How to Swap Your Wheels Without Wrenching Your Back
I’ve made many references over the past 18 months to my back issues. It’s nothing acute—no smoking-gun bulged discs showing up on the MRI—just the usual 65-year-old-man-stuff of easily-triggered low back pain and sciatica. But it’s annoying as hell.
A four-month-long stint of physical therapy to strengthen my core has helped enormously, allowing me to reach the point where I was able to do all that wrenching on the recently-purchased Nissan Armada without reinjuring myself. However, I feel like I’m always one bad decision away from a relapse, so I try not to make those bad decisions. I lift very little without help (as difficult as that is when you’re used to being a lone wolf working by yourself in the garage), and I don’t yank on things when I’m in a bent or crouched position.
The winter/summer wheel swap has become a bellwether for me—e.g., if I can’t do this, I can’t do anything. When my back issues reemerged in 2022, the combination of rolling a floor jack, skooching down to properly position it under the car, working the jack handle to raise it, cracking the lug nuts, dismounting and mounting the wheels, and using a torque wrench in a bent-over position was difficult enough that I was beginning to think that this part of my life might be over. Fortunately, there are back-saving tricks that allow me to cruise through wheel-swapping. Yeah, I know, this sounds like that “one weird trick” online clickbait. But trust me.
First, let me offer a warning that is crucially important. My college physics professor was killed when the car he was working on fell on him. That’s all the more tragic considering he was my mechanics professor, which, in addition to “mechanics” applying to both the physics as well as to working on cars, has the unbearable irony that mechanics is the study of how physical objects move in response to forces on them, and part of mechanics is “statics,” which analyzes the forces on stationary objects that keep them from moving. Ever since that horrible tragedy, I have been assiduously careful never to work under a car that isn’t properly supported by jack stands and a floor jack as backup. Swapping wheels is a gray area where many folks argue that they’re not technically under the car, so they feel that they can jack up one wheel without taking the time to set that corner of the car on jack stands. I see garages and tire-change shops do this all the time. I’ll admit that there have been times when I’ve done it myself, but in what I describe below, it’s absolutely imperative that you support the car on stands, because there’s no question that part of you is under the car, and you don’t want to get your legs crushed if the jack slips.
I’ve identified four aspects of wheel-swapping that are problematic in my AARP years. I’ll address them each below.
Moving the wheels
I keep the off-season wheels for both my and my wife’s daily driver under the back porch, which is on the opposite side of the house from the garage. Both are slightly downhill from street level. So wheel-swapping both cars requires rolling eight wheels up and down the path a total of 16 times. This bending-while-rolling effort eventually triggers back pain. For a while I was asking my kids to do it for me while I grumbled, “You mean I can’t even do this?” but I found that by keeping my back straight and doing a Groucho-Marx-like duck walk (for those old enough to know the reference), I can keep my dignity and move them myself.
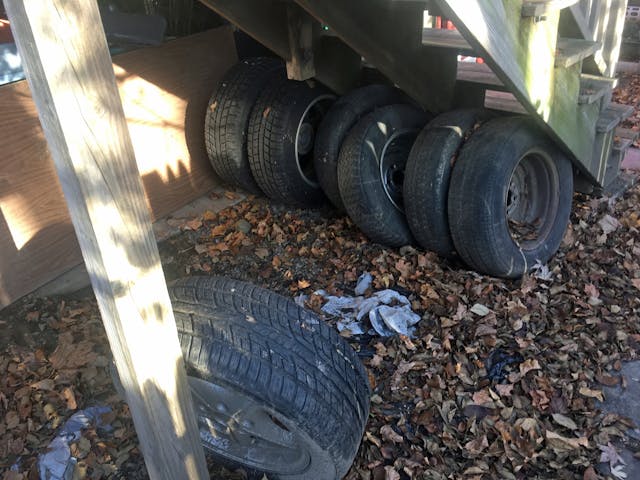
Jacking up the car
I have a mid-rise lift, but it’s usually not worth using it for a simple wheel swap. In the first place, there’s always another car parked over it, often in mid-project. Plus, it takes time to position a car on the mid-rise. The vintage cars get lifted by their frames, which allows a lot of slop in their placement, but it’s difficult to lift my daily-driver 2003 5 Series BMW by anything but the jacking points on the rocker panels, and there’s perhaps two inches of positioning leeway for the lift’s arms and sliding jack pads to be able to reach all four. Plus, as I’ll get to below, the low-back-pain key to all this is keeping the car as close to the floor as possible, so the added height capability of the lift is a detriment, not an advantage.
That means that I swap wheels the old-school way—on the garage floor with a floor jack. In the past, I’d raise the nose of the car by putting the jack in the middle of the front subframe, swap both front wheels, then do the same in the back, but for back-pain reasons, it’s easier for me to do one wheel at a time and use the jack points at the corners. That way I don’t need to crouch down to get eyeballs on where the floor jack is contacting a point deep under the car.
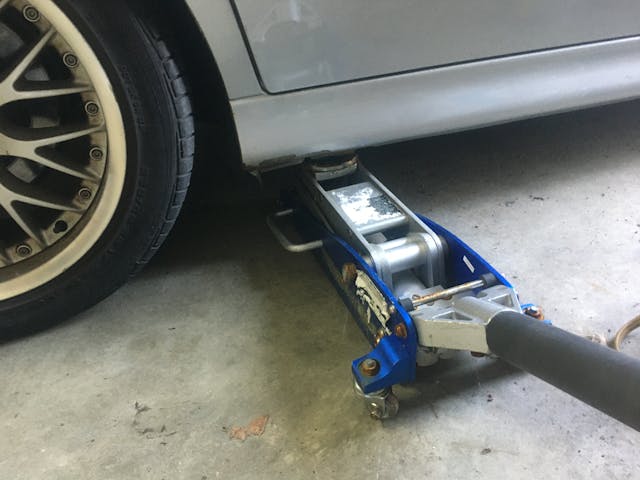
Using the jacking points on the corners of the wheel wells has the added advantage that the lever arm of the floor jack is well-clear of the body of the car, which lets me pump it up and down using my foot. This is another big wear-and-tear savings on my back. I can also do this if I use my long-reach floor jack on the middle of the front subframe, but it probably weighs four times as much as my small aluminum jack.

The back-saving key is to raise the wheel just enough to set the corner of the car on a jack stand and swap it. Don’t put the car up any higher than it needs to be.
Loosening the lug nuts
Before you jack up the wheel, if you don’t have an impact wrench, you need to crack the lug nuts the old-fashioned way with a breaker bar. By all means, save your back by putting one foot on the end of the breaker bar and standing on it, but be careful not to lose your balance and twist funny when it lets go. An air-driven or electric impact wrench is a major back-saver, as you can position yourself directly in front of the wheel and zip the nuts off. Leave one nut on finger-tight.

Finally, the “one weird trick.” When you mount or dismount the wheel, don’t ever lift it with your hands, arms, and back—lift it instead with your knees and legs. With the corner of the car safely supported by a jack stand, sit directly in front of the wheel and slide your legs around it. Then slide your feet toward you and raise your knees until some part of your legs contact the tire. It could be your shins, knees, or thighs. Whatever feels comfortable to you. Loosen the last lug nut and tip the wheel onto your legs. Then slide your feet forward, lower your knees, and roll the wheel onto the floor.
Removal is easy because you have gravity working for you. “The trick” is far more important on installation—roll the wheel onto your legs and pull your feet toward you to raise your knees to get it onto the hub. If the hub has studs, rotate the hub or the wheel to get them through the holes. It’s a little tricker if the hub has threaded holes and the studs are part of the lug nuts. Most hubs have a raised ring in the center that the bore in the wheel sits on. You need to use your knees to maneuver the wheel onto it, then rotate it to line up the holes and spin the nuts on.
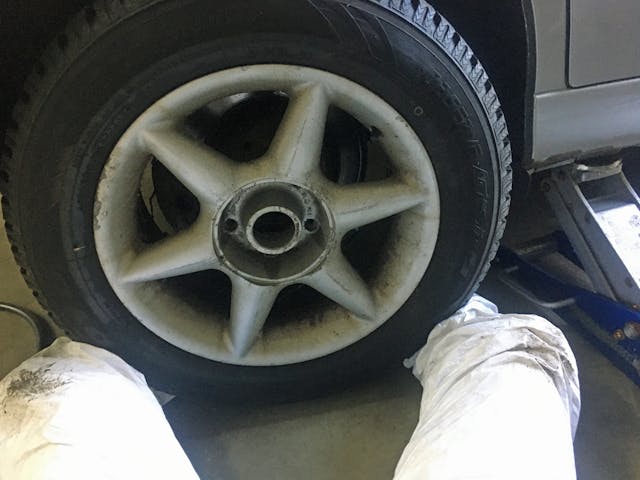
Use your foot on the torque wrench
Get the lug nuts seated with a ratchet wrench. If you have an impact wrench, you can put it on its lowest setting and give a quick blip of the trigger to snug each nut down. Then lower the car, set a torque wrench to the appropriate setting, and use your foot instead of your back to torque the nuts down. You can hear and feel the click of the torque wrench just as easily as if it’s in your hands. You still need to bend down to move the torque wrench from lug nut to lug nut, and with five per wheel, four wheels, two cars, even this needs to be done with care if your back is sensitive, but it’s still way less wear-and-tear than forcing your upper body to crank the torque wrench.

Although I didn’t have to swap seasonal wheels on the Armada, I did have to pull the front wheels off and put them back on to do the front struts. They’re 20-inch wheels, a full three inches bigger than anything else I’ve ever owned. Using these steps, I got them off and on again without so much as a sidelong glance from my back.
I hope some of you find this as helpful as I have.
Dealing with those four transmissions under the porch, though, is another matter.
***
Rob’s latest book, The Best Of The Hack Mechanic™: 35 years of hacks, kluges, and assorted automotive mayhem is available on Amazon here. His other seven books are available here on Amazon, or you can order personally-inscribed copies from Rob’s website, www.robsiegel.com.
Check out the Hagerty Media homepage so you don’t miss a single story, or better yet, bookmark it. To get our best stories delivered right to your inbox, subscribe to our newsletters.
Google “wheel jack”, all manner of tools to do the heavy work for you.
I have a Mercedes Benz (W126) where the bolts ARE the lugs holding on the wheels. I purchased a threaded rod that’s used to hang tire on while putting the other bolts in. I highly recommend it for those wheels where the studs are part of the lug nuts.
You all realize you can convert those pesky bolts to studs and nuts, right? I was at a Mazda dealer years back when they had those things. We delivered every new car with studs and nuts and put the OEM nonsense in the glove box. When doing this remember to put thread locker on the stud!
Lot of good ideas here, not too sure about the foot on torque wrench as easy for socket to slip off bolt, but to each their own. I always use my little rolling stool and use my legs to lift by spreading my legs wide open and putting my hand inside wheel and gently lift up with my toes and arms. The worst are the wheels on my 560 no studs to “hang” wheel on but use cut off lug bolt to assist. Most important thing is to stay in shape. Just as it is with cars same with our bodies is “Motion is Lotion, Rest is Rust”. And if you can’t do it yourself you can always pay someone to do it for you.
I have a slightly different trick for lifting wheels on and off, as I also have to deal with back issues.
When the wheel is ready to come off, squat down (keeping back straight) in front of the wheel, such that your knees are pointed at the tire. Rest your elbows on top of your knees, and lift the tire. To replace the wheel, I roll it into position and lean it against the car. Squat down, elbows on knee tops, and lift into position.
I’m guessing this method may require more bicep and leg strength, but it has worked for me without tweaking my back.
Careful with the standing on the lug wrench method. I sheared off a bolt once that way…and I’m not that heavy.
You miss the best way of all….get your son, son-in-law, or grandson to ‘help’. They get to learn useful skills and my back never hurts.
I just swapped out 2 cars, 8 wheels and tires twice a year. I have never, and at 67 cannot sit with my ass on the ground legs out and have to be on my knees! My wife’s Chevy Sonic has studs to hang the wheels onto making it easy to then put on the lug nuts. My BMW e61 and e24 both use wheel bolts so on my knees it’s much harder to raise the wheel and to line up the bolts while lifting the wheel. The fix is I use a simple positioning stud, this allows me to screw it in by hand enough to easily lift the wheel and allow it to hang while I insert the bolts and remove the positioning stud. Makes it easy on my back and my knees are good as well!!
Rob, my ’68 e-type with center knockoffs is never a pain!
I had to put the wheels back on my car last weekend and had a recently aggravated 63 yr-old lower back I was trying to protect. I ended up putting a folded-over fiberglass tarp onto the concrete floor then rolled the wheel onto the tarp in front of the wheel hub. The tarp allowed me to rotate the wheel in place to align the holes with the studs, then to slide the whole wheel onto the studs – no lifting! Had to fiddle with the jack height a bit to make things line up, but it worked great.
There is a much better way to lift a wheel assembly on to a hub, especially if changing heavy truck tires. Putting your feet/legs under a car while jacked up with a hydraulic floor jack is dangerous.
I’m 78 years old, have trouble lifting 40 pounds with arms or legs.
I would love to tell you, but I would like to show how it’s done with a picture. Don’t see where I can post a picture.
Fred, as I said, I only do this when the vehicle is also supported by a jack stand.
OK, we don’t need pictures to show how to lift a wheel assembly on to a hub. Go to your garden shed, grab a flat square shovel, slip it under the outside edge of tire, push down on handle lifting tire on to hub or lug nut studs. Works great if tire is off ground about one inch and one stud is on top.
Lots of good tips here. I find like others loosen up the lugnuts, etc. while on the ground then lift up enough to remove the wheel worked for me well. I’m not trying to do an oil change so I don’t need to get under the car.
I also have a history of back problems. Regarding mounting the tires: I once watched an old-timer mount a tire during a vehicle state inspection. He sat on a creeper-stool facing the hub, then rolled the tire up onto both feet, then just pivoted his feet on his heels, lifting the tire while aligning the studs. Works great for me.
I also have back issues at times, and do the summer/winter wheel swap on two cars twice a year. One time when my back was iffy, I hit on an idea that worked great to minimize any risk. I got one of those GoJak style wheel dollies (normally used in sets of four to lift and roll cars around) at Harbor Freight (currently about $130). Once the lug nuts are loosened, you can position the dolly under the tire, jack it to take the weight, remove the nuts, and roll the tire away (the dolly has casters). It’s even better for installing wheels, because the tires are supported by rollers that allow it to be rotated to align the holes with the studs. Since the dollies are meant to carry the weight of one corner of the car, the weight of a wheel/tire combo is nothing even for a cheap one.
The beauty of this method is that it eliminates the need to sit with legs under the car and lift the wheel with extended arms.
You beat me to it. I bought one of these back in 2015 (from Harbor Freight) when I had an acute back problem and it was time to put winter tires on. I haven’t had a repeat of the back problem, but I still have the dolly in the garage just in case.
Both my E39 M5 and my son’s 335i are a pain to position for the lift pads. As you pointed out, there is only a couple of inches of position that work with the jack points. I finally had to Sharpie a tire outline on the garage floor for both cars to avoid multiple back-and-forths. One of many BMW annoyances.
I have a BMW M3 1995 that I track- I drive it to the track and change to good tires at the track. What I do is raise one tire at a time- just barely above the ground so that the tire spins- remove the tire/ replace it with the track tire by putting the tire up on a pc. of wood- push it so that it catches on the center ring/ install one lug and then slightly alter the wheel so that all the lugs go in and finger tighten each one- then tighten each one with a socket wrench, lower the tire to the ground and finish the process with the torque wrench. I have a bad back and I am not straining and I don’t see the need to jack the car way up/ using stands.
What am I missing? It seems so easy- 10m per corner.
I have suffered with back pain for 50 years- but intense stretching including some yoga position leaves me pain free- cannot recommend it enough!