Media | Articles
How Bilstein Makes Its Iconic Dampers
Plenty of car parts have an effect on the handling and ride characteristics, but the damper is critical in a properly functioning suspension. We all know the basic premise: A piston moves in a pressurized cylinder to help control compression and rebound, but do you really know what’s inside or how it’s built? Let’s take a look inside the Bilstein factory in Germany and find out.
The plant employs 180 workers and manufactures a whole range of products that start as raw materials before they are sorted and distributed within the building to various stations for processing. The facility is large enough to handle the entire process of turning raw materials into finished pieces, but too small to store many finished parts. That means delivery and pickup operations happen five times a day to keep everything running smoothly.
The assembly line is broken into three parts: pre-assembly, main assembly, and final, before finished parts head out the door to the warehouse. The pre-assembly area is where a lot of the dirty work gets done, including welding and machining to build sub-assemblies that will be fit together as they move through the process. Before that can happen, some testing is required, though: a special machine tests the freshly-welded damper tubes by filling them with helium. A green light tells the technician that the part can move forward, but if the part fails the test by leaking, the testing machine itself removes the piece to eliminate the chance that a bad part would end up in assembly.
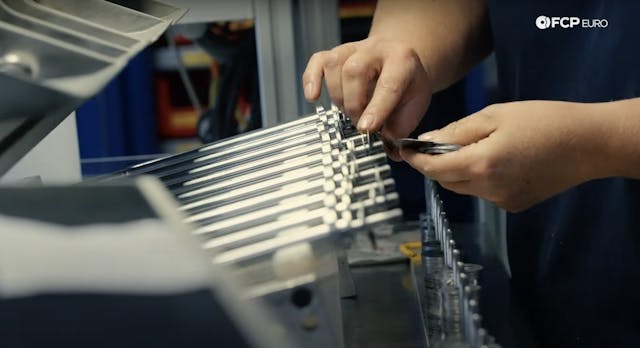
There is no shortage of high-tech equipment to handle a lot of the plant’s operations, but there’s plenty of human presence, too. Bilstein staff visually inspect pieces between steps and ensure the product is as expected. It’s also human hands that tackle the delicate work of assembling the shim stack, or the small, precision, washer-like pieces that set the characteristics of the damper and how it flows fluid during use. Each type of damper has its own “recipe” for the shim stack and that means it is easier for a person to assemble as they can adapt to changes more quickly than a machine.
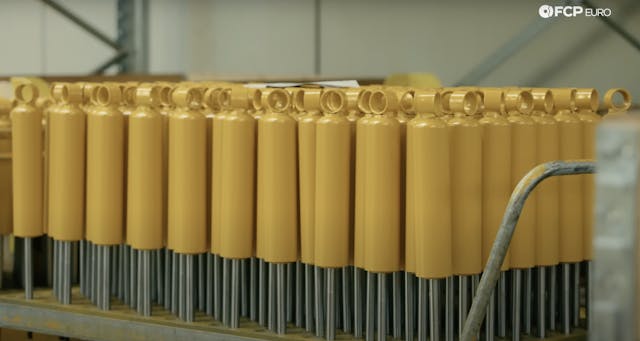
The final step is applying the recognizable yellow paint. The paint line is comprised of seven different steps that vary from washing off any oil residue from the filling just one step prior, to drying and ensuring the paint is fully cured before the final touches.
Marketplace
Buy and sell classics with confidence
This detailed process highlights just how complex many of the pieces of our cars can be. Getting the massive assembly of parts we call vehicles to operate properly is very intricate business, and nothing shows that as much as looking at the effort that goes into making just one part of the thousands required.
***
Check out the Hagerty Media homepage so you don’t miss a single story, or better yet, bookmark it. To get our best stories delivered right to your inbox, subscribe to our newsletters.
Good product. Just make sure the parts you need are instock before you need them. If out of stock it can take a while to get some part numbers in. Plan ahead is recommended.
They do production runs and it take time to get them up and then shipped here. Some back orders can linger.
Best to order if you put the car away for winter and then you have time to wait or get them while no one else is buying. Spring is the worst time for most parts as everyone is buying. Wheels are the worst.
My Subaru Legacy GT wagon had KYB shocks stock. I replaced it with the Japanese model spec Bilsteins and it was a night and day difference. I believe the OEM shocks on my Supra are Bilsteins. I’m a fan of their products.
I am an automotive engineer and was shock absorber (damper) design manager at Maremont Corporation for a short time, Then I started my aftermarket business and discovered Bilstein. I have had an ongoing business relationship with them for about 40 years. They were the first company that I became aware that the compression/rebound ratio was changed for different spring rates. Maremont did not offer this level of design sophistication.
I have used Bilstein dampers on several of my cars and, once installed, I tend to forget ever needing to replace them, which has never been required, even on high mileage cars. I also found they are very tolerant of differing spring rates and vehicle weights. As an example, I had a 1984 Mazda 626 coupe as a company car for many years. At about 20K miles the factory dampers were leaking and needed replacing. I obtained a set of warranty take offs from a dealer, cut the tops open, and removed the internals so I had empty tubes. I worked with the folks at Bilstein in California and found that VW Rabbit cartridges would fit the front tubes and Fiat 128 cartridges would fit the rear tubes. These were built using weld on threaded collars and the assemblies were installed in the car. The cartridges chosen were for lighter, smaller cars but performed well on the Mazda.
The car was used as a daily driver, company travel car, and driving school track day car for 12 years and 140K total miles before being sold. The purchaser could not believe how well the car drove, considering its age and mileage, and drove away with a big smile. I lost track of it, so do not know how much further it went on those mismatched dampers.
I have not kept up on some of the newer damper technology, so am not aware of how some others compare to Bilstein. However, based on previous experience, they will be my default damper if available for my vehicles.