Media | Articles
6 Tools We Hate to Reach For
Most of us treasure the time we spend working on projects. The mental flow state that comes with forcing our minds to mellow out and focus on solely the task at hand can be therapeutic—in the right situation. Every bright light casts a shadow, and every garage holds some tools we hope never to use.
These are the devices that mean our time in the garage is not going well. The steel canaries in the horsepower mine. Projects go sideways just as many times as they go flawlessly, and many of us have various gadgets that serve no purpose until all else has failed.
Here are a few tools that we love to have but hate to reach for.
Tool #1: Tap set
More often than not, forming—or re-forming—threads in a part or piece follows the destruction of those spiraling channels. You’ve probably broken a piece of hardware—or, worst of all, an easy-out. Toss in the fact that taps are very hard, and thus brittle, and you have a very volatile evening of work ahead of you.
When used properly and carefully, a tap set can be a reset button on the life of a part. Even drilling up one size and tapping so that a fastener can have appropriate holding power may be better than replacing the fastener. Sometimes it’s all about perspective.
Marketplace
Buy and sell classics with confidence
Tool #2: Spring compressors
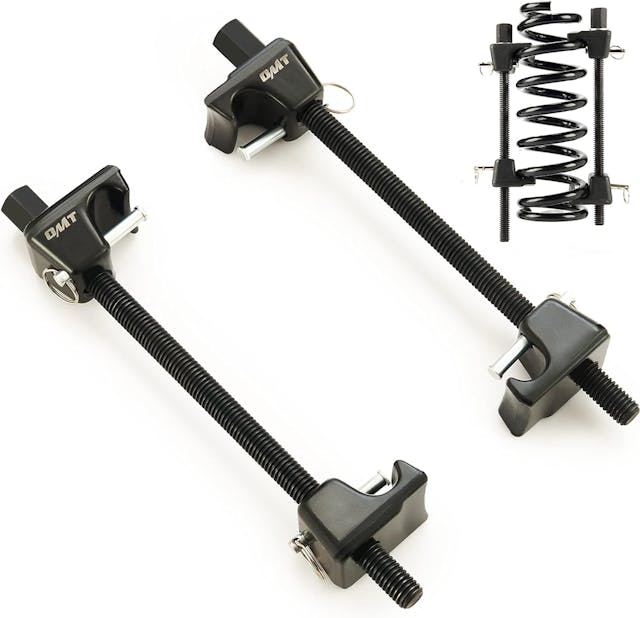
The sudden release of potential energy describes a lot of scenarios: The explosion of a firecracker, the expansion of an airbag, and the release of a compressed spring. Each of those can have serious long-term health effects if it happens too close to your person. There are two groups of people who work on automotive suspension: those who are uncomfortable, and those who ignore the forces at play.
Springs and suspension still need to be serviced, though. Carefully inspect and service spring compressors before using them to ensure there is no damage or problems that might pop up. Sometimes just that bit of added confidence is enough to soften the fear factor.
Tool #3: Camshaft locker
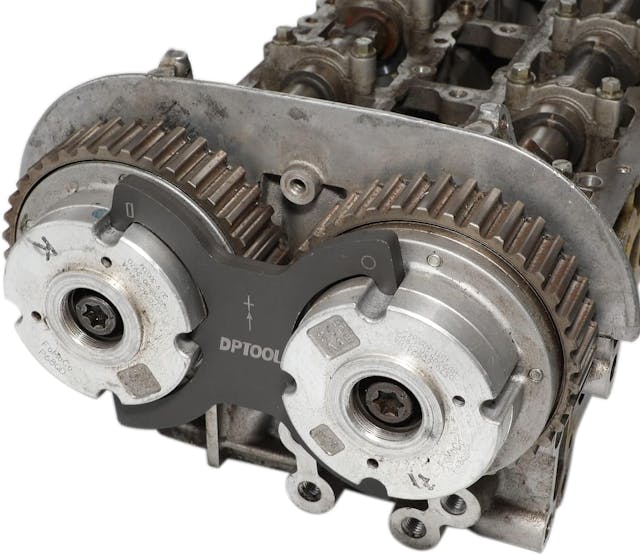
It’s not that this tool is so bad; it’s that the consequences of human error when using it are high enough to make us uneasy. Variable camshaft timing has unlocked horsepower that comes with minimal compromises in fuel economy and also drivability. Unfortunately, the technology also makes for more complicated service; replacing a timing chain or belt often requires careful alignment of multiple points while also holding tensioners and gears in proper orientation. The job can be fairly painless, but that doesn’t mean it’s fun.
Tool #4: Air hammer
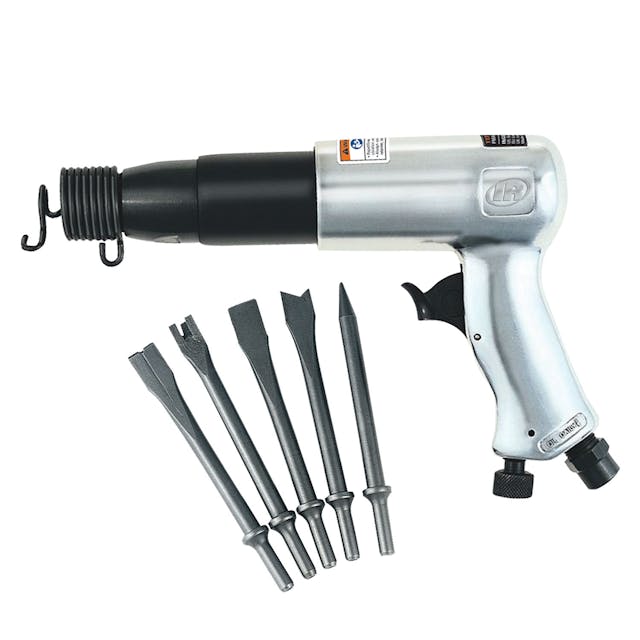
Percussive force breaks the bonds of rust, and it hammers eardrums just as thoroughly. The compromise can often be easily overcome with a good set of earplugs or over-the-ear muffs, but using an air hammer still isn’t a pleasurable experience. Compared to using the torch, and the chance of lighting everything on fire, it is the lesser of two evils. We don’t love you, air hammer, but, after all these years, we haven’t let you leave the toolbox.
Tool #5: Impact driver
Stripped hardware is the bane of any DIYer’s existence. Even with the proper tools and experience to handle stripped screws and bolts, we don’t want to spend the limited time we have in the garage dealing with them. The combination of driving and turning force delivered by an impact screwdriver can take quickly solve the problem of a partially stripped screw. It can also result in hitting your wrist with a hammer, or create an even bigger problem by snapping a bolt off where you can’t grab it. Often, our opinion of an impact screwdriver is based on how well it worked the last time we used it.
Tool #6: The Big Hammer
You know the one. The handle is slightly stained, and the face features a few chips from that one time you got a little carried away on that ball joint. You probably started addressing the problem at hand with a couple of smaller hammers and, when you realized that things were not going your way, and that you were tired of talking nice, opened the drawer to grab The Big Hammer.
This list is all a matter of opinion and personal experience, so we may have missed one or two here. If you’ve got a tool you avoid reaching for but might not be able to put a finger on why, leave a comment. Consider it an unofficial survey.
***
Check out the Hagerty Media homepage so you don’t miss a single story, or better yet, bookmark it. To get our best stories delivered right to your inbox, subscribe to our newsletters.
first is the drill , then the easy out , next the tap , and of course the helicoil ,, one of my favorite tools is the flaming hacksaw in the right hands it stop you from having to pick up the drill..
Left-handed drill bits & a reversable drill have saved the day more times than I can think of.
When a job is going really, REALLY bad, I plan on the welder, the lathe & the Bridgeport mill.
If all else fails, a total re-fab of the part gets things done.
Just not a “quick & easy” job.
You know your day is going bad when you have to resort to Heli-Coils to complete a job. Hopefully there is more than enough liquid nerve calmer in the shop fridge to enjoy after the job is complete.
I agree, Easy-outs should be #1 on the list. Make sure you use top quality Easy-outs, taps and anything you are going to hit, like a chisel. From personal experience, if you break a top quality tap you are either rushing, doing it wrong, or just plain pushing your luck. I’ve been guilty of all 3 examples, I’m sorry to admit.
While I remember many of my father’s expressions while I was growing up, one of my favorites is – Don’t force anything, just get a bigger hammer.
Around my shop and my buds garages, that very useful Big Hammer is called a Harley Tool. 😂
Soldiering Gun…JB Weld… EZ out…grinder/cutoff…..
Wire Stretcher….
There are SO many! Slide hammers, vice grips, magnets, inspection mirrors, air impact tools, bolt heaters, head gasket in a can……
I have a 14 inch iron pipe that fits over my socket wrench end for leverage I named it “The Convincer” It has lived up to its name many times. I’ve had it for over 40 years!
grease gun . any kind of cut off chisel.
I don’t completely agree with the tap and die set on this list. I’m putting an Explorer 5.0 into my 1966 Mustang and while I’m at it I am running a tap into/through all the holes to ensure that everything goes together nice.
I have a love hate relationship with my torque bars ….
Recently I came to change my summer to winter tires.
One set of brontosaurus wheel bolts would not break loose with my impact wrench.
Ended up with a 2’ toque-bar extended with a 4’ length of tubing and standing my full 160 lbs. on the end of the torque bar to break it loose – that’s around 900 lb ft of torque!
At this point I remembered that this was the wheel that I had a pesky slow leak on and I had let my trusted tire shop remove and fix.
There is a lesson in all if this.
Most tire shops employ fresh faced school grads with no formal training to do this work, and they have probably never used a torque wrench let alone know the correct torque for wheel nuts, and how excessive torque can damage nut, bolts and, stud threads.
I read the riot act to the owner of my tire shop, and told him to invest in a some high quality torque wrenches, turn all the impact wrenches down to minimum setting, and do some training on his tire Jackie’s.
Think about this the next time you trust your new $60k pride and joy to some local tire shop…..
I have all of these except the air hammer. The hand impact driver is the right tool for older Japanese motorcycles with soft Phillips head screws. I also have the other secret for motorcycle and bicycle parts, JIS screwdrivers because they shape is subtly different. I also have some Pozidrive bits somewhere in case I have the misfortune to work on 70s British stuff. Fortunately for my sanity I live in Oregon so rust is a non-issue and most of the orange stuff on my truck is volcanic rock dust.
Hold chisels with vise grips and keep your hands safe.