Media | Articles
6 DIY Tips from One of America’s Master Racing Mechanics
This article first appeared in Hagerty Drivers Club magazine. Join the club to receive our award-winning magazine and enjoy insider access to automotive events, discounts, roadside assistance, and more.
On a bright March morning, a delivery van backed up the driveway of a modest tract house in suburban Detroit. The avenues in these parts are named for flowers: Periwinkle, Wisteria, and Amaranth.
The garage door opened to reveal a workshop that would register as familiar and unremarkable to anyone who has worked on a car. Yet this home belongs to Dan Binks, the master racing mechanic, crew chief, and fabricator who steered the Corvette Racing team to six victories at the 24 Hours of Le Mans. The truck was here to pick up a $125,000 racing engine assembled right here in his home garage.

All to say Binks, technically retired but busier than ever, is a great guy to learn from, no matter how much or little you already know. I shadowed him for a day to glean some of his wisdom. Here are the ABCs of wrenching, from the man who has seen and done it all.
01. The Point Is to Have as Much Fun as You Can without Killing Yourself
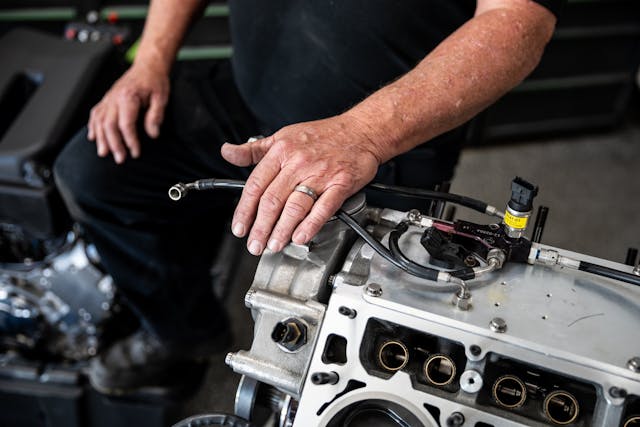

Be religious about safety. Get jack stands rated for 3 tons and a stout floor jack. I’m fine with the stuff from discount stores and use a $100 engine stand to hold six-figure motors. Wear safety glasses. Always. They even sell pairs with readers at the bottom. You might want a hand truck to move stuff around and save your back. Tie up long hair and loose clothing. You’ll also likely want an internet connection in the garage. Even I watch YouTube videos to learn all the time.
Marketplace
Buy and sell classics with confidence
02. You’re Never Not Buying Tools
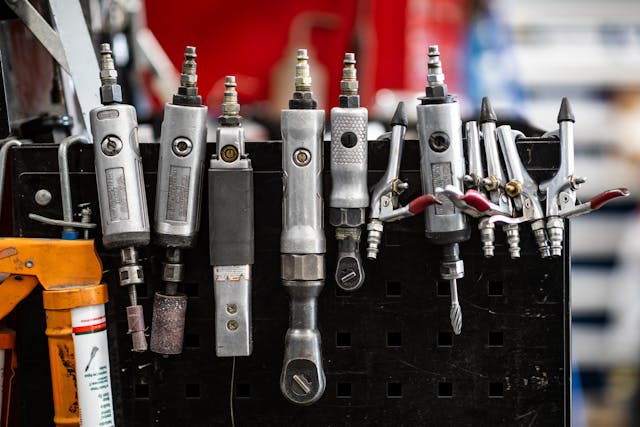

If you’re starting with nothing, buy a large tool set from any of the mainstream brands, like Craftsman, Kobalt, or Gear-wrench. You don’t need the pricey Snap-on tools. Use the discount stores for toolboxes and even a compressor. Thanks to battery-powered tools, I don’t use as many air-powered tools as I used to, but the compressor is still handy. Harbor Freight sells a two-cylinder compressor that’s reasonably quiet. For the battery-powered tools, pick a brand and stick with it so the batteries power multiple devices. Also, you want a vise—the bigger the better.
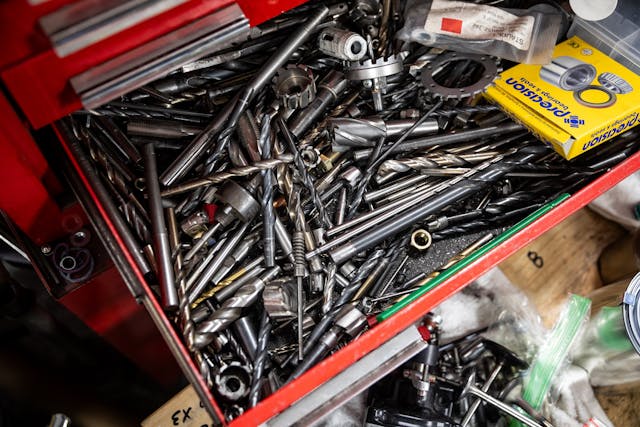
Some tools are consumables, like drill bits. I don’t bother sharpening them when they get dull; I simply wait for the sales and buy in bulk. When drilling metal, 90 percent of people spin the bit too fast, which overheats it. It’s hard to hurt the bit if it’s going slow. I use 3-in-1 oil to lubricate.
The final must-have tool is a multimeter. The device measures voltage and amps, and you’ll use it to diagnose electrical problems and battery health.
03. Get Familiar with Fasteners

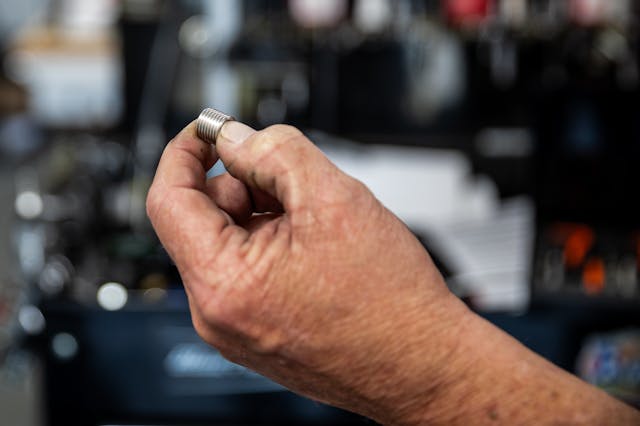
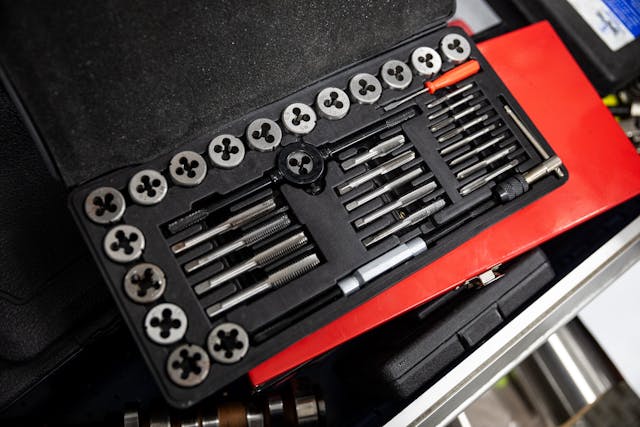
You need to understand the different types of bolts, thread pitch, and the torque requirements. Thread everything by hand, and over time, you’ll get a feel for when something is cross-threaded.
You will, at some point, damage threads. A set of taps and dies is a good thing to have on the shelf. The taps cut threads in a hole, and the dies do the same to a shaft. Those bits are useful to restore nicked or bent threads. Also, practice shortening bolts. Thread a nut all the way on the bolt and then cut it with a hacksaw. Unscrew the bolt and then see if you can reinstall it. Use a file to remove burrs. There are helpful videos on YouTube. I buy fasteners from McMaster-Carr, which has a handy phone app.
04. Live and Die by the Proper Torque

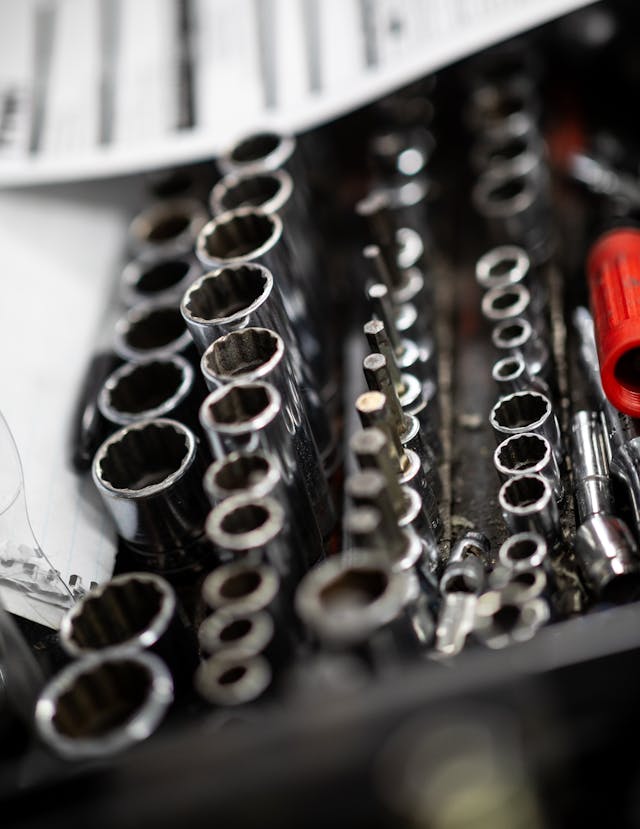
Every bolt has a setting for how hard it should be tightened. The setting is a twisting force known as torque. Apply 10 pounds of force on a foot-long wrench and you’re applying 10 ft-lb of torque. Go over that setting and you risk snapping the bolt. That’s when garage rage often arrives. You can find the proper torque in most service manuals or figure it out by the size of the bolt. If that fails, Google it. You’ll need a torque wrench to measure the amount of twist. Most brands will do.
Loosen bolts, especially rusty ones, with care. A good rule of thumb is to use the tightening torque specification for removal. If a suspension bolt requires 70 ft-lb, don’t apply more than that to remove it. If it’s stuck, then it’s time for heat. I use a readily available torch fueled by MAPP gas. Heat the bolt until it’s red, then apply a candle. The wax will flow into the threads. Let it cool and try again. You might need to try the heat and candle procedure several times.
05. Don’t Fret about Fluids

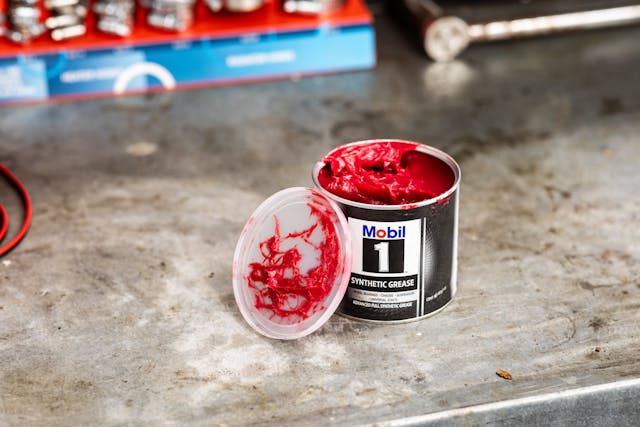
Which grease? I hear that all the time because there are many different types described with big words like molybdenum and disulfide. Some grease is better than no grease. I use Mobil 1 grease for almost everything. That said, there are times when a pressurized can of a spray lube is handy, like squirting white lithium grease into door latches or graphite lube for lock cylinders.
Beyond the slippery stuff, the most commonly used fluid in my shop is a liquid glue called Loctite, which prevents bolts from coming loose. It comes in three flavors specified by number and color. Use blue Loctite, number 243, for most fasteners since it’s easy to break free. The red, number 272, is for the bolts that are almost never removed, and number 620 is for high-heat applications.
06. Moving to the Pro Ranks
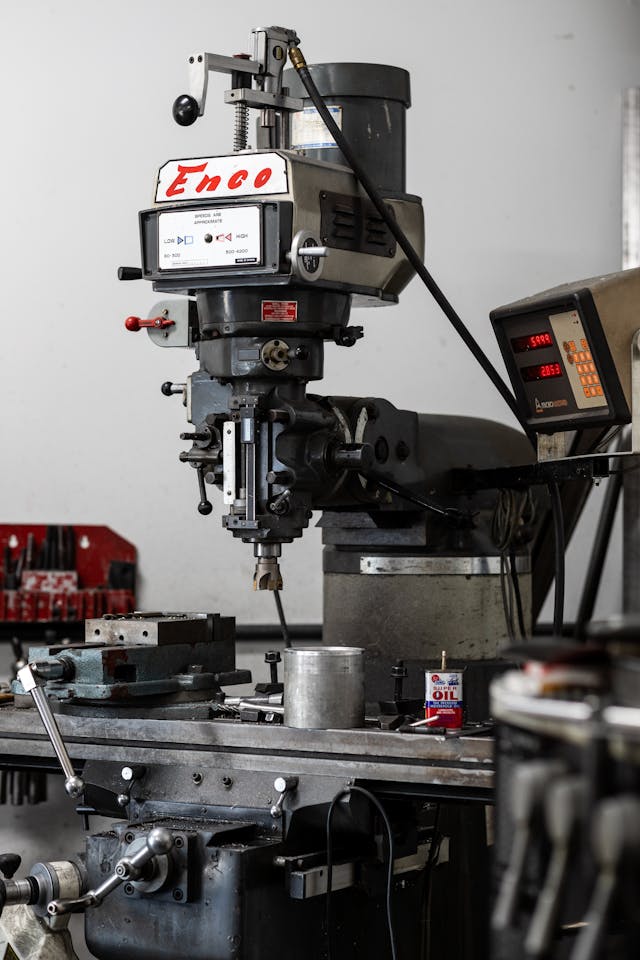

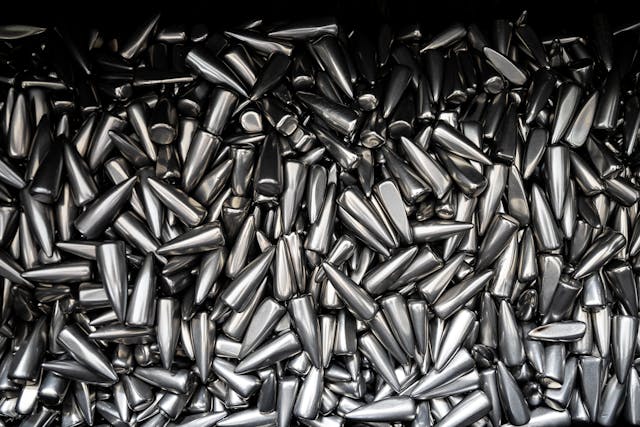
The more you do, the more you’ll want to do. That means more skills and tools. After the basics listed above, the next step is usually a welder. For your first one, stick to a basic wire-feed unit known as a MIG welder. Some folks take a class to learn that skill, but there are plenty of instructional videos on welder manufacturer sites and, yep, YouTube. Practice.
Once you’re welding, the next rung up the fabrication ladder is precise metal cutting known as machining. Most of you don’t have enough need to justify the spendy tools required, but if you’re ambitious, let me recommend a few things: You need a lathe and a milling machine. Don’t buy a unit that claims to do both. For the mill, which looks like a fancy drill press, a digital readout that shows the position of the piece is a must.
Great article! Thanks!
Number 1: learn to read manuals, literature, EVERYTHING you can BEFORE you start and watch videos from reliable sources online. Nothing will ruin your day faster than making expensive mistakes because you THOUGHT you knew what you were doing.
Great article very helpful for new guys coming into the hobby and even an old guy like me learned some things here too. Will certainly be trying the heat-candle thing next time I have some stuck bolts to deal with.
Terrible advice ! When your wipe out a lobe on your camshaft because you used the wrong oil, or your wheel bearing failed because you used the wrong grease, and the list goes on and on. I see guys wreck a transmission because they put in any ATF, not what it called for. Or how about the cheap torque wrench that is off by 10-20%. and you wonder why you have head gaskets or oil leaks. When it cones to tools you get what you pay for ! Spend once cry once. Maybe if you lean how to treat your tools you won’t have to buy in bulk when they are on sale. Lean how to sharpen a drill bit and take care of it, how to keep a edge on your files.
There are drilling fluids (not oil) and also drilling & cutting wax’s that work far better than any oil, Look online for those.
Great story!
I like the candle trick on seized threads. I had never heard of that and will give it a try next time.
My training, however, was not to use a lubricant when cutting metal, whether drilling, tapping or what ever, but to use a Cutting Oil.
I also am a retired mechanic / truck driver for SCCA and Rolex series. Winner of the 24 hours of Daytona, 6 hours of Watkins glen and a few championships in the AGT class. Also worked on and was the first C4 corvette to win at Daytona in 2000. As far as tools I have been using snap on since 1988. This article hit my heart strings and my memories.
Correction I stated first C4 I should’ve said C5.
Excellent article. I don’t make or reshape parts but the rest is good to know and reinforce what people already do.
Great article, thank you! I never heard the candle wax trick. I have used heat to heat the object the bolt was threaded into to pull the metal away from the bolt (learned when I was a Navy Nuc Sub Machinist Mate – BIG bolts), but obviously not applicable to all scenarios. Another related “tool” is Kroil – the oil that creeps. I can’t count how many times my spray bottle filled with that has been successfully used. Thanks again!