Media | Articles
E-motor swapping your classic isn’t as simple as it sounds
We recently got behind the wheel of a Tesla-powered Mustang owned by AEM Performance Electronics, a company that is developing tools for hobbyists and big companies alike to make electric-swapped cars behave on our streets and highways. Our takeaway from the experience was that while the sound of an e-motor in a classic is completely different, good engineering can help retain a lot of the original car’s feel—even with a swap that’s as mechanically involved as dropping in a completely new rear suspension.
In our drive story we touched on how the car uses a Tesla drive system, which packages the motor and gear reduction into a compact unit along with the control arms. Sounds straightforward, right? In principle, yes, but AEM showed us in detail how the ins and outs of EV conversions are a bit more complex than they often seem.

Powerful motors require powerful batteries
It sounds intuitive that you’d need a lot of battery capacity for a long-range EV; but even if you want something for short-distance fun, it’s going to take quite a bit of battery power. Just look at the CobraJet 1400 and eCOPO Camaro, which both have significant battery capacity. Unlike capacitors, batteries aren’t meant to dump all their stored energy in a hurry. That means that if you’re hoping for a whole lot of power, you need to plan on bringing a lot of voltage with you.
Lawson Mollica, AEM Director of Marketing & Public Relations, likened a powerful electric motor EV to having a huge engine under the hood and the batteries are the fuel system. Seems simple enough. But as with a liquid fuel system, any bottleneck will be a limiting factor. Just like a blown Hemi won’t be happy if it’s fed with a ¼-inch fuel line, a powerful motor won’t work to its potential if its batteries can’t handle the power draw. As a practical EV example, an AWD conversion with twin Tesla Plaid motors won’t be up to its full potential with just 20 kWh worth of batteries.
Mounting batteries on a car built with an internal combustion powertrain can be difficult. But with a vehicle built around a longitudinally-mounted powertrain, there’s room for an engine, transmission, and fuel tank, so that’s exactly where AEM mounted its battery packs in the S197 “Testang”. The biggest section of batteries is located under the hood, although the undercarriage shot shows where the remaining batteries were mounted.
Marketplace
Buy and sell classics with confidence

“Tuning” an EV is a holistic endeavor
When tuning an engine, it’s all about getting fuel and spark just right to coax out peak performance. When tuning an electric vehicle, the situation is about far more than the ability to make the power. The torque mapping is the basic response of the motor to throttle input, but there’s also regeneration and battery management to ensure longevity. AEM’s “Testang”, for example, was initially converted by a hobbyist and was functional and powerful—but it didn’t have any kind of software protection for its batteries until AEM’s hardware and software were added.
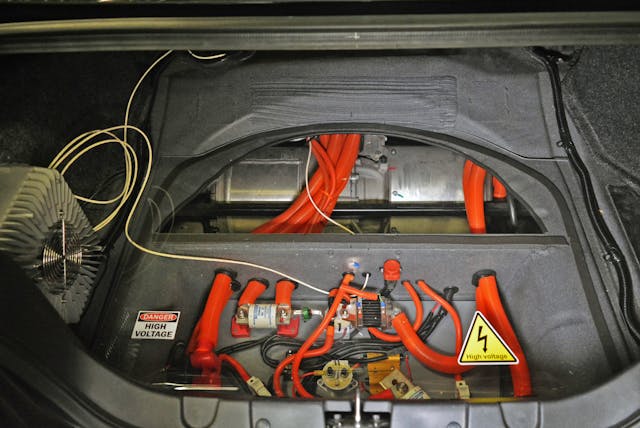
There’s enough electric power to weld battery connections or worse
Electric vehicles use a floating ground, so it’s important to know when and how electricity is flowing. An Insulation Monitoring Device (IMD) allows EV hobbyists to know for certain when the vehicle’s batteries have been switched off and the rest of the car is safe to work on.
Redundant safety is no joke
With so much power on tap with the flip of a switch, it’s critical to have a redundant safety for the vehicle’s major switch: the throttle. The throttle position sensor (TPS) should always fail to the “closed” position to prevent the alternative, which is full throttle. On top of that, AEM will use two sensors to ensure another layer of safety. The AEM team also never performs a calibration on an EV when the car is on the ground, just in case installation of new software causes anything unexpected. Nobody wants to learn this lesson the hard way.