Media | Articles
Restoration Shops Today Face Major Challenges
Keeping classic vehicles up and running isn’t always easy, and these days, that’s just as true for shops as it is for DIYers. I recently talked to four owners or operators of restoration shops to find out what their top business challenges are in 2024. Some of the answers I received were not a surprise. Frankly, everyone has been talking about finding qualified labor in almost every field. But some of the answers I got were eye-openers.
Every independent restoration shop operates differently. Some shops are very well-established with a long track record, and a few have major national or worldwide concours wins under their belts. Some are more focused on their local area, building a reputation as well as a customer base. Many shops also tend to specialize in a particular field, such as engine and transmission rebuilds, paintwork, or a specific type or decade of cars. In 2024, even full-service shops tend to utilize independent rebuilders or repair shops for specific skills such as radiator repair and rebuilding, powder coating, or rebuilding clocks or radios.
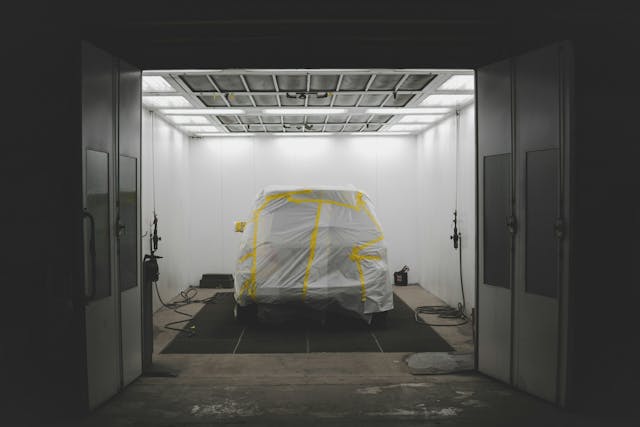
The repair, not just restoration business is also thriving at many restoration shops. Those services that might have been handled by a local service station 20 or 30 years ago—tune-ups, hose and belt replacement or air conditioning repairs—now represent part of the day-to-day work docket of many restoration shops.
Adam Hammer, owner of Hammer and Dolly Automotive Restorations LLC in Traverse City, MI, sees the value in doing many of the small jobs alongside the full restorations that they also perform. The “small work adds more volume, and helps to make sure that everyone in the shop keeps busy” says Hammer.
Marketplace
Buy and sell classics with confidence
Hammer, a graduate of the McPherson College Automotive Restoration program, has been in business as Hammer and Dolly for 13 years, has 10 employees and offers services ranging from full restorations to maintenance. Challenges include increasing costs for parts and equipment, as well as labor. In addition to increased cost, backorders for those parts is also an ongoing issue. Hammer also mentioned environmental challenges, as some regularly used compounds such as paints and solvents are no longer sold, making substitutions, often seen as harder to work with, a necessity. As to finding qualified workers, Hammer says “find the right person with aptitude to grow the skills, and we can teach the skill.”
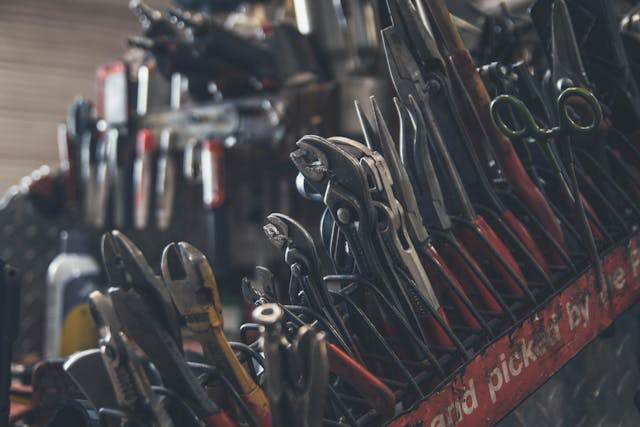
Husband and wife Ed and Melissa Sweeny are the co-owners of Proper Noise, LTD, a restoration shop located in Mount Penn, PA that specializes in both postwar British and Brass Era cars. In business for seven years, there are six employees including the Sweeneys. They specialize in the mechanical side of a restoration, and will outsource paint as well as some other areas of restoration if needed. When asked about current challenges, Ed focused on a few areas such as the quality of parts that they source from vendors. The issue is serious enough that Sweeney has turned in-house to scanning and 3D printing parts when necessary. Another challenge? Finding correct tires post-pandemic for those cars that use odd sizes, including many of the Brass Era vehicles he works on. “No one can go into production for just a small amount of tires, making it too expensive for the supplier, it becomes impossible for them to make any money,” says Ed.
Another problem facing all of these small shops? “It’s always hard to say no to clients, but sometimes scheduling work can be very tough.” Sweeny is talking about “job creep”, where a car comes in for brakes, for example, but, upon inspection, tie rods and shocks and more are needed, turning a few days repair into a week, or longer.

Mechanical Arts, located in Tenants Harbor, ME, is owned by Philip Reinhardt, also a recent McPherson College graduate. In business for four years, the shop has three employees. Specializing in repairs and restorations of pre-1980s vehicles, with a sweet spot for cars of the 1930s through 1960s, Reinhardt is facing another common problem in the restoration world: Running out of space to work on client’s cars. Their 3000 square foot shop is overwhelmed with customer cars, forcing staff to “play musical cars.” Although he characterizes this as a “good problem to have” Reinhardt hopes to expand soon, with plans to more than double the size of Mechanical Arts. Reinhardt also sees the “job creep” on client cars which can make effective scheduling tough. “Maine doesn’t have a State Inspection for older cars, so a car coming in for a routine service can have a completely worn out front-end” said Reinhardt. This type of problem is especially important to owners who are new to the old car world, some of whom have grown up in an era when going 10,000 miles between services is expected.
Finally, Eric Peterson is the manager of Leydon Restorations in Lahaska, PA, a shop that has been in business for just over 50 years. Peterson has worked there for 16 years, and been manager for 13. Leydon is known almost exclusively for mechanical restorations, which you can expect to see (or hear) at concours lawns around the globe. Peterson has a bit different take on finding talent. With the advent of television “rebuilder” shows and pop culture expectations of the mythical 30-minute total restoration, occasionally managing expectations of potential new hires is a challenge. “The realities of the work-a-day life at a shop is much different than what some might expect. You can’t have someone who is only interested in the glitz and glamor side of the restoration.” That said, Peterson reminds us that good people are an investment, and that he feels very fortunate to have a great crew aboard.
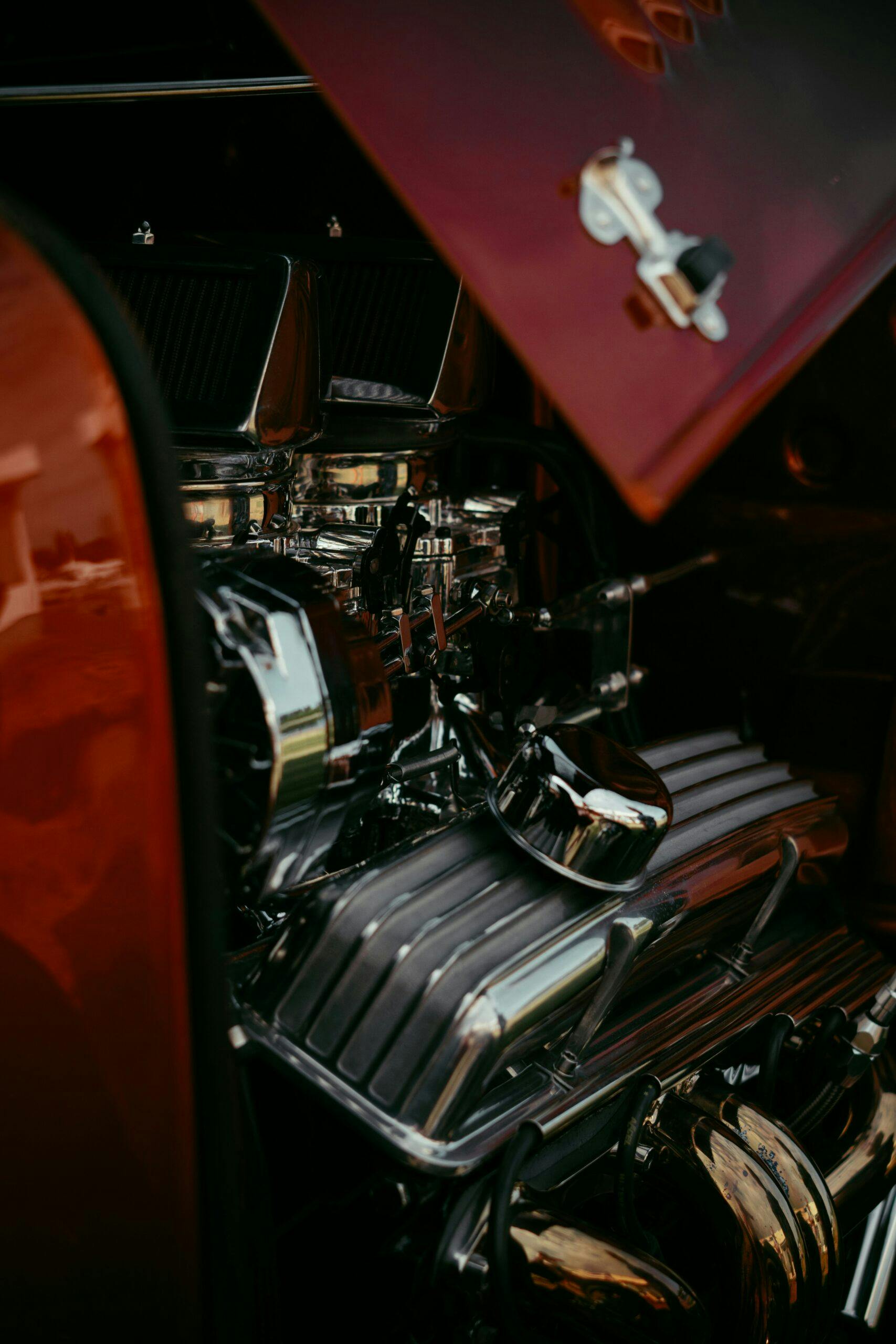
Like other shops, Peterson laments the quality of parts that are currently available. “The quality keeps getting worse. I have one car that has had three ‘bad from new’ condensers. Few things are of the lasting quality (that we used to see). Manufacturers are just looking for the cheapest way, the least expensive supplier. Charge us more the first time if you have to, but give us a part that works!”
Peterson also brought up a theme that ran through just about all of my discussions with restorers. Perhaps the biggest problem facing restorers in 2024 is simply finding the right specialty shop that can do the smaller jobs that used to be easier to farm out. A town that used to have three, four or five radiator shops might have one remaining. The owner is usually older, too, and often looking for someone to take over. It’s the same deal at a radio repair facility or that automobile clock repair shop. Finding someone who can reline brakes, grind cams or even make replacement keys is becoming increasingly more difficult.
The takeaways are twofold: For the consumer, understand that constraints are tightening for the shops that keep your ride on the road, so once you’ve found a good one, be patient with them. For the entrepreneurs who might be reading: Perhaps you should set your focus on becoming a specialty supplier. Find a need and fill it. And do it soon, because the demand is strong.
***
Check out the Hagerty Media homepage so you don’t miss a single story, or better yet, bookmark it. To get our best stories delivered right to your inbox, subscribe to our newsletters.
Folks need to understand that most restorations are money losers if you hire everything done. If you want a nice restoration, know up front that quality paint and body work costs a lot — and that’s a skill most of us don’t have. You can ease the pain a little if you can do mechanical work, normal repairs, lay your own carpeting, etc. However, picking the right car is probably the most important thing. You can afford to paint the 1967 Shelby you bought 30 years ago — likely not the small-engine 1964 Olds Cutlass you just inherited. Do the Cutlass if you have enough money and you are still in love with the one your grandfather had. If not, its a hobby — and hobbies generally cost money. For example, compare the restoration cost (and money loss) to that trip to Europe you’ve been wanting to do. Which will bring you the most satisfaction?
Is it any wonder that most guys just drive rusty and unpainted cars, at least until they get a little older and can find the time and gain the experiance to complete most of the work themselves
Sure makes sense – and that’s the guys who invented the “patina” craze.
Restoration shops should have a model where classic car owners can rent space in the facility and do their own work. There would be a couple of qualified mentors to teach to teach/coach the owners the skills necessary to work on the car and how to behave in a shop, handling of tools, etc.
Yes the biggest problem I have is getting good parts. Notice I say good parts, I’ve had to lower my expectations in quality. I don’t know how any shop can make it when they have to do the job twice because of bad new parts.
I bought a cool resto-mod Lancia with a K20 six speed swap on auction for $10K as a project car spent 18 months and another $10K and got only $10K from the resell on auction ( no reserve) I will never do the no reserve thing again
The loss of old school radiator shops was mentioned. Which is the case in my area. Also machine shops by me dried up. Used to have an old school machine shop by me that could do anything grind crankshafts, head work,boring cylinders,cam bearings,etc. at a reasonable cost. They had several employees and they always had a ton of work. Not sure why they closed shop
For me in my simple garage it’s definitely the quality of parts that is the toughest thing to deal with.
Even brand name stuff has gone waaaaay downhill over the last decade or so. Spark plugs shouldn’t be a problem from a reputable company who has been making the same plug for literal decades, but apparently that’s too much to ask nowadays. The same is true for points. I had quite a time setting my point gap and couldn’t figure out why I was unable to get it. I finally realized that the stamping was bad. Whenever I’d tighten the screw it would move because the bottom wasn’t flat, but convex where the screw mounted it. Having to break out a hammer and punch to make points work is not exactly good testimony for your product. 🙁
I don’t want to sully names, but Suffice to say I’m happily putting NGK plugs in my old VWs from now on. 😉
Great comments reviewing the author’s take on the business of restoration today.
I’m an amateur restorer only doing cars pulled from my collection of 40+ years.
I understand as a non-professional my labor times would be longer but that said it’s still remarkable the amount of time needed to do a proper restoration. Today one either restores a car for the love of that particular car or if the car, when complete, can easily be resold for a 6 figure amount. Depending on the restoration that may not even cover the bill .
As the financial toll gets even bigger it looks like many of the “mid field” classics will never get a chance to get restored, only to be relegated as parts cars.