A Family that Welds and Wrenches Together, Stays Together
This Member Story first appeared in the July/August 2024 issue of Hagerty Drivers Club magazine. Join the club to receive our award-winning magazine and enjoy insider access to automotive events, discounts, roadside assistance, and more.
Bob: We build custom bicycle frames. Not so much now because we’re all distracted by cars, but that’s where my oldest son, Finn, learned how to weld. He comes from a long line of handy guys—my dad, who’s almost 90, is still building and flying radio-controlled planes, and my grandfather, Finn’s great-grandfather, held a nuclear-rated welding certificate. Finn showed the knack at an early age. He went from Lego to RC cars to bicycles to cars.
Finn was 14 when we started on our first build. We traded a bicycle racing buddy a bike frame for a 1974 International Scout. I think he got more metal than we got, because we had to make a frame to hold the body together while we patched up the sheetmetal. Once the body work was done, we painted it, but it turned out all fisheyed. So we had to sand it off and paint it again.
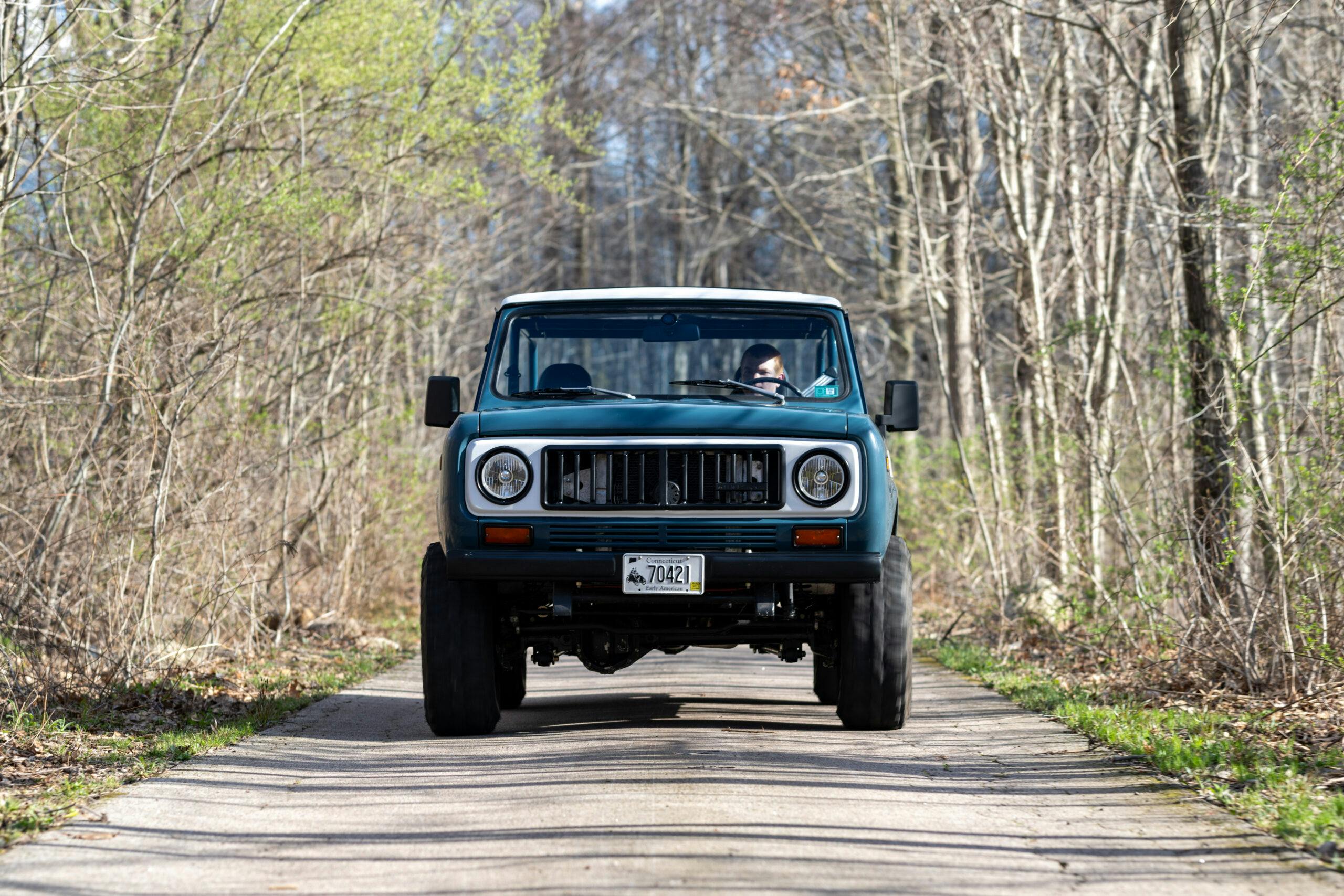
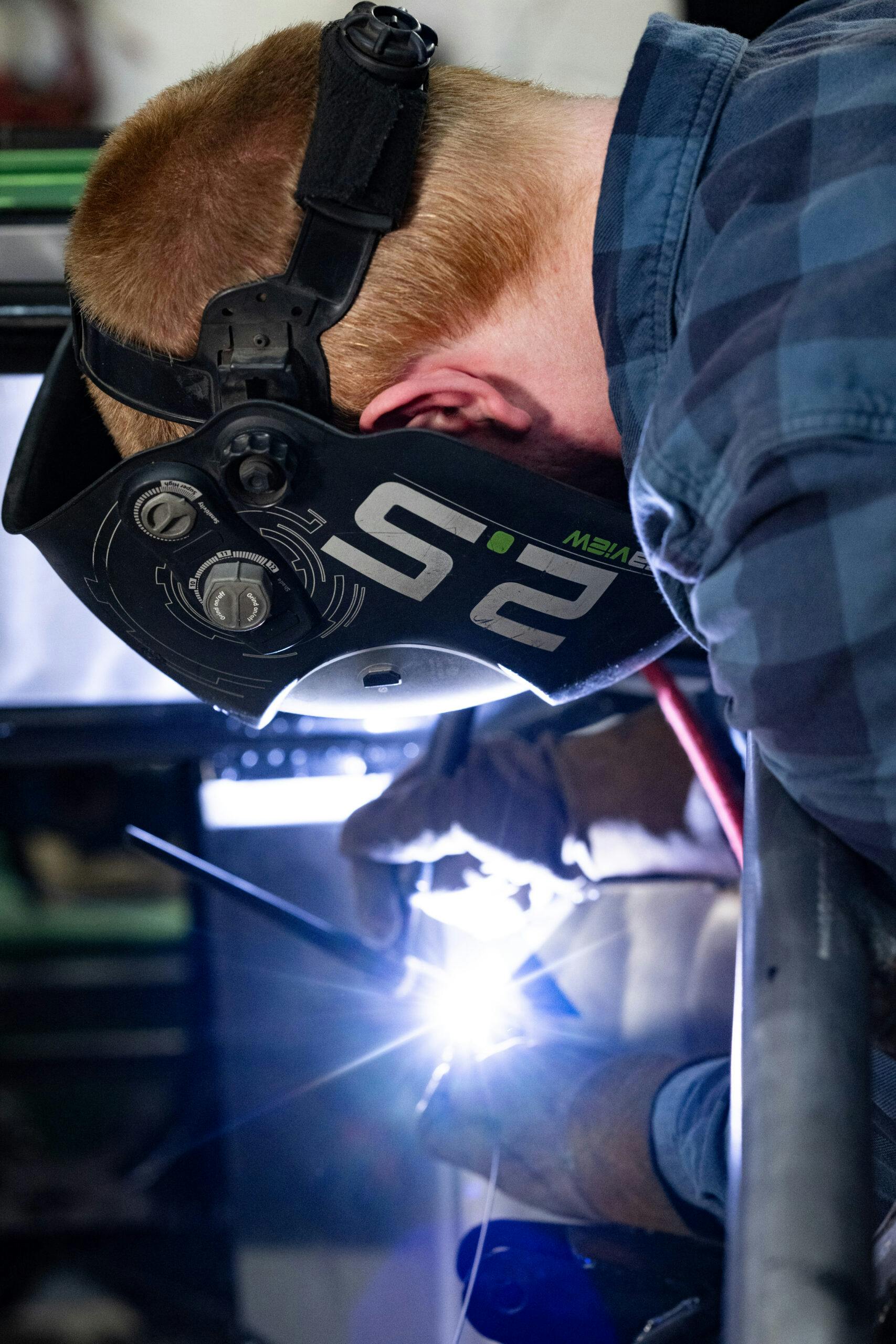
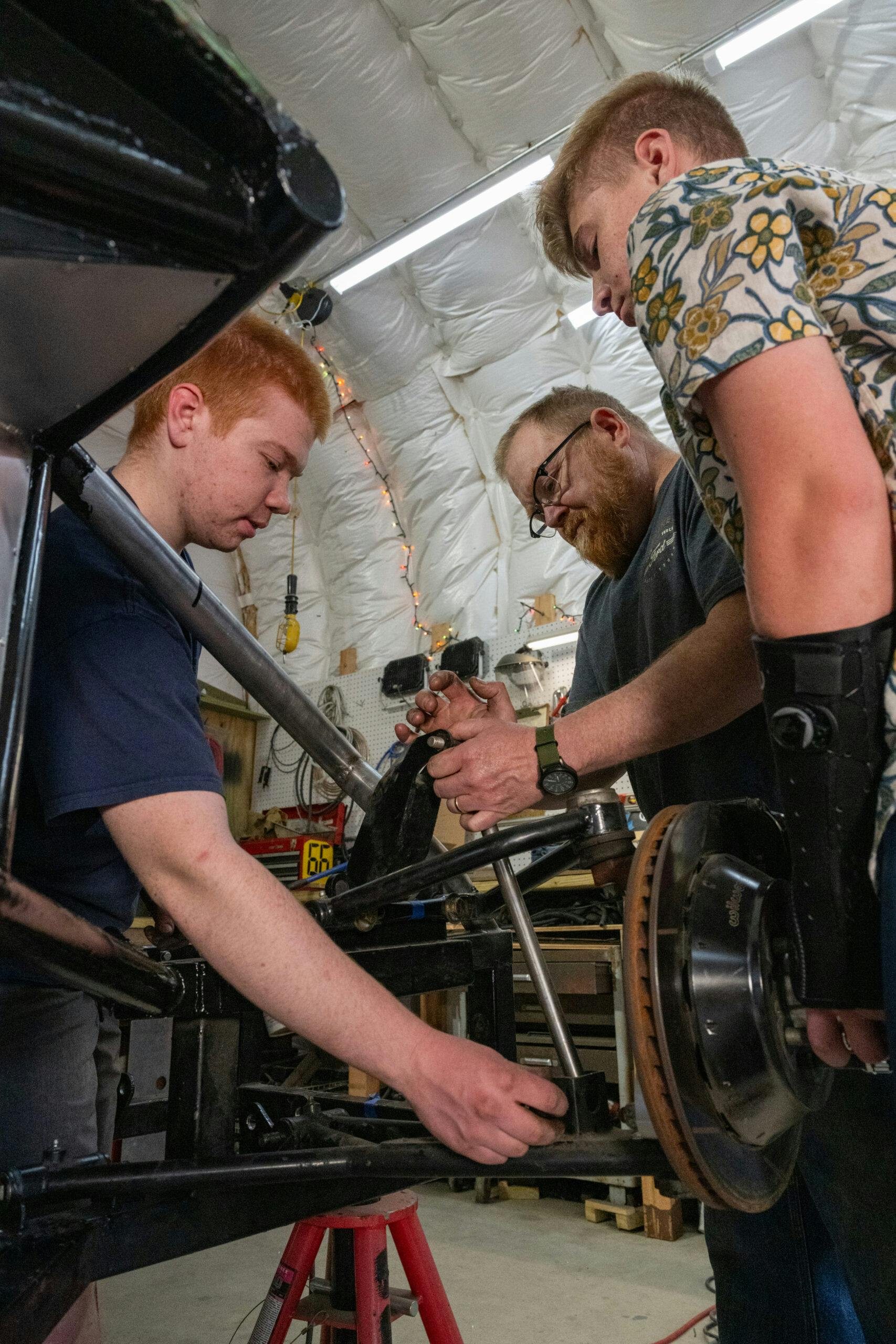
(left) is taking his skills to the next level by studying mechanical engineering at UConn, where he
is a member of the Formula SAE team.Josh Sweeney
I found a 4.0-liter engine from a 2004 Jeep Wrangler for $500, which was cheaper than fixing up the Scout’s old 258-cubic-inch straight-six. It came with everything except the ECU, but that gave us the chance to install a MegaSquirt stand-alone ECU and learn about fuel-injection tuning. We didn’t have a clue how to do that, but we muddled our way through it.
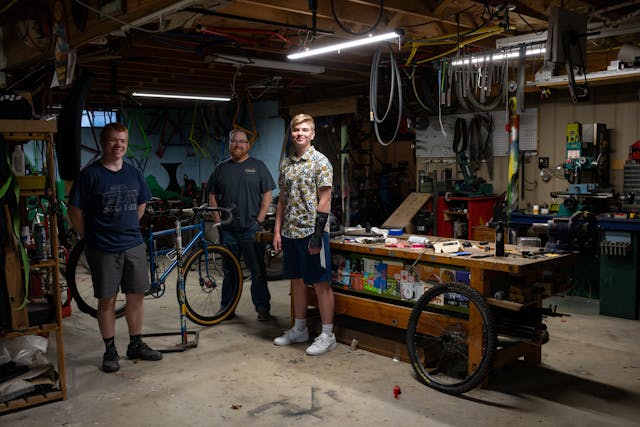
We did the Scout and the truck in the family garage, but my wife eventually wanted her garage space and gave the green light for us to build a barn—a 25-foot-by-35-foot metal arch that looks like a Quonset hut. It’s insulated and heated, and it keeps the mess out of the garage. It’s big enough we have both the truck and another project in there simultaneously. We were thinking of installing a lift because that seems cool, but it’s really not big enough for that. We make do with Quick Jacks, floor jacks, and a set of sturdy jack stands.
The Scout is mostly a driver, but there’s still some stuff we need to do. It doesn’t have the front driveshaft in yet, but we’ll take care of that before we vacation on Martha’s Vineyard and drive around on the beaches.
The Scout project lit a fuse, and we snowballed right into the truck and then the Volvo.
Finn: I had always wanted a hot-rod truck I could autocross. I saw this 1958 Ford F-100 every day on my school bus route in middle school. A few years later, it popped up for sale while we were in the middle of the Scout project, and we bought it. It was pretty rusted out and didn’t have an engine.
We had to replace all the floors as well as the bottoms of the doors. For the engine, we installed a Ford 302 V-8 that also uses a MegaSquirt. We studied chassis and suspension design books, and then we drew it all out on paper. The custom tube frame accommodates a 2016 Mustang rear end and the unequal-length A-arm front suspension. It handled well for being a 3400-pound truck—285-width sticky tires certainly helped.
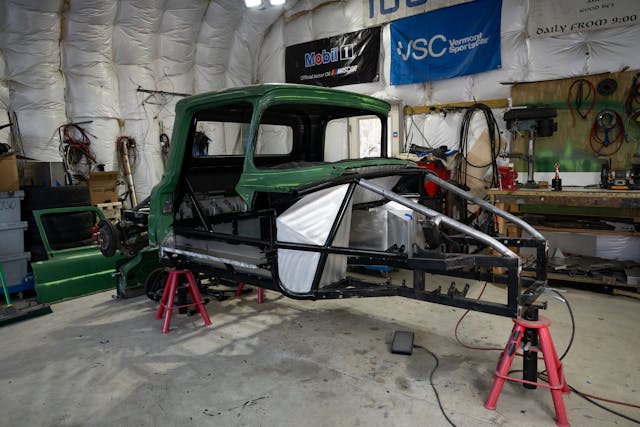
I competed in autocross and drove the truck all over the place for two years, but now it is under construction for version two. I chopped eight inches out of the body under the windows and dropped the cab down and moved it back three inches. This is so I could push the engine back 10 inches behind the front axle for better weight distribution. At some point, we’ll try to make some fiberglass pieces for it, like a one-piece front end, bed sides, and fenders. The goal is to have it weigh less than 3000 pounds and still be streetable.
Bob: It’s cool when people at the autocross compliment the F-100. They ask, “Who made this truck?” and I point to Finn. I wanted Keenan, my youngest, to have the same experience, even though he doesn’t have the fabrication bug like his older brother.
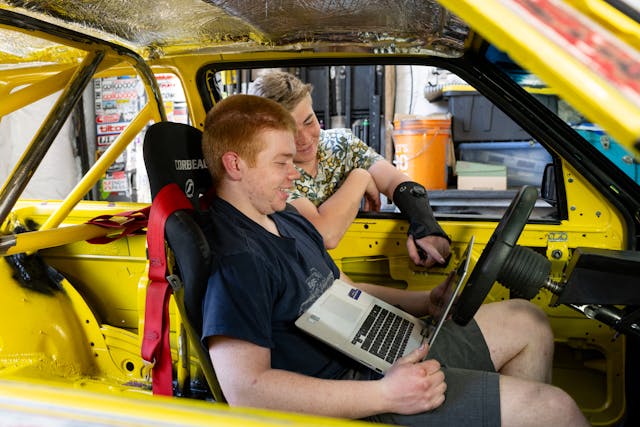
Keenan: We got a 1967 Volvo 122S for $8000 when I was 13. It was in a barn for 35 years before a friend of ours rescued it. The Volvo still had original paint, but the original owner had painted orange stripes on it.
Right after we finished the truck, we started tearing down the Volvo. We did the interior, like the headliner and the floors and the dashboard, and we rewired the whole car, putting in a fuse box and all the lights.
The original 1.8-liter four-cylinder didn’t have a lot of power, so we took that out and put in a Ford 2.3 turbo engine and a T-5 transmission from a Thunderbird Turbo Coupe. We got two of the engines from Facebook Marketplace for 600 bucks. Finn did all the welding for the intercooler and the exhaust. We also replaced the rear axle with one from a 1968 Volvo P1800 because it’s stronger and bolts right in. We put in a limited-slip differential, too, so it’s good for autocross. It’s nice now, and it’s fun to drive. On good days, I take it to school.
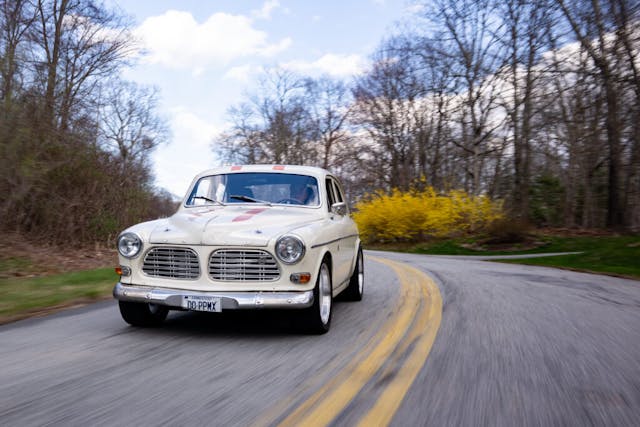
Bob: As a dad, both of these guys make me super happy. They get a lot of attention because there aren’t a whole lot of kids doing autocross in the club—and certainly none driving vintage vehicles. We’re having fun doing it ourselves, and the boys are learning valuable skills along the way. And when you build it yourselves, you know you can fix it no matter how thoroughly you break it. Luckily, we haven’t blown anything up too badly yet.