Media | Articles
How Caterham Is Racing Forward in Its New Factory
Parked outside a standard-issue industrial unit in the town of Darford in the U.K. are two gleaming race car haulers. Like the building itself, they proudly display “Caterham Cars” on their flanks.
The racy introduction to Caterham’s brand-new factory sets a theme for the 54,000 sq ft facility. Meeting rooms are named Paddock Hill, after the infamous off-camber corner at the nearby Brands Hatch circuit, and Gravel Trap—because that’s where you end up if you don’t make it into Paddock. The administrative offices are Race Control, there’s also a Fan Zone merchandise shop, but it’s only once you step out onto the Terrace overlooking the production floor that it’s clear just how transformative the move to the new building has been.
“We were 36 years in the old factory and it was like a working museum,” says CEO Bob Laishley.
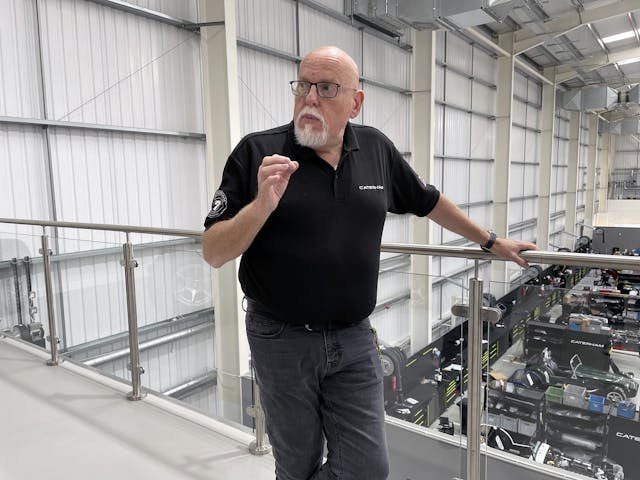
Now, however, the Lotus Seven-derived lightweights are all assembled in a gleaming white environment that looks like a modern F1 facility. In each of 33 bays, a single technician assembles a car from around 1500 components. Ask Laishley how long it takes to build a Caterham and he answers candidly, “I don’t know.”
That’s because each builder has his or her own methods and each car is unique. There is, however, a target of two cars per month per engineer, which would allow Caterham to build 750 cars in a year—up from 500 in its old factory.
Marketplace
Buy and sell classics with confidence
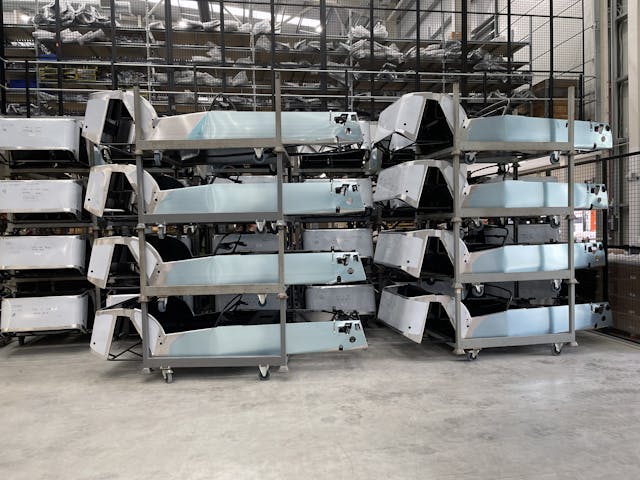
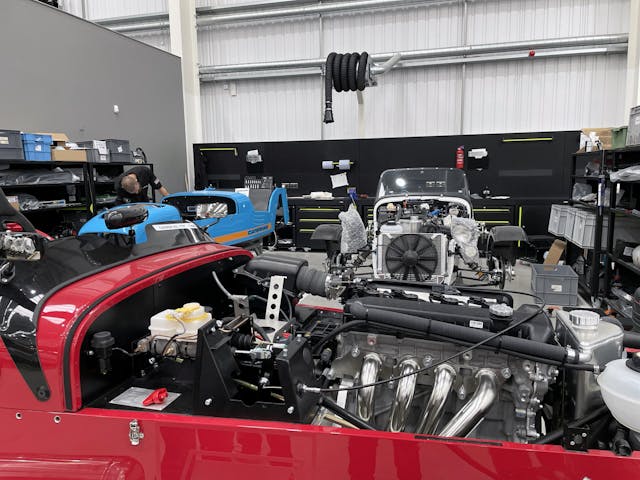
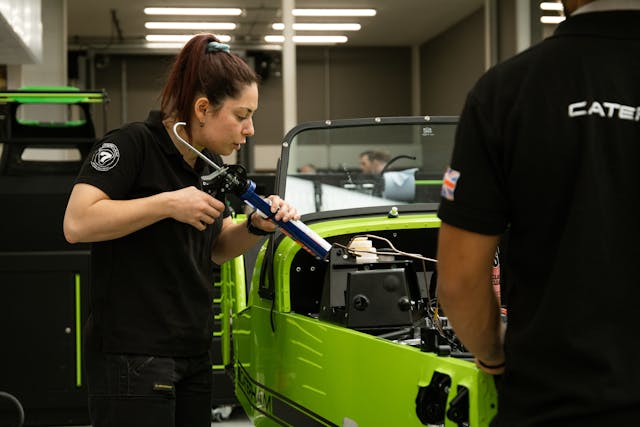
The chassis come in from a separate facility in Westbury, Wiltshire, some 140 miles away, while engines are supplied direct from Suzuki in Japan and Ford in Mexico. After assembly, the Sevens are shipped all over the world. While the U.K. remains the company’s biggest market, Caterham’s Japanese owner is taking delivery of more and more cars, there’s a healthy appetite in Europe and a growing enthusiast base in the U.S.
Although by far the majority of Sevens leave the factory fully-built, around 20 percent of British buyers choose to build them at home. All cars bound for the U.S. are in kit form with powertrains having to be sourced locally.
Laishley says he’s looking closely at the Replica Act to export complete cars to America, but having observed the difficulties Morgan has had to homologate the Plus Four, he’s in no immediate rush. “Thankfully we have another route into North America which doesn’t have a limit. But we haven’t exploited North America, because we haven’t had the capacity to build cars.”
That’s already changing with the new plant’s capability, as evidenced by a whole line of brightly-colored part-built cars awaiting shipping to the U.S.A.
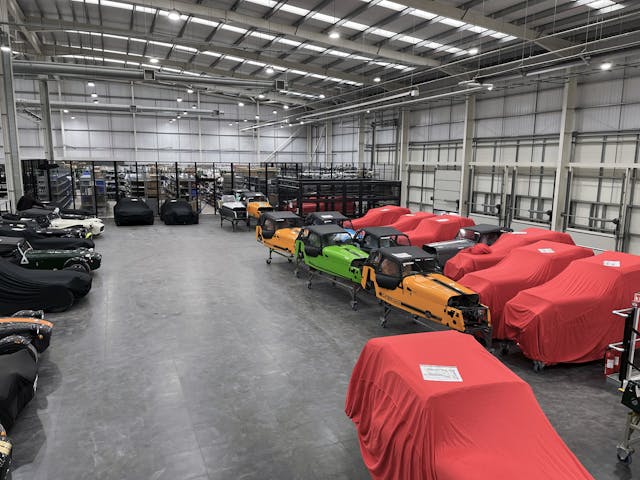
Some buyers, notably in Japan, like the look of bare polished aluminum, harking back to Colin Chapman’s original, but most Sevens go through the state-of-the-art paint shop where Laishley insists the finish is better than you’ll find on many supercars.
“Our guys are amazing, just feel that hand-painted stripe,” he says. And yes, the transition between racing green and yellow on the finished nose cone in question is indeed almost imperceptible.
There is clearly a pride and a passion here in the factory, with many employees devoting their whole working lives to Caterham. Others are just starting through apprenticeships and training programs. With a commitment to building internal combustion-powered Sevens here for at least the next decade, those jobs look secure as well.
If there’s one fly in the ointment it is the question of what will power future Caterham cars. Currently around one-fifth of production leaves the factory with a little 660cc Suzuki three-cylinder turbo engine, and the rest feature two-liter Ford Duratec units in various states of tune. Those are now out of production, but thanks to the financial backing from Japan, Caterham has bought enough for the next three years.
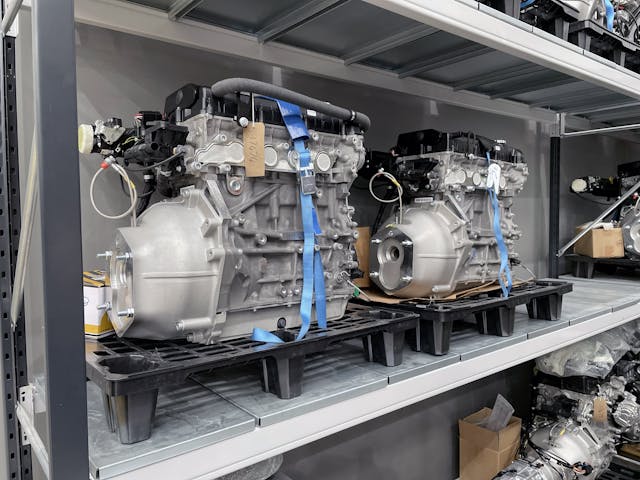
After that “We are looking at five or six different engine options form four different manufacturers,” explains Laishley. “And we have completely shifted from buying old engines at the end of their model lifecycle to something that is not even in production.”
Caterham owners tend be loyal, keeping their cars for many years, so getting buyers to upgrade or replace their Sevens is a challenge for the British firm.
For many years it’s the company’s race programs that have been the strongest path to repeat purchase. In the U.K. there are five rungs on Caterham’s racing ladder and as drivers progress upwards they need to upgrade. Around 200 Sevens are registered as race cars in the U.K., with 160 competing on a typical weekend. There are dealer-run series in France, Portugal, and the U.S. as well.
Those drivers know all-too-well just how fun these little cars are, but getting new people to experience the joy of light is a key part of Caterham’s plan for growth. That’s why there’s a fleet of cars available for track day hire, drift days or rental for road use.
The company is also opening the factory doors for tours, and tickets have sold out until the end of 2024 already.
As Caterham enters its sixth decade since buying the rights to the Seven from Lotus, there’s a sense of renewed vigor within the walls of its new facility. Long may it continue.
***
Check out the Hagerty Media homepage so you don’t miss a single story, or better yet, bookmark it. To get our best stories delivered right to your inbox, subscribe to our newsletters.
No mention of the Project V?
Project V won’t be built at this factory and is being developed under a separate company which is why it wasn’t mentioned here.
The factory looks quite nice. Fun cars!