Media | Articles
Now on Its 500th Build, Icon Has Embraced Tech While Preserving Classic Design
We’ve spent a lot of time with Icon’s hand-built, six-figure restomods over the past several years. Well, we’ve spent a bit of time in quite a few of its builds. From 4x4s and pickup trucks to 1000-hp one-offs and battery-powered cruisers with carefully preserved patina, the SoCal outfit has proved it can cover a wide swath of the premium restomod market. Countless rivals have appeared since Icon’s founding in 2007, but Icon has established itself as a shop with high build quality, rich customizability, and a signature style.
Founder and owner Jonathan Ward took us for a spin in the 500th build to come out of his shop in Chatsworth, California, and we took the opportunity to ask him how things have changed since the early days, when Icon was a Land Cruiser specialty shop.
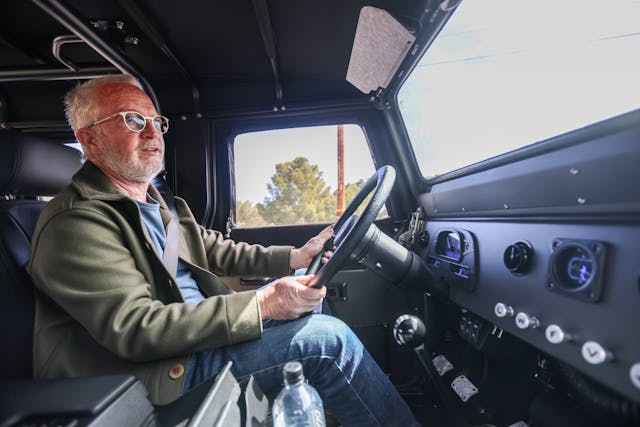
The Platform
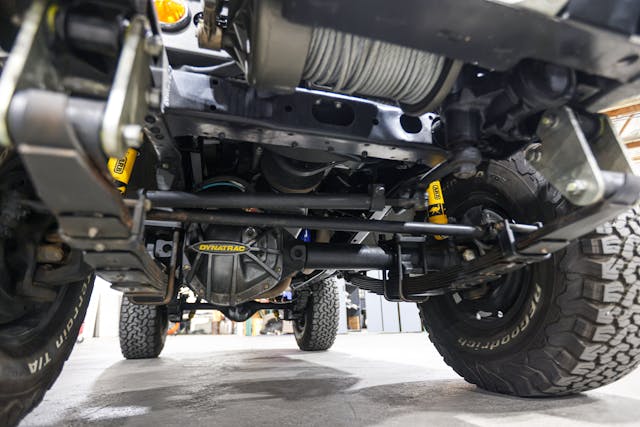
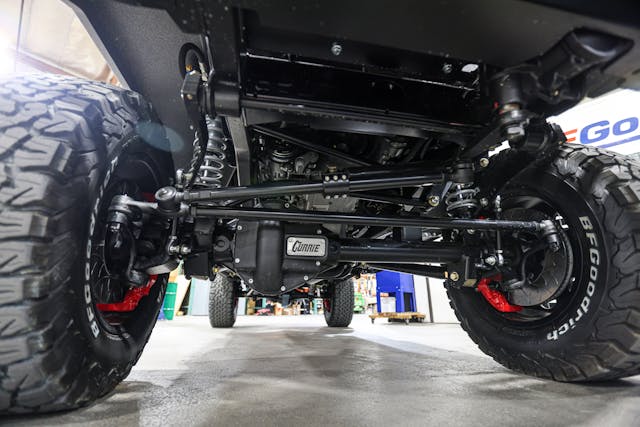
“We had a little soul-searching early on. Are we going to have to go disc/drum? Are we going to have to go with a fiberglass body?” The company wasn’t sure if there was a market for the high-end FJ it envisioned. Would Icon have to cut corners?
A friend Ward described as “far smarter and more successful” warned him not to go down that road. “If you build it, they will come,” he assured Ward. The friend backed up his words and signed on to buy the first truck.
The money from the first 12 FJ40s built by Icon was squirreled away to finance the development of the chassis for the next trucks. “The second I had enough cash,” said Ward, “We sat down with Art Morrison. We re-engineered the suspension, the [frame] rails, and the steering geometry. We got Fox Racing involved. That was probably the biggest evolutionary improvement to our product and to this day the biggest differentiator is our ride quality.” The combination of on-road comfort and rock-crawling flexibility of the link suspension is what makes the Jeep Wrangler so successful. When it has that much unsprung mass, a solid-axle 4×4 never feels like driving a modern car, but the ride quality improvement over leaf springs, like the FJ40 and the early Broncos originally had, is huge.
Marketplace
Buy and sell classics with confidence
The Process

“We used to receive our axles from our manufacturer in these coffin-sized wooden crates,” Ward explained. “We would pull all the parts needed for the build, take the axles out [of the crates], and fill that crate for the axle with all the parts for the build.”
For the first few years, they built the FJs and BRs that way, with the build techs “dumpster diving” into the wooden crates for the right part. They soon realized the method wasn’t too efficient. The impetus for the current process came after Ward accepted an invite to tour the Pagani factory in Italy. The hypercar manufacturer uses a carousel design to deliver a tray with the customer’s parts just by the staff member entering the associated client number.
Ward researched the Italian manufacturer of the system and found that while the pricey carousel wouldn’t work for his SoCal operation, he could get many of the benefits at a more affordable entry point. Now the parts, organized by model and order of installation, are stocked onto a cart that includes everything needed for that build to make it through the next step in the build process. “Before we start any physical labor, other than tearing apart the original truck, those parts come out and are palletized on that dedicated bay for that client.” Each step in the build happens the same way. Soon after the inventory system was implemented, a proprietary shop management software tied it all into the configurator on the website. “Now, when a customer presses ‘Go’ on their configuration, the software pre-populates all of the purchase orders for all of the content for that specification, saving hours of hassle.”
New processes have also changed the labor involved in transforming a worn-out project vehicle into an Icon build. Icon’s employees start by training in one or two build processes with a single model, whether it’s the Land Cruiser–based FJ or the Ford Bronco–based BR. Lately, the push has been to cross-train crew members to become certified in all stages for the vehicle line they work on—and also for all stages in the other vehicle lines. The cross-training makes the staff more flexible and allows builds to progress even when people take time off.
Parts and Partnerships
Icon used to make the exhaust system of every truck by hand. The results fit well, but the bender would crease the tubing and Ward always hoped to get a better finish. “Then we started doing our own in stainless and were just hemorrhaging time and money,” he said. Today, Icon has a relationship with Borla, whose Oxnard facility, where the company builds its short-run and prototype products, is just an hour’s drive away. Icon can now offer customers “rowdy or restrained” options depending on their taste.
As Icon’s brand grew, so did its ability to partner with more manufacturers. While the early builds featured off-the-shelf wheels, now Icon works with a U.S. manufacturer to forge four proprietary designs for Icon and Icon only. Those partnerships extend to other components as well. “We used to use off-the-shelf gauges; now we design our own face and typography to match the original but then partnered with a couple of companies, but mostly Dakota Digital, to take advantage of their technology and repeatability.”
Perhaps the best example is Ward’s expansion of textile options when it comes to selecting upholstery for his clients. Two of Ward’s companies he’s recently started, Campfire Coats and The J Ward Collection, are offshoots of his love for textiles and his journey into becoming a master leathercrafter, respectively. He’s visited tanneries in Europe, and in North and South America, and now has access to a wide variety of leather products. Synthetic material choices are also expanding. Chilewich, a woven fabric most commonly seen as placemats in upscale restaurants but also used in commercial and industrial applications, appealed to Ward: “I just thought it looked cool, and it was made in the States.” Ward has grown Icon’s relationship with Chilewich and they collaborate to create custom weaves. He’s also included luxury outdoor textile suppliers like Maharem and Knoll in the upholstery design palette. The antimicrobial, UV, and double-rub-count ratings for durable outdoor fabrics make them a great choice for the interior of a topless 4×4. “The tech specs for what the Four Seasons is gonna put on their patio furniture make automotive specs laughable,” said Ward. “It’s more expensive, but in our volume and that amount of yardage we’re gonna need for a car, nobody cares because it’s so cool.”
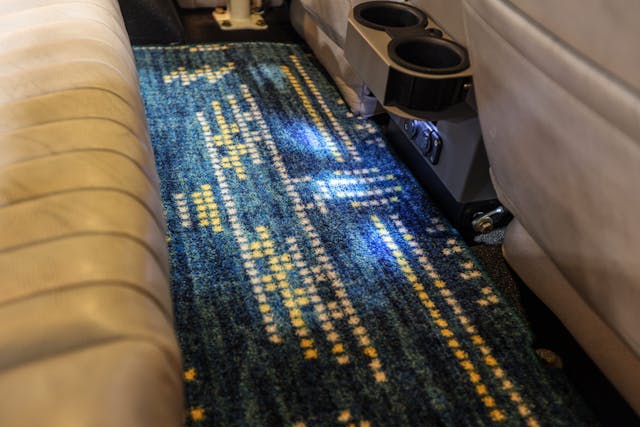
We got to see the interior of one of Icon’s current BR builds. “We’ve recently started partnering with one of the few remaining American rug manufacturers,” Ward said, referring to American Dakota. “They do a lot of American Indian partnerships and scholarship programs. Many of their patterns come from American Indian trade blankets. They make seven sizes of all their production rugs. Fortunately, the template pattern cuts for everything I need for my flooring fits within a combination of those seven.” CAD software allows the carpet sizes to be overlaid onto the existing rugs while ensuring the patterns are maintained.
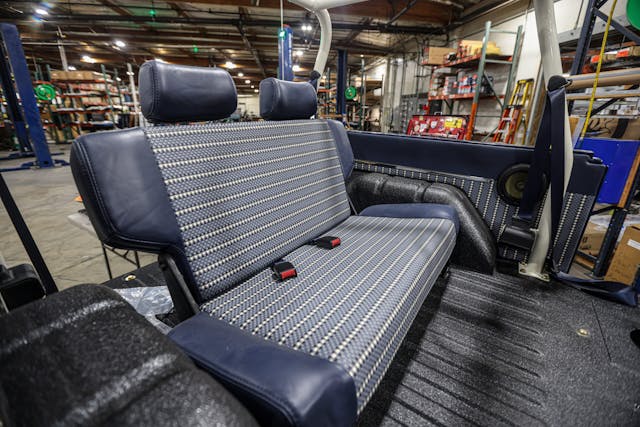
Ward showed us some of the leather weave on one of the Broncos they’re building. The shop can create custom weaves of up to eight colors and even plan specific designs. It can also use a computer program to try out other variations of those same colors and see if anything else sticks. The weave is heat-laminated to an interface to keep it from stretching or distorting. Alcantara has also made interior color matching much better in recent years. “The range of colors they have is nuts,” Ward exclaimed. “It used to be ‘two light brown, two dark brown.’ We were able to get this Alcantara exactly as we wanted it.”
They noticed in early builds that the piping on the interior stitches would be the first to show wear because it stood proud of the seam. A new French double-stitch machine eliminates the need for piping and creates an elegant, flat seam Icon can sew in-house.
Powertrains
We asked Ward about using late-model GM V-8s in its FJ products. “As much as I hear, ‘Why aren’t you putting a Toyota in a Toyota?’ people in the know in the industry, with the engineering and build experience, know that those CANbus network powertrains, outside of their native network, are a disaster,” he explained. Conversely, GM and Ford make it easy to swap in one of its crate engines. Besides that, there’s precedent. “Chevy V-8s have been put into Land Cruisers since there were Land Cruisers,” said Ward. It’s also worth noting that the Toyota inline-six used on the early Land Cruisers was based on a GM engine design.
Icon isn’t buying crate engines from GM, but the two companies have a relationship that allows Icon to get the right engine for the application. “We can mix it up,” Ward said, explaining that his shop can select the engine, front engine accessory drive, and intake that fits a given chassis and engine bay while providing the proper torque curve for a truck. While the early builds used Gen I Chevy small-blocks, they have been supplanted by all-aluminum Gen III engines. “We’ve benefited from riding on GM’s coattails. We just evolved with them.”


“With Ford engines, we buy direct from Ford and have to buy them five at a time. It’s kind of a bummer for cash flow,” Ward joked. Icon uses the production Mustang GT engine, and it’s nice match for the compact Bronco, revving freely and producing an appropriate exhaust note.
Ford is supposedly working on an emissions-compliant Coyote to compete with GM’s E-Rod engines, a prospect that excites Ward. Even though the majority of the vehicles Icon builds are exempt from most emission regulations, each vehicle gets an evaporation system, catalytic converters, and wideband O2 sensors. Power output is still fantastic, and the vehicle doesn’t fill a garage with fumes. Icon designed its own baffled fuel tank and machined a filler neck to work properly with vapor recovery pumps. “To add a rollover valve and the appropriate plumbing for an evap system, at that point, it’s negligent not to do it,” said Ward.
Transmissions have also evolved at Icon. “In the old days, we ran a New Venture 4500. They’re super heavy, they’re super clunky, with 10-foot throws. We developed adapters in partnership with Advance Adapters to run the brilliant, underused, and underloved Aisin Warner AX15 used by Jeep, Toyota, and Dodge. I love the feel of that trans.” The only one he likes better is the Tremec six-speed, which Icon uses on the rear-wheel-driver Thriftmaster trucks. “I’d run Tremecs in everything, but they’re not transfer-case-adapter friendly.”
The Engineering
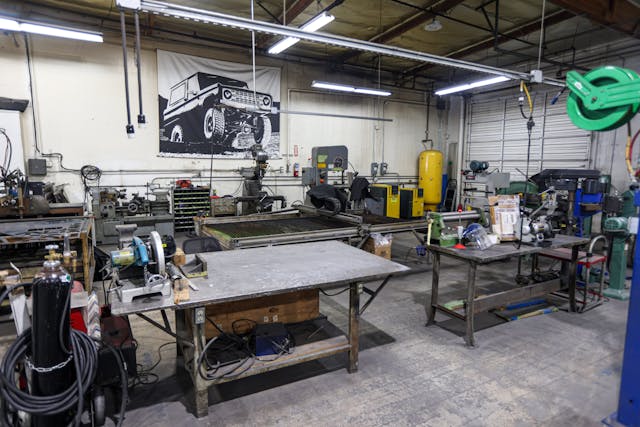
From bumpers and center consoles to brackets and widgets, Icon has spent years transferring its fabricated designs into computer drafting software. “We’ve constantly been doing this, but we’ve finally gotten to the point that it’s pretty much all done. It’s all locked down in CAD,” said Ward. That eliminates a lot of hand-fabrication and allows the small but time-consuming parts to be outsourced to regional sheetmetal shops, often those in the aerospace industry. “They have tools I could never afford with my volume,” Ward said. “The results are 100-percent interchangeable parts with fantastic repeatability that are turned around faster and built more affordably than if they’d been tinkered with by hand.”
Icon’s basic rule is to hand-fabricate the first four versions of a new part, evolving it closer to a production part each time. When the prototype reaches its final production form, they lock the design down into a CAD file. If a customer wants a one-off version of an existing part—a custom center console to house a new radio shape, for example—the CAD file can still serve as a starting point.
The Philosophy
Something that hasn’t changed over the last 500 builds is Icon’s philosophy. “I’ve learned in previous business decisions and career moves to protect the ethics, the DNA, and the core values of the brand at sometimes extreme cost. Turn down the collaboration if it waters down the brand,” said Ward. As Icon evolves, the production changes have to pass a set of core tenets, and they often get settled during companywide meetings. Staff have helped guide build processes and add options to the vehicle lines. It boils down to the products looking the part but more importantly, holding up to the promise made by the classic design. “I want the conveniences, the comforts, and the safety,” Ward said, “but only to the line of being able to respect traditional industrial design ethics of simple, strong, longer life, built to last, and built to be fixable.” Icon’s customers believe the same. They still expect modern amenities to a point, and nothing is keeping them from getting seat heaters, a modern sound system, or navigation. “All in all, they don’t want the martyrdom of vintage,” says Ward, “but they want the essence of retro.” Ditch the carburetor, the drum brakes, and the leaf springs, keep the silhouette, the clean interior, and the classic vibe.
The Future
Icon’s products have improved over the years, but what’s next? We asked Ward if Icon’s forays into EVs will result in a production EV 4×4. “There is a mule in development right now,” he replied. The plan is to study what’s out in the market and go the extra mile to fill in the gaps to make it safer, stronger, faster, more reliable, and easier to service. Ward hopes to get all of the details right so that a demanding consumer can jump in and get the experience that they expect. “We’re gonna test it, beat it up, quantify the engineering with a third party, and then put it onto production.” A prototype should be on the road—and off—by early next year.
The Icon trucks look great. I still wish they had a Toyota/Lexus engine option myself.
Huge fan of the ICON builds and Jonathan’s ideas.
Hello, my name is Gustavo and I own a 1989 Toyota Landcruiser still running but it starts to smoke, I am considering rebuilding engine and transmission as well and since i been looking on line for this project, would you be able to give an estimate? Also I am looking for some parts at the moment, such as the speedometer cable and the throttle cable too, would you have these two available in stock? I look forward for your reply, thanks.