Media | Articles
The world’s smallest automotive rotary was built to save lives
If someone asked you about the smallest rotary ever used in a car, what machine comes to mind? An NSU Prinz? Maybe one of those CERV Corvette prototypes that played with a mid-engine Dorito-spinner? Surely a litany of Mazdas is on the tip of your tongue.
Of course, I’m leading you on. It’s none of those—in fact, it barely qualifies as an engine, though it does operate using internal combustion. Hidden in the back seat of many 1994–2005 Volkswagens and Audis sits a tiny Wankel rotary engine whose sole duty is not to turn fuel into horsepower and braps but to save the life of a person.
When VW/Audi introduced the B5 platform in 1994, the all-new chassis showcased the German automakers’ engineering prowess in the mid-’90s. Safety was one of these models’ main selling points, and while Mercedes-Benz was the first to introduce a pretensioner in 1981, Audi brought its own innovative solution to the table in 1986 with the insane Procon-Ten system. For context, Mercedes had introduced a fairly conventional pretensioner—a device that pulls the belts tighter during a crash to reduce the chance of an occupant coming out of loose belts—that utilized a small, explosive-charge drive mechanism to rotate the seatbelt’s spool and thus tighten the belts against the driver. Audi used a series of cables and pulleys tied to the engine. Audi engineers figured that, in a hard frontal crash, the engine would be the first major component to take the brunt of the hit after the bumper deformed.
In more aggressive impacts, the engine is typically dislodged and shoved back in the chassis—especially when that engine is placed as far forward as Audi’s longitudinally-mounted units. With the cables attached from the driveline to the seatbelts and steering wheel, Procon-Ten would use the dislodged engine’s inertia to pull the seatbelts tight while also pulling the steering wheel away from the driver. This design was intended to eliminate the need for a steering-wheel-mounted airbag, but the wholly mechanical system proved less than predictable.
Enter a 1995 patent granted to Thompson Ramo Wooldridge, Inc. (TRW) for a Wankel-based pretensioner, which was first used in the B5 platform. Typical seatbelt pretensioners, even today, use a linear motion to either pull the seatbelt’s buckle itself or to rotate the spool on which the belt is mounted. This linear style relied on a small explosive and a piston to create the mechanical force, but despite its simplicity, this sort of pretensioner was bulky; the piston’s ability to tighten the seatbelt in an accident correlated directly to the distance it could travel within the unit. TRW’s solution was to build a tiny Wankel rotary that could replace the larger, linear piston designs, and while it’s not ultimately part of the driveline, it’s the smallest Wankel ever installed in an automobile.
Marketplace
Buy and sell classics with confidence
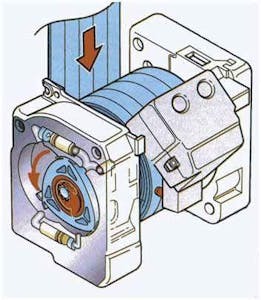
TRW’s clever design used no electronics and was entirely independent of the front airbags and pretensioners. Instead, it operated on many of the same principals as a firearm. The seatbelt’s bracket acted as a safety: when the belt was in use, it pulled a cable-actuated block on the firing pin inside of its inertial trigger, allowing it to strike the first of three explosives cartridges inside the rotary housing.
We don’t suggest you try this at home, but for your viewing pleasure, here’s a deep-dive into the tiny Wankel:
The Wankel tensioner is to the left, the inertial trigger is in the middle, and the seatbelt’s spool is on the right.
Inside the inertial trigger, there’s a weight that’s suspended by plastic struts designed to break away at a predetermined impact force. The spring is for the firing pin mechanism, which is released when the block breaks but can only strike the initial explosive cartridge if the seatbelt is bolted to the car.
With the housing split, you can finally see the heart of the mechanism, a familiar oblong combustion chamber. Just like a Wankel engine, the TRW pretensioner uses a rotor, eccentric shaft, and carefully placed ports to spin the seatbelt spool.
The rotating assembly consists of three main components: the rotor, which is lined in a high-durometer rubber to act as the apex and side seals; an eccentric clutch which engages the output shaft via a set of spring-loaded teeth once the pretensioner is fired; and the output shaft itself, which engages the seatbelt spool and free-spins with it until the pretensioner is fired.
Possibly the wildest part of the mechanism is its power source, a series of three cartridges that are very similar to firearm blanks (they even measure approximately 9mm in diameter). This particular one shown is the third stage, but the first stage (which is struck by the firing pin of the inertial trigger) is just below it and shares the “intake” port into the combustion chamber. The second and third stages are fired passively during the crash event by utilizing the exhaust pressure to push the plunger that sits just behind the cartridge. The D-shaped port in the housing is the exhaust port, which dumps spent combustion gasses while the rotor spins.
Pulling back the camera, we’ll walk you through the operation. Once the first charge is fired, the rotor begins spinning counter-clockwise as the rapidly-expanding gasses enter the lower-left. As the charge spins the rotor a third of the way around, the apex seals eventually reveal the next port and allow it to push the plunger into the second stage. After the first cartridge fires, the rotor turns another third of the way around and reveals the firing port for the third and final stage. All of this happens in a fraction of a second in what sounds like one big pop as the rotor spins the toothed clutch that acts as the eccentric shaft, thus engaging the seatbelt’s spool.
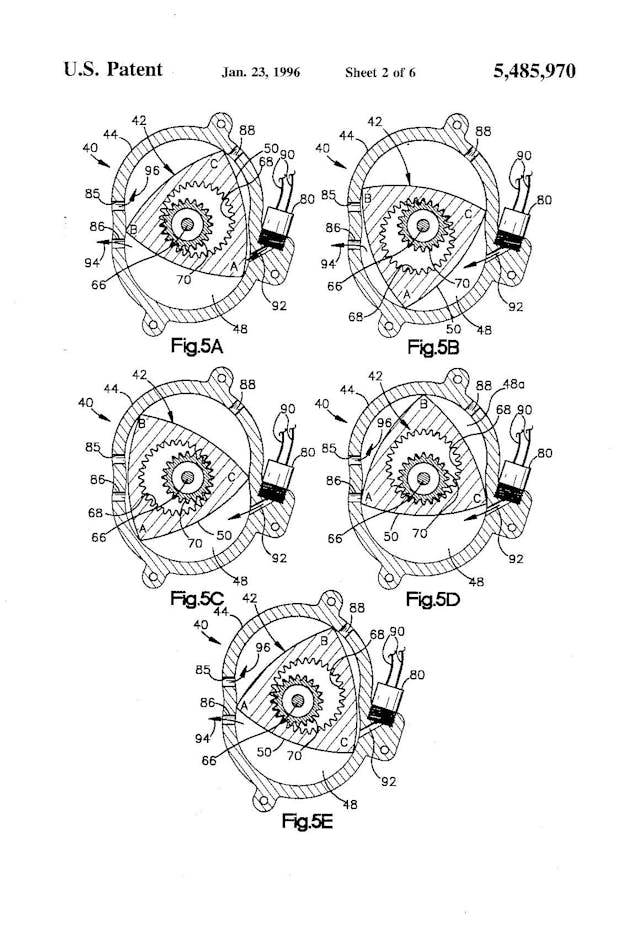
This was a marvelous solution from TRW, and VW and Audi were well ahead of the competition in using pretensioners for back-seat passengers. Airbag systems at the time were not as sophisticated as they are today; very few even disabled the passenger airbag for children and other underweight occupants who could be injured by the airbag itself. By creating a passive system, TRW’s design allowed for a simple airbag control routine to be handled by an electronic module while these rotary units hid in the back seat. It was compact, self-contained, and served duty in millions of Volkswagen and Audi sedans throughout the ’90s and into the 2000s.
So there you have it, the world’s smallest automotive rotary. You could call it an engine, we suppose—it’s an internal combustion machine which turns burning fuel into rotational motion—but either way, it’s one more fascinating piece in the legacy of Felix Wankel’s unorthodox design.
Zoom Zoom seat belt tensioner?
This a great application for a Wankel, it only runs once for about 2 seconds so no tip seal wear issues, it’s tiny and it’s powerful. The blank cartridges are a miniature version of the 12 gauge size cartridges used for aircraft engines and old diesel tractors.
I owned three different vehicles that likely had these installed (and one prior that had the Procon-Ten), but of course, never new it before today. I remember the seat belt pretensioner being touted as a safety feature in the first of those three Audis in 1994, but I always assumed it was a simple system that merely locked the belt in-place rather than actively recoiled the belt.