Is this the next great leap for internal combustion?
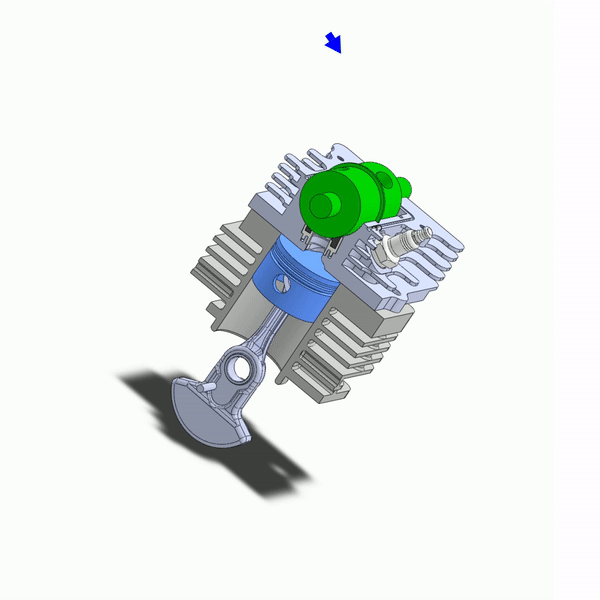
We may have been doing this wrong all along. With cylinder heads, that is.
Back when it all began, steam was the start—how we first captured heat energy from fuel and put it to work. More than a century ago, steam powerplants formed the basis for the design of the first internal-combustion (IC) engines. Moving the combustion from an external source (a steam boiler) to the inside of the drive cylinder was a major step forward in power and efficiency.
Since steam engines were laying around all over the place, many parts were carried over. Components like pistons, connecting rods, and cranks were near-enough correct to make a gasoline engine sort of run, and things evolved from there. The sliding sleeves and popular barrel valves used to control the flow of high-pressure steam, however, did not make the cut. They leaked.
Leaking a little high-pressure steam here and there is not of major consequence in the grand scheme of a locomotive. Because cylinder leakage carries real drawbacks with an IC engine, sleeve valves and barrel valves were abandoned, replaced by a kind of valve called the poppet. The type of valve now found in almost every four-stroke IC engine on earth.
Poppet valves were and are a decent fit for a four-stroke’s high internal pressures and combustion temperatures. Mated with a countersunk seat, the poppet’s chamfered face forms a positive seal, and that seal improves as pressure on the valve face increases. Although they require complex drive and support systems (cams, keepers, springs, lubricated guides, etc.) poppets have been developed into a reliable solution.
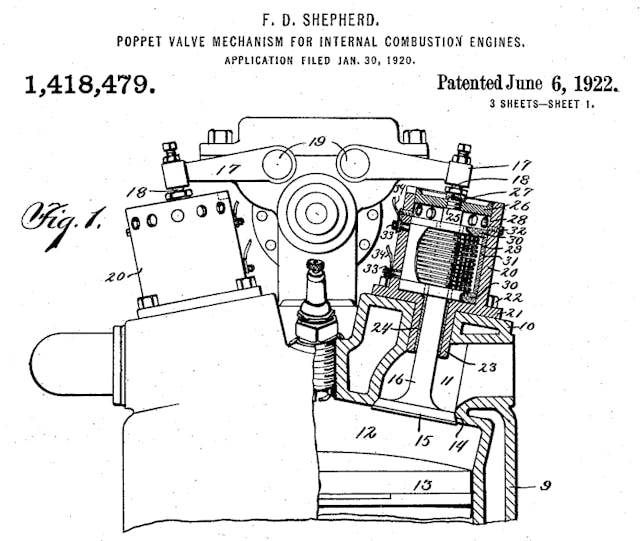
What we gained in reliable sealing, though, we lost in flow. A poppet valve’s head is always in the way. On the intake stroke, a poppet valve’s head blocks about 20 percent of the air trying to fill the cylinder. With the exhaust stroke, the valve is essentially attempting to evacuate a crowded theater through a door that won’t fully open. The piston is rising, pushing combustion byproducts out the exhaust port, but the valve’s head is in the way.
In the case of the intake valve, we’ve evolved to a sweet spot where a poppet can flow more than 100-percent capacity—more air can be moved past the valve and into the cylinder than the dimensions of the intake path and cylinder would suggest. But that’s due to the velocity of the incoming airstream, the air “ramming” itself past the valve’s head. (For an exaggerated illustration of this effect, see the now-outdated Japanese “subway stuffers”—they were literally ram effect personified.
This is no small issue. Every engine is, in essence, a dumb air pump, limited in its ability to bring in air. Burning gasoline and exhausting high-pressure gases are pretty easy tasks by comparison.
Cylinder filling has been the problem for two centuries, since we began moving away from steam. The column of air sitting over the earth weighs only enough to create around 14.5 psi of ambient pressure at sea level. When it comes to pushing air into a vacuum—like the one created by a piston moving down a cylinder—that pressure isn’t much. It’s even less at altitude, like on Pikes Peak, where the mountain’s height leaves the air column above short enough to give less than 9 psi. (Ever wondered why turbo- and superchargers predominate on race cars run at altitude? Now you know.)
After 100 years of being fussed with, the poppet valve is, in a sense, grandfathered in. It is now highly functional but not optimal. We have band-aided the poppet’s poor performance partly by increasing the number of valves—some cylinder heads have four or more per piston. Over the last century, however, the inventive human mind has tried to revive certain steam-engine concepts, to take advantage of their superior flow ability.
During World War II, when air power was the ultimate arms race, engine designers on both sides dusted off the concept of sleeve valves. By configuring those valves around pistons, they found tremendous power improvements. (While also making massive progress in the development of things like high-octane fuels, superchargers, turbochargers, and nitrous-oxide injection—all over the span of about five summers.) The power increases came mostly from the airflow made possible by those sleeve valves, a clean and unobstructed path from intake port to cylinder, no poppet head in the way.

This improved air flow was put to good use: A fighter plane that can out-climb or outrun an opponent can easily turn and shoot them down. For all the benefits brought by their improved flow, though, sleeve valves leaked oil, they wore out too quickly, and they required monkey-motion levers in the crankcase in order to work correctly. The technology never made it to automotive production in any significant form.
Still, the siren song of full flow capacity is hard to resist. And like the sleeve valve, the barrel valve—a type of rotary valve—has long captured the fascination of engine designers.

A shaft with a slot cut into it, rotating in seals, is so simple and capable that it has been tried dozens and dozens of times. Where a standard poppet valve may peak at flowing 85 percent of its intake area (and then only temporarily, when fully open), a rotary valve opens faster and can flow 100 percent of its intake area more of the time (meaning, over more of the valve’s opening duration). If you have a 5.0-liter engine that can only breathe at 85 percent of capacity, you don’t really have a 5.0-liter engine. One-hundred-percent intake-valve flow makes more power every time.
With the barrel valve, the gremlin has always been sealing. For a long time, any seal material that pressed against a barrel valve’s shaft enough to contain combustion pressure—upwards of 1500 psi at 2500 degrees Fahrenheit—would also give high friction and wear. If you loosened up the seal’s tolerance on the shaft to reduce that friction, it would leak. Either way, the high temperatures ate away at any sealing material tried.
The industry birthed prototypes, test engines, and a few production attempts, but no rotary-valve design or layout has been fit for real commercial success. Felix Wankel, the inventor of the rotary engine, started his career developing disc rotary valves that were eventually used in German torpedoes. In 2004, the Mercedes-Ilmor Formula 1 team got as close to the summit as anyone, with an adaptation of a rotary valve patented by a man named Bishop. But alas, F1’s (power-hating?) sanctioning body responded by outlawing any valve not a poppet. So much for racing promoting innovation.
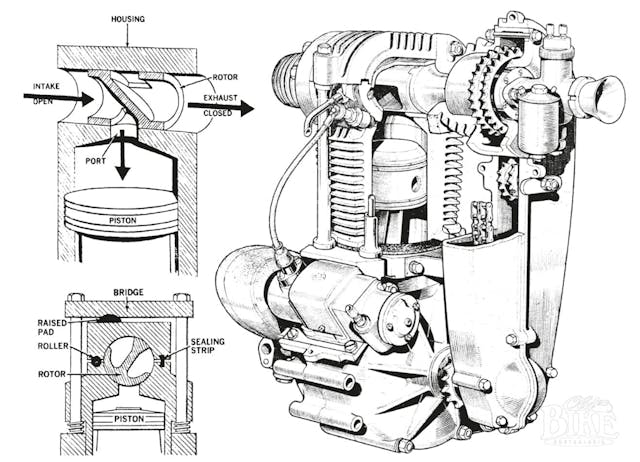
All hope is not lost. As part of my work as a professor of IC Engine Design at UNC-Charlotte, I was called to consult in “Race City, USA” (a.k.a. Mooresville, North Carolina, home of NASCAR), to assist a company that had found a way to seal a rotary valve and take advantage of the potential.
That company, Vaztec, was founded by a team of engine developers who had supported GM and Ford racing for decades, and who had grown disillusioned with how badly a poppet valve actually flows. Now six years in, they have just returned from a Society of Automotive Engineers conference in Japan, where their white-paper presentation on a successful rotary-valve design won an award.
Maybe time is nigh for a change.

Vaztec has developed and patented a dynamic, high-temperature sealing system that adapts to the shape of a rotary valve as it expands. That expansion is the true Achilles heel of a rotary-valve system. Almost all metals expand as they heat up. If your valve seal relies on a thousandth of an inch of clearance to work, as many automotive seals do, having that valve grow three times that amount as the engine warms is a recipe for failure.
As the Vaztec project advances, some interesting side benefits have appeared. One is a cooler-running valve. The poppet is a sitting duck in the combustion chamber, exposed to 2500-degree combustion gases during the piston’s power stroke. Then, during the exhaust stroke, the valve’s head gets stuck in a jet blast of 1400-degree exhaust. Milliseconds later, that head carries leftover heat into the engine’s next power cycle. Because a barrel valve is constantly turning, heat transfers more evenly into the cylinder head.
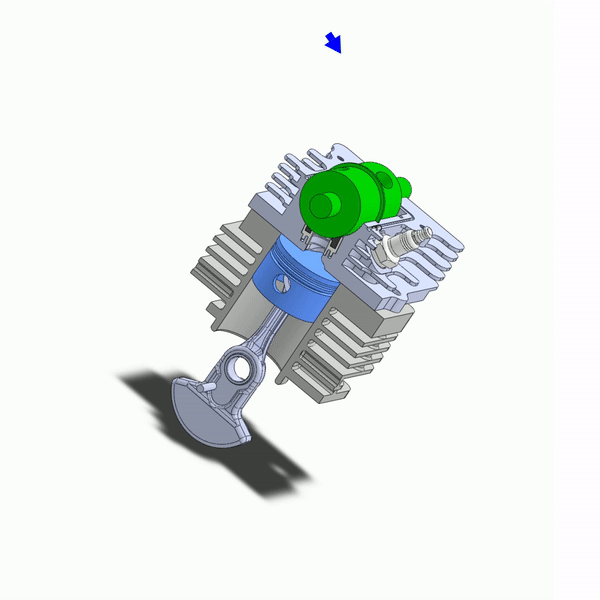
That heat transfer is helpful. At peak power, the head of a poppet exhaust valve can serve as a “glow plug,” growing so hot as to spontaneously ignite fuel and air. Lowering an engine’s static compression ratio helps alleviate this; by the same token, if you eliminate the glow-plug effect, you can make that ratio higher. All else being equal, higher compression ratios improve power and efficiency—a strong step toward keeping the IC engine alive and relevant in years to come.
Those benefits were somewhat expected. An unexpected byproduct of unobstructed intake flow was the increased, and now very high, velocity of intake air as it rushes into the combustion chamber.
Intake air gets up to crazy speed in high-load conditions—Mach 0.55, or around 450 mph. That velocity is what drives the aforementioned “ram effect,” the jamming of a combustible air-fuel mixture into a cylinder. That velocity generally produces turbulence, which stirs up and quickens the combustion process, aiding power.
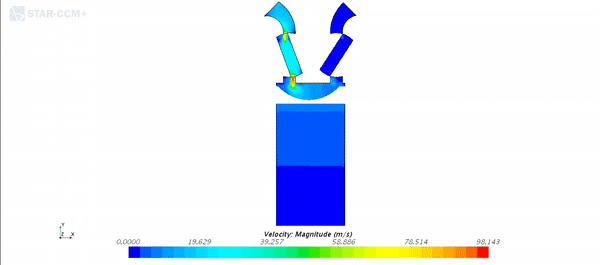
Interesting side note: A few decades ago, I had a fascinating conversation about intake velocity with former Car and Driver editor Gordon Jennings. He proposed Mach 0.9 as the actual goal—near-sonic airflow. Even then, however, things would still be greatly disturbed by the poppet valve’s head, which hangs out at the end of the intake port like a bouncer at the entrance to a party. With the bouncer gone, things change. Rather than an orderly “deflagration” (picture of a sheet of paper lit by a match at one corner, the flame moving slowly to engulf the page), we get flame-folding and combustion that takes place much more quickly.
This is a different type of cylinder process than we are used to, one highly efficient, very rapid, and very useful. A telltale is how Vaztec’s development engines have required roughly half as much ignition-timing advance as they would with poppet valves. Because the fuel-air mixture burns quicker, these engines can fire their spark plugs later in the compression stroke, which lets them make more power—the force of the cylinder’s burn is no longer trying to shove the rising piston back down. (With slower combustion rates, this is a very real “taxation” cost of advanced ignition timing.) The greater turbulence also sweeps lazy end-gases into the combustion party, giving less time for detonation sites to emerge in the chamber.
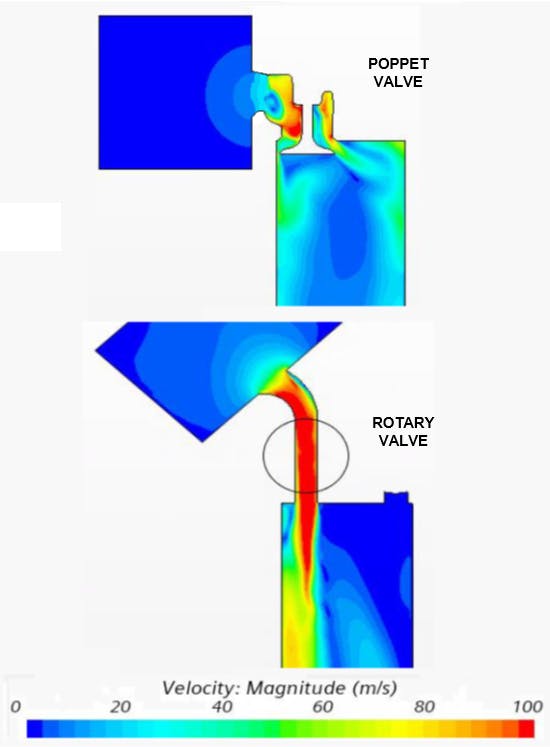
Designing a new engine system is one thing. Actually getting it to run is another. Six years ago, Vaztec began developing its rotary valve inside, of all things, a diesel engine. Diesels use extremely high combustion pressures, up to 2500 psi, so this was a tall bar, but also a fine way to prove the idea. Next, the company set its sights on the power kings of the engine world: two-strokes.
A two-stroke cylinder has a firing cycle every crankshaft rotation. A four-stroke fires only every second rotation, half as many power pulses for a given rpm. Although two-strokes excel in power output per cubic inch, they offer relatively poor control of incoming and outgoing gases, and that serves as an upper limit for output. (My ’72 Bultaco 250-cc two-stroke motocross bike made 144 hp per liter when I raced it 45 years ago, and Honda’s two-stroke, 500-cc NSR 500 grand-prix bike made 400 hp per liter in the 1990s. Compare these to the laudable 5.5-liter V-8 in the current Corvette Z06, which makes 122 hp per liter. What two-strokes don’t do well is run cleanly, which is why federal emissions regulators are eyeing them for eventual banishment.)
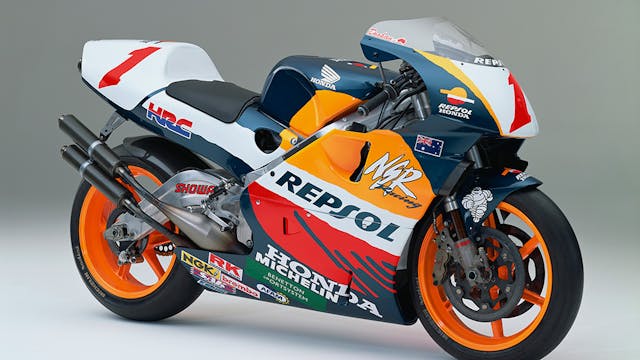
As a test, Vaztec set its sights on making a high-power, clean-emissions replacement for a 50-cc two-stroke, in the form of a rotary-valve four-stroke. This was the topic of the award-winning SAE presentation mentioned earlier. Vaztec’s rotary-valve, 45-cc single matches the power of a production 45-cc two-stroke chainsaw/weed-trimmer engine, and it can rev just as high (more than 12,000 rpm). It also made 50 percent more power than a similar, 48-cc four-stroke poppet engine currently on the market.

About that rpm peak: Poppet valves give an engine an upper speed limit by nature. At extremely high rpm, a spring-closed poppet valve will float—hover off its seat, unable to fully close and seal before the cam that controls the valve forces it open again. Since a rotary valve spins like a shaft, supported by bearings (imagine a camshaft without lobes or loads), it lacks that traditional limit. That Mercedes-Ilmor F1 engine easily spun above 20,000 rpm, limited primarily by the strength of its crankshaft and connecting rods.
For a more automotive-scale test, Vaztec has developed a one-cylinder engine with two rotary valves, one each for intake and exhaust. This engine uses a 90-mm bore and a 70-mm stroke, which makes it comparable in size to one cylinder of a 1.8-liter in-line four. It currently makes 50 percent more power at 4000 rpm than the similarly sized poppet-valve engine that Vaztec chose as a baseline. Very promising.
On the endurance front, Vaztec has built ten prototype engines over the past six years, from a 28-cc single to a 5.3-liter version of GM’s LS1 V-8. The company’s engineers have hundreds of hours of durability tests showing scalability and strong results. The valve itself is simple, with very little to deteriorate. Even at these early stages of development, wear rates of these prototypes extrapolate to an engine life exceeding 5000 hours.
At the moment, Vaztec is working with engine manufacturers to scale the technology into powersports, and eventually automotive-production applications, including hybrids. The greater power density, improved combustion, and increased efficiency are coupled with reduced noise, reduced vibration, and reduced wear. On top of that, those benefits are brought by a system that uses 33 percent fewer parts than a traditional poppet arrangement, that requires no special materials or processes to create, and that costs less to make and assemble.
An added bonus? No valve adjustments for the life of the engine. And we get to keep our pistons and crankshafts.
While most of the advances in engines in the past three decades have related to controls like direct fuel-injection and variable valve timing, it seems we’ve found a way to improve the fundamentals once more.
Could the poppet valve go the way of the choke lever and dashboard cassette player, into the dustbin of history? Perhaps, just as carburetors have been largely replaced by fuel injection, rotary valves will take over. We shall see.
***
Full Disclosure: Norman Garrett is an engineering consultant for Vaztec and has helped develop the company’s rotary-valve technology. He is a freelance contributor to Hagerty and was paid for this story.
Check out the Hagerty Media homepage so you don’t miss a single story, or better yet, bookmark it.
Bishop wore his shoes out at Indy trying to get funding for his idea. Glad it is finally happening. He was a wonderful man to talk with.
Great article and information!! But with the push to electric, is it too late for adaptation??
I know the sealing is Vaztec’s secret sauce, but after all the buildup about how hard it is to do, some sort of explanation on how they have overcome the sealing challenge seems warranted. Otherwise a very interesting article.
Car manufactures will never release significant design improvements rapidly. A gradual improvement will keep people coming back for something better at a higher price.
This is an interesting story. As someone who worked on Sleeve valve aircraft engines I can attest to the incredible power but also reliability of the old Bristol Hercules engines. In comparison to the Pratt and Whitney R2000 radial engine with the same displacement the Bristol engine produced 30% more power and had a time between overhaul of 3000 hours vs an average lifespan of about 1200 hours for the Pratt. I really can’t comment on the oil consumption as they both used oil. The line maintenance on the Bristol was a fraction as there was no valve train adjustment to worry about. I hope we give the =se new engines a chance before we switch to the electric motor – which in all reality will probably replace the IC engine in short order for most applications anyway.
rotary valves have been tried in cars many times over the years. if these folks have a long life solution, great!!
one thing i did not see in the many excellent illustrations is any indication of seals running parallel to the axis of rotation that actually would do the sealing against combustion. i assume that is to keep the proprietary info away from prying eyes.
Dykes mentions rotary valve in several locations, including their use in the “Speedwell” auto
“Honda’s two-stroke, 500-cc NSR 500 grand-prix bike made 400 hp per liter in the 1990s. Compare these to the laudable 5.5-liter V-8 in the current Corvette Z06, which makes 122 hp per liter”
Comparing a 2 stroke racing engine with a life span of a couple hours, to a production car engine designed for power and longevity is just dumb.
The 3.0 F1 V10s were hitting almost 1000hp. And the 2.4 V8s were at 930-940 hp- despite being restricted for years- for about 385 hp/litre.
Had the same idea in 1955, at that time (question=what metal for rotors, and what kind of bearings, combined
with seals ?)
Of course it will work fine , but wear is the problem combined with carbon ?
In the “nothing new under the sun” department, a rotary valve engine that was designed, built and used in a car dates back to the early 20th century. Look up the “Mead rotary valve engine” that was used, albeit briefly, in Dayton-built Speedwell car back around 1912 or so.
The Mead design sealed the rotating valve with what were essentially piston rings in grooves on each side of each valve port. However, metallurgy of the time wasn’t quite good enough to provide a truly gas-tight seal, and in actual use, the engines gave all sorts of problems–to the extent that Speedwell had to replace all those Mead engines with ones using conventional poppet valves. On top of that, their entire winter production of cars (most were sold in the spring and summer back then) were ruined when the factory flooded during the 1913 Dayton flood. Together, they bankrupted the company.
This valve system is fine for a stationary engine, but it would be totally unsuitable for revving up and revving down engines.
Very slow response due to the inertia of all those steel valve shafts.
Certainly no good for racing.
The issue of lubrication still exists and always will.
In reading their white paper on the Vaztec website, they are not using any lubrication for their rotary valve system which greatly simplifies things…no oil in the cylinder head means no oil sealing/burning issues.
Somebody’s thinking! Great article! Remember the 70’s dirt bikes from Suzuki that used what they called a rotary valve….carb mounted on the crankcase…flat flexible plate….with a cut out to control fuel timing…..o ring to seal….exhausting conventional through a cylinder port…..
Rotax is still making them
What ever happened to the Coates design that was similar in concept and design?
Then why not build this highly efficient rotary valve engine, that is ideal for small displacements, into, say, a 10hp “pony” engine, whose sole function is to power a generator that keeps the batteries charged on an EV? You’d have stellar range, ultra-low emissions, the added weight would be minimal, as well as little maintenance. Plus, you would have solved the “home-charging” power grid dilemma. You could even offer both means of charging for convenience. Fill the tank on the in-car generator once a month as it only runs when necessary, rpm would be constant so engineered for minimal wear. Air-cooled so you’ve eliminated cooling system. Am I off-track here? What am I missing?
When you look at the average efficiency of a production internal combustion engine and even the maximum that can be yielded, there is still a lot left to be gained as far as efficiency. From what I’ve read it looks like 40% efficiency is in the ballpark of what engines achieve. Even for anything that reaches 60% efficiency, that still leaves 40%. If they can get internal combustion engines up to around 80% to 90% efficiency, that would make them a lot more environmentally friendly and use a lot less fuel. Speaking of which we can probably improve fuel itself as well
Whether it’s possible or not I don’t know but I think it is. Apparently it is very difficult but that doesn’t mean impossible. It is definitely going to require radical changes in design and thinking way outside the box. Hopefully this system gets perfected, and then something revolutionary happens with the crankshaft, I think there’s a lot that can be gained in that area as well.
Gasoline has about 100 times the energy density of lithium ion batteries. Plus those materials are very bad for the environment to mine, and They are not very recycle friendly either.