Media | Articles
Is Your Battery Impact Better Than Military Grade?
Some of the most innovative technology has come from the efforts and minds who help defend the U.S. from all enemies, foreign or domestic. There are many “tools” used to complete that task and, just as important, there are tools that maintain those implements. Given that an M1 Abrams weighs over 70 short tons, you’d think the tools needed to keep it up and running would be massive and high power. You’re half right.
Thanks to the Torque Test Channel on YouTube—one of my favorite places to learn things I don’t really need to know—we get a glimpse of what “military grade” tools really are. Having grown up next to a military base, I’m familiar with the jokes about what “military grade” means. Often it boils down to clarifying that the item is purpose-built, to a price point, with tolerance for misuse heavily considered.
That explains some of the electric impact’s strange features, if you would call them that. A bulky NATO connector ensures the tool can only be powered by a consistent 24-volt electrical system like the twin batteries of a Humvee. Torque Test Channel overcomes this with some crafty wiring and a couple of adapters that look like they could be sourced at a military surplus store, if you can still find one.
With power sorted out, a socket was put on the anvil snout, and the whole setup was put on a dynamometer. The relatively clumsy tool struggled to reach 75% of the nearly 800 pound-feet that a consumer Milwaukee M18 battery impact could muster. A little embarrassing, until the consideration that this impact was designed for a relatively narrow set of tasks—servicing the tracks on the Abrams tank—and that might be all the power needed, with any more just increasing the risk of damage during use.
Marketplace
Buy and sell classics with confidence
It’s an idea and concept that likely shapes your tool selection when you grab wrenches or ratchets from the drawer while disassembling your latest project: Enough to get the job done. I don’t need a 2-foot breaker bar to remove the float bowl screws on my Corvair’s Rochester carbs, and if I tried it would likely be both a pain in the butt and increase the chance of stripping one. Instead, the proper tool sets me up for success. And I only work in extremely low-stress environments compared to what that impact might see. The inability to over-tighten is built into multiple parts of the toolkit, chiefly the torque multiplier that only allows about 150 pound-feet of tightening torque but is unlimited when working to break things free.
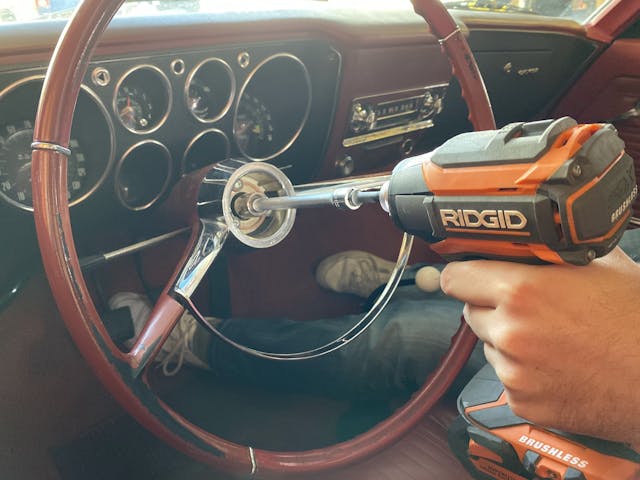
So yes, your tools likely are better than military grade, but that’s by design. It also underscored just how stuck the lugnuts on that rusty truck I worked on last week were. Poor thing needed everything my battery impact had and it was just a 1500 Chevy. I still can’t imagine working on a 70-ton vehicle. At least I know I’ve got the tools to do the job should I need to.
My M18 does it all.
I view impact tools with a degree of caution
When I was mechanicing and air power was still king, I used impact tools sparingly and primarily for the intended job of removing lug nuts
Now that everybody has these electric impacts, I see constantly the hazards created by the relative laziness of using them. Instead of wrenching bolts off and neatly organizing them, I see folks zipping them off and of course letting them fall on the floor or catching them until they get a handful and then plunking the handful on a bench. This inevitably leads to the ‘which bolt goes where’ and ‘where is that last bolt’ scenarios.
Then of course someone who is not willing to wrench bolts off certainly is not going to wrench them back on, so this leads to the inevitable snapped fasteners and cross-threaded tools. In my opinion, leave the impacts for the lugs and take your time. We aren’t getting paid by the hour to do what we do
While in the military, I used a hydraulic 1″ drive impact driver to deal with tank tracks. Rechargeable cordless tools weren’t very evolved before 1990.
One of the unusual off label uses for a cordless impact driver is trailer stabilizer jacks. The last time I rented a camper the owner had a 20V Dewalt in the toolbox.
I find the impact driver and power ratchet make it quicker and easier to do stuff, as long as you are aware of what needs to be finished with a torque wrench
The military one looks beefy. The power connector is a bit crazy for the average user.
Found out the hard way about using a impact driver to put wheelnuts back on – fortunately in the driveway before heading remote. Lesson learned about tools AND to carry spare wheel nuts and studs