Media | Articles
Ohm me, ohm my: Spark plug wires demystified
Fuel, air, compression, and spark. Those are the four things a gasoline-fuel engine needs to run properly. While it sounds pretty simple, the reality is that even vintage engines are quite picky about how each of these four items is attained. Today, let’s dive into spark plug wires and the developments in technology that these simple conductors have experienced over the years.
That’s what a spark plug wire is—a conductor. At its basic level, the spark plug wire exists solely to transmit electricity from the coil or distributor to the spark plug. Over the years the demands on these humble wires have increased, and thus the technology wrapped into them has also advanced. Now the market is flooded with options when it comes to plug wires. We’re here to help you make sense of the features and technology out there.
Size matters—but not in the way you think
The spark needs of a stock 216-cubic-inch inline-six Chevrolet are drastically different than those of a supercharged big-block Ford. Plug wires are often advertised by the diameter of the wire, making it easy to look at the options for plug wires and immediately think if 7mm is good, 8.8mm must be great. There is more to consider though.
Those larger wires typically have a lower resistance per foot—and this, not size, is the key thing to pay attention to. Plug wires of larger diameter could simply have larger conductors inside the wires, but their size could also be due to other features. Early spark plug wires were very simple—just metal that conducted. There wasn’t even insulation. The automobile had been around for at least 50 years when my 1930 Ford Model A was built, and guess what, it’s plug wires are just straps of metal from the distributor to the plugs.
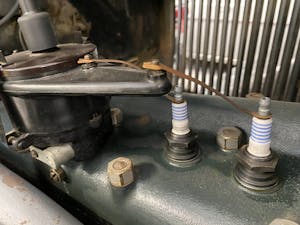
Those simple conductors evolved to require insulation to shield the ever-increasing voltage from jumping to an unintended ground rather than through the spark plug. Not only did insulation join the features list for plug wires, increasing use of electronics as the decades wore on required the development of EMI and RFI suppression. Electromagnetic and radio-frequency interference can be a real pain in the butt. The most common instance of radio frequency is the phenomenon that occurs when a home mechanic replaces the plug wires on a vintage car and afterwards the radio has a pinging noise whenever the driver turns on sweet tunes while the engine is running. That pinging noise is the radio-frequency interference from an uninsulated plug wire.
Marketplace
Buy and sell classics with confidence
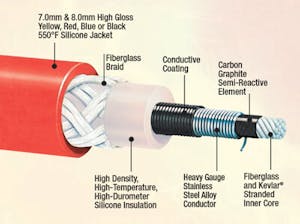
The EMI and RFI suppression keeps the electrical noise of the ignition charge moving within the wire to a minimum. That electrical noise can wreak havoc on everything from AM radios to engine and transmission control computers. So if a little insulation is great, more must be better, right?
Resist the temptation
Yet again, not quite. Like everything in life that is good, that insulation has side effects. The side effects are resistance and cost. The resistance of many wires is measured in ohms per foot. A wire with high resistance can be in the 5000 ohms per foot range for especially high-output ignition systems, whereas a low resistance performance wire could easily get double digit ohms per foot. Lower resistance means more of the ignition coils energy is going towards bridging the gap or the spark plug. That hotter spark can create a more even burn of the fuel/air mixture in the cylinder, and thus, more power output from the engine.
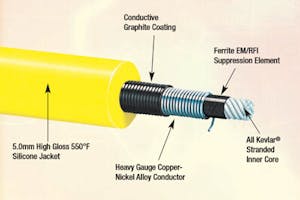
Also, all the shielding inside a wire is not free. The best spend of your money is to buy a wire that protects against just enough interference to keep the rest of your car functioning properly—but no more. That is a tough balance to strike on modern computer-heavy cars, or even racers with sensitive data logging equipment. For stock applications, an OEM-spec wire might be best despite it having greater resistance than an aftermarket wire.
Ignition systems which use a magneto are often best served by the lowest resistance wire possible. The higher voltage of a coil on plug or distributor system can create enough voltage that a slightly higher resistance wire will not greatly affect spark strength, but the relatively lower output of a magneto means using a lower resistance wire is more important to ensure a hot spark from the spark plug.
Get the connection right
Once you have your wire chosen, you’ll need to connection the distributor cap (or coil, for coil on plug applications) and the spark plugs. There is often the option to purchase pre-terminated wires, where the wires have been cut to the proper length for your application, but if you have something custom or want a cleaner appearance than factory, building your own spark plug wires might be the way to go. High-temperature-rated boots might be required if you have headers or other routing that puts the sensitive wires near a strong heat source—mainly the exhaust. Headers are notorious for causing problems, so invest in some extra insulation to prevent your new wires from literally melting down.

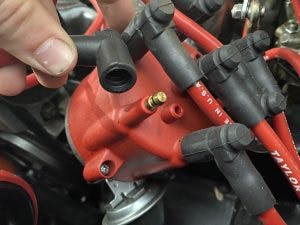
It’s not a difficult process; it just takes a bit of patience and attention to detail—like any other automotive project. Installing new plug wires is a part of most basic tune-up to-do lists, and if your favorite cars wires haven’t been changed in a decade or so it might be time for you to start shopping. If you have any additional tips, be sure to leave them in the comments below.
I have a question (ignorance) why are modern GM LS engines with individual coils required to have a specific set of spark plug wires coded to the number stamped into each coil? Thanks
I didn’t know this was a thing, mostly because all the aftermarket ones I see do not have numbers on the individual wires. If this was a really important thing, you’d assume the aftermarket wires would also need those numbers?
Most oem and oem replacement spark plug wires are cut to specific lengths to neatly reach each cylinder, so they’re numbered accordingly. Sort of making installation idiot proof.
Sorry for the double post. I meant to reply directly before.
I’m having a hard time keeping wires from burning 🔥 up, the passenger side where my 80mm Turbocharger reside. Just belowi the Turbo is the header very close to the wires I need help to stop destroying 😫 the wires on that side, Any help please.
I don’t know if it will help but I had similar failures on a Chevy 454 in a motorhome. Then I found that UPS had found a source of ignition wires that would handle the heat in their vans with 454s in them. I got a set, and my failure problem disappeared. I bought them while on vacation in the UP.
what brand were they
Have you tried the Taylor ThunderVolt 50?
https://www.amazon.com/Taylor-Cable-98026-ThunderVolt-Ignition/dp/B000CQ25P0/ref=dp_prsubs_2?pd_rd_w=toVuE&content-id=amzn1.sym.ec3cee7c-6bd8-496a-8166-4fdb6d51cad1&pf_rd_p=ec3cee7c-6bd8-496a-8166-4fdb6d51cad1&pf_rd_r=E417R4TBV7GE0PD58ZZV&pd_rd_wg=m8DKO&pd_rd_r=2df4de53-8d15-4deb-bb9c-399a58142ae4&pd_rd_i=B000CQ25P0&psc=1
You may also need to install heat shields, on wires and the turbo.
https://www.summitracing.com/parts/sum-350160red?srsltid=AYJSbAe5ijpPqJXHsVRSvH4kDWCWCZgYbqT5-lo9tYYdO7bIFnDzX-JDimY
You could purchase a set of wires to cut and crimp yourself. I’d reroute them away from the heat source. Also, a few companies (I use DEI on my Rx7) makes spark plug wire heat shields that attach via heat shrink. They’ll protect from direct contact up to 1800°F and radiant heat up to around 2500°F.
If your running stock manifolds, where are your heat sheilds, if headers then routing is key.. BUT you can also source quality wires from Blue Streak with ceramic boots, and others like Accel. These wire will make all the difference.
Boy if we can put Re heads together , we can make this happen. 🙏🙏🙏🤔😊
Most oem and oem replacement spark plug wires are cut to specific lengths to neatly reach each cylinder, so they’re numbered accordingly. Sort of making installation idiot proof.