Media | Articles
Broken Bolts and Unrealistic Expectations
There’s a classic Monty Python routine called “How to Do It” where they issue laughably simplified explanations on how to do very complex things (“Today we’re going to learn how to build box-girder bridges. But first, here’s Jackie to tell you how to play the flute: ‘Well, you blow here, and move your fingers up and down there.'”) I come back to this time and time again because it tracks with just about anything that requires expertise someone else has that you don’t.
Witness broken bolts. I’m not sure there’s any aphorism truer than the one that says, “every 15-minute repair is one broken bolt away from being a three-day job.” Yet there are—reportedly—tricks to removing them that put you back on track.
Allow me to digress for a moment. In a recent issue of Hagerty Drivers Club magazine, Matthew Crawford—author of Shop Class as Soulcraft: An Inquiry into the Value of Work—wrote a piece commemorating the 50th anniversary of Robert Pirsig’s Zen and the Art of Motorcycle Maintenance: An Inquiry Into Values. I’ll freely admit that I read ZATAOMM when I was in college, and that I re-read it (and read Matt Crawford’s book) while I was writing Memoirs of a Hack Mechanic 12 years ago. I’ve never met Matt, but he and I (and many of you) are clearly cut from the same cloth where we enjoy working on cars because we find it fun, because it saves money, and as Crawford says, because it makes us “master of our own stuff.”
Where was I? Oh. Broken bolts. Right. One of the reasons I re-read ZATAOMM was that I recalled a chapter titled “Stuckness,” and wanted to reference it in a chapter of my book where I enumerated several techniques for removing seized bolts. Imagine my disappointment when I found that the, uh, nut of Robert Pirsig’s chapter on “Stuckness” was this useless train wreck of words:
“Stuckness shouldn’t be avoided. It’s the psychic predecessor of all real understanding. An egoless acceptance of stuckness is a key to an understanding of all Quality, in mechanical work as in other endeavors. It’s this understanding of Quality as revealed by stuckness which so often makes self-taught mechanics so superior to institute-trained men who have learned how to handle everything except a new situation.”
Marketplace
Buy and sell classics with confidence
Right… so tell me how to get the broken stud out.
“What your actual solution is is unimportant as long as it has Quality. Thoughts about the screw as combined rigidness and adhesiveness and about its special helical interlock might lead naturally to solutions of impaction and use of solvents. That is one kind of Quality track. Another track may be to go to the library and look through a catalog of mechanic’s tools, in which you might come across a screw extractor that would do the job. Or to call a friend who knows something about mechanical work. Or just to drill the screw out, or just burn it out with a torch. Or you might just, as a result of your meditative attention to the screw, come up with some new way of extracting it that has never been thought of before and that beats all the rest and is patentable and makes you a millionaire five years from now. There’s no predicting what’s on that Quality track. The solutions all are simple…after you have arrived at them. But they’re simple only when you know already what they are.”
Okay, so pretty much useless.
Why am I on about this?
Well, guess who had to deal with a snapped-off bolt?
As the weather in Boston warmed, I returned to resurrecting the air conditioning in the FrankenThirty, my salvage-titled 1988 BMW E30 325is. I pulled the rusty original serpentine-flow condenser out of the nose and was about to swap it for a new parallel-flow condenser when I remembered something: I’d encountered a snapped-off bolt last August when I bought the car and was resurrecting it. It was one of the bolts holding the upper timing cover. Because this car has a timing belt and not a chain, the timing cover is really just a dust cover, so the missing bolt wasn’t part of an oil seal or anything, but it not being there had an unusual consequence. The distributor cap (well, there’s no actual distributor because the spark advance is computer-controlled, but there’s still a cap and a rotor) is bolted to the upper timing cover, so the fact that the cover was unsecured at one corner created a misalignment that was allowing the spinning rotor to wear a groove in the cap.

Now, if a bolt is stuck but hasn’t yet snapped off, I detail a number of techniques for removing it in my book (all of them are basically heat, grip, and the right amount of leverage so you don’t snap it). But if the bolt head has snapped off and left nothing to grab onto with Vise Grips or an external-gripping stud extractor, I’m only aware of two real choices: Drill out the bolt, or weld a nut to it.
Let me set something straight right now. There’s a widely-held misconception that the purpose of drilling out a bolt is so you can put an EZ-Out in it, turn it counter-clockwise, and back the bolt out. If you want to do that, knock yourself out, but know that the experience of yours truly as well as thousands who have gone before you is that if the bolt’s threads are so seized in the hole that the head of the bolt snapped off, the odds of it suddenly saying “Oh crap this guy’s got an EZ-Out I’d better high-tail it out of this hole where I’ve been living since the Eisenhower Administration” is vanishingly small. In fact, the odds are that what’ll happen is that the hardened-steel EZ-Out will snap off in the hole, in which case you are truly, magnificently, and completely boned. In general, the best thing you can do with EZ-Outs is to go to your toolbox right now, find them all, and throw them all away, thus removing the temptation that this time they’ll help you instead of pulling the football out from Charlie Brown.
(A few people in the cheap seats are grumbling that you can use left-handed bits to drill the hole, and maybe, if The Automotive Powers That be are smiling on you, the heat and the left-handedness of the drilling will loosen the bolt so that the EZ-Out will in fact back the bolt out. I’ve had it happen. Once. In nearly 50 years of wrenching. It’s not a bet I’d make in a situation where, if EZ-Out snaps, you’re screwed.)
So, you’re not going to use an EZ-Out, why drill out a bolt? Because, most of the time, what you’re trying to do is remove as much of the bolt as possible. If you drill exactly in the center of the bolt and use progressively larger and larger bits, you can then re-thread the hole by using a tap. Or sometimes, if you’re lucky, once you’ve removed enough material, you can start to peel off the remnants of the old bolt using a pick, sort of like peeling an orange from the inside. Or if the bolt isn’t really supporting a big load, you can cheat and tap a smaller hole for a smaller bolt (shhhhh, don’t tell anyone I told you). But whichever of these options you use, it’s slow-going work, and it’s trickier to do on a blind hole (one where the drill bit never emerges from the back).
So you can imagine the attraction of the weld-a-nut-to-it method. There are dozens of videos on YouTube showing this being done, sometimes in a matter of seconds. If the surrounding metal is steel, you put a washer around the threads so the weld will stick only to the bolt (whereas if the bolt is snapped off in aluminum, it doesn’t really matter, as the MIG wire won’t stick to aluminum). If the bolt is snapped off below the surface of the threads, you need to build up a pool of melted wire on top of it. Then you weld the nut to the mound and/or washer. The beauty of the technique is that, in addition to creating something you can twist, the act of welding to the broken bolt—of putting a crap-ton of amperage through it—directly heats up the bolt, which, just like applying a torch or an induction heater, can help to break the bond of corrosion in the threads. At least in theory. (As they say in physics, in theory, theory and practice are the same, but in practice, they’re not.)
Now, I do own a welder, a Millermatic 141 that I bought about ten years ago when I had dreams of teaching myself how to weld and doing my own bodywork. That never happened, but I have used it a couple of times to do the weld-the-nut-on trick. Both times were on snapped-off exhaust studs on heads that I’d already removed, so I had them on a milk crate on the garage floor, and the surface I was attacking was horizontal. This time, I was about to try removing the FrankenThirty’s snapped bolt with the engine in situ.
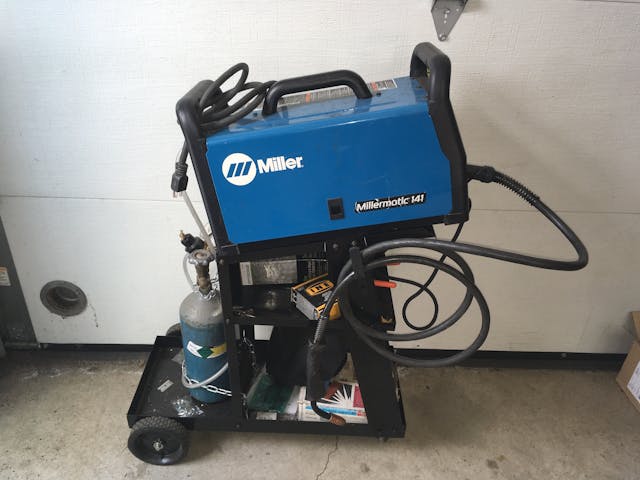
So, back to the present. The FrankenThirty was sitting in the driveway with the grilles, condenser, and radiator out, and as I looked through the nose at the front of the engine, I remembered the snapped-off bolt, and thought “It’ll never be easier to deal with than right now, and if you don’t, you’re going to worry about that distributor cap cocking just enough to cause the car to die on the George Washington bridge. Do it now.”
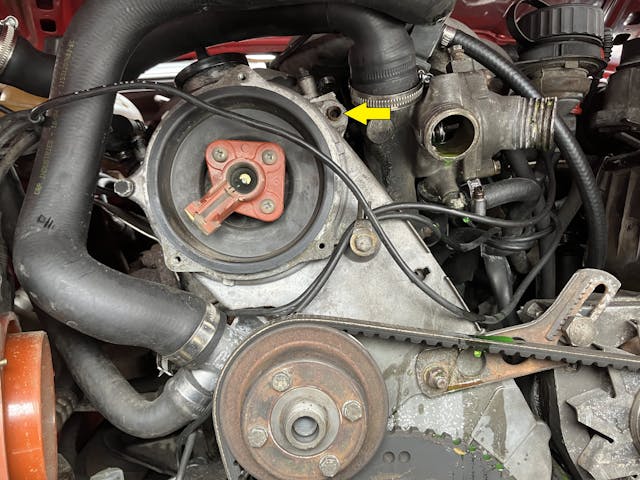
I rolled the welder out into the driveway, and… long story short, I couldn’t get the technique to work.
It seemed to start off well, though. I cleaned the broken surface of the bolt with a Dremel tool. I shielded the car’s rubber timing belt first with aluminum foil, later with a cut-up disposable roasting pan. I built up a nice mound on top of the snapped-off bolt, though it drooped due to gravity.
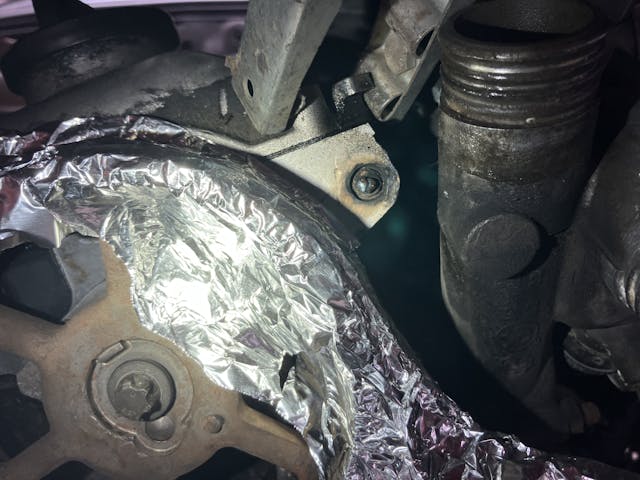
But whenever I tried welding a nut onto the mound, I got very little adhesion. I tried holding the nut in place with needle-nose Vise Grips. I tried pounding it on with a hammer so I had a clear shot at it with the welder. I varied the amperage and the wire speed. I read in GarageJournal that you may need to try this multiple times before the nut sticks. Of the 17 (yes, 17) nuts I tried, only three of them stuck enough to even begin to put any torque on the bolt.

In frustration, I called a good friend of mine, a professional wrench who welds in his sleep. I explained what I was doing and what kept going wrong. His reply was the last thing I ever expected him to say:
“Yeah, I’ve tried the weld-a-nut-on trick. I’ve tried it with and without the washer. I’ve only ever gotten it to work once. I always wind up falling back to drilling the damn thing out. The only thing I can recommend is that new nuts almost always come with a coating. You might try drilling out the threads and belt-sanding the faces.”
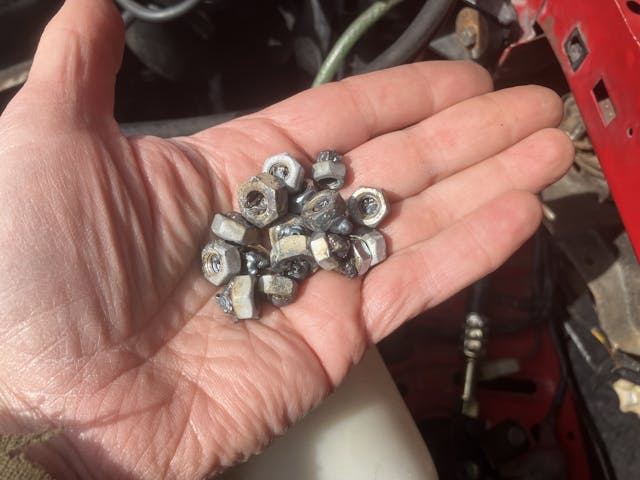
So I did. No difference. I’m not sure what the problem was. Maybe lack of good electrical contact between the nut and the head for everything to heat up together and the melted welding wire to adhere to both. I gave one last try by abandoning the nut and trying to build up a weld mound (as that seemed to work fine) that I could grab onto with needle-nosed Vise Grips. I did succeed in getting enough of a grip to convince myself that, no, the broken bolt wasn’t simply going to unscrew if I could get something on it to twist it. It reached the point that I worried about risking damage to the head, as well as to the rubber timing belt I was trying to shield with a cut-up roasting pan.
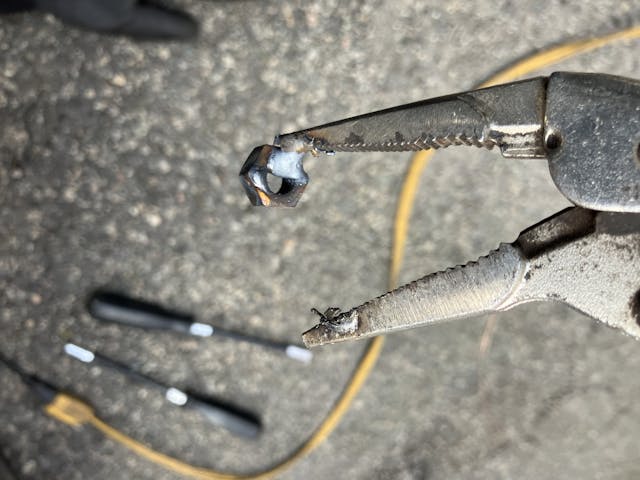
So my future clearly involved a drill. I found that my left and right-handed bits were too dull to be functional. I read up on and watched a few videos on the best bits to use to drill out bolts, and one fellow swore by Bosch glass and tile bits. I ordered a set, ground off the welded mound I’d created, center-punched the face of the bolt as best I could (which wasn’t very accurate at all), and used the smallest (1/8”) bit. I wouldn’t say it cut through it like butter, but there was progress. I then moved up to the 3/16” bit. In about 15 minutes, I’d drilled myself a decent hole.
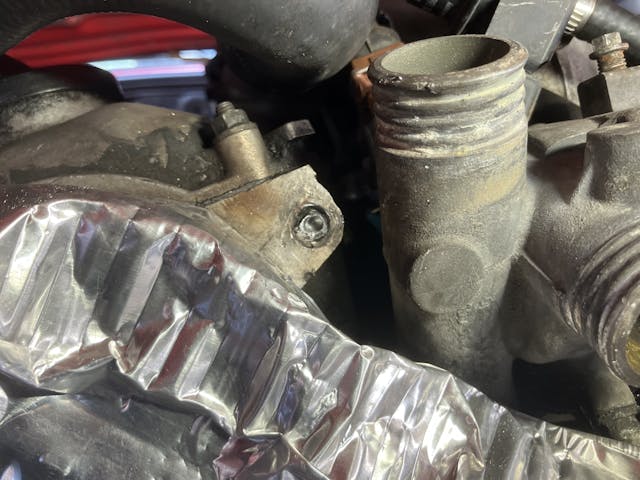
The original bolt was a metric M8 with a 13mm head, but it originally held not only the timing cover but also an engine hoist bracket. Since all I needed to do was secure the corner of the timing cover so the distributor cap didn’t wander around, I thought I’d use a smaller M6 bolt with a 10mm head. To my surprise, though, I couldn’t find my M6 tap anywhere. I did, however, find a 10-24 tap, and by coincidence, the hole I’d already drilled seemed to be the right size to receive it. A quick trip to my local Ace Hardware store revealed another surprise—they didn’t have 10-24 cap head bolts that short. They did, however, have an Allen-head bolt just the right length. A washer, a lock washer, a bit of blue Loctite, and done.
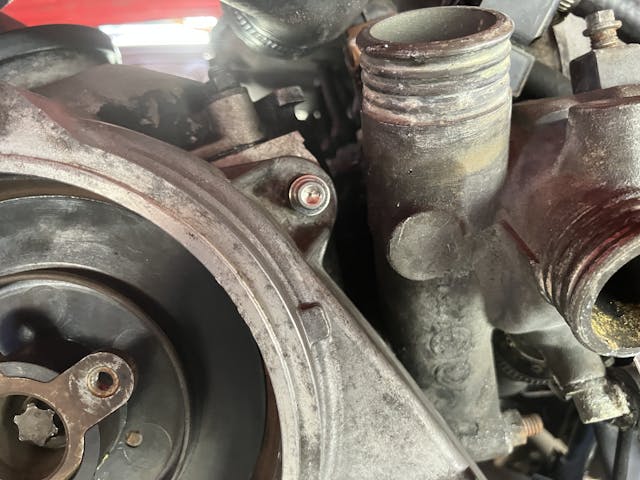
So. If you snap off a bolt and leave nothing to grab onto, if you have a friend who has a welder and swore he’s done this a dozen times, take him or her up on the offer. Maybe they actually know “how to do it.”
But don’t look in Zen and the Art of Motorcycle Maintenance. The only Zen about stuck bolts is being calm enough not to commit hara-kiri with an EZ-Out.
***
Rob’s latest book, The Best Of The Hack Mechanic™: 35 years of hacks, kluges, and assorted automotive mayhem, is available on Amazon here. His other seven books are available here on Amazon, or you can order personally inscribed copies from Rob’s website, www.robsiegel.com.
I am glad it’s not just me! Never got the EZ-out to work and broke a few off too. If I ever win the lottery I know what it’s going to feel like, just like when you remove a broken bolt with the threads still intact.
Thank God, I now know I’m not alone. I consider any tap extractor to be the biggest fraud ever perpetrated, right up there with the magic 60 mpg carburetor that somehow GM or the oil companies managed to kill, on anyone in the machining or wrenching business!
I have been running big diesel ships for forty years with broken bolts aplenty over the years but would never say I’m an expert as every situation is different. My only oilpatch recommendation from the early 1980’s is heat the stud and melt in beeswax, it sucks in by capillary attraction and even after it cools it’s a little easier to release. As an aside, a relative brought his hemi Durango to the Dodge dealer who snapped off two exhaust studs in the process of a routine service only to be told to live with it or fork over $3000 to remove the head and properly repair,(something a fellow hack would never sanction!!). Even though I was itching to take a crack at the hemi I wisely kept my mouth shut as sometimes in the end the 3 Grand would be a cheap fix!!!
Perhaps in all this talk of burning, grinding and welding there should be a safety note. Cad and zinc, found on many pieces of auto hardware are dangerous, both now and down the road. So are Brake clean and various rust busting chemicals, ESPECIALLY when welding. Always use respiratory protection when messing with processes and materials with which you are not utterly familiar.
BTW, read ‘Zen’ and found it very helpful. I realized I am the friend who believes you should pay money, and make it someone else’s problem. Never once have I regreted it.
Really, has anyone EVER said “Shoulda done this myself”
Agree with ExTech for the welding technique for sure, key is to let it or make it cool after welding and give it a good smack with a punch and hammer before extraction. If you are drilling for extraction a cobalt drill for hardened bolts is recommended and drill all the way through as Baconhat recommended. I’ve also had very good luck with heat and cool, weasel spray and a good smack with a hammer and punch and then drill with a left hand drill bit. It will very often catch enough and back it right out.
Being retired and not having to get anything done by today, I learned that good penetrating oil applied daily for a week or so will loosen up nuts/bolts. Running a die down rusted threads can prevent snapping a bolt when the nut is half way off. I also try tightening the offending hardware just enough to break it loose from the rusty threads so it doesn’t have to break the rust on the exposed threads at the same time as the internal threads. And finally I have drilled out bolts too.
I worked as a mechanic for many years, and when faced with a broken bolt that I really, REALLY did not want to have to disassemble components to remove (head, block), I’ve found two things to be most important.
1) Don’t be in a hurry, you’ll just make the problem worse. Use a good penetrating oil like Kroil, and give it time to work. Put ti in there every few hours for a couple of days and just wait. It doesn’t hurt to heat the surrounding metal.
2) When you drill it, use left-hand bits, and – this is the single most critical thing – drill the pilot hole dead center. Use a good center punch, and take as long as you need to be sure the first drill will be centered. If you don’t, it will be downhill from there. If you do, you’ll find that at some point the thin remains of the broken bolt will usually spin out with the drill that’s just a bit smaller diameter than the bolt.
I normally drill out 95 percent of the bolt and then extract it, but I tried melting in wax a few weeks back and it worked!
Hagerty had an article no more than 2 years ago about a retired racing mechanic/machinist. He also mentioned using wax for broken bolt extractions. If (more like when) I’m cursed with another broken bolt, I hope I don’t grab a glue stick by mistake!
I recently experienced that Cold Flush feeling you get when you realize you are now screwed and have a big headache to deal with. When the 24″ breaker bar was failing to get my big harmonic balancer bolt to snap! loose as they usually do, I pulled even harder until I could feel it moving slowly. In a “I’m going to twist my head off before I come loose” kind of way. And yes, I had to complete the de-capitation. Fortunately, I was able to lower my Corvair motor to where I could get a straight shot with my drill. SLOWLY I drilled the bolt out (in size steps) to where I could collapse the remains to the center. Turns out the white dust I encountered was the Loctite some previous idiot put on all the threads. Friends, remember someday, somebody might have to take your work back apart.
Yep, done this on a Mitsubishi Eclipse exhaust manifold. Those bolts were known for snapping if you looked at them.
I consider myself an expert in this and if it’s broken flush or too short to grab securely I go straight for the drill. Eyeball the center referencing the countersink of the hole if you can see one, it’ll be more accurate than the broken screw, one side of which will be at the crest of the thread and the other side at the root therefore not concentric to the hole. Use sharp drills! Learn how to sharpen them if new ones aren’t handy.
Bolt the part back on, make up a bush to go into the hole where the broken bolt was, and use this to pilot a small drill exactly in the centre of the broken bolt.
If you are welding a nut on, heaps of amps for a smallish burst, much more than if you were putting in a weld seam.
Don’t snap off the head off the bolt in the first place! Putting head-snapping torque on seized threads creates a bigger problem. What I learned to do, after the usual penetrating oil soak and heat application, is to re-tighten the bolt after trying to loosen it. This helps break the bond between the bolt threads and the hole threads. Alternate between loosening and tightening, gradually increase the torque, and use more oil and heat. Hitting the bolt head with a hammer, if possible, might help also. Sooner or later, with luck and patience, you’ll feel the bolt move just a tiny little bit. Now you’ve got it! It may take an hour or more to get to this point. Keep going back and forth, slowly using more torque as you get more movement, and eventually it’ll come all the way out. It worked for me when I had a very stuck bolt, took most of an afternoon, but it was worth it.
Don’t snap the head off the bolt in the first place! Putting head-snapping torque on seized threads creates a bigger problem. What I learned to do, after the usual penetrating oil soak and heat application, is to re-tighten the bolt after trying to loosen it. This helps break the bond between the bolt threads and the hole threads. Alternate between loosening and tightening, gradually increase the torque, and use more oil and heat. Hitting the bolt head with a hammer, if possible, might help also. Sooner or later, with luck and patience, you’ll feel the bolt move just a tiny little bit. Now you’ve got it! It may take an hour or more to get to this point. Keep going back and forth, slowly using more torque as you get more movement, and eventually it’ll come all the way out. It worked for me when I had a very stuck bolt, took most of an afternoon, but it was worth it.
I really enjoyed Zen and read Lila after that. In Lila, he ditched the motorcycle and replaced it with a boat. Not a boat person, but still enjoyed the book and I think it’s worth a read