Media | Articles
Mythbusting: The truth about the GM EV1
About halfway down the long hill leading to the General Motors Proving Ground test tracks in Milford, Michigan, it hit me that the electric concept car I was driving rolled on a cobbled-up show-car suspension and was armed with barely functional brakes. Uh-oh! It would be a supremely stupid, costly, career-ending blunder to crash this incredibly significant hand-built prototype EV by plowing off the fast 90-degree corner that awaited down the hill. Though the concept was called the Impact, I had no intention of putting that name to the test.
But wait! I recalled that the Impact featured variable regenerative braking with a rheostat control between the seats. I eased on the friction brakes, cranked the rheostat up to full regen, and barely made the corner. Whew! Shaken and chastened, I continued carefully to where I—as GM EV program Vehicle Test and Development manager—was heading to give members of the Board of Directors demo rides on the “Black Lake” skidpad.
Dramatic beginnings
At the 1990 Los Angeles Auto Show, people stopped in their tracks to gawk at this sleek, silver-bullet-shaped concept that would later morph into the EV1. Engineered and developed with high-tech California contractor Aerovironment, the Impact did more than just look cool. It could sprint from zero to 60 mph in a (then-quick) eight seconds and had achieved—in one test from 100 percent to absolute zero state of charge under ideal conditions at GM’s Arizona Desert Proving Grounds—a stunning 125 miles of range. At the time, that was better performance than any other practical electric car could claim.
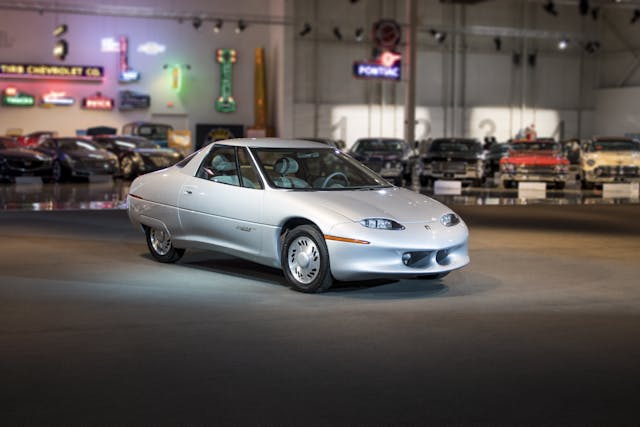
Many saw it as the industry’s automotive future. Idealists cheered while skeptics scoffed. Politicians plotted to force-feed it to the American public. So positive was its press and public reception that on April 22, 1990 (Earth Day) GM CEO Roger Smith announced GM’s intent to produce such a car, targeting 25,000 units a year. Ken Baker, then head of Advanced Vehicle Engineering for GM’s Chevrolet-Pontiac-Canada Group, was recruited to lead the effort.
“We recognized the obvious shortcoming of EVs,” Baker later said. “Our plan was to be battery agnostic—take the best available and focus on engineering the world’s most efficient vehicle, which would give dramatically better performance once a better battery came along. We had just come off of the success of the [race-winning solar-powered] SunRaycer and were encouraged by the sold-state electronics that had been demonstrated in that car, and [in] Impact.”
Marketplace
Buy and sell classics with confidence
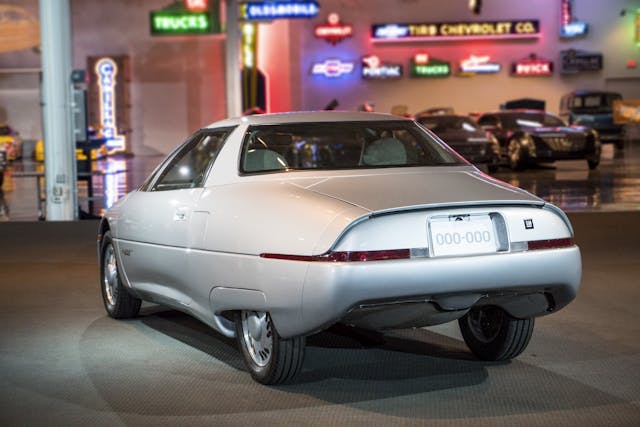
One key goal was to see how quickly and efficiently GM could do a completely different new car through a new Systems Engineering approach. The production target was just 36 months.
Then, by September 28, 1990, California’s Air Resources Board (CARB) mandated the seven top-selling automakers to make two percent of their California sales “zero emissions” by 1998, five percent by 2001, and 10 percent by 2003.
Myth: GM’s EV program was a reaction to the CARB mandate.
Truth: Other way around. GM was already working to produce a practical electric car, so CARB decided to force all major automakers to follow suit.
No business wants to be told how many of anything it must sell, since no sales mandate can force people to buy something they don’t want. And if a practical EV could be developed and built at a price people would be willing to pay, GM wanted to be there first. No one knew how many EVs could be sold, yet CARB’s mandate was nonetheless forcing GM’s six strongest competitors into an unpredictable new market.
The pause
As if that weren’t challenge enough, GM was going broke by 1992. CEO Bob Stempel and president Lloyd Reuss were ousted and Jack Smith stepped in as CEO. Smith proceeded to cancel or delay a number of product programs and (apologetically) put our nascent EV effort “on the shelf.” After 27 months of enthusiastic hard work by the team, Advanced Vehicle Engineering head Baker emotionally told us that our program was delayed.
While nearly everyone inside and outside the company wrote off the project as canceled, and about three-quarters of our group was reassigned to other programs, a core team of roughly 100 of us—mostly engineers—relocated to an off-site facility and continued development work. Baker was promoted to R&D vice president and kept the effort alive under that organization.
In the fall of 1993, my Test and Development team planned and coordinated a series of briefings and test drives for selected media using “Proof of Concept” (POC) early development cars. The resulting articles were highly positive. “GM’s hard-charging Impact is practical, fun to drive and a master stroke of engineering,” said Popular Mechanics. “The world’s best electric car,” gushed Popular Science. Even enthusiast magazines were pleasantly surprised.
Then, as part of the June 1994 “PrEView Drive” program, my team tested and prepped a batch of 50 hand-built POC-level Impacts. These vehicles were then loaned to regular citizens in a dozen U.S. cities, for three months at a time. Virtually everyone loved them and provided very positive and useful feedback on them. We were on our way.
Rebirth
In March 1994, with GM’s finances recovering, then-executive-in-charge of corporate strategy Bob Purcell was appointed to reboot the EV program and “make a business of it.” The aim was to lead the industry in EV technology and sell it to other automakers uninterested in investing a billion dollars or more to develop their own. Later, it came out that the positive ink generated from the aforementioned media drives had helped the board reach that decision.

Purcell began restaffing our group and elevated it to divisional status as GM Advanced Technology Vehicles (ATV) Division. “There were two fundamental challenges,” he later said. “Technical feasibility—can you make it work?—and commercial viability—can you make it at a cost that people can afford and shareholders can get a return on their investments?”
Myth: GM’s EV program was never serious.
Truth: It was deadly serious, and Purcell’s career-defining direction was to make it profitable.
Our tireless ATV engineering team worked simultaneously on three generations of what would later be badged EV1: Gen I with “advanced” lead-acid (PbA) batteries; Gen II offering an optional range-doubling but a much-higher-cost nickel-metal hydride (NiMH) battery; and Gen III with more affordable, longer-range lithium-polymer batteries that 3M Company and others were developing. GM was awarded 23 different patents for its advanced technology and features associated with the EV1’s development. By rethinking and reinventing virtually every element of the automobile, engineers on this project brought to reality such breakthrough technologies as the first heat-pump automotive climate system, electro-hydraulic power steering, and power-blended, electro-hydraulic regenerative braking. A 137-hp AC induction motor powered the car’s front wheels through a dual-reduction gearset.
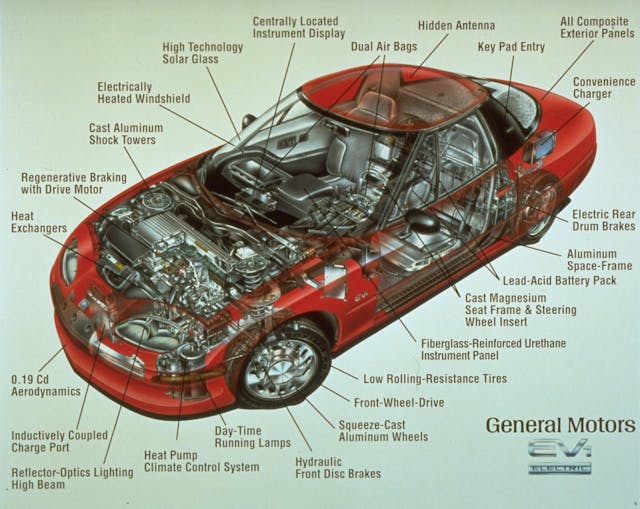
On my vehicle Vehicle Test and Development team, engineers Marty Freedman and Garrett Beauregard helped make the EV1 the most energy-efficient, practical road vehicle in the world, while former Lotus development engineer Clive Roberts delivered surprisingly good ride and handling on its narrow, 50-psi, low-rolling-resistance tires. Gently driven in warm temperatures, the car could achieve 50 to 70 miles of range and could be recharged in about four hours using GM’s innovative, all-weather “inductive” 240V charger. Household 120V charging required 12 to 16 hours.
Myth: GM could have made EV1 more appealing by giving it more conventional looks and a back seat.
Truth: Because the Gen I’s 1175-pound pack of 27 advanced lead-acid batteries held the energy equivalent of just a half-gallon of gas, the car’s shape had to be a two-seat teardrop for maximum aerodynamic efficiency. Many hours of wind-tunnel testing honed the EV1’s drag coefficient (Cd) to an astonishing 0.19. Analysis showed that stretching the car to add a back seat would hurt aero, add weight, and reduce the already marginally acceptable range by 25 percent.
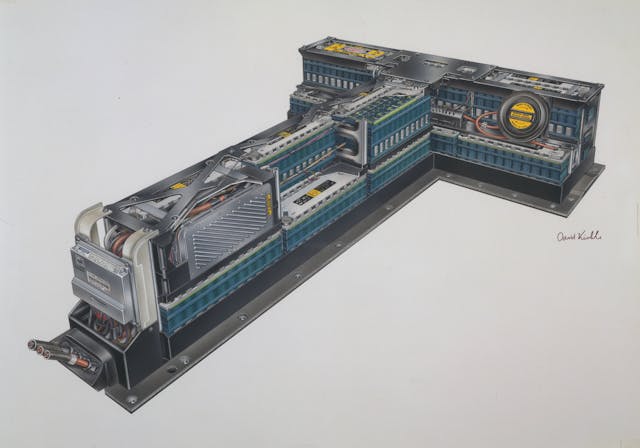
Finally, production … in a manner of speaking
All EV1s were essentially hand-built using a unique “craft station” process in the small Lansing Craft Centre plant that had previously built the Buick Reatta. In late November 1996, to a round of applause from assembled team members, the first 1997 models were loaded on transporters for shipment to specially trained Saturn dealers. Partly because production was limited by component (especially battery) availability, but mostly due to unacceptable cold-weather range and very limited public-charging opportunities, EV1s were offered strictly for lease (no sales) at a rate of $399 per month ($669 when inflation-adjusted to 2021). Leases were limited only to Los Angeles, Phoenix, and Tucson at first, then later expanded to San Francisco and Sacramento. Ultimately, just 660 of these Gen II 1997 EV1s were built (with 288 leased that first year), followed by 457 Gen II ’99s—some with the optional NiMH batteries for double range. No ’98 models were built while GM engineers reworked the battery tunnel to provide cooling for the optional batteries, which were not offered in Arizona because they performed poorly in hot weather at that early stage of development.
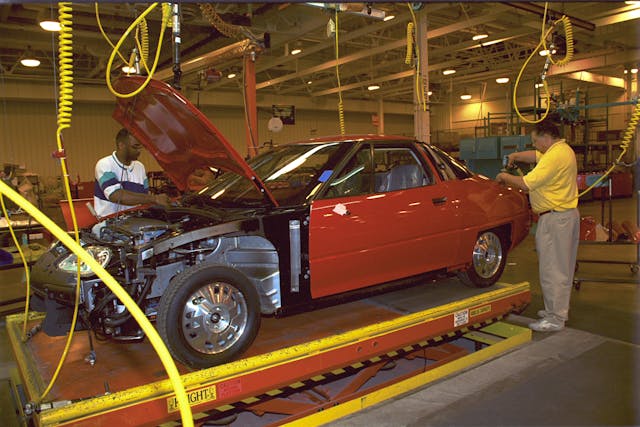
However, when EV1 customer demand proved so weak that suppliers stopped making replacement parts, GM had to pull the proverbial plug. Lithium-polymer batteries were not happening, so until a practical, affordable, gasoline-competitive battery technology could be developed, there would be no GM EV2 or EV3.
Myth: GM wanted the EV1 to fail, so it didn’t properly promote or advertise the vehicle.
Truth: Our TV and print ads were limited mostly to markets where EV1s could be leased, and for our part, my team worked hard to aid our PR department in facilitating EV1 loans to auto writers.
Toyota, Nissan, Honda, Ford and every other automaker facing California’s unrealistic EV mandate also gave up, and CARB eventually was persuaded to back off its ill-considered force-feeding of technology that was nowhere near market-ready. GM collected all EV1 production vehicles when their three-year leases expired and destroyed all but about 40 examples that were donated to universities and museums with deactivated powertrains. That made most of their lessees, who genuinely loved their EV1s and did not want to relinquish them, extremely unhappy. And, in my opinion, the nasty crockumentary Who Killed the Electric Car? severely trashed “evil” GM for stopping EV1 production and destroying the cars, while assigning little credit for what was a sincere effort to “make a business of it.” In the end, GM invested more than a billion dollars to design, develop, produce, and market a vehicle that was simply way ahead of its time.
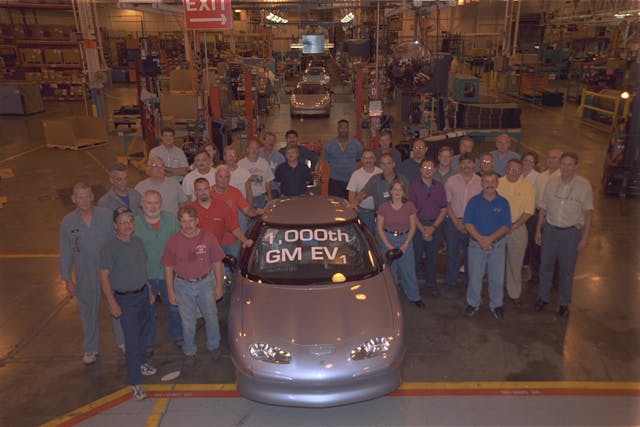
For those who contend EV1 lessees should have been permitted to buy and keep their cars, there are three practical, tangible reasons that GM didn’t allow any of them to remain in private hands. First, there were serious liability risks for both untrained owners and technicians to deal with aging 312V batteries. Second, GM had a reasonable desire to protect its proprietary technology and prevent its competitors from reverse-engineering the car. Finally, there was the matter of state laws requiring parts and service support for up to 15 years after sale—impossible since many EV1 parts suppliers went out of business or no longer made the necessary components.
Two decades later, EV buyers can enjoy a plethora of much better choices, available from several different automakers, that offer 200–300-plus-mile ranges. As an expensive two-seater with very limited range, the EV1 was a technological triumph in its day but a marketplace failure. But no one should believe that the program was unserious. I was there, I lived it, and I know better.
Myth: GM walked away from electric vehicles after canceling the EV1.
Truth: The momentum the EV1 program generated led to fuel cell electric vehicle (FCEV) research; Allison hybrid buses; plus “two-mode” hybrid technology for trucks, SUVs, and two generations of extended-range electric (EREV) Chevrolet Volts. (Successful and satisfying as the Volts were, they were too costly to be profitable.) Now GM touts the battery-electric (BEV) Chevy Bolt and Bolt EUV, with many more electric vehicles to come.
As anticipated all those years ago, the arrival of viable battery technology opened doors that were firmly shut with 1990s tech. That was the impact the industry needed.
“However, when EV1 customer demand proved so weak” Total B.S.
Why did GM fail to pay the USPTO the 10 year renewal $fees on their 20-30 EV patents that constrained progress for a decade and why would GM actively pursue “infringing” little-people and even Toyota (GM’s partner at NUMMI) in the US courts?
The GM brass dumped as many Ingersoll-Rand electric golf carts into California as possible, quoting GM VP Larry Burns; “sell as many as you possibly can in three years and pocket the credits”. As a Quaker meetinghouse, we were offered a few for free!
Why would Hagerty publish such tripe without comment?
Why would General Motors Corp. Vice Chairman Robert Lutz trash TSLA for five years? Lutz was CEO of Exide Technologies & dumped Exide’s development of the Ni-Fe Edison battrie, then walk away from 100 square miles of toxic lead in South Los Angeles.
Trust is just a four-letter word.
Disclaimer: In 2000, I bought two wood crates, each with complete controllers and GM/Hughes 15kva motors for $300 in surplus
Wonderful article about a innovative, pioneering car that is now largely forgotten.