Media | Articles
Polestar breaks from Volvo mold with unique aluminum EV platform
Polestar may be co-owned by Volvo and its parent company Geely, but the mimimalist, future-minded brand is determined to strike out on its own. The latest evidence? The bonded-aluminum electric-vehicle skeleton before you.
The brand’s previous two products, the 1 and the 2, each borrow from a Volvo. The sultry, $156K grand tourer that, as its name suggests, came first, rode on Volvo’s Scalable Product Architecture and used a hybrid powertrain. The crossover-ish sedan that is the 2 also dips into the Volvo modular bin. (It rides on a version of the Compact Modular Architecture, or CMA.) Dubbed 5, the next model will take over from the limited-edition, carbon-fiber-bodied 1 (Polestar only made 1500 total, with a mere 150 allocated for the U.S.) as the crown of the Polestar portfolio—and will ride on a unique, bonded-aluminum platform developed by Polestar in-house.
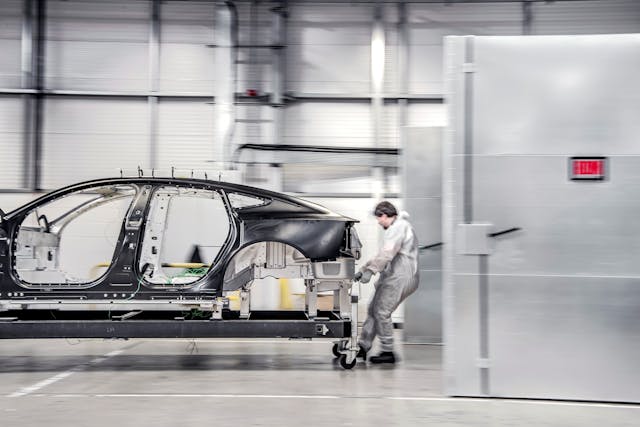
While the Polestar 2 used stamped steel for its chassis, the 5’s bones will be made from bonded aluminum. It’s an appropriate, weight-saving upgrade for a halo model and falls in line with the vision of Polestar’s U.K.-based R&D team, headed by Pete Allen, who says: “We knew we wanted this car to be light-weight, we knew we wanted high quality and we knew we wanted it quickly. This architecture delivers outstanding dynamic and safety attributes, with low investment technology applicable to high production volumes.” Which plant will build the 5 is so far under discussion—it could be at the Polestar Production Centre in Chengdu, China, at the Ridgeville, South Carolina, facility which Polestar shares with Volvo, or somewhere else entirely.
Even for a high-dollar, high-tech model, it’s still in the marque’s best interests to minimize cost, one of the main advantages of steel over bonded aluminum. Polestar’s breakthrough with the 5 lies in a new, faster manufacturing process in which body and chassis are built at the same time. So far Polestar has no plans for other models beyond the 5 to use this aluminum skeleton, but, as Steve Swift, Polestar’s director of vehicle engineering, tells us in an email, lessons learned from the overall construction technology will absolutely be applied to future models.
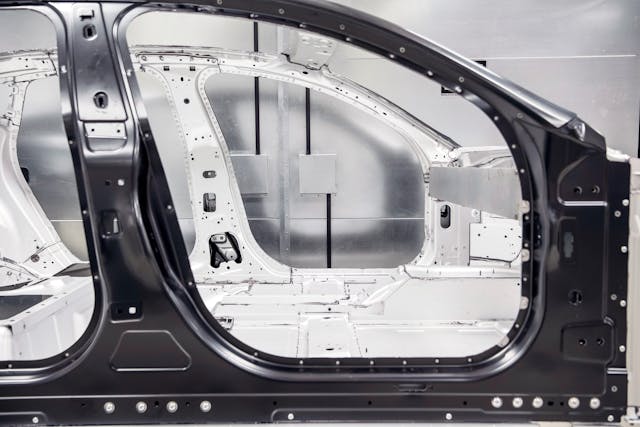
Polestar makes a point of touting the aluminum platform’s torsional rigidity, a characteristic that should only be amplified by the batteries destined for its belly. Though Swift is keeping mum on specific benchmarks, the four-door 5 should rival shorter, two-seat sports cars and even supercars for skeletal stiffness. Polestar also reports that the body-in-white, comprised of the platform plus the body, is similar in weight to much smaller cars.
Marketplace
Buy and sell classics with confidence
Expect the final product to borrow heavily from the svelte Precept study. Swift says the dash-to-axle ratio of the 5 will hew closely to that of the concept car, lending front proportions closer to Tesla’s luxury-focused Model S’ than the stubby-nosed Model 3.

Developing an in-house platform from scratch is no mean feat, and it says much about Polestar’s ambitions to establish an identity outside Volvo. We can’t wait to see the finished 5—and we’re even more excited to drive it.