Media | Articles
4 Levels of Hardware Retention
Our beloved vehicles are massive assemblies of parts. Some of those parts are superfluous to the critical function of a car, so if they fell off we might get a bit of a chuckle at the situation. Other parts we want to stay tightened and torqued exactly how we set them, and that means some form of retention on all those nuts and bolts is imperative, lest our wheeled machines quite literally lose their wheels. Amazingly, this is all less complicated than you think.
Threaded hardware is all about friction. The threads are little more than long spiraling incline planes that wedge against one another, and the friction of the two surfaces is too great for the hardware to turn without outside assistance. Vibration and heat conspire against the smooth bond though, as differing materials could potentially expand at different rates and reduce or spike the load on the threads, allowing things to rotate even fractional amounts. Small, unnoticeable changes over time compound into catastrophic failures. Ever seen a loose wheel and tire rolling down the freeway? Terrifying. A drainplug that falls out and turns an engine into scrap metal? Nightmare fuel.
So how do our cars not fall apart? Well, it boils down to just a few types of retention. Here are the key ones:
Torque Spec
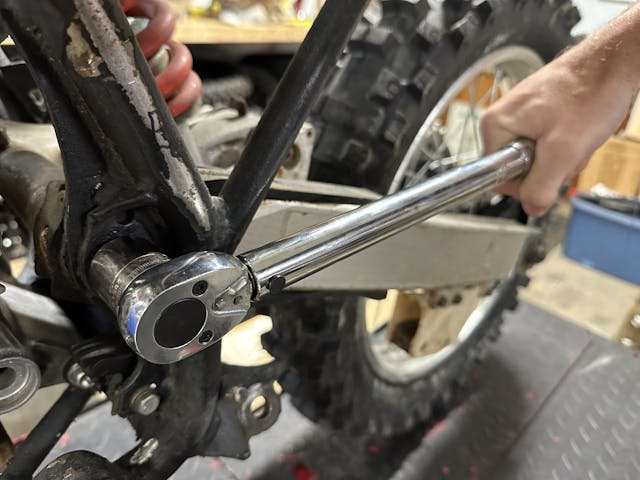
A proper torque specification uses the threads to stretch the hardware enough that it will not lose tension during its intended use. For a lot of common hardware, the torque spec is fairly low, enough to be done by hand with relatively small tools. Just the stretch of the hardware can be enough to keep things clamped tight for a long time.
The perfect example is torque-to-yield bolts that are tightened by degrees of rotation rather than torque. This more accurately sets the clamping load of the hardware, and with the proper number of threads it takes a lot of force to break those back loose. If you need more than that, start looking at . . .
Marketplace
Buy and sell classics with confidence
Chemicals
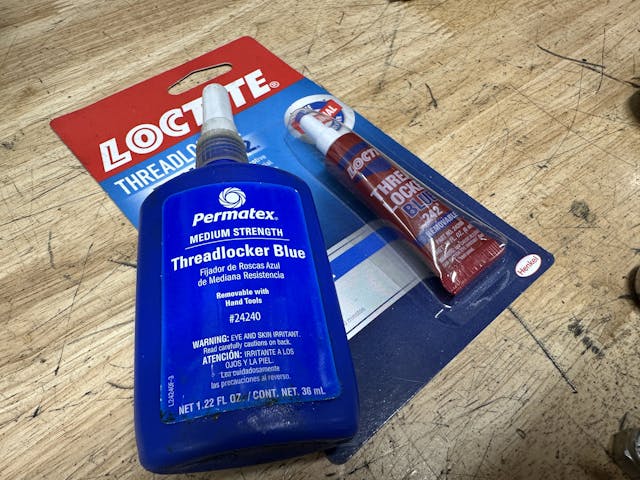
Fresh and clean assemblies might need just a little help to ensure everything stays tight, and one of the easy and cost-effective ways to do that is with liquid threadlocker chemicals. These are typically anaerobic-curing adhesives that essentially glue together a portion of the threads as they are final-assembled. The anaerobic part just means the formula cures without the need for oxygen, a good thing consider how tight the tolerance is on threaded hardware.
But threadlockers have limitations, like cure times and cleanliness standards, along with no visual indicator that it was actually applied—unless the installer makes a note. This can lead to frustration if higher-strength threadlocker is used in an area where it cannot easily be heated to help break its bond.
Additional Friction
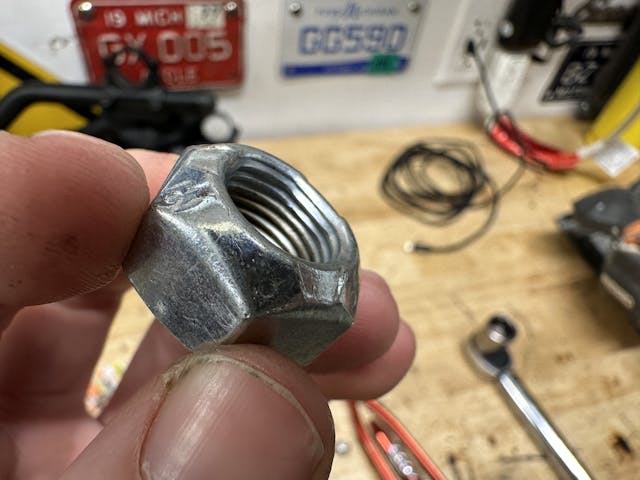
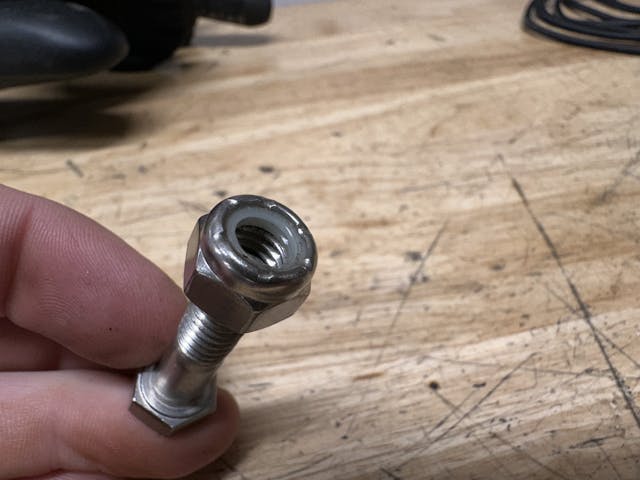
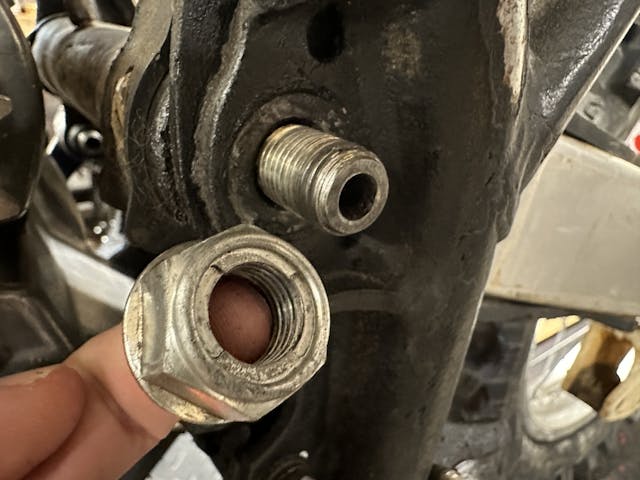
The threads might be one source of friction, but they don’t have to be the only source. Adding an additional feature or piece to the hardware that increases the amount of torque required to turn a fastener can be a solution when more clamping force is not needed but additional turning resistance is.
Two popular options for this are nylon-insert locknuts (aka nylock or nyloc) or metal washers, which are added to the back side of a nut to provide additional friction when the final tightening of the hardware is done. The nylon option does require temperature consideration in the final install. Nylock-style nuts are not the solution to header flanges that always loosen, as the nylon would be cooked off and gone after the first heat cycle.
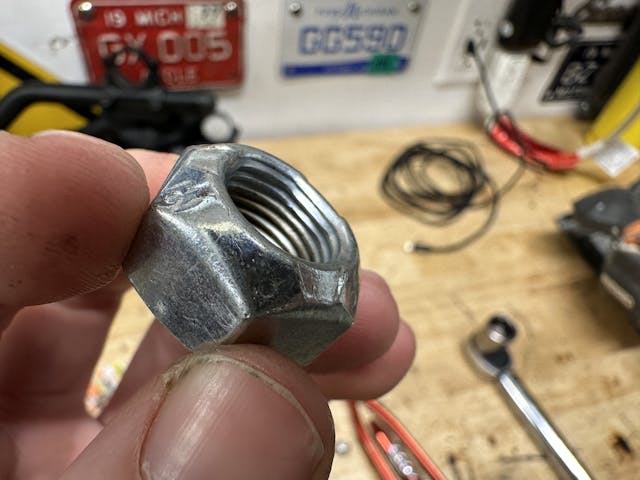
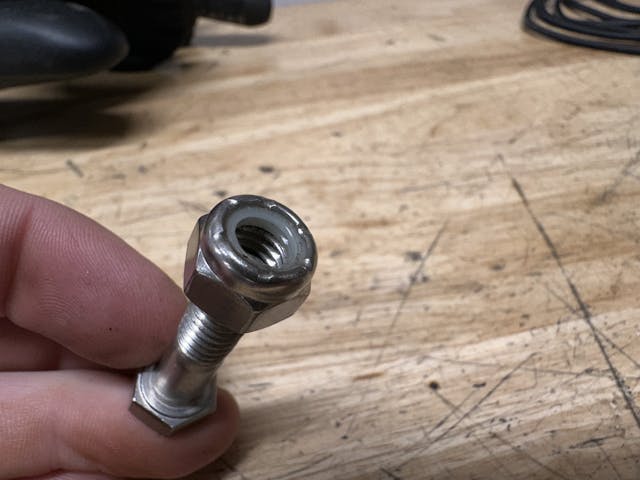
For something like that, it might be better to use a metal waster that deforms rather than the nylon. Another option for this is to have the final few threads of a nut be deformed just slightly. When using this type of hardware it should be factored into the final torque setting, if applicable, and most deforming hardware has limited ability for reuse, as each use lowers the performance of the specific part you are using it for. So if you need retention and serviceability, maybe it’s time to think about . . .
Positive Retention
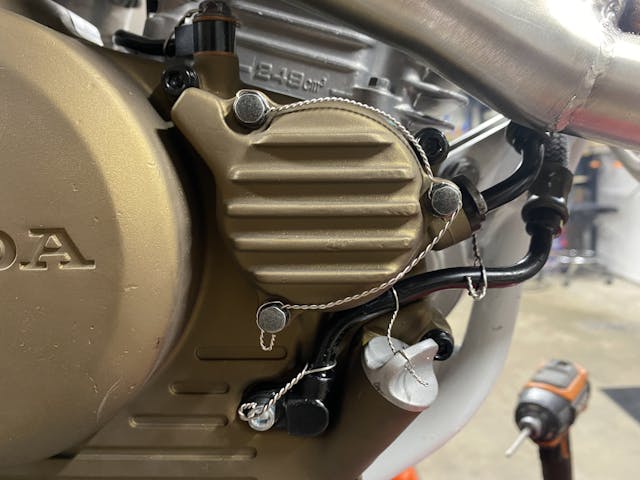
When you absolutely do not want things to start spinning on their own, you don’t leave the hard work to physics. You instead apply some type of physical retention as the final line of defense. This is the go-to for those with trust issues—and for people who fly airplanes. There is a fascinating art to tensioning and tying the strings of stainless wire between bits of hardware, carefully ensuring each pulls correctly on the next with properly minded ends.
I’m not an A&P (airframe and powerplant) guy, nor do I pretend to be, but even I can do safety wire that will retain hardware for the likes of my track motorcycles. I take comfort in knowing my oil lines will not be coming loose—although recently I did see a safety-wired line puking oil everywhere, but that’s because the banjo bolt broke. Which is a good reminder that the safety wire only prevents the hardware from turning, not from failing. Other styles that are easier on the hands include various types of lock washers that either dig into the materials or can be folded to prevent rotation. Of course, there is always the cotter pin and castle nut arrangement as well.
***
Even the simplest parts of our cars are hardly simple. Just keeping the thing together as it rolls down the road is a feat of engineering that I only scratched the surface of here. Any of us who choose to do our own work at home need to understand at least the basics of these items, though, so we can better understand appropriate reuse of parts and hardware, along with proper assembly. It’s the hardware that keeps us driving—best keep it together.
As a powerplant guy, I would tell you that safety wire is not intended to keep the fastener tight. It is intended to keep it in place and prevent it from becoming foreign material if it does come loose. I would not rely on it for tightness.
Military 2.5-ton hubs use twisted safety wire between pairs of nuts to keep the hub fixed to the brake drum. I think the 5-ton truck hub-drum assemblies are the same. I’m talking M35, M54, M813 and related trucks. I think they might have a torque spec too, can’t remember.
I guess its a “belt and suspenders” deal. Yes the safety wire will not keep a fastener tight or ensure its correct torque remains in place but it will, as far as automotive uses, make it less likely that a bolt or nut will simply part company with the rest of the car. If that happens, and depending on the situation, that loss of a bolt or nut can have dire consequences. A loose engine mount is bad, an engine falling out of the car is much worse.
I have made it a habit, based on my own experience with Murphy’s Law (and noting that Murphy was in fact an optimist) to “nut and bolt” any car I run on the track before and after each track day. Sometimes that may only be a few (3-4) hours on the track but vibration and the pounding of high g-forces means that stuff comes loose. That saying “an ounce of prevention is worth a pound of cure” could never more accurately describe both the terror and relief when you find a loose suspension bolt and realize that but for it remaining in place there would possibly been no why to know what caused the “fatal crash”. This is also why, although I am more a driver than a mechanic, I have taught myself as much as can be gleaned on the process of how to “nut and bolt” and use blue/red (depending on application) Loctite like it is water- cheap insurance to keep stuff where it is supposed to stay. That and I paint mark every fastener and joint to be sure I can visually check while at the track. Has saved my butt more than once.
Personally I’d take Loktite over safety wire any day of the week. My big concern with safety wire is you are drilling a hole right through the head of the bolt, and particularly on external applications, if the bolt is loose, you can see it. If it is safety wired, that thing can sit there loose, fretting your threaded hole into a nice smooth bore before you notice anything is wrong. Different strokes for different folks
Yes I agree , just had a bolt go through the ring & pinion on my 36 Ford with a two speed Columbia rear axel . The Ring gear is safety wired to the spider gear carrier however the Colombia side is not where the bolts broke . What came first the ring gear teeth broke or the bolt came loose? A little blue lock tight I think could have prevented this.
Good comment! Not coming out and staying tight are indeed two different things.
Right. That top bolt in the photo above can loosen up about 1/4 turn before the wire can have any effect.
Looks like all 3 could come loose unles the safety wire is straight from one fastener to the other. It looks nice but not very fuctional.
One other method is the use of “jam nuts.” These nuts are half the thickness of a regular nut. Using them requires that the bolts have a fair amount of exposed threads after the regular nuts have been tightened down. You just add the jam nut, put an open-end wrench on the main nut to keep it from tightening more, and tighten the jam nut against it.
Yes indeed!
Those of us that live in colder climates know that common rust (Fe 2 O 3 ) makes an excellent thread lock. It can also be made easily and cheaply by combining common household items. Hydrogen peroxide, vinegar and salt for example applied liberally, then look for a reddish brown hue.
Hilarious!🤣
How true. Vey funny but it does work especially with aluminum rims and steel hubs. Bimetallic corrosion works wonders.
Hard snicker ‘mate !
On some folks’ drag cars in the ’60s and ’70s, a lot of things that didn’t HAVE to come apart at the track got a tack weld on the fastener. Not mine, which is probably why I dropped the front bumper off a ’56 Chevy and ran right over it just after hitting second gear. (I lost that race…)
Good article, but I’m left with a question: how valid are torque values for fasteners that have been reused many times? My stable of old crocks each have well over 200,000 miles on them, and most parts (suspension components, engine parts like water pumps, etc.) have been on and off many, many times. I know this because of all the “creative” fixes I see from previous owners.
When I replace something, I inspect the fasteners carefully and replace defective or super-critical ones, but for the ones I reuse, e.g. brake caliper bolts, water pump attachment fasteners, a/c attachment bolts, etc, how should torque values be adjusted? Those fasteners have stretched over the years, and my experience is that applying factory torques results in looseness down the road. If the interlocked slinkies are now pulled further apart, aren’t they attaining a greater slope, thus resulting in less of the friction surface area? Short of replacing every fastener, which is gonna be horribly expensive, it’s hard to know.
Remember, it’s not just the fasteners stretching, it’s also the threads into which the fasteners are going that experience some deformation after multiple outs-and-ins (albeit to a lesser degree, I’m sure). It’s an interesting question!
Quality of fasteners has declined over time as well.
I did some lab testing in college on a handful of old Deere bolts vs brand new, same grade fasteners from the box store.
Much greater margin in the old Deere bolts, vs box store bolts that often BARELY made their grade criteria.
When I torque fasteners in a series – lug nuts, rod bolts, etc – I pay attention to how far I turn the wrench on each nut or bolt at each step. If the wrench turns with a different feel from one to the next, something is wrong and needs to be fixed.
I replaced the rod bolt castle nuts with nylock nuts in a Model A after shimming the babbitt bearings . I ran it by the Model A group using the nylock nuts, that became very controversial if they would come loose running in oil. The original castle nuts had cotter pins . I guess time will tell.
Good summary article. Could you do another on when to use:
a. just a bolt
b. a bolt with a washer
c.a bolt and lock washer (and do I use a flat washer as well?)
Thanks in advance
A manual with the proper torque specs is always my first weapon I go to.
Some great comments about the most common and yet most misunderstood devices. Static loads are one issue, but the most important ones are the fasteners with cyclic loads. The tension on the bolted joint must significantly exceed the loads applied (Connecting rods anyone?).
There are some great references for the average hobby mechanic to the pro. One of the best is by Carroll Smith, “Nuts, Bolts, Fasteners and Plumbing” Also known by its unofficial title “Screw to Win”. https://www.carrollsmith.com/books/nutsbolts.html
This is a single page that provides some excellent graphics on bolted joints and backs it up with the math.
https://mechanicalc.com/reference/bolted-joint-analysis
I had a wheel come off my 1951 Buick Super because I didn’t sand off the powder coating where the rim contacts the brake drum. After a few hard turns the coating became compressed allowing the lug nuts to come off. The damage to the left rear fender and the trunk lid surround cost me a LOT of money to have repaired.
I’ve heard of this happening after powder coating wheels also. Torque & re torque several times .
Please keep in mind products such as Loctite have expiration dates on their labels. Probably not a concern for the shade tree mechanic, but if you are racing or flying, it might not be a bad idea to double-check. I learned this the hard way (Is there another way to learn?) during an ISO 9001 audit of our manufacturing facility. The auditor observed an assembly mechanic applying thread lock before torquing some hardware. He asked to see our procedure which included a reference to the threadlocker and required torque value. He than asked to see the expiration date on the container. He then wrote a minor audit finding. We then combed through our assembly areas and discarded a lot of expired containers. Of course we wrote a new procedure and added another item to our Pre-Audit check sheets.
Vibration and heat conspire against the smooth bond though, as differing materials could potentially expand at different rates and reduce or spike the load on the threads, allowing things to rotate even fractional amounts.
I know this one. A spark plug unscrewed itself on my Solara V6 after 4 years and 200k km (125k miles) damaging the coil pack and blowing some fuses. Fortunately, it did not damage the threads. A new spark plug, used coil pack, and the aforementioned fuses and it’s back on the road.
FOD, foreign object damage, worked as a mechanic at O’Hare, we installed magnets on the front and rear of tug tractors to collect nuts, bolts and other pieces of metal that dropped off equipment, we safety wired, Loctited, and used lock nuts on everything we repaired, those magnets we installed collected a tremendous amount of metal Debree.
In my days as a manufacturing manager in an industrial environment, I was not directly involved in machine maintenance but I saw too many issues to not get involved. I worked continuously to try to convince the maintenance people that every nut and bolt needed either never-sieze or some sort of Loctite/locking fastener when installed. Too much time was spent removing stuck/broken bolts fixing stuff because some fasteners had become loose. Not directly related but it was always interesting to see the zillion different approaches to loosening stuck bolts. Home made recipes, PB Blaster, you name it, everyone had their favorite and swore by it.