Media | Articles
Mattel turns actual cars into Hot Wheels at the Handler Team Center
The Handler Team Center, formerly the Mattel Design Center, is located in El Segundo, California. It was named for Mattel’s founders, Ruth and Elliot Handler, who are responsible for Barbie and Hot Wheels, respectively. Even from the curb, you can tell there’s something special happening inside, as the entry ramp includes a Hot Wheel track and you follow either Barbie’s footprints or Hot Wheels tire tracks up to the front door.
Hot Wheels invited us to take a look inside the Handler Team Center to learn how Hot Wheels and other Mattel toys move from concept to production. As we were set to be judges at the Hot Wheels Legends Tour the following day, we were primarily focused on the 1:64 scale cars that make up the world’s number one toy brand. That said, there’s a ton more going on inside this building than just cars.
Leading our tour was Bryan Benedict, the design director for Hot Wheels and Matchbox. Benedict is an Art Center grad and has been with Hot Wheels for 19 years. Here he is showing us the major steps in the design and production process for turning the Texas Toot, last year’s Hot Wheels Legends Tour winner, into a 1:64 die-cast. The entire design process can take up to 18 months. Meanwhile, HotWheels has to secure the licensing to make a toy using an automaker’s design. Hot Wheels casting library includes all of the models that Hot Wheels still has licensing to create. Contracts get renegotiated and new contracts get written all the time. Hot Wheels creates about 50 unique models every year and will repurpose previous designs with new colors, graphics, or other treatments to create 400 additional designs.
This color chart shows the various colors that are available at Hot Wheels’ major manufacturing plants. MBK is in Thailand MMSB is in Malaysia. Some multipacks are also produced in Indonesia
We got to see Texas Toot in person when it won last year’s Hot Wheels Legends Tour, earning the right to become a 1:64 toy. Designers first 3D-scanned the actual vehicle and then refined the design. Manson Cheung sculpts Hot Wheels and is often tasked with bringing two-dimensional sketches into three dimensions, something that takes true artistry. He has to keep the production tolerances and final vehicle durability in mind when designing, while still rendering all of the vehicle’s character. Cheung gave us a hands-on demo of their modeling software, called Freeform, which emulates how they used to design Hot Wheels using clay. The articulated stylus, shown on the bottom right of the photo above, gives feedback when interacting with the 3D model, allowing designers to “touch” the computer model and carve it just like clay.
The wheelbase of a Hot Wheel car is virtually unlimited, but there are only five options for track width, which they call chassis span. The parallel lines on this model represent the optional widths.
Hot Wheels has been using 3D printing in its development process since 1996 when it began operating a stereolithography machine, and the vast majority of its products start here. Depending on the type of toy, Mattel can print various plastics, resin, and nylon. These action figures can be tested for freedom of movement of the joints. Carbon-fiber filament can be used for testing parts that need to be strong and thin, like pieces for RC cars. They even have a 3D printer that laser-welds powdered 17-4 Stainless steel to create durable metal parts. Mattel runs two additional 3D printing facilities, one at its Fisher Price facility in Buffalo, and a third in Malaysia.
“Once it’s approved, we turn it over to our development engineers in Malaysia. They will then work with us to part it out and create the four-part car like you see here,” Benedict explained, holding up a red, blue, and black prototype. Before moving forward, designers make sure the gaps are correct and the design has carried over into the prototype. Then, it’s time to cut metal for the dies. Engineering pilot samples are in metal. They get scrutinized, but by now they’ve got the design and function dialed in. “Sometimes there are some minor tweaks needed,” said Benedict. This is the point where the car is tested for safety and durability.
When that’s approved, it moves to the final engineering pilot, a test run that shows the car for the first time it’s in full color. If everything checks out, it moves on to the final product and packaging phase.
You’ll find the same kind of passion and creativity throughout the toy development at Mattel, something that became clear when we stopped by to see how the legendary Barbie is styled through collaborations with designers and music legends alike. This makeup inspiration and its final product is the result of several steps of masking and painting. Mattel designers must make sure that the process is repeatable when the products go into production.
Shirley Fujisaki gave us a demonstration of how doll hair is sewn in using an intimidating sewing machine that spun loops of hair fibers into position and set them in place to survive the rigors of being a child’s play companion. Fujisaki is a licensed cosmetologist and another Mattel veteran with years of experience.
In a building full of visionary car designers and creative artists, Paul Schmidt might have the coolest job. He’s responsible for designing the tracks and playsets that Hot Wheels cars interact with. He told us that he prefers to start his designs with simple foam core and poster board to help bring his imagination into reality, but other designers go right to 3d modeling. Sets he works on range in size from a drive thru burger joint that retails for less than $20 to three-feet-tall garages that house 100 Hot wheels and a looping, jumping playset that launches Hot Wheels cars at a menacing dragon.
This set of four playsets shows the various steps in production. Moving clockwise from the white foam core and posterboard concept is the first 3D modeled part. The colors here match the final design, but the details aren’t set just yet. The initial test model, shown on the left, has almost all of the details, but the parts have been cast in leftover plastic from whatever happened to be in production at the time. The final design in the back has the proper colors and looks just like the production product, minus the stickers.
Matt Gabe, the lead designer for Hot Wheels packaging, gave us a quick look at the process of creating the iconic Hot Wheels blisterpack. Gabe knows some collectors like to keep the packaging intact, but it’s also a win when he sees his hard work end up in the trash, as it means someone is enjoying playing with the toys. Sometimes Gabe and his fellow designers get to flex their creative muscle and drum up packaging that’s a noteworthy display for the product and makes the vehicle inside even more special.
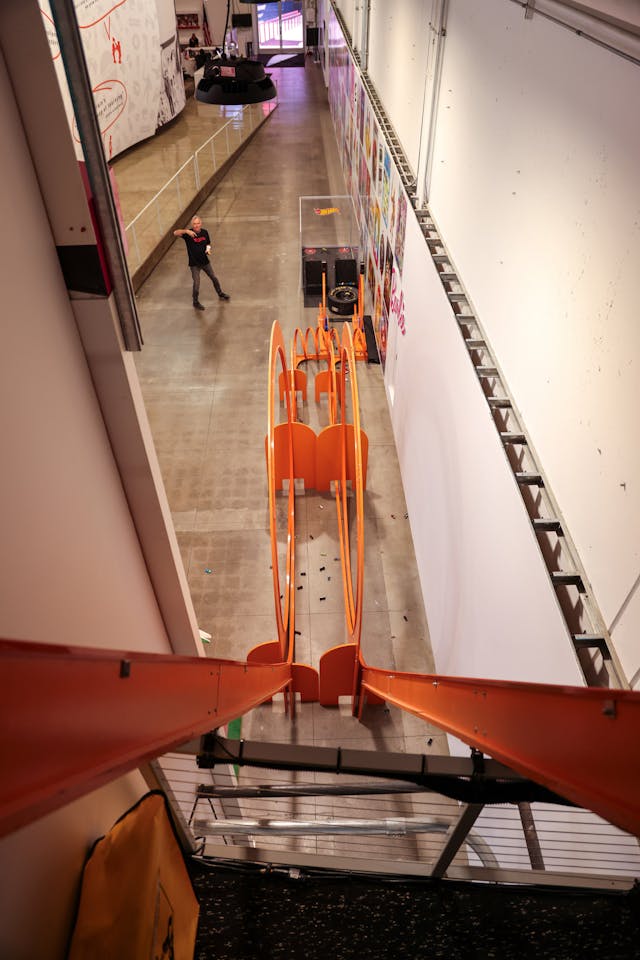
If you’ve got a favorite Hot Wheel as part of your collection, let us know its story. Are you a meticulous collector with scores of intact blisterpacks, or do your cars roam free on your bookshelf or desk, like many of us here at Hagerty?
***
Marketplace
Buy and sell classics with confidence
Check out the Hagerty Media homepage so you don’t miss a single story, or better yet, bookmark it. To get our best stories delivered right to your inbox, subscribe to our newsletters.
I liked it where the Hot Wheels were a but less over the top. Even the customs were not as goofy as some of these are getting.
I saw a street rod truck the other day called Gotta Go. It had a toilet seat on the bed? That is a long way from the Deora or Split Image.
I miss more of the customers like the 57 T bird or 36 Ford Coupe I have yet today. My mom bought those for me and they really had an effect. Especially the 36 Coupe.
I agree about the silly, over the top stuff, but I don’t think were are the target audience.
Texas Toot? That’s what happens to me after dinner at my favorite Tex-Mex restaurant.
Thank you for the most enjoyable article about Hot Wheels. I have dozens upon dozens of hot wheels that I have accumulated over the years. I prefer the one that look like real cars but sometimes the creations are interesting especially when they are turned into real life size cars, trucks or other vehicles of transportation