Media | Articles
Watch Rimac explain the science behind hypercar battery testing

Like everything with a battery electric vehicle (BEV), nothing is tied to the traditions of internal combustion engines—and the is true for the validation and safety testing phases. When your upcoming ground-breaking BEV hypercar will churn out 1700 lb-ft of torque, you need an incredible amount of electrical energy. With that comes several challenges in safety, reliability, and repeatable performance.

Rimac’s C_Two features a massive 133-pound, H-shaped battery pack that consists of nearly 22,000 lithium nickel manganese cobalt oxide (LiNiMnCoO2) cells, all of which act like links in a chain as they force 720 volts to each of the four motors in the C_Two’s unique drivetrain. Each cell is equally responsible for the overall performance of the battery pack; if one lags behind in its discharge rate or becomes damaged, it affects the entire chain’s output. Thus, the design process is a game of selecting the components necessary to build advanced battery management systems (BMS), wiring harnesses, cooling systems, and enclosures to support the health of thousands of individual cells.
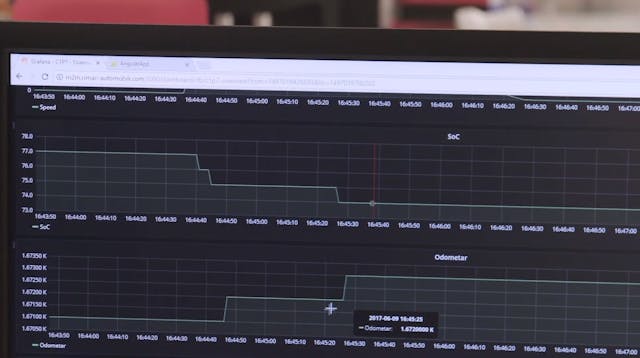
For Rimac’s founder and CEO, Mate Rimac, the intricacies of the powertrain created a unique approach to dyno testing his bleeding-edge battery packs to ensure that they’re capable of producing the C_Two’s astronomical acceleration figure (0–60 in 1.85 seconds, as promised) while providing usable range over the lifetime of the vehicle.
“We simulate the same things the battery [would] do inside the car. So acceleration, braking, track usage, highway usage,” Mate mentions in APEX.one’s latest video on the C_Two’s development.“And we do that 24/7 here, so in a few weeks or a few months we can simulate a good part of the lifetime of the batteries.”
Marketplace
Buy and sell classics with confidence
Batteries operate on a chemical reaction whereby ions are motivated to move from the cathode (in this case, LiNiMnCoO2) to an anode (graphite) via a chemical reaction between the two materials. The positive and negative terminals of a battery are connected to the cathode and anodes respectively, and the cathode material ultimately dictates the exact characteristics of a cell’s capacity, voltage, and rate of discharge.
Like all chemical reactions—even baking a cake—the surrounding conditions play a vital role in how quickly that chemical reaction occurs, thus dictating the ultimate discharge rate that the battery can sustain. “If you go slightly out of [ideal conditions], it doesn’t necessarily break, it will just be a little bit worse,” Mate explains. “And with some countermeasures, this can be slowed by software.”
These countermeasures are largely fulfilled the BMS, or battery management system, which regulates current flow into and out of the battery and manages its own inventory of cells inside the battery pack. In most automotive battery packs, both for hybrids and BEVs, you never have full “access” to the battery’s ultimate capacity and discharge rates. This is to ensure that, as the cells naturally degrade, some of that headroom can be allocated into the usable power sent to the car via the BMS.
In a BEV, the battery replaces a traditional car’s fuel system. It stores energy from a source and transfers it to the driveline where the “fuel” is turned into the kinetic energy that spins the wheels. In the same way that you can simulate fuel flow from the tank to the injectors without running the engine itself, you can test a BEV’s battery packs in an isolated state by simulating the discharge commanded by the motors.
“For example, for Koenigsegg, we do a full acceleration from 0 to 400 kph, [but] the battery, it feels exactly like it was doing the full acceleration run,” Mate explains. “We monitor a bunch of things, like every cell’s voltage, every cell’s temperature, the cooling inlet/outlet temperature, the terminal temperatures.”
The novel thing is that because we’re playing with electricity, and not gasoline, the expended energy from the battery packs is simply dumped back into the grid instead of the noise, heat, and torque created by internal combustion engines during similar durability testing. If you’ve been around a dyno, you understand how much of a ruckus is created while engines are tested at full-bore—but with Rimac’s testing, the process is essentially silent, according to Mate: “There’s lots of energy flowing here without anything moving, so that can seem a little bit strange.”
What do you think? While this isn’t a video of the C_Two’s four motors pumping out 2000 hp, it does bring up an interesting discussion in the ground-up differences between BEVs and traditional combustion engines. If we must rethink the end product, then our design and testing must similarly be reinvented. And while the battery testing Rimac conducts is highly efficient—most all of the energy used to charge the battery packs is returned back into the grid—we do love that wasteful cacophony of noise produced by an engine’s exhaust system.
Image Credits:
000, 002, 003, 004 — APEX.one
001, 005 to 010 — Rimac