Media | Articles
5 Things Every Great Workbench Has
There are many staples of a DIY shop or garage, but the workbench stands above the rest. Having a work surface that is not the floor can make working on projects safer, more efficient, and more enjoyable. Sadly, just because benches are ubiquitous does not mean each one is good.
Like so many other things in life, a workbench must balance budget, function, appearance, and specialization. While we can’t help you with the last one on that list, we can get you to a great starting point by calling out some of the attributes that every good workbench will have. Whether you are building a new one or checking up on one that you’ve been using for years, here are five characteristics every great workbench needs.
A Flat (ish) Surface
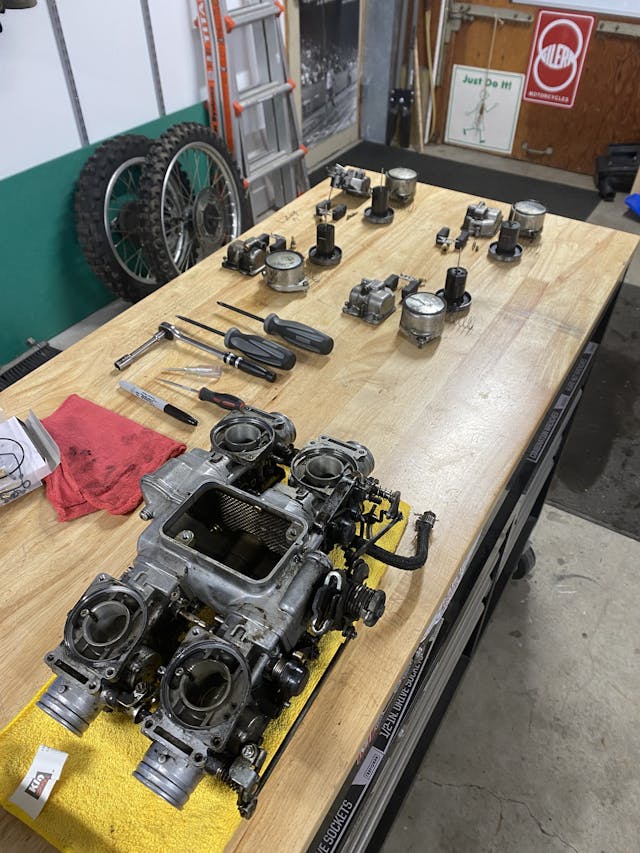
You don’t need to rebuild a carburetor on a certified granite slab, but you do want a surface that can be clean and smooth while not allowing parts to roll away. You’ll often need to level your bench using shims or some other method, because garage floors are not typically very even—occasionally, on purpose.
Dozens of materials can be appropriate for bench tops, so be sure to take a deep look at what kinds of projects you think you’ll tackle and choose a material that can take the amount of weight you need it to and that won’t deform during use. Butcher’s block surfaces have been great to me, though there are a few sections of my bench that have some serious dents from hammer blows or heavy parts.
Height
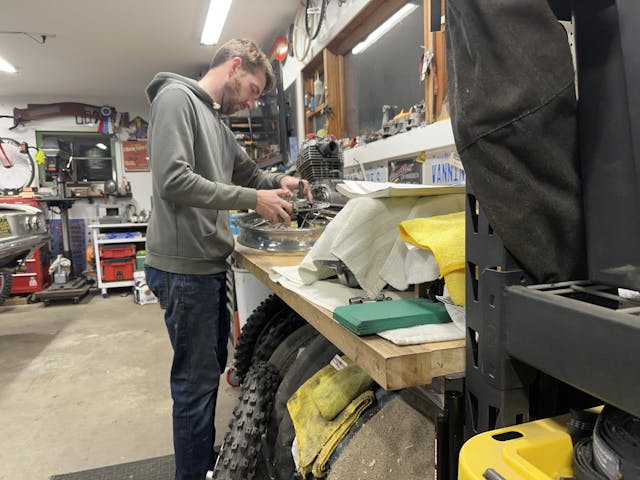
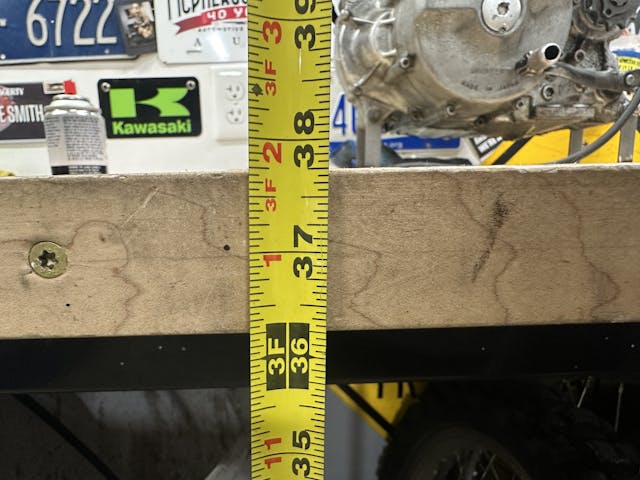
It might be tempting to plan your workbench around the height of a kitchen countertop (36 inches is standard), but be careful: Most kitchen tasks are less precise than most DIY projects, and food prep and cooking don’t require leverage or a large range of movement, like garage work often does. A lower work surface height is more tolerable in a kitchen, the arrangement of which needs to be somewhat standardized. Your workspace has no such constraints. Set your bench at a comfortable height for you and the work you do. That might even mean two benches at two different heights: parts cleaning is best done at a lower bench, while carburetor rebuilding is best done at a higher one, so that it’s easier to see.
Marketplace
Buy and sell classics with confidence
Heft
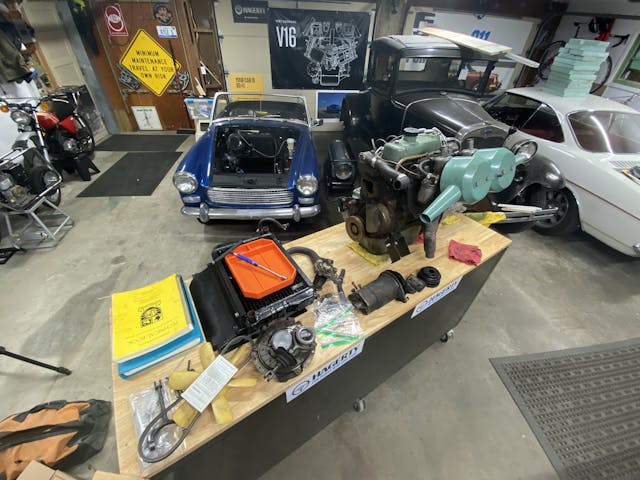
A flimsy bench makes work difficult in a number of ways. If you’ve got a component plopped on top of your workbench and every time you move it or shift something for access, the whole bench moves, you won’t feel confident in the work you’re doing.
Again, be careful: You can have too much of a good thing. Nice and sturdy does not require using 6×6-inch steel tubing for legs and 1/2-inch plate for the top. There’s a place for a bench like that in a welding shop, but in most home shops, it would be more annoying than helpful.
A Solid Vise
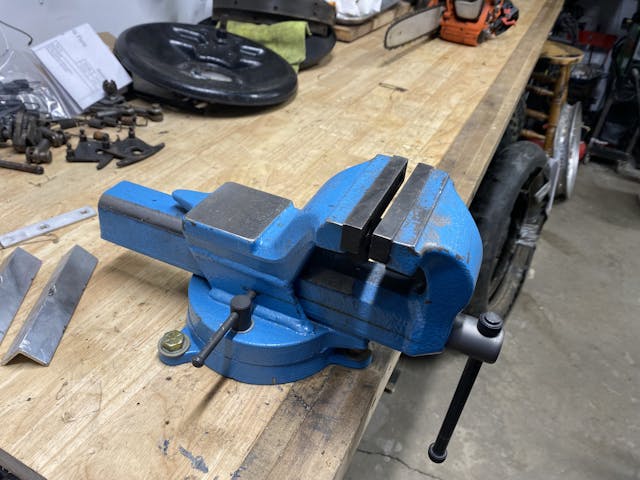
The third hand we always seem to need, a vise is a necessity for any shop for many reasons. It can be a anvil, a press, or an anchor that can help projects big and small in a multitude of ways. Don’t believe me? Try and work without one for a while.
Like the other characteristics listed here, consider your specific needs and choose accordingly. Do we all need Wilton Bullets? No, but most people would be better served with one than with an import vise whose jaws don’t line up evenly and have a ton of slop. If you’re on a budget, consider buying an old vise to restore. It’s a fun project, and we can honestly say that cast metals aren’t what they once used to be.
Sturdiness

When wrenching on something, it’s nice to have a workbench that doesn’t move an inch to the left when trying to loosen something and an inch to the right when tightening something. Especially if you are not planning to bolt the bench to a wall or other structure in your garage, consider using an under-bench shelf for storage: It will add a nice, low weight and improve stability.
Bonus: Wheels
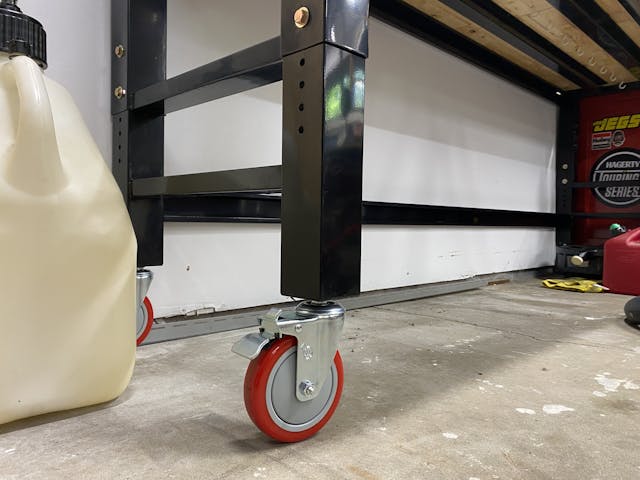
I’ve said it before and will say it again: The ability to bring your tools and workspace to your project is a superpower. Buy a good set of double-locking casters, put them on your bench, and suddendly it is a tool that goes places with you. The other side of the shop? Easy. The driveway? No problem. Putting multiple benches together to create super bench? Also an option! Use this power wisely.
No matter what, having a workbench is better than not having one. If you are looking to maximize your workspace and haven’t assessed whether your workbench is working for or against you, now is the time.
***
Check out the Hagerty Media homepage so you don’t miss a single story, or better yet, bookmark it. To get our best stories delivered right to your inbox, subscribe to our newsletters.
Space. Something I grew up having, something I never seem to have enough of.
When we renovated our kitchen, I was careful about taking out the cabinet carcasses. I relocated them to my shop where I installed them on a 2 x 4 grid. I reused the laminate top. My bench height is 39″ (1 metre). Works great for me. The cutlery drawers have dividers which make great places to store screw drivers and pliers and the pot & pans drawers make excellent places to store my multi-meter, battery chargers, timing light, dwell meter, and other test equipment.
I had a cut-out in the countertop where the stove burners sat. I put a couple of stout supports under the hole and filled the hole with a piece of 3/4 inch form-ply. I’ve got a piece of granite countertop that fits the hole perfectly and that makes a good place to stick down a piece of wet / dry paper when I’m resurfacing aluminium parts.
I repurposed the old ss double sink and tap as a parts washer. A bit of pipe and a storage can for the cleaning fluid was all it took to make a recirculating parts cleaner.
I’ve also have a rolling bench that’s the same height as the fixed bench, my table saw, and the radial arm saw. All I need now is another 20 square metres of floor space because as we all know, you can never have too many tools, too many cars, or too much garage space.
I had been sketching out plans to do a drop-in parts washer into my bench! I resolved that it likely wouldn’t be worth the work but when you literally already have a good chunk of the work done it would be a neat feature. Maybe I’ll get around to mine one of these days.
I’m currently using one of the “$100 Specials” from Harbor Freight. It’s OK for some things, but I cringe at the idea of putting a vise on it!
Since my son has volunteered (willingly, no less!) to build a new bench for me, we’ll be incorporating the ideas I’ve had for decades, along with the suggestions here.
My main bench top is a 30″ steel door (residential style) that came out the rear entrance to my garage after a remodel 30 years ago. The corners are starting to look a little like Swiss cheese after repositioning the vise & drill press a few times. I keep the bench on wheels, but only move it for cleaning.
Kyle, on the left side of the first photo it looks like you came up with a nifty way of storing your electric drills. Is that PVC tube with a wide slot cut lengthwise to slide the tool into? Hope you don’t mind if I steal the idea; I can never figure out an elegant method to keep those items handy but out of the way.
Wheels maybe not for the main bench, but a solid steel shop cart on locking 500lb castors is a must in my shop. A couple full-width drawers to keep a selection of task-specific tools at hand seals the deal.
Other rugged wheeled conveyances and even containers are just the ticket when you need to rapidly re-prioritize tasks as the forces of chaos and seasons necessitate.
These are great gifts to your “future self” to be honest.
I built mine myself. It has all those things and more. If you’re not jealous, you should be.
My Horizontal surfaces fill up, I have one workbench that is a solid core door is hinged to the wall, flips up and has folding legs, it is my working bench, the car will fit with it up (but you cant really get the door open) so it gets folded back down at the end of the days work. At least I have 1 flat place to work.
That’s a neat solution!
Best all around durable workbench top is Formica kitchen counter tops bought in long 12ft single piece from Loew’s or Home Depot. I’ve bought these as “damaged stock” blanks (find in the back aisles of the stores or ask) for 3 homes when we’ve moved through the years. Stout 4×4 or 6×6 for legs makes for a sturdy, heavy duty workbench.
Kyle—KEEP writing these articles! You bring to the fore so many things which a lot of us take for granted but
never really address! The good which is accomplished through your articles cannot be assessed–but, be assured that you put LOTS of us “out here” to thinking–then putting into action, your suggestions and ideas.
Great article and a great lead to networking ideas. One of the comments pointed out your charging bench with the tool hangers made from large diameter, PVC. I think I will copycat your design!
for most people (contrary to a lot of folks Belief) most of us have a tight one car garage if we have one at all–So space is at a premium- seems like most folks here are very well off if not Rich–
a LOT of good ideas here, including the article itself. thanx. one thing i find frustrating is that i work on both vehicles and wood projects. i find they do not mix, meaning working on both in the same area. sawdust gets on everything. and when it gets on greasy stuff, even slightly oily surfaces, what a mess. everything needs to be covered, even that car you just had ceramic coated. and handling wood with greasy hands, well, good luck removing the grease. fortunately i have a large pole barn/shop where i work on each in different areas. it helps, but the dust still gets on stuff. oh the luxury of separate shops!
if i ever make a bench out of wood, i’d use 2x4s for the bench top, gluing the longer sides together, and assembling it tight with threaded rods & nuts. angle iron positioned in the shape of a ‘V’ (with holes/nipples/drain hoses placed at the bottom of the V) on the front and sides could catch oil runoff. the supporting frame would be built stout enough to support it. thick sheet metal would be place on the table top while draping it over the sides. a squeegee could be used to clean oil off the surface. true, most do not need something this robust. but i like the insurance of strength and don’t like it when a bench collapses.
having a bench tall enough where you’re not bending over much helps me a lot. leaning against the edge is a relief when standing. offices are now equipping work desks with adjustable desk tops, allowing the worker to switch from sitting and standing – less fatiguing. when i was a mechanic, i used to put a vehicle on a lift just high enough to lean against or over the fender (with fender cover, of course), even when performing a fairly quick, simple job. if building/installing a bench, consider its height in relation to your height and the amount you’ll need to reduce bending over while working. and yes, a stool is great, too, to switch back & forth when possible, or always sitting.
All good points. I recently discovered Rousseau Metal Inc. They make custom work cabinets and the quality and cost are amazing!
I had my top size, height, material all customized for way less than SnapOn.
A work tip, similar to the baking sheet pan idea mentioned earlier: keep a supply of egg cartons in the shop. I use them all the time when working on projects with lots of small parts, such as rebuilding a carburetor, keeping spark plugs organized by the cylinder they came from, etc. They keep all the little parts from getting lost, and you can keep track of the order in which you disassembled a project by placing each part you remove in a successive cell in the tray. Makes it easier when reassembling to avoiding putting part C back in place, then having to remove it to get part B installed first. I find the compressed paper/cardboard trays work the best if working with parts that may have solvent on them. Solvents and styrofoam generally don’t play well together. When a tray gets dirty or damaged, I throw it away and pull another off the stack. They’re the only tool I have with the added benefit of edible contents.
My neighbor is an elevator repair man… He brought me over eight 3 inch thick, stainless steel elevator doors , I mounted them on four Costco stainless steel toolboxes… found some matching stainless steel cabinets… i’m the envy of the neighborhood… Lol