Media | Articles
Engine revolution: Mazda’s rotary and its uncertain future
Conventional gas and diesel engines do a commendable job serving car and truck owners’ needs, but futurists insist that electric motors will eventually supplant them as the power source of choice. Some 50 years ago, a similar situation cropped up: Mazda’s ultrasmooth rotary engine had bright hopes of sending pistons the way of the buggy whip. With Mazda celebrating its 100th birthday this year, what better time to toast the brand’s most ambitious technical stride?
First things first: Mazda didn’t invent the rotary. It was German Felix Wankel who, in the 1920s, drew inspiration from pumps, compressors, and turbines to create an engine without the stop-start, up-down reciprocating motion of pistons and connecting rods. After working on disk valves and rotary compressors, the self-taught engineer earned a 1934 patent for an engine consisting of components that rotated, with no hint of reciprocation. Since the Otto-cycle gas engine (which powers most of our cars today), Rudolf Diesel’s compression-ignition concoction, and Karl Benz’s two-stroke all arrived late in the 19th century, Wankel’s rotary was the 20th century’s only new engine type.
Following more than two decades of experimentation, in 1957 Wankel finally persuaded NSU Motorenwerke, a leading German motorcycle manufacturer, to construct a prototype engine. It produced 28 horsepower at 17,000 rpm from only 125 cc of displacement. But the 1957 design was flawed. Both the rotor and its housing rotated, an arrangement totally impractical for mass production; changing the spark plug required a complete teardown. Unbeknownst to Herr Wankel, Walter Froede, a fellow NSU engineer working down the hall, created an elegant variation with a fixed housing. Though Wankel scorned, “You have turned my racehorse into a plow mare!” the rotary we know and love today descended from Froede’s simplified design.
In 1960, NSU and the U.S. aircraft manufacturer Curtiss-Wright (CW) signed an agreement to promote the new engine’s development. Wowed by performance claims, more than 20 British, European, Japanese, and American manufacturers took the bait, signing licenses in hot pursuit of rotaries for automotive, aircraft, marine, motorcycle, farm implement, and military applications. The Soviets also carried out experiments without paying a ruble in fees. Recognizing the rotary’s tremendous potential, Mazda was an early adopter. The formal agreement between NSU and Mazda was signed in July 1961.
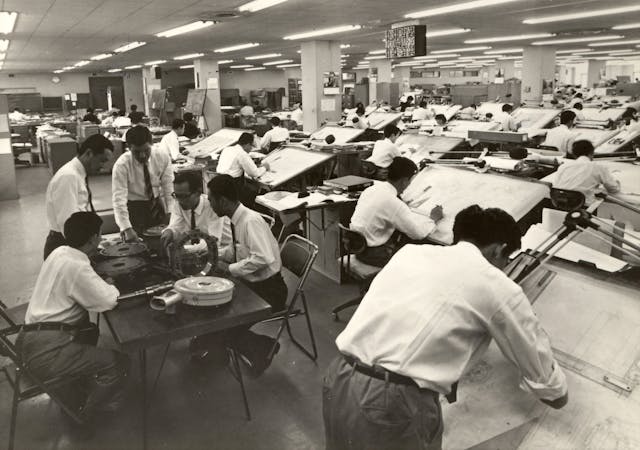
Rotaries are fundamentally simpler, lighter, and more compact than piston engines. A triangular-shaped rotor orbits within a chamber to convert combustion energy to torque delivered to a shaft rotating at the engine’s center. There are no connecting rods or camshafts opening and closing valves. Instead, as the rotor sweeps past ports in its housing and/or side covers, a fresh mix of fuel and air enters the moving combustion chamber while spent gases are swept out the exhaust port. Counterweights attached to the output shaft cancel vibration. Thus the rotary’s ace in the hole is supreme smoothness: one power pulse every turn of the output shaft versus one every other turn for single-cylinder four-stroke piston engines.
Marketplace
Buy and sell classics with confidence
Touting the rotary’s size and weight advantages, CW compared its RC2-60 rotary engine to a 1960s-era 283-cid Chevrolet V-8. The 185-hp rotary weighed 237 pounds compared to the 195-hp V-8’s 607 pounds. Although the rotary occupied only 5.1 cubic feet of space, the V-8 was more than four times larger, at 23.2 cubic feet. The number of individual components in each engine was also dramatic. The Chevy engine had just over 1000 parts, 388 of which moved, as opposed to the rotary’s 633 parts, only 154 of which moved. The rotary’s size, weight, simplicity, and smoothness were undeniable.
In our cutaway drawings, take note of the center of the engine. That’s where the eccentric shaft resides, a device functionally similar to a piston engine’s crankshaft. It is supported by a bearing at each end, also like a crankshaft. Near its middle, there’s an offset journal called an eccentric, which functions exactly like a conventional crank’s throw.
The rotor is a triangular-shaped component about 3 inches thick. The distance from its center to each tip, or apex, is roughly 4 inches. This hardworking element performs piston, connecting rod, and valvetrain duties. A plain bearing lining the rotor’s center mates with the aforementioned eccentric shaft journal.

The rotor’s orbital motion is a two-part symphony driven by combustion pressure on one flank following ignition. This pressure forces the rotor to spin like a pinwheel on its eccentric journal. The eccentric also moves because the rotor pressure is asymmetrical (offset, from one flank only). To keep this compound motion in sync, there are two phasing gears. The smaller one, located at engine center, is fixed; this gear’s external teeth mesh with the rotor’s internal gear teeth. A 2:3 gear ratio yields three full turns of the eccentric shaft for every 360 degrees of rotor motion. To visualize the overall kinesis, think hula hoop: rotor spin compounded by eccentric-shaft rotation.
The moving rotor’s apexes define a path called an epitrochoid. (Google this word for an extra helping of confusion.) The rotor housing mimics this shape—what resembles a figure eight in our illustration—to keep the apexes permanently within half a millimeter (0.02 inch) of their confines. Think piston-to-bore clearance. Add a plate covering each side of the rotor and you have a contained volume. As the rotor orbits, the changing space between each of its three flanks and the rotor housing supports the four standard Otto-cycle operations: intake, compression, expansion (power), and exhaust. The rotary’s parlor trick is that three of these cycles occur simultaneously.
As with a two-stroke engine’s pistons, the rotor exposes ports as it rotates to admit fresh fuel-air charges and to broom out exhaust. Ignition occurs when spark plugs fire on cue through small holes in the rotor housing. Due to the long, thin shape of each combustion chamber, Mazda uses two spark plugs firing sequentially to light the compressed fuel-air charge.
The rotary engine’s operation sounds simple and elegant once you grasp the subtleties, but developing one to provide years of faithful service was a feat; there are vexing issues galore. The hardworking rotor and its housing must be kept within tolerable temperature limits. Air cooling has worked in a few applications, but the more common approach is to circulate the lubricating oil through the hollow rotor to cool it while also routing a water-antifreeze mix through internal passages to cool the rotor housing and side plates. Unlike a piston engine’s cylinder, which is cooled by the fuel-air charge once per cycle, the spot where combustion occurs in a rotary remains permanently hot. As a result, keeping ample cooling flow through that area of the engine is critical—and difficult. Seals that keep the cooling, lubricating, and working fluids in place have posed the tallest developmental hurdles. For some idea, compare the five-part piston ring set of a conventional engine with the 30-or-so parts required to seal each rotor’s apex and flank surfaces.
Following years of development, NSU won the race to production with its 1964 Spider. Unfortunately, the single-rotor engine’s apex seals weren’t perfected by the time the two-rotor NSU Ro80 luxury sedan arrived three years later. A common salute when one Ro80 owner encountered another such soul on the road was a multi-finger wave to signal the number of engines replaced. Modest sales and high warranty claims drove NSU so near bankruptcy that in 1969, its assets were taken over by Volkswagen.
The first durability issue Mazda discovered after commencing rotary research in 1961 was chatter marks across the inner surfaces of the rotor housing caused by apex seals resonating (skipping along) as they swept over that area. The Japanese termed these “nail marks of the devil.” Before Mazda launched its first rotary, the 1967 Cosmo 110S two-seat coupe, engineers made sure that chatter-mark and apex-seal issues had been resolved. A small flat spring combined with combustion pressure behind each seal helped press them in touch with the rotor housing. For the seals themselves, Mazda experimented with self-lubricating carbon, various sintered metals, and cast iron “chilled” and shaped by an electron beam. To ease the seal’s sweep over the housing surface, oil was metered with the incoming fuel-air mix, a technique borrowed from two-stroke engines. Ultimately, Mazda achieved a durable rotor housing by lining an aluminum casting with a thin sheet of steel finished with an electroplated-chrome wear surface.
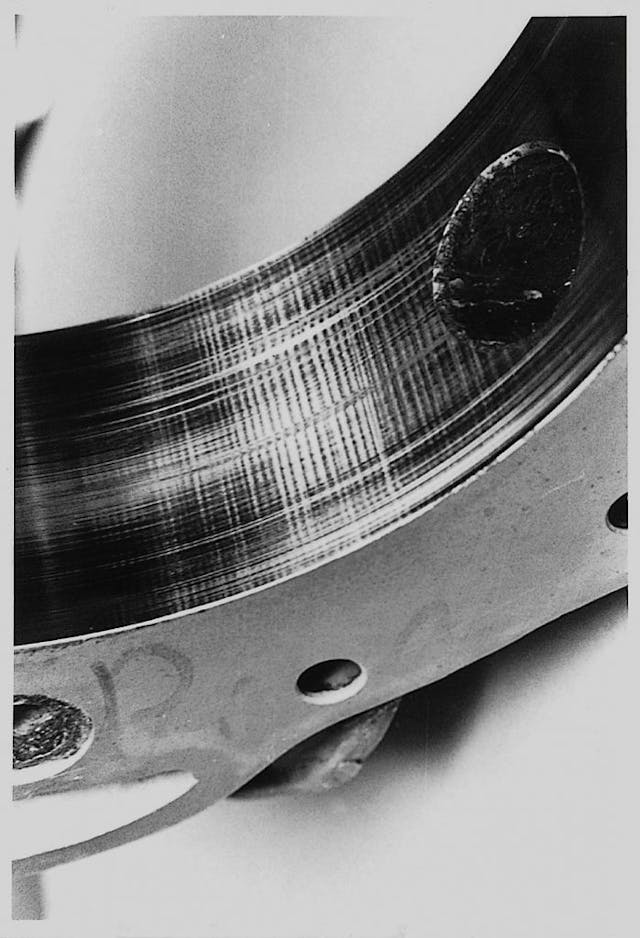
Strapping several rotors together to build a larger, more powerful engine is complicated by the fact that each rotor must be inserted from the opposite end of the eccentric shaft during assembly. That’s easy in a two-rotor setup, but combining three or more requires an awkwardly long eccentric shaft or an intricate coupling of two eccentric shafts.
The mix of materials Mazda chose to make its engines durable—aluminum housings, cast-iron rotors and side plates, steel eccentric shafts—resulted in widely varying expansion rates, which hindered the design and development of the O-rings responsible for sealing coolant passages. Since the rotary was born when gas cost pennies a gallon, fuel mileage wasn’t a concern. But in the mid-1970s, following the first energy crisis, the EPA began measuring and reporting mpg, exposing the Mazda rotary’s poor efficiency.
The problem of efficiency was two-fold. The ample surface area defining the rotary’s combustion chamber results in substantial energy loss to the cooling system. In addition, a portion of the unburned fuel-air charge is simply swept out of the engine as exhaust. To curb tailpipe emissions in 1970 U.S. models, Mazda employed a thermal reactor that mixed fresh air with the exhaust constituents to continue combustion outside of the rotor housing.
Bitter fights soon ensued between Mazda and the EPA over urban mileage tests that included cold starting. Mazda demonstrated real-world results better than EPA figures, and the government did begin efforts to align its procedures more closely to customer experiences, but the damage was done: Mazda’s rotary-powered cars were stuck at the thirsty end of their size class. During a 40,000-mile test of a Mazda RX-2, Car and Driver recorded city driving mileage as low as 14 mpg and rarely topped 18 mpg on the highway. The only saving grace was that rotaries were happy swilling regular-grade gasoline.
Emissions were a related issue, but here the rotary enjoyed one advantage. Because its peak combustion temperatures were below those typical of a high-compression piston engine, there was less formation of polluting oxides of nitrogen (NOx). Unfortunately, that plus was offset by the rotary’s long, flat, moving combustion chamber, which is hardly the ideal way to achieve a complete fuel burn. As stated, unburned fuel-air mix was simply swept out the exhaust port, raising hydrocarbon (HC) and carbon monoxide (CO) emissions in the process.
General Motors, the world’s most prominent rotary license holder, invested heavily in this engine. This included a manufacturing plant tooled and ready to produce what it called a Rotary Combustion Engine for the 1975 Chevy Vega and for AMC’s Pacer. Difficulty meeting emissions standards and poor fuel economy forced cancellation of those plans. In fact, the plug was abruptly pulled the instant GM president and rotary advocate Ed Cole retired in September 1974.
If GM could not solve the rotary riddle, who could? Hercules/DKW, Norton, and Suzuki did enjoy modest success building and racing rotary-powered motorcycles. Arctic Cat and Outboard Marine offered them in snowmobiles. Mercedes-Benz had high hopes with its magnificent three-and four-rotor C111 Gullwing sports cars, but Citroën went bankrupt developing its Comotor engine. There have been plenty of aircraft and helicopter experiments and hundreds of home-builts powered by Mazda engines. Ultimately, though, Mazda became the last manufacturer standing mainly because of its patient, persevering rotary engine devotion.
Such devotion was certainly encouraged by motorsports success. Along with turbines, rotaries thrive on track. With no reciprocating parts or valvetrain fragility, they love to rev. Huge intake and exhaust passages with minimal flow restriction are an easy upgrade. Except for their notably high fuel consumption, rotaries run for hours on end with minimal need for pit stops. They also shriek like furious banshees, requiring huge mufflers to curb their din, because hot, flaming exhaust gas leaves the combustion chamber unimpeded by valves. Even with earplugs inside a helmet, your author suffered two days of partial deafness after codriving an RX-7 at Daytona in 1979. Bonneville spectators wince every time a rotary leaves the starting line.
Sanctioning bodies struggle comparing rotary engine displacement to that of piston engines. The Southern California Timing Association, which oversees salt flats competition, bought the one-power-pulse-per-output-shaft-revolution argument (versus a piston engine’s two turns) to assign rotaries a 2:1 “correction” factor. Other bodies, such as the FIA, justified 3:1 by the fact that each rotor has three working side surfaces. Some agencies simply banned rotaries outright, especially after witnessing their speed and reliability. In 1968, anxious to strut its stuff, Mazda campaigned two race-prepped Cosmos at the 84-hour Marathon de la Route staged at Germany’s Nürburgring. One entry dropped out after 81 hours with axle failure; the other finished a surprising fourth behind two Porsche 911s and a Lancia Fulvia.
By 1976, Mazda RX-3 coupes had logged 100 victories in Japan. In 1979, the RX-7 launched its illustrious competition career with first-and second-place GTU class finishes at the 24 Hours of Daytona. Mazda’s sports car ultimately earned the GTU series championship 10 times, including eight consecutive titles.
Privateer assaults on Le Mans commenced in 1970, with the first rotary finish requiring a decade of effort. Respectable class finishes followed in the 1980s. Mazda’s day finally arrived in 1991 when its wailing four-rotor 787B thumped the Jaguar and Mercedes factory efforts to win overall, the first Le Mans victory by a Japanese manufacturer.
Even without seemingly essential all-wheel drive, Mazda RX-7s finished as high as third overall in World Rally Championship events during the 1980s and ’90s. And in 1994, Norton won the British Superbike Championship with its RCW588 ridden by Ian Simpson.
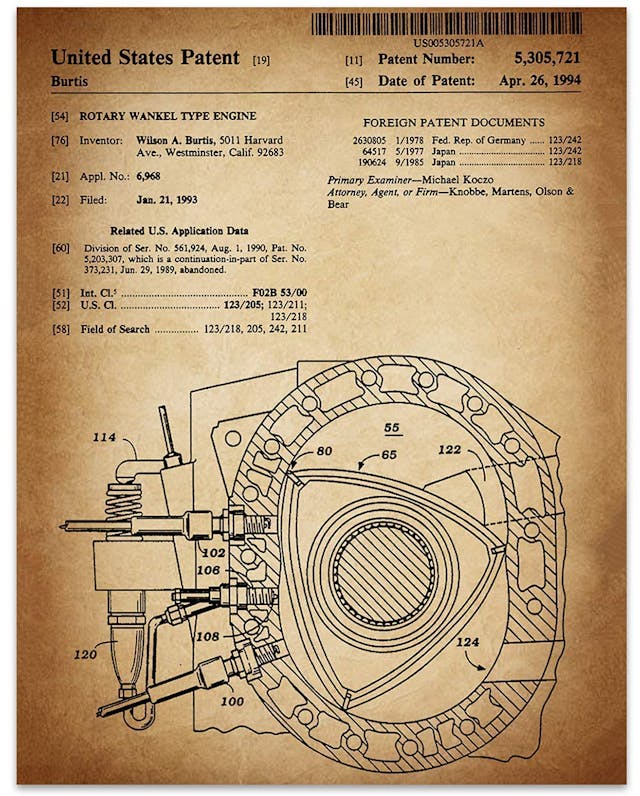
Unlike 20 or more enterprises around the globe that failed to advance the rotary’s cause, Mazda stuck with this engine through thick and thin for 44 years. Production ceased with the last RX-8 in 2012. In truth, the introduction of the magnificent piston-powered Miata MX-5 sports car in 1989—only a decade after the RX-7’s birth—marked the beginning of the end.
Despite its relative longevity beneath a Mazda badge, the rotary’s service record was hardly perfect. A rash of O-ring seal failures in the 1970s forced Mazda to operate an engine rebuild center near its U.S. headquarters in Irvine, California, to service warranty claims. RX-8s had a reputation for high oil consumption, and poor gas mileage was a concern from the start.
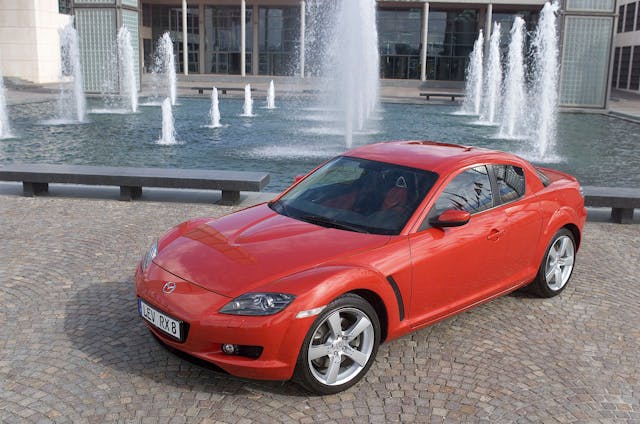
Piston engines got lighter, more powerful, more efficient, and cheaper to build at a faster rate than the rotary, mainly because only Mazda championed its cause. When Mazda’s engineering, manufacturing, and ownership allegiance with Ford ended in 2015, the small Japanese brand became totally responsible for its future. In 2017, Kenichi Yamamoto, who guided rotary development from the beginning and later served as Mazda’s president and chairman, went to rotary heaven without a successor who shared his passion.
That said, various Mazda powertrain directors have touted the rotary’s suitability as a range extender for gas-electric hybrid applications. The engine’s size, shape, and centered output shaft match electric generator characteristics nicely. And operating the rotary at a constant speed and load would diminish its emissions and fuel efficiency shortcomings. If the brand is truly serious about advancing the hybrid cause, there’s a chance the rotary just might outlive its piston engine nemesis. That was the hope all along.
As the rotor turns
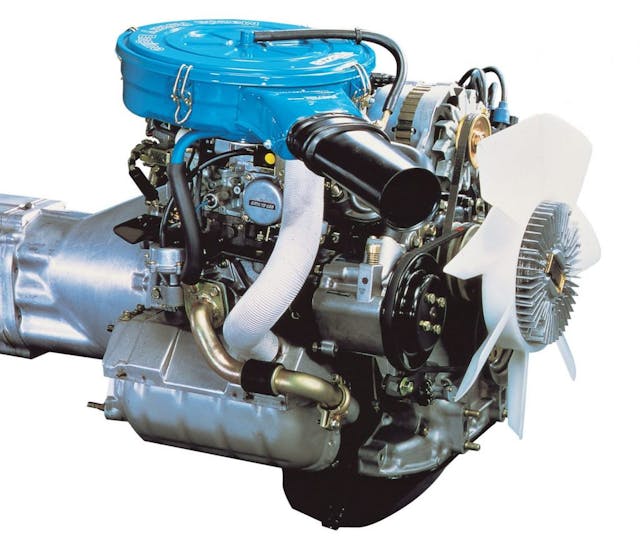
10A:
1970–’72
A 982-cc two-rotor with 4-bbl carburetor making 100–120 hp in the R100 coupe. Built under license from NSU, Mazda’s first rotary sold in North America incorporated notable advancements in apex-seal design to improve durability. The water-cooled rotor housings were aluminum castings; rotors and side housings were made of cast iron.
12A:
1971–’78
An 1146-cc two-rotor with 4-bbl carburetor making 120 hp in RX-2 and RX-3 coupes and sedans. To add power to propel larger and more sporting models, rotor width was increased by 10 mm (0.39 in). Basic engine design and materials were otherwise carried over.
1979–’85
An 1146-cc two-rotor with 4-bbl carburetor making 100 hp in the RX-7. Like the 10A design, the larger 12A featured intake ports in its side housings and peripheral exhaust ports. Peak torque occurred at 4000 rpm, and the power curve crescendoed at 6000 rpm.
13B:
1974–’78
A 1308-cc two-rotor with 4-bbl carburetor making 135 hp in RX-4 coupes and sedans, Cosmo coupes, and pickups. Another 10-mm (0.39-in) increase in rotor width boosted displacement, torque, and horsepower. The torque peak remained at 4000 rpm, but peak power now occurred at 6500 rpm.
1984–’86
A 1308-cc two-rotor with fuel injection making 135–146 hp in the RX-7 GSL. The addition of Nippondenso electronic fuel injection yielded a broader torque curve peaking at a streetworthy 2750 rpm. A sophisticated engine management system, relocated spark plugs, dual mufflers, and lighter rotors for 1986 raised output to 146 hp at 6500 rpm and boosted torque another 4 percent to 138 lb-ft at 3500 rpm.
1987–’95
A 1308-cc turbo-charged two-rotor with fuel injection making 182 hp in the RX-7. Adding a twin-scroll Hitachi turbo (6.2 psi of boost), an intercooler, and a detonation sensor yielded speedy throttle response, with peak power at 6500 rpm, and a healthy 183 lb-ft of torque at 3500 rpm. Remarkably, there was little or no loss of fuel economy over the previous naturally aspirated rotary.
1991-’95
A 1308-cc twin-sequentially-turbocharged-and-intercooled two-rotor with fuel injection making 255 hp in the RX-7. Bosch D-Jetronic injection metered fuel to three side intake ports per chamber. Torque peaked at 5000 rpm, power at 6500 rpm, and the redline was an enthusiastic 7500 rpm.
20B:
1990–’95
A 1962-cc twin-sequentially-turbocharged-and-intercooled three-rotor with fuel injection making 276 hp in the (Japan-only) Eunos Cosmos. Internal dimensions were identical to 13B engines, but a two-piece eccentric shaft and special assembly procedures were required.
R26B:
1991
A 2616-cc four-rotor with fuel injection powered the 900-hp 787 and 787B sports prototypes at Le Mans, winning the 24-hour race in 1991. The engine had three spark plugs per rotor and peripheral intake and exhaust ports.
Renesis:
2003–’12
A 1308-cc two-rotor with fuel injection and side exhaust ports making 207–247 hp in the RX-8 2+2 coupe. This was a new design with exhaust ports moved to the side housings for improved efficiency. Two versions were offered, with modest and competitive power outputs and a remarkable 9000-rpm redline.
The Rotary engine was just at the wrong place at the wrong time. If it had come to market several decades sooner it may have developed more and may have survived but the emission doomed it.
Also the materials today are much better one has to wonder how much durtable it would be today.
The Engine was not for the Vega it was for the Monza. It also was going to be sold to AMC for the Pacer. That is why the I 6 and the V8 never fit well.
I can attest to the noise at the IMSA races. I saw these cars black flagged for losing a muffler and you had to hold your ears as it passed by.
Was this article written in 2020?
Yes. The publish date on this story was August 5th, 2020.