In praise of the Torx fastener
If any of you out there have owned a domestic vehicle from the ’80s or ’90s, perhaps you also know the frustration of having to keep both SAE and metric tools in stock. Vintage Detroit iron is naturally going to feature SAE fasteners, and both European and Asian imports will naturally be assembled with metric hardware, but for far too long the Big Three made a slow transition to metric, leaving vehicles with both kinds of fasteners.
Often a vehicle’s chassis and body would be SAE while its drivetrain would use metric, making it possible for a single job to require both types of tools. My Jeep Cherokee, built by the Chrysler Corporation, uses an engine originally designed by AMC and a transmission made by Aisin AW, a subsidiary of Toyota. One set of sockets won’t cut it.
Once I’m in the habit of wrenching, I can eyeball a fastener and know the size pretty accurately, although for me that’s a skill that wears off rather quickly between wrenching sessions. It wouldn’t be so bad with just one type of socket or wrench to choose from, but it can test your patience when, after eyeballing a distant bolt head and snaking a few extensions, you realize you’re off by the tiniest of margins.
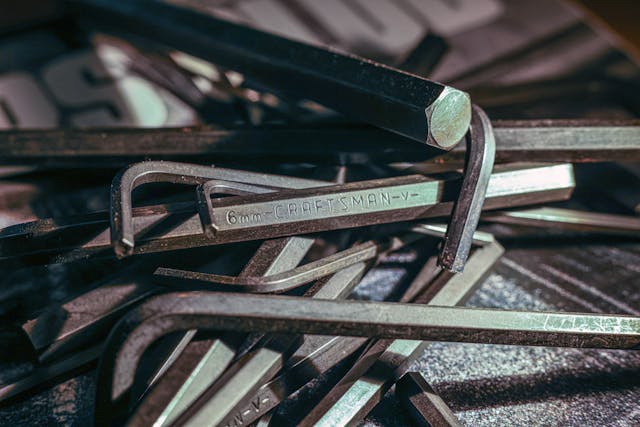
Hex bolts and nuts have that problem, Allen bolts, which are in internal hex, have that problem. There is a fastener that doesn’t have that problem. Torx. Is that an SAE T55 Torx or is that a metric T55 Torx? Nope, it’s just a T55 Torx. The fasteners are used for both metric and SAE threads. The graduations between Torx sizes make them pretty easy to eyeball as well. Torx fasteners and drivers have been around since 1967, when the six-pointed star pattern was invented by Bernard Reiland at Camcar and patented in 1971.
Torx isn’t perfect, as they are a rather tight tolerance. It can be difficult to insert the driver if they collect gunk in an engine bay, for example. I’d take that over a Phillips fastener that would rather cam its driver out of the fastener than apply enough torque to break it loose.
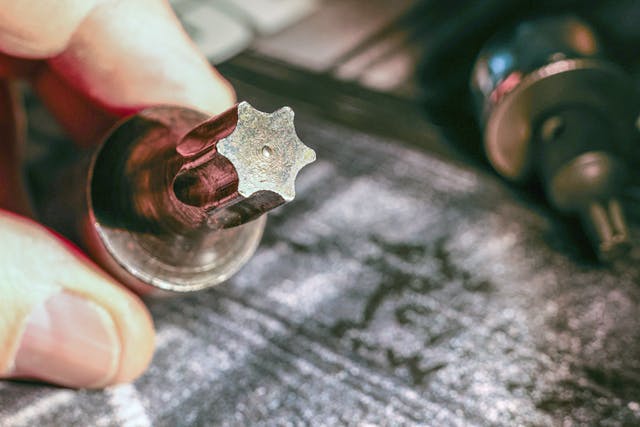
Unfortunately, Pandora’s box of different fastener types has been opened and manufacturers seeking lighter, stronger fasteners have created a myriad of options, requiring the DIY wrench to expand their toolbox with every new vehicle that enters their stable, Torx drivers included. I do admit that I don’t hate adding new tools to the toolbox, I just wish we’d come to a consensus on fastener shapes and sizes. There is one consolation, however. Every one of my sockets still has at least one half that’s SAE.

***
Check out the Hagerty Media homepage so you don’t miss a single story, or better yet, bookmark it. To get our best stories delivered right to your inbox, subscribe to our newsletters.
I have found Torx drivers to be both endearing and maddening – for some of the reasons Brandan lists. But they are truly better than Phillips, which I used to consider leaps ahead of straight-slot heads. I guess there is no real perfect solution. I also used to steadfastly refuse to consider that the U.S. should adopt metrics. USA! USA! But in my old age, I kind of have softened my stance, especially since we seem to be slowly absorbed by it anyway.
Finally, I’m wondering how Brandan got a picture of my Allen wrench drawer, and why I didn’t get proper credit for it! 🙄
Robertson Drive is simple and effective.
I find smaller Torx there is too many increments and they get mashed up too easily. This applies to the drivers/bits as well.
Button-head cap screws with hex heads are good too, but I agree you get into the SAE/metric issue.
I used to do a lot of work that required T25 and T27 frequently and discovered that you had to have several of these key sizes because they break easily and wear quickly. I do not want to see an all Torx world no thank you
As far as American iron, I generally found the opposite to be true where the drivetrain was standard and the body was metric… as far back as the 70s. I remember telling the parts guy in the late 90s that it was time for the metric bin to come out front and the standard bin go in the back corner
In addition to sae and metric, raise your hand if you have a set British Standard and Witworth sockets and wrenches to work on older British vehicles.
Off course I do — how do you work on pre 60`s vehicles / boats etc without
Why else would one endeavor to work on old British machinery than as an opportunity to need more tools?
And then there is the “clutch head” – used on ’55 Chevy gas tank retaining screws – probably on other tings as well, but my experience is limited to the ’55 Chebby
I also feel like I’m having to replace my Torx bits more frequently than anything else. They break or get twisted on stubborn fasteners, like 1980s Ford door latches with those giant Torx heads. I prefer using my Allen sockets over the Torx, but both are annoying in the engine bay for grime filling up the heads as mentioned.
Using an impact driver and wood screws I prefer Torx over Phillips, but the square head is the best.
We have a 2005 Jeep Wrangler Unlimited we are bringing back from a state of disrepair from the previous owner. It’s a mixed bag of SAE, Metric, and Torx.
The problem is Jeep used very shallow Torx fasteners in a many places, making them more prone to stripping. Torx is a tapered tool head, so you need deeper engagement compared to hex keys. The hood and door hardware are especially prone to stripping the heads and were thus replaced with stainless hex key panhead fasteners.
KTM does Torx right – beautiful deep engagement for the tool and there’s only about 4 different sizes on the whole 890R – all of which are in the included tool kit. I’m pretty sure I could have that bike down to a bare frame using nothing but the included tools.
Torx works great. I prefer it over Phillips. I’ve stripped or nearly stripped too many Phillips on accident.
A bit of valve grinding compound on the Philips tip will allow a LOT more torque without popping out of the screw head. And it saves your wrist since you don’t have to push down so hard!
KELLY, what compound do you use?
Fine or Course
Have not heard of this, but will try.
Great idea! It must work well. I’m a big believer in anti seize and this would help on both sides of the issue. Thanks and looking forward to trying it out.
Phillips head fasteners have been junk since inception. They were an inadequate U.S. alternative to the Robertson or square head as some like to call it.
The Torx was designed as a much improved alternative to the Allen head, Phillips and Robertson.
Europe has been using metric for a long time. The UK hung on to SAE and didn’t fully dispose of Whitworth until the 60’s.
The US seems to be the holdout on going fully metric with the US military being the exception, they’ve been metric for a long time. The Torx is currently about the most user friendly fastener
You also have to make sure what looks like a Phillips is not really a JIS (japan industry standard) screw. They look the same, but are different.
The JIS (Japanese Industrial Standard) screw head is superior to the Phillips. It appears to be identical, but it’s not.
Is JIS the same as Posi-Drive, or a different critter all together? Posi-Drive was common on Austin-Healeys – not sure what else.
If you want one socket set that does both, get metwrench. They are sort of ellipseoid, if that’s a word, on the walls of the socket. I’ve had my set for 20 plus years. Love them.
I have never liked Torx, and probably never will. Pain in the rump.
Henry Ford tried to buy or licence the Robertson screw head and it was a no go from the
Canadian inventor—I actually forget why
Ford was pulling a Walmart and wanted the deal to heavily favor Ford. There is a short run of Model T (iirc) Ford made in Canada with Robertson screws.
Some like to say Robertson stood on principle and wouldn’t be screwed by Ford…
I heard that Henry wanted the Robertson screws shipped in wooden boxes. The boxes had to be a certain size so he could use the wood in the Model T (floors??). Robertson said no and the Robertson screws stayed in Canada.
If you have not heard of Pozi-Drive you should look it up. It is an improved Phillips of British origin. The head will have thin lines marked between the +cross+ slots. I have found many people who should know about them don’t; appliance repairmen (British Asian influence) and also SU carburetors.
I wonder if the evolution from Phillips to Allen to Torx is so automated assembly machines can hold them on the end of a driver. They stay on a magnetized driver very well, even with the thread pointing down. The problem with them filling with dirt and grease is our problem, not the manufacturer.
A reasonably well fitting Torx driver will never strip, you’ll break it first. If you need even MORE strip resistance check out Bristol splines.
I think my experience with Torx is clouded by the following:
-cheaply made bits from those “socket set for the universe” sets, because someone bought me one for a present and that is the only Torx I have small enough
-gunky/rusty fasteners that are very small torx and it is tricky to figure out which one it is. Oops guessed it wrong and it just chewed all the splines off something.
Most of my tools are at least medium duty reasonable hobbyist stuff, some are even good! But my Torx does fall into the “suspect garbage” pile. Something I hadn’t thought about until this article and forum posts to be honest.
I’ll address it, because I am dabbling in 90s vehicles now where it matters. My previous hobby vehicles have all been 60s to early 70s so it rarely applied.
For those who have frustration with Phillip head fasteners – a quick review and solution. Phillip head fasteners were invented by the automotive industry in the late 1930’s when the switch from manual assembly of cars to mechanical, or robotic assembly was underway. Phillip head drivers were constructed to “cam” out when torquing down a fastener, as so not to overtighten and applying to much torque. This is why one tends to strip the heads, either by tightening or loosening phillip head fasteners. The construction of the phillip head driver is meant to due that.
The solution to this common problem was the introduction of the Japanese Industry Standard (JIS) fastener. Although not intended to replace the Phillip head fastener (screwdriver), the construction of the JIS fastener (screwdriver), with a slightly different head, ( almost impossible to see unless examining up close) allows one to get full torque on the fastener head (screw) therefore allowing one to fasten or loosening the object intended. The only caveat is since the contact between the tip of the fastener and the top of the object being fastened is so good (a good thing), that if you apply to much torque, one could shear the head of the object being fastened. I have never had this happen to me. Probably
could happen on cheap fasteners. Motorcyclists have been using them for years, as the exterior of many bike have Phillip head fasteners, and one likes to keep them looking good. As both a motorcyclist and an avid classic car collector, these or the only tools I use on my machines for Phillip head fasteners.
Japanese Industry Standard screwdrivers are available nationwide. You can find them online. The brand I use is Vessel, but there are others. They are not inexpensive. Quality tools are usually not. But if you care about the project you are working on, they are a must have tool. Use them once and you will agree with me. I do not represent any tool manufacturer or company. Just a guy who enjoys his vehicles and does what he can to keep them in the best shape possible. Thanks for reading.
I was going to comment on JIS, Walt. I’m glad you beat me to it. You did so far more eloquently and thoroughly than I could have! Thanks!