sure. But if that’s all you do, you still won’t be as safe as you could be.
With that said, I’ve been wrenching on my own cars for 40 years and writing about it for 35, and in my Hack Mechanic opinion, the dominant safety issues working under a car are these, and they remain these, even after you’ve exchanged your Harbor Freight jack stands:
Always, always, “double-jack” the car. I can’t write this often enough or say it strongly enough. The single most important thing you can do to make working beneath a car as safe as possible is that, after you’ve used your floor jack to raise the car and set it down on jack stands, leave the floor jack in place as a back-up. This is literally zero extra work, and it costs you nothing. I realize that, at times, the floor jack may then be in the way, but consider approaching the part you need to work on from another angle.
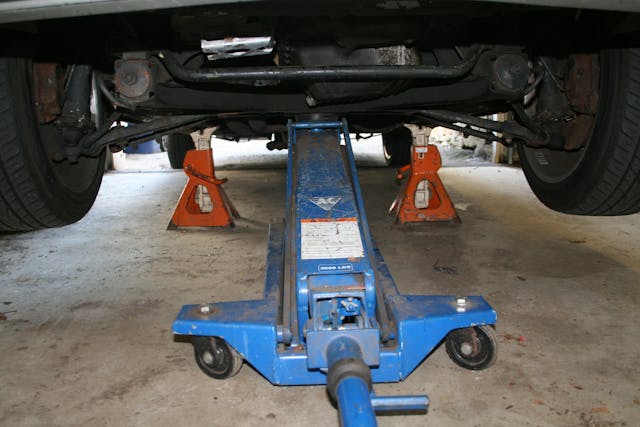
Always jack up the car on a level surface, never on an incline. You’d think you need to be suicidal or an idiot or both to jack up a car on a hill, but people sometimes make poor choices in the heat of the moment. I was a physics major in college and had a mechanics professor—that’s “mechanics” as in the study of the forces on moving and stationary objects—who died when his car fell on him. Months after it happened, I looked at his driveway and was astonished at its steepness. What caused him to do it, I don’t know. The best, smoothest, most level, safest place to jack up a car is usually your concrete garage floor. Maybe there was already a car in his garage and all he wanted was a quick oil change. Who knows. That a mechanics professor could get this wrong enough to get himself killed haunts me to this day.
Don’t jack up a car on asphalt, especially on a hot day. Asphalt is never as hard as concrete, and as its temperature increases, it can get soft enough that a floor jack and jack stands can sink right in, causing a car to topple. Combine it with a surface that isn’t laser level and things can go sideways very quickly. I’ll never forget checking out a car I was thinking about buying. I met the seller in a CVS parking lot in July. I’d brought an aluminum floor jack and used it to put the nose of the car in the air to quickly wiggle the front wheels and check for front-end play. I didn’t “double-jack” the car because I wasn’t even pulling the wheels. I didn’t perceive the parking lot as slanted, but it was, and the slant was at a right angle to both the car and the jack, and that—combined with the hot temperature and the soft asphalt—caused the jack to sink and the car to topple, with the nose abruptly jumping one foot toward me. My body was never under the car, but it scared the bejesus out of both me and the seller, and I’ve never forgotten it. If you have no place other than asphalt to jack up a car and have absolutely no other choice, I strongly advise making sure it’s dead flat and putting metal plates beneath the floor jack and all jack stands.
Once settled, check the jack stands. Once you’ve released pressure on the floor jack and let the car down on the jack stands, check the stands both top and bottom. Make sure that the part of the car the cradle (at the top of the stand) is touching is in the middle and is sitting flat, and verify that all four legs of the base of the jack stands are sitting securely on the ground. This is especially crucial if you’re trying to put all four wheels of the car in the air, as the act of jacking up one end of a car can easily cause stands already at the other end to tip forward.
Don’t overload the jack or the stands. I’ll talk about load ratings below, but basically, don’t be an idiot and jack up a truck with a little jack and then set it on little stands.
Don’t rock the cradle. Once the car is up on stands, give it a few good shoves from all four sides. Any motion should be barely perceptible. It certainly shouldn’t sway. (Note, however, that some owners of pinned jack stands report that, due to that circular pin, they do sway more than ratcheting stands, where the pawl rests on a squared-off tooth). However, once you’re under the car, do not rock it. It can be surprisingly easy to set up a resonant harmonic motion if you’re doing a lot of shoving, such as while installing a transmission and trying to line up the splines and seat the input shaft in the pilot bearing.
Jack stand load ratings
Jack stands manufactured after 2015 should be rated in pairs. That is, a pair of three-ton jack stands should together safely support 6000 pounds. The ratings come from the American National Standards Institute (ANSI) and American Society of Mechanical Engineers (ASME). You may see the standards referred to as ASME PALD (Portable Automotive Lifting Devices) and ANSI PASE (Portable Automotive Service Equipment). Stands manufactured to these standards are tested to 200 percent of their rated load for 10 minutes and experience less than 1/8-inch of deformation. However, note that testing is by the manufacturer, not by ANSI or SAME, and merely allows the manufacturer to claim certification of the product line. It is not assembly-line testing of each set of stands.
If you look up your vehicle’s weight in the owner’s manual or online and divide that by two, in theory that’s the minimum load rating you need for a pair of jack stands to support the front or rear of the vehicle. However: 1) for both safety and peace of mind, you probably don’t want to use the minimum, and 2) weight is just one factor. Jack stands also need to reach the underside of the vehicle and support the load in a stable manner, and the higher the stands are extended, the more the vehicle can rock. For example, half the weight of a 6000-pound truck is 3000 pounds, and on paper, even a little pair of two-ton (4000-pound) jack stands exceeds that, but two-ton jack stands are typically short and may not reach the frame rails of the truck even when fully extended.
So, apply some common sense and use the little two-ton jack stands for small passenger cars, three-ton stands for medium to large cars or mid-sized SUVs, and real five- or six-ton truck jack stands for a full-sized truck or SUV.
Floor jack load ratings
There are a few ways to think about floor jack load ratings. A floor jack that is ASME PASE 2014-certified should have been tested by the manufacturer to 150 percent of its rating, so as with jack stands, there is a built-in safety factor. It also should have a bypass valve that prevents you from continuing to lift if it’s overloaded. (Safety tip: If it’s getting really hard to keep pumping up the jack, you’re probably close to overloading it.) However, as is the case with jack stands, if you look at the load ratings the wrong way, you can fool yourself into doing things that aren’t safe. It’s important to understand that the physical size of the jack is probably just as important as the numerical load rating, since a big jack is simply more stable than a small one.
Case in point: If you’re only ever using a jack to lift one wheel to change a flat and want to factor in that the wheel could be on the heavy end of the car where the engine is, assume the jack has to safely lift 33 percent of the weight of the car. For a big vehicle like a 6000-pound truck, one-third the weight is 2000 pounds, so, on paper, even the smallest 1.5-ton (3000-pound) trolley jack has an adequate rating. But, as with the jack stand calculation above, this is so misleading that it’s unsafe, as the jack needs to reach the lift point, get the vehicle high enough in the air to lift the tire off the ground and allow a stand to be put under the frame, and do all this in a stable fashion. I simply don’t believe that a little trolley jack with a narrow base can do that repeatably and safely on a big vehicle, no matter what the load rating says.
For this reason, an oft-quoted rule of thumb, cited by Tom and Ray Magliozzi (“Click and Clack” of Car Talk fame) is that a right-sized floor jack should be rated to at least 75 percent of the vehicle’s weight. So, 6000-pound vehicle à 4500-pound (2 1/4-ton) jack. That still feels a little light to me, but the recommendation does say “at least.”
My option is that, as with jack stands, you should use a good dose of common sense and only ever use a narrow little trolley jack to lift one wheel of a small car, use at least a two-ton jack for repeated in-garage lifting of most cars, use at least a three-ton jack for SUVs, and use a real truck jack to lift a real truck.
Where to lift, where to support
This could be a whole column in and of itself. Consulting an owner’s manual doesn’t always help, as it’ll probably only tell you where the factory jack points are for the flimsy little jack that comes with the car. An enthusiast web forum is probably the best place to look. The nose of an older car is typically lifted from the middle of the front subframe, and jack stands are typically placed either under the subframe or the frame rails, but on a newer car, these locations may be hidden under cladding, and the plastic jack pads on or under the rocker panels may be best. Be hyper-aware of the rust situation on your car, as the car world is filled with stories of jacks puncturing rusty frame rails.
You own more than one screwdriver, right?
To a certain extent, with both floor jacks and stands, bigger is better, as bigger generally means a larger load rating, more stability, and higher lift, but it also means heavier, and that’s at odds with portability. If you’re looking for just-in-case floor jack and stands to have in the trunk for a road trip, you want them light and right-sized.
One wildcard is that, if you have a very low car with a jacking point that is far underneath and difficult to reach, you need a low-rise, long-reach floor jack, but the quirky tradeoff is that even though these are big and heavy to have the structural rigidity necessary to achieve the long reach, that very design means they don’t have as high a load rating as an equally-heavy truck jack would have.
I currently own four floor jacks. The biggest is an AC Hydraulics DK13HLQ, which was and still is the cream-of-the-crop of low-rise long-reach floor jacks and has an insanely low 3.15-inch profile. They’re very expensive, but about 10 years back I found a used one locally and treated myself. For reaching the jack point of my BMW M Coupe or playing limbo with the front sway bar of my lowered Lotus Europa, nothing else I own will work. However, due to its long reach, it’s only rated at 2900 pounds. The Harbor Freight 2 1/4-ton jack has been kicking around the garage since it was still called “Harbor Freight and Salvage.” The Pittsburgh 1.5-ton aluminum floor jack gets thrown in the trunk for road trips. It’s a little bigger than the little yellow trolley jack that used to perform that function, but that makes it more stable. I don’t currently have a real truck jack, but then again, I don’t currently have a real truck.


Stand-wise, there are three sets, all of which are ratcheting stands. There’s a set of tall six-ton truck stands that I bought nearly 20 years ago when I needed to put the back of the Porsche 911SC way up in the air to drop the engine. There’s an old set of Harbor Freight three-ton stands that still see the most use. And there’s a set of aluminum stands that get thrown in the trunk along with the aluminum floor jack for road trips. These are all old enough that none have the new “double-locking” redundant safety pin, but since I always “double-jack” the car, I don’t lose sleep over it. I do check the welds on all three sets for any signs of cracking.
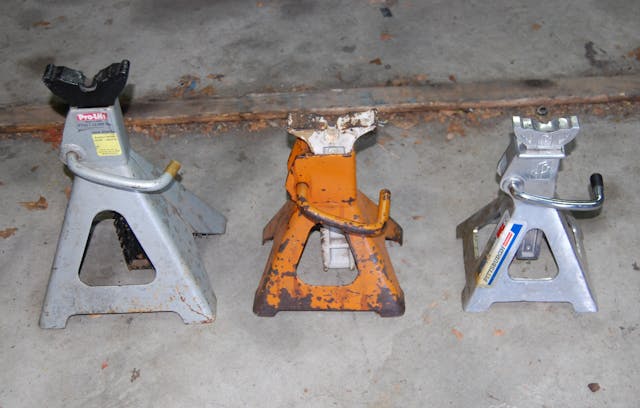
If you won’t feel safe working under a car until you have the best most expensive jack stands available, by all means have a look at the D41609 from US Jacks or the ESCO 10498 stands. But once you have them, please remember everything I said above—always double-jack the car, work only on a level concrete surface, do not overload the stands, and do not rock the car.
Lift safely, my friends!
***
Rob Siegel has been writing a column (The Hack Mechanic™) for BMW CCA Roundel magazine for 34 years and is the author of seven automotive books. His new book, The Lotus Chronicles: One man’s sordid tale of passion and madness resurrecting a 40-year-dead Lotus Europa Twin Cam Special, is now available on Amazon (as are his other books), or you can order personally-inscribed copies from Rob’s website, robsiegel.com.
One other thing I do is when I remove a wheel, which happens at least 90% of the time I’m jacking up a car, I lay it down and store it underneath the vehicle. It’s my last line of defense. It may not keep me “safe” but it will keep me from being best served with butter and maple syrup.
The first thing you say is don’t buy jacks from Amazon. Then you include links to buy jacks – from Amazon!
😳
Great article here Rob.
Was a pleasure to read and quite informative.
I have been wrenching for 20+ years and your tip about double jacking, is spot on.
I was never taught this school, but it just makes sense.
Thanks
Thanks for the article. Nice work on making it engaging and understandable with photos.
you know those disturbing statistics about how long you’ve spent sitting on the toilet – how many years of your life – same with me for how long i’ve spent underneath cars. i’m 73 and won’t do it anymore. i need a lift in my garage, and that would be heaven, affordable – 5-7000 dollars, but my wife would kill me – in a bad way. but thanks for the article anyway. cheers, kevin in minneapolis
sorry my caps lock on my mac don’t work no more.
Another good tip with the ratcheting type….do not ‘raise’ the posts. If you need it higher get taller ratcheting type.
I may have missed it in the article, but any wheels that will remain on the ground should be chocked for added safety.