Media | Articles
How It Fails: Shocks, bushings, and ball joints
Passionate about all things automotive and mechanical, Graham O’Neill grew up working on cars. He later opened, and for several years operated, a repair shop before deciding to instead focus on restomod engine swaps. His personal project: a V-8-swapped BMW Z3. We love the simplicity of the drawings he provided for this story. -Ed.
A suspension is critical to a car’s performance. Struts, control arms, the bushings holding everything together—they’re what keep your wheels on the pavement. The job of a suspension is much greater than simply “absorbing” bumps in the road, however. Next to tire grip, suspension design is the most critical factor in a car’s ability to put power to the ground.
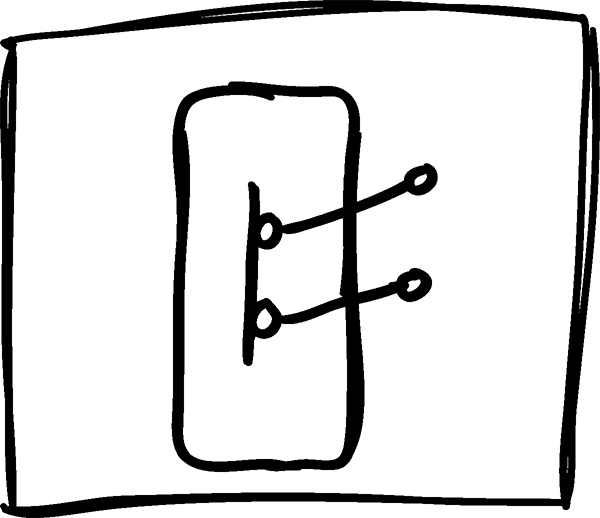
At the most basic level, suspension components work together to maximize the effectiveness of a tire’s contact patch—the ever-changing small section of rubber, at the bottom of the tire, that touches pavement. To facilitate acceleration, braking, and cornering, you want that patch to remain in contact with the road as often as possible.

Some suspensions are all but solid, like the trucks on a skateboard. Most, however, move up and down, within the car’s body, on a controlled path. When the car is loaded with passengers or cargo, when it enters a corner, when it brakes or accelerates, the suspension at each corner rises—it “compresses”—or falls—it goes into “droop”.
A simple double-A-arm independent suspension is shown above. The spring—the part that actually supports the car’s weight and holds the body off the ground—is not shown.
Marketplace
Buy and sell classics with confidence
The red lines in that image represent the path, or arc, traveled by the wheel hub as the suspension compresses against the car’s spring. That path helps determine how the tire is presented to the pavement. Which helps determine how a car rides and handles.
Simple, right?
Today, we’re going to talk about three types of components in this system and how they wear out. When these parts fail, your car’s acceleration, its braking, its handling—and most important, its safety—can be drastically altered.
Those component types are:
- Shocks: Also known as shock absorbers or dampers. They control, or damp, the motion of the car’s springs. (They do not “absorb” road shocks.)
- Bushings: The soft components, often rubber or polyurethane, that allow suspension parts to bolt to a car’s body or frame structure, and move relative to that structure, without binding.
- Ball joints: Spherical metal bearing joints, often packed with grease, often inside a rubber or plastic boot for protection. They do a similar job to bushings but work with far more precision. The downside is less give, or compliance, than a bushing offers. (Unless you’re building a race car, where comfort and passenger isolation don’t matter, you only want to use ball joints in certain places.)
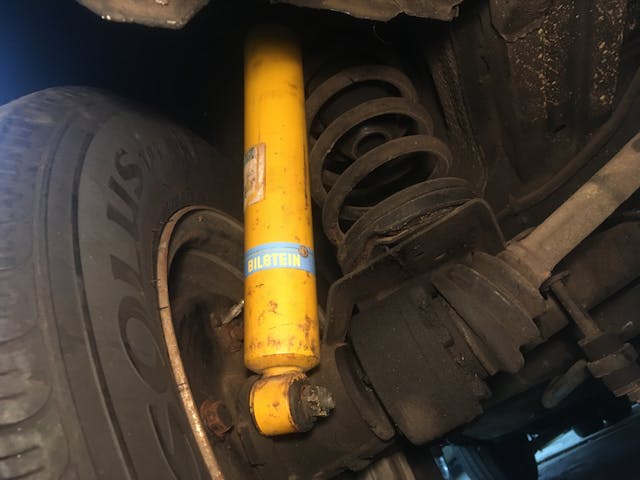
Shocks: How They Work
The automotive shock absorber is a more complex component than most people realize. We know they leak fluid from time to time, so it is logical to conclude that a shock’s inside contains that fluid. Beyond that, what’s going on?
Let’s take a modern, nonadjustable, non-electronically controlled, gas-charged, monotube passenger-car damper. This type of shock has been around for more than half a century, and it’s still the default answer for many new vehicles, import and domestic.
Most shocks attach to the car in two places: The top end bolts to the car’s body, and the bottom bolts to a part of the suspension that moves with the spring.
In the cross-section below, the car’s body is shown in gray. In our hypothetical layout, the shock’s bottom mounts to the wheel hub through two bolt holes.

As the spring compresses and releases under load, the shock must collapse and expand with it. See the two tubes, one inside the other? The inner tube moves up and down, but the outer tube—and the shaft attached to the piston—are bolted to the car, so they stay fixed.
The piston is basically a small disc. It travels up and down in the shock’s inner tube, its perimeter a close and sealed fit. The green stuff is that fluid from earlier, usually a type of oil. As the shock compresses and expands, the piston moves through the oil. The piston has holes in it, to let the oil pass.
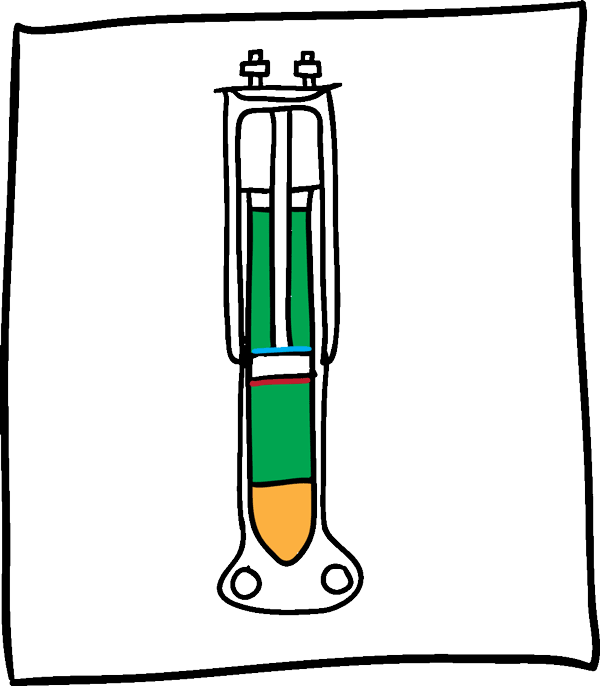
The rate at which fluid moves through those holes is governed by a pair of one-way valves. Those valves are represented here by the red and blue lines. One valve dictates how quickly oil moves through the piston when it comes from the shock’s bottom—that’s when the shock is being compressed. The other dictates how quickly the oil moves when coming from the shock’s top. That’s when the shock is being extended.
The gas reservoir at the very bottom is often nitrogen. In some shocks, the gas is there solely to keep the oil from absorbing air and foaming as it moves around and heats up. In other shocks, the gas does that job but also serves as a tuning element, to help refine the piston’s movement in certain conditions.
Because the piston is sealed to the side of the inner tube, and because the valves control how quickly oil can move through the piston, the valves dictate how the shock controls the spring. The spring wants to move, and the shock basically calms it.
Shocks: How They Fail
Now that we know how it works, let’s talk about how it comes apart.
The most common failure is when a strut is leaking oil. Remember, the piston shaft is bolted to the car and doesn’t move. The shock’s inner tube moves up and down around it. There is a small circular seal where the shaft enters the tube, to keep the oil in and dirt out.

This seal can fail for a few reasons, but it usually dies from age. This failure is rarely instant—the seal usually has a long, slow death, weeping oil onto the shock’s outer cover for hundreds or thousands of miles.
If oil is leaking, that means there’s less of it in the shock. Oil leaves the shock’s inner tube and is displaced by air, and air is compressible. This can cause the suspension to feel a lot “softer,” for lack of a better term. Alternately, if the shock loses too much oil and the piston runs dry, or if a worn seal begins to bind on the shaft, the shock will not move when “needed” to by the spring. In that case, you’re likely to get a harsher ride.
The other shock failure modes are often far more obvious. The rubber or spherical mounts that hold the shock to the car’s body and suspension can deteriorate and grow loose with age; this often results in a clanking, a creaking, or a moaning while turning at low speed. Hard curb or pothole impacts or other worn suspension components can bend a shock piston shaft, effectively seizing the shock and creating an extremely hard ride.
Regardless of how it dies or gets hurt, a damaged or worn out shock cannot control a spring as its designers intended. The result is less traction, less grip, less stability at speed, and greater braking distance.
If your car is bouncing, wandering, wobbling, or just plain feels loose and funky, ask your mechanic for a closer look.
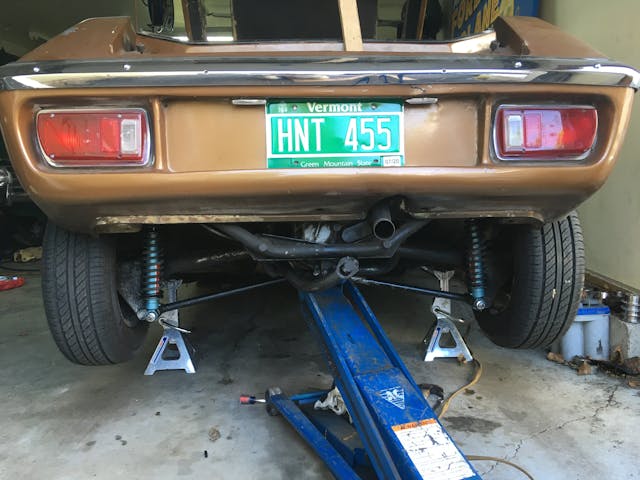
Bushings: How They Work
Spring and shock specifications can be changed to increase a car’s comfort level or its performance, but that’s only one part of the equation. The rest of the suspension needs to be isolated from the chassis.
This is accomplished through rubber bushings. In many cases, these bushings resemble a steel tube filled with rubber or polyurethane. The outside of this tube is pressed into or bolted to the car’s chassis or subframe. A second metal bush or tube is molded or slip fit inside the rubber or poly. Suspension components are bolted to or through that bush or tube.
A healthy bushing helps absorb and dissipate forces. It serves to locate suspension components while providing a set amount of comfort and precision.
Take a look at the drawing below. The brown is the bushing’s inner rubber. The white areas are air gaps, molded into the rubber and designed to allow flex in certain planes of movement.

The drawing below shows the top air gap closed—the bushing is in compression. Not all manufacturers use air gaps; some high-performance and/or luxury cars use molded-in pockets of hydraulic fluid instead.
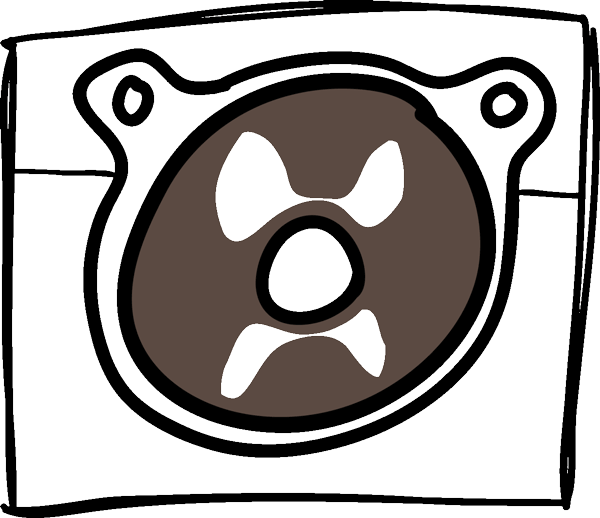
Bushings: How They Fail
The problem is, rubber changes with age. UV exposure, heat, and even just time all cause cured rubber to harden and lose flexibility. In the case of a bushing, that hardness means reduced ability to absorb and distribute force.
After enough time and hardening, the bushing simply cannot flex when it needs to. The rubber cracks and splits. Ride quality and handling worsen. After enough abuse, the bushing will come apart—the rubber will chunk and fall out, and the bolt holding the suspension arm will simply bounce and clunk around. (You’ll probably hear the noise. But you’ll likely notice, first, how the car doesn’t go where you point it.)
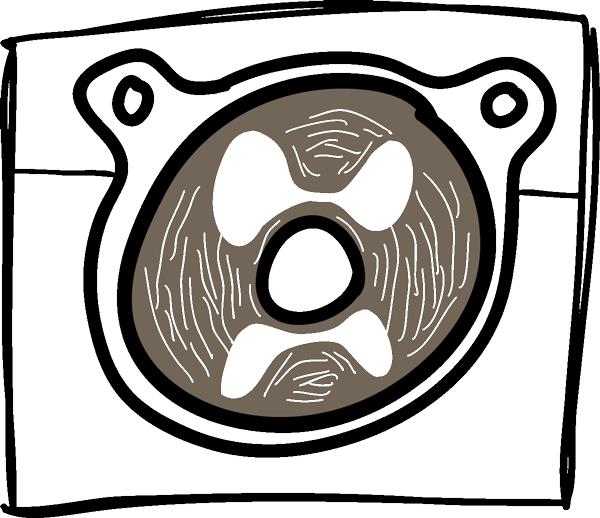
Bushing failure can be unnerving, not least because the car’s behavior grows unpredictable. The effect is compounded when multiple bushings wear out or fail at once, as they often do.
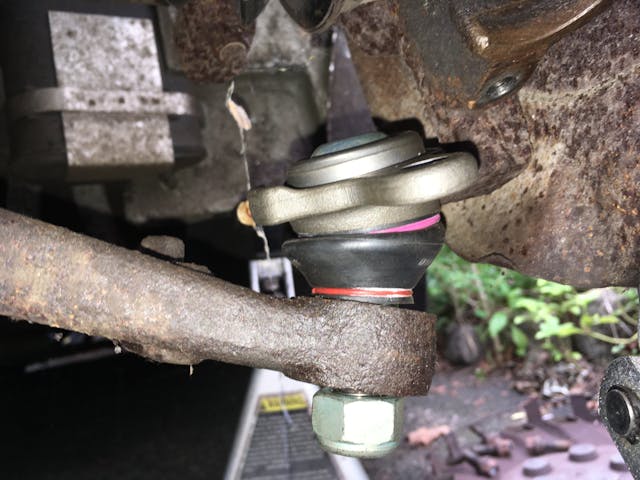
Ball Joints: How They Work and Come Apart
Ball joints are pretty simple: They consist of a metal ball running in a precision-fit socket. That socket is often lined with a composite or plastic sleeve, to extend the joint’s life and/or increase ride comfort. A threaded stud extends up off the ball, and suspension or steering components attach to that stud. The whole assembly is protected from the elements by a rubber or plastic dust boot or grease boot.
Steering tie rods are ball joints; some shift linkages are ball joints; most strut-type suspensions use a ball joint at the bottom. You’ve probably seen one, even if you think you haven’t. These are simple and reliable components, and, in modern cars, they’re fairly long-lived.
Ball joints usually fail when their protective boot rips. Dirt, debris, and water get into the joint. The water makes the grease less effective and promotes corrosion, and the dirt and debris grinds into the joint’s socket, increasing wear. After a while, this wear becomes great enough to cause the joint to move too much in the socket. It makes noise—often a clunking or squeaking—and the car begins to feel unstable while moving.
Check out the Hagerty Media homepage so you don’t miss a single story, or better yet, bookmark it.
How It Fails: Shocks, bushings, and ball joints by Graham O’Neill, 11 November 2022 is a great article. Short, informative and simple to understand. Keep ‘em coming’
I have a fairly rare 1998 chevy S-10.It’s only rare since it had to be custom ordered with a manuel 5 peed and their higher powered Vortec 4.3 liter V^. they normally don’t mate the standard to that engine. Did alot of pulling back then and it made parking in downtown gargages much eisier and expensive than the full size trucks but much eiser to park or make U turns. Other thann being able to lay straches anytime you had the urge in 1st second third and sometimes 4th gear very fun little extended cab to drive.
Biggest problem though was the computer still cuts the power at 98 or 99 mhdo to the governer I never reprogramed the computer for. The other was the larger V-6 loved to eat bushings due to being to close to the exhaust manifolds. After making my own tools for removal and pressing in new ones a couple of times. I went with stiffer urethane bushings and they are still going strong after 60,000 miles. although starting to show some play, and since it has lasted into classic status I get a nice discount on insurance. Totally sold on Urethane bushings now they are harder riding and with stand heat better than the cheap rubber ones.