Media | Articles
5 things that changed how I build engines
Few things in the automotive world are as complex as building an engine. Not assembling an engine; building an engine. It’s similar to cutting a diamond: The beauty of the finished product is simple, but the process—taking the time to ensure proper setup and function at every step—can be intense.
Becoming a professional engine builder requires years of experience. I’m definitely still an amateur, but these five things helped me make huge leaps in my own engine-building process.
Layout/space for layout
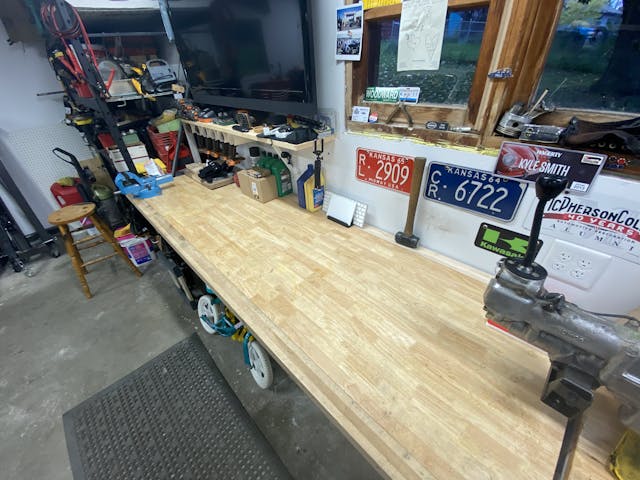
One of my first engine-rebuild jobs wasn’t even the full engine, just the top end of a vintage thumper after it was destroyed by a short and torrid love affair between intake valve and piston. I set up shop in a friend’s garage. We pulled bits and pieces off with reckless abandon, stacking them on the motorcycle lift under the bike. Only once we reached the reassembly stage did I realize all the parts we needed were a jumbled mess.
Today, I prepare my workspace. I prefer to have enough room to lay out each and every part: They don’t have to be organized very strictly, but nothing is stacked, in a box, or otherwise hidden from sight. Attention to detail is one of the most important resources in engine-building; I don’t want to waste it on making sure parts didn’t fall off the table or get jumbled underneath it.
White linens
Honda famously requires all its assembly-line workers to wear white head to toe: The process should be so clean that the uniform stays white. I’m not a professional engine builder, but I did stay at a hotel last night—and I kept the towel to lay on my workbench. Only once a part is fully ready to assemble is it placed on this now-sacred space. Depending on the component, I might even wrap it in a plastic bag or container first.
Marketplace
Buy and sell classics with confidence
That clean white space is where I first assemble the engine—mentally. I can visually take stock of the parts and pieces and know that I have everything, and each component is properly prepared. This prevents me from being surprised or having to source something on short notice: If a part I thought was cleaned and ready needs additional work, I address it now, before assembly starts.
Write it down
A failed seal once forced me to rebuild an engine I had already assembled. As I took the engine apart, I did the standard “while I’m in there” look-around. The only problem was that I couldn’t tell whether the wear on a given part was new: Certain pieces like rocker arms are totally safe to reuse if still in spec, but failing to document the wear in specific terms leaves me open to confusion when trying to diagnose other issues. Did I re-use a worn part, or did I produce that wear because of a sloppy assembly?
Eliminate that game and draft a personalized cheat sheet. Anything that can be nominally measured gets touched by the digital calipers before being final-assembled. If taking a measurement isn’t possible, document a part’s condition, including any flaws that you might need to monitor or allow for in the future.
These sheets are also handy if any of my engines go up for sale before I run them or put them in a bike: The buyer can see from photos and notes exactly what they are buying.
Understand each part
Once I started noticing each individual piece of the engine worked, my brain was able to prioritize. Suddenly I worried less about using factory hardware to hold on a side cover and obsessed instead of the one little lip seal that ensures oil coming out of the oil pump goes through the crankshaft to the rod bearing.
This mental process is also great for troubleshooting issues, especially if, like me, you use some components outside of the engine’s original design parameters, and thus deal with problems and fixes that the original engineers would never imagine. If you truly understand the system, you can more quickly deduce which component is not doing its job.
Repetition
Just like it takes a couple of watches of Inception to know what the hell is going on in the second half of the movie, it takes more than one rebuild of an engine to fully understand what you are doing. It’s tough for us home garage folks, but rebuilding the same engine multiple times is an awesome way to learn a lot in a short amount of time.
Your first time through a build is often spent just trying to not do things wrong. Then, as your confidence builds, you start asking why this works, not how it works. Suddenly you are primed to understand what improvements you can make and, if you seek more performance, what is a good spend of your time and money.
***
Check out the Hagerty Media homepage so you don’t miss a single story, or better yet, bookmark it. To get our best stories delivered right to your inbox, subscribe to our newsletters.
My first engine rebuild was a West Bend Go Kart two stroke. It would hurt the rod bearing every time I used alcohol. I was 14 years old and rebuilt it using grease to hold the needle bearings in place. It was difficult and time consuming. Anyway an old timer told me to line up the bearings on a clean surface and then melt a candle over them. Walla. Then you just pick them up and roll them around the crankshaft. Hours of time saved.
I rebuilt a lot Mac’s starting at the same age. Was to beat pro built engines and guy’s who’s dads paid or builteverything
Sorry, was great to beat, built everything. Wish we could edit!
Every vehicle I have has a log book with it. Day of purchase, when built. VIN etc.
Everything I do I document. ie July 12/23 remove front bumper then any comments or specifics and pictures if needed. Rebuilding an engine I will record the ring end gaps and which bolts were torqued and how much. Then later when I am thinking, did I remember to torque …. I can just look it up. I sleep better at night. I usually use half size spiral wound notebooks, get 200 pages. I also keep all invoices in a file for that vehicle. NOTE: Try NEVER to add up the totals. You will only be disappointed at how much you have spent. I do this for “fun”
Although I’ve done some rebuilds more than once – 90% of the time it’s a one-and-done (hopefully). I would love to see/hear hints and tips from expert rebuilders on how to avoid common mistakes on “once-and-done” rebuilds
Interesting idea on hearing from an expert. I think I know just the guy… We’ll see if we can spin that one up.
In the article you mentioned “write it down”. definitely good stuff and I suggest you include take a picture, Most if not all of us own a smart phone and there are things that you should take a picture of so that you put it back together exactly like it came apart…
A third for the Greg Edwards comment.. You have to FLOAT the hone grit out of the cylinders after they have been machined. Scrubbing will only partially do it. Watch a pro race shop clean an engine block post machine work and you will get it.. Trying to do it at home is tough but if you can run a paper towel through the bore after clean with WD-40 on it and ANYTHING shows up on the paper towel – you will have scoring.
Is hagerty promoting theft from motels?
I have a tin-topped workbench. I put cardboard down, then the parts.
I then line the edge of the bench with tool hanging magnetic strips from Harbor Fright to hold the cardboard down and catch anything that rolls away, either by stopping it or grabbing it.
Dollar Tree and others sell white poster board that appears to have a very smooth finish. Since the sheets are fairly large and usually are two for $1. they are very cheap insurance for keeping parts clean while assembling engines, transmissions, etc.