Media | Articles
4 Levels of Hardware Retention
Our beloved vehicles are massive assemblies of parts. Some of those parts are superfluous to the critical function of a car, so if they fell off we might get a bit of a chuckle at the situation. Other parts we want to stay tightened and torqued exactly how we set them, and that means some form of retention on all those nuts and bolts is imperative, lest our wheeled machines quite literally lose their wheels. Amazingly, this is all less complicated than you think.
Threaded hardware is all about friction. The threads are little more than long spiraling incline planes that wedge against one another, and the friction of the two surfaces is too great for the hardware to turn without outside assistance. Vibration and heat conspire against the smooth bond though, as differing materials could potentially expand at different rates and reduce or spike the load on the threads, allowing things to rotate even fractional amounts. Small, unnoticeable changes over time compound into catastrophic failures. Ever seen a loose wheel and tire rolling down the freeway? Terrifying. A drainplug that falls out and turns an engine into scrap metal? Nightmare fuel.
So how do our cars not fall apart? Well, it boils down to just a few types of retention. Here are the key ones:
Torque Spec
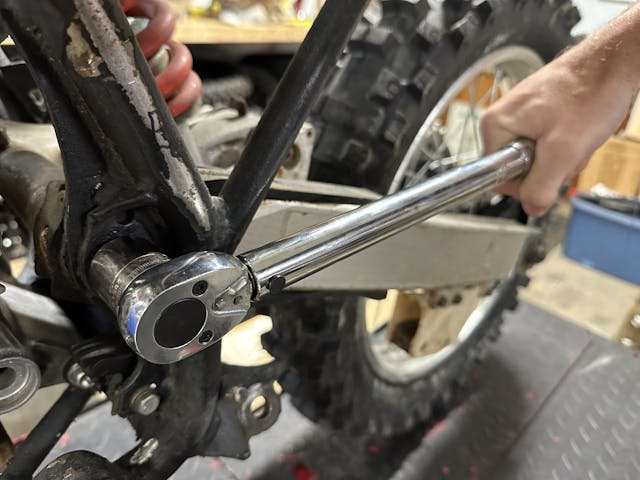
A proper torque specification uses the threads to stretch the hardware enough that it will not lose tension during its intended use. For a lot of common hardware, the torque spec is fairly low, enough to be done by hand with relatively small tools. Just the stretch of the hardware can be enough to keep things clamped tight for a long time.
The perfect example is torque-to-yield bolts that are tightened by degrees of rotation rather than torque. This more accurately sets the clamping load of the hardware, and with the proper number of threads it takes a lot of force to break those back loose. If you need more than that, start looking at . . .
Marketplace
Buy and sell classics with confidence
Chemicals
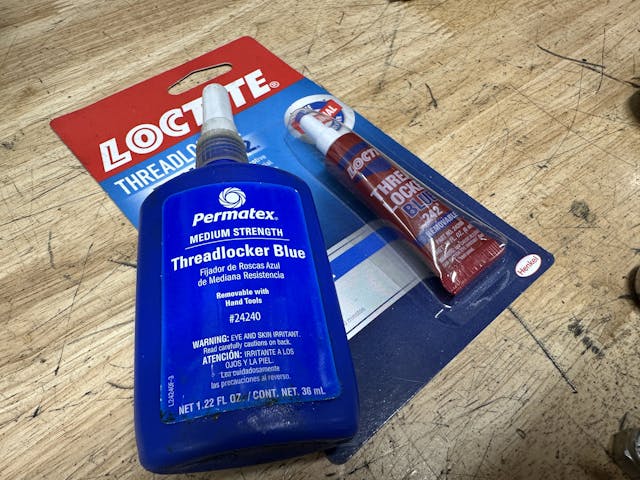
Fresh and clean assemblies might need just a little help to ensure everything stays tight, and one of the easy and cost-effective ways to do that is with liquid threadlocker chemicals. These are typically anaerobic-curing adhesives that essentially glue together a portion of the threads as they are final-assembled. The anaerobic part just means the formula cures without the need for oxygen, a good thing consider how tight the tolerance is on threaded hardware.
But threadlockers have limitations, like cure times and cleanliness standards, along with no visual indicator that it was actually applied—unless the installer makes a note. This can lead to frustration if higher-strength threadlocker is used in an area where it cannot easily be heated to help break its bond.
Additional Friction
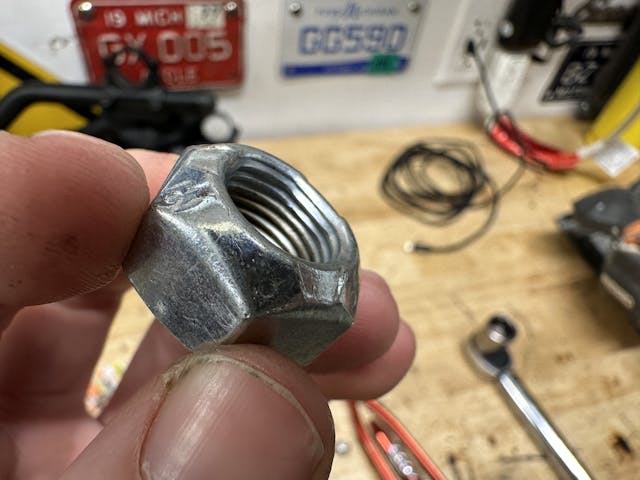
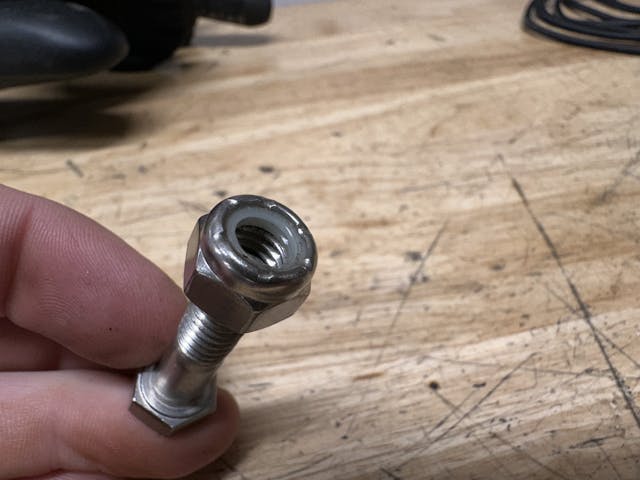
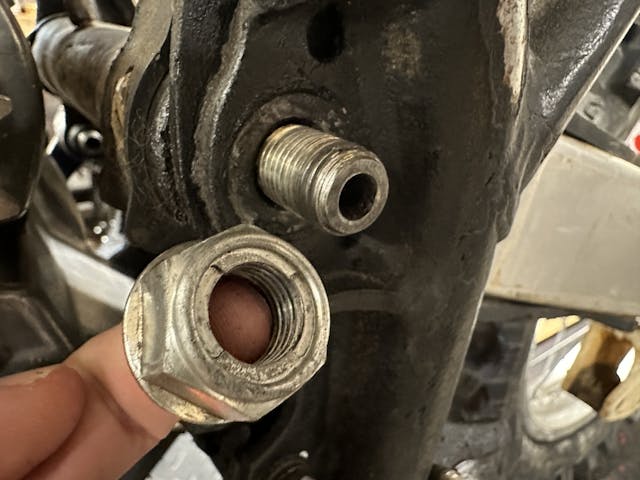
The threads might be one source of friction, but they don’t have to be the only source. Adding an additional feature or piece to the hardware that increases the amount of torque required to turn a fastener can be a solution when more clamping force is not needed but additional turning resistance is.
Two popular options for this are nylon-insert locknuts (aka nylock or nyloc) or metal washers, which are added to the back side of a nut to provide additional friction when the final tightening of the hardware is done. The nylon option does require temperature consideration in the final install. Nylock-style nuts are not the solution to header flanges that always loosen, as the nylon would be cooked off and gone after the first heat cycle.
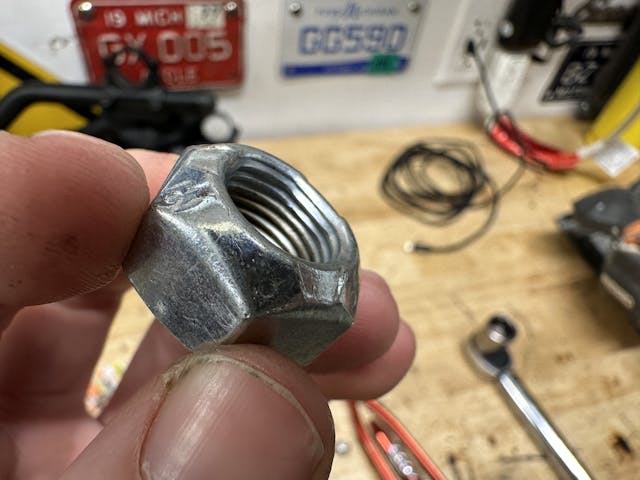
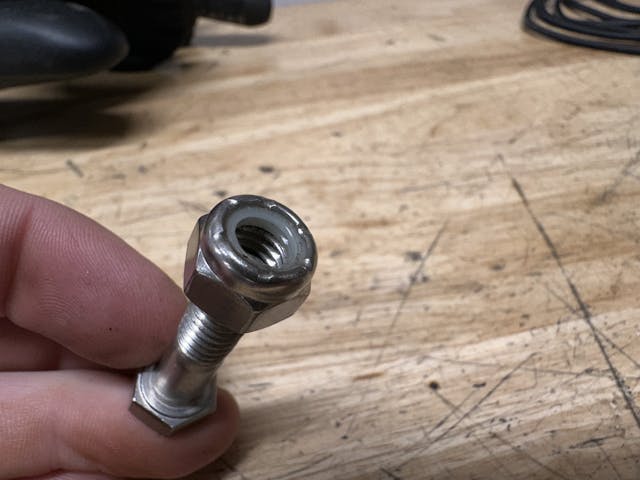
For something like that, it might be better to use a metal waster that deforms rather than the nylon. Another option for this is to have the final few threads of a nut be deformed just slightly. When using this type of hardware it should be factored into the final torque setting, if applicable, and most deforming hardware has limited ability for reuse, as each use lowers the performance of the specific part you are using it for. So if you need retention and serviceability, maybe it’s time to think about . . .
Positive Retention
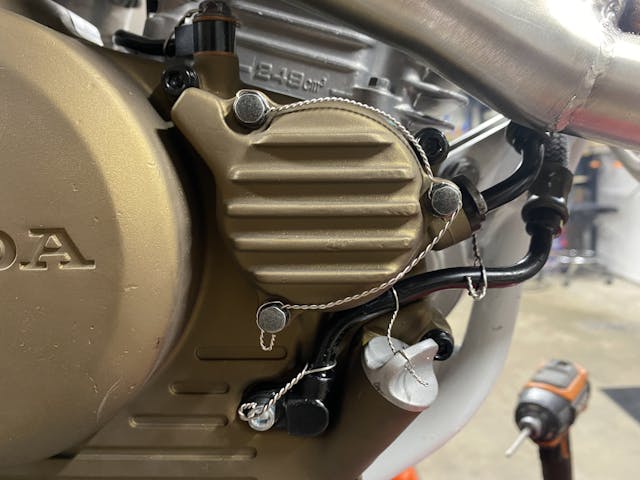
When you absolutely do not want things to start spinning on their own, you don’t leave the hard work to physics. You instead apply some type of physical retention as the final line of defense. This is the go-to for those with trust issues—and for people who fly airplanes. There is a fascinating art to tensioning and tying the strings of stainless wire between bits of hardware, carefully ensuring each pulls correctly on the next with properly minded ends.
I’m not an A&P (airframe and powerplant) guy, nor do I pretend to be, but even I can do safety wire that will retain hardware for the likes of my track motorcycles. I take comfort in knowing my oil lines will not be coming loose—although recently I did see a safety-wired line puking oil everywhere, but that’s because the banjo bolt broke. Which is a good reminder that the safety wire only prevents the hardware from turning, not from failing. Other styles that are easier on the hands include various types of lock washers that either dig into the materials or can be folded to prevent rotation. Of course, there is always the cotter pin and castle nut arrangement as well.
***
Even the simplest parts of our cars are hardly simple. Just keeping the thing together as it rolls down the road is a feat of engineering that I only scratched the surface of here. Any of us who choose to do our own work at home need to understand at least the basics of these items, though, so we can better understand appropriate reuse of parts and hardware, along with proper assembly. It’s the hardware that keeps us driving—best keep it together.
Don’t forget Tab Washers. These used to be relatively common on exhaust manifolds and the like. They’re also still pretty much the standard for bearing locknuts, etc.
On aircraft applications safety wire may not always maintain proper torque, but it will keep the fastener (or turnbuckle or rod end, etc.) in place. That safety wire job shown in the picture has the wire pulling the wrong way (it should always pull in the tightening direction). Still, even done imperfectly safety wiring is generally very reliable. For non-aviation use cross-drilled hardware is not always available in the sizes we need, although there are commonly available jigs for this.
Also, castellated (or cross-drilled) nuts bear mention. These are most often seen on spindle nuts and bearing locknuts. They’re also used a lot in aviation, particularly on older aircraft.
I’ve occasionally seen these with hairpin clips on fasteners that need to be secured but frequently removeable.
Stevie B’s comment about index marking is a good suggestion for critical fasteners as well, regardless of what retention method is used.
Torque specifications are a whole ‘nother can of worms. Bolt material, thread pitch, bolt length, lubricated vs dry, nut type, threaded hole depth, material and type, etc. , plus age, corrosion, etc. all come into play.
“Hardware Retention”
Tell me I’m not the only one, who from the title, thought about the coffee cans and drawers full of extra nuts and bolts I have in my shop…that I will use one day.
😁
LOL – thought I was the only one! Always telling myself to buy some parts bins and sorting all the different size bolts, nuts, washers, etc. then realizing it would probably take 2 lifetimes. Keeps the blood pressure up trying to sort through all the coffee cans, buckets, drawers, & old tool boxes looking for that right size bolt or nut.
100 percent what I thought this article was going to be about. Lol
Axle bearing nuts use castleated nuts and cotter keys so they don’t come off. Especially on the drivers side (left) which would be the first to spin off. Once you set the tension on the bearing the cotter key keeps the nut from turning in either direction. You can’t torque a wheel bearing in most cases.
During my offroad bike and quad days, I used bright Yellow fingernail polish for a visual to see if anything had loosened up. A line across a bolt end and nut, or two dots next to each other worked great. I didn’t want to break the chemical bond ( ?? ) of Loctite by putting a wrench or socket to the nut if the lines or dots hadn’t moved.
Worked for me and saved a lot of labor over the years.
On the issue of fatigue in reused bolts:if the fastener won’t reach a torque setting appropriate for the bolt size and grade or feels mushy as you approach that torque setting discard it , as it’s probably fatigued and may fail…
Kyle, this is a good overview, but also the basis for a more technical article. Some of the questions to be addressed would be: 1) Torque specs are based on dry new fasteners. What correction should be applied when using liquid thread locker, which is a lubricant? I read 20% less but can’t verify it. 2) What about those KTM and BMW bolts which come with a dry thread lock applied and are rated as “single use.” Of course, most of us just put on blue Loctite and use them again and again. A good idea?
Locktite used on older hardware may not work. If the threads on the bolt or nut have been “chased” with a tap or die several times, the gap between the mating surface will be wider and allow air to be captured internally at the threads, so the locktite will not set up properly. Found this out the hard way while working on missile hardware after vibration testing caused parts to fall off!!
Years ago my brother and I rode motorcycles from his house in Oregon to glacier national park. I rode his BMW following him on his recently restored Harley. I watched parts and stuff fall off his Milwaukee vibrator. Muffler bolt came loose and pipe was bouncing around. Then his shifter peg fell off. Luckily I saw where it went in the grass and we found it. He lost a wine skin with water that fell of the back of his bike. He did pack loctite so we fixed stuff on the side of the road. Good times
I had a Norton Matchless. I’ll see you out there.
When my wife saw that I was reading this article, Kyle–she asked if this meant “cutting off the childrens’ hands if they touched the hardware” as a means of “retention”. Smirking
No mention of serrated lock nuts?
Never ‘gift’ your loved-one a torque wrench long enough to be used as a club… ask me how I know.
no one mentioned the often used castle nut and cotter pin
Check the end of the second to last paragraph… The author mentioned it.
Wire twist pliers are my coolest tool.
Your lock wire job is poorly done, I wouldn’t use this picture as example for your article . In aviation, it will be cut by the quality inspector ….
Yes, I’m sure all race tech inspectors work in the aviation field… super pertinent to an article concerning automobiles…
CR’s point about the image is correct; the wire job is done backwards; it won’t retain from loosening.
The top bolt on the motorcycle pic is safety wired backwards.