6 tips for using jack stands
Working on cars requires a whole slew of relatively specialized tools. Often times we don’t even realize how unique those tools and practices are until we talk to someone new to the hobby. Or someone who is on the outside looking in. Just one example: How casually we discuss (and practice) the act of lifting our multi-thousand pound vehicles into the air and then supporting them with separate load-bearing apparatuses that allow us to work on, disassemble, or reach under the vehicles. It’s dangerous when done right, and deadly when done wrong.
That sounds scary, and to a point it should be. Being cautious when the risks are this high is not a bad thing. That’s why we created a quick list of tips for using jack stands: good for newbies, but it’s also a refresher for those experienced enough to have lifted up a vehicle many times, in many ways over the years.
Buy once, cry never
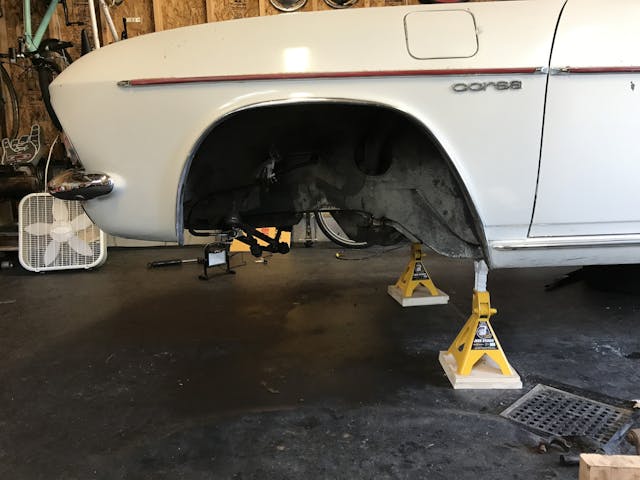
There are many factors in selecting jack stands, and price is one that many of us are forced to consider. While tools can and will be shopped based on price point, jack stands should not be one of them. These are critical safety items that should come from reputable and trustworthy sources. The Harbor Freight jack stand debacle of 2020 should be burned in our collective memory for a long time, as being crushed by your car is not the way to go. Cheaping out with jack stands is a fast track to a mere feeling of safety, rather than possessing actual safety.
Jack stands should be sturdy with a good wide base. A secondary method of locking them at the desired height is also a plus. Do not modify jack stands or otherwise compromise safety features in the name of convenience. Doing so is only making it easier to get hurt.
Size appropriately
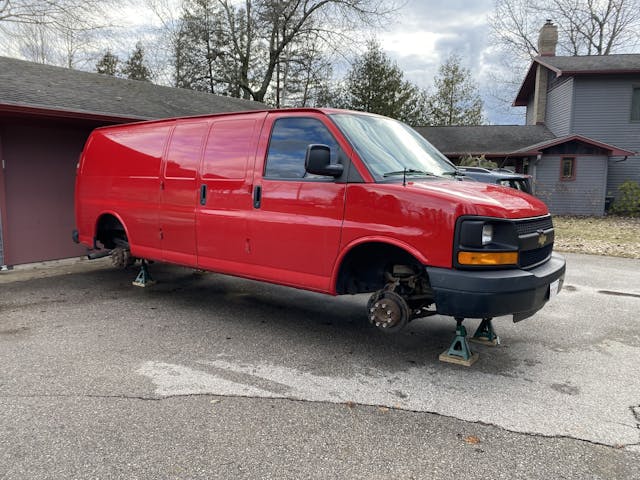
Jack stands produced after 2015 are rated as a pair. Which means if you find some at the local parts store that say they are “three-ton” jack stands, the ability to support the claimed 6000 pounds requires both stands. In reality, three-ton jack stands should be the smallest used in most home shops, as it gives a good safety margin when working on smaller cars, yet a set of four does have enough capability to hold a medium-sized truck or SUV in a pinch.
Remember that storing jack stands can be a hassle, so having one set that covers anything you’ll work on is the best way to go. That said, a small and large set of them is a nice luxury if you have the space. Inevitably something gets “stranded” on your one set of stands…and you’ll need another set shortly thereafter.
Trace the load path

Jack stand placement is as critical (if not more critical!) than proper sizing. The biggest jack stand in the world is useless if you place it in the wrong spot, letting the car fall down anyway. The service manual is the best place to look for jack points and jack stand placements. Even the owner’s manual in the glove box, a book that’s been shrinking over time and loaded with “please see dealer” language, likely still outlines the jack points for safe lifting. A quick internet search will likely reveal appropriate information too.
But sometimes that doesn’t work, or what you are doing is something the original engineer from decades past could have never imagined. That’s when a little bit of critical thinking goes a long way. Look under the car and locate a place that looks sturdy enough to place a jack stand, then follow what that is connected to. From there, imagine how it would support the load being placed on it. Supporting the rear of a car by placing stands under the rear differential makes sense because the entire weight of the car is normally supported by that part. Using a bumper or frame brace that doesn’t support and wasn’t designed for that load is a bad place to put a stand. If unsure, consult professionals.
Do the shake test

Now that your project is up in the air and supported by jack stands, there is one last step before you roll underneath: You gotta shake it. No, not the latest TikTok dance. Shake the car. Go to one of the corners and give it a good push and pull to make sure the car is stable and the stands are not going to move or shift while you are underneath. This is the same thing that mechanics in shops do when putting a car on a two post lift.
After all, now is the time to find that the ground isn’t really flat or the stands aren’t fully seated on their safety catch. Only after a good shake can you roll under the car with confidence that it will not be coming down on top of you.
Buddy system
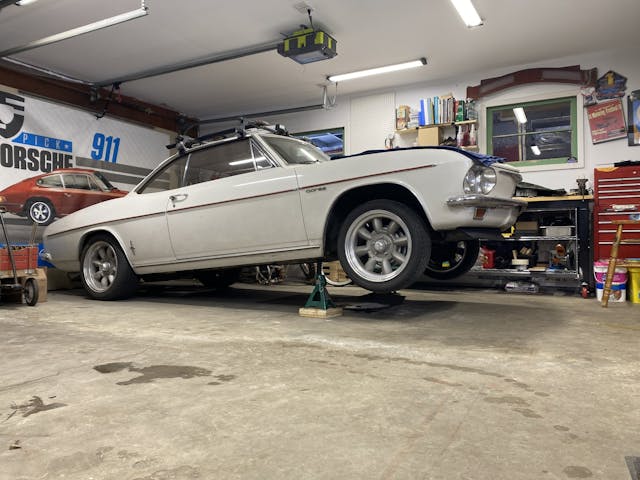
It feels strange to do when performing an innocuous task like adjusting a transmission shift cable or removing a driveshaft, but telling someone that you are working underneath a car with jack stands is a good practice. A text or call to a friend just to say “hey, I’m working on my project and am under the car for a bit” is enough of a heads up: if they don’t hear from you in awhile they know to check on your well being. Being pinned or injured under a car with no means to get help should be horrifying to you, and encourage you to whatever is necessary to prevent it.
Keeping a phone on your person is one option, as is using smart speakers or other items that require nothing more than yelling at them to activate them. I personally have a Google Home Mini above my workbench, which allows me to broadcast a message to another speaker inside my house by just yelling at it. This lets me feel safe-ish when I am working on projects while my wife is inside. (Presumably enjoying her time without me.) This practice isn’t for everyone, but it works for me. Find a system that works for you and use it.
Cribbing away that sinking feeling
Motorcyclists are familiar with the peril of asphalt: Ride somewhere on a warm day, set the bike on the kickstand, stop for a coffee, and the bike is laying on its side by the time you get back. Vandals? Inattentive drivers parking too-big SUVs? Nope. The asphalt did that.
Asphalt comes in a variety of flavors and mixtures, some of which isn’t nearly as solid as it feels under your feet. A heavy load concentrated on a small point can sink into asphalt. And the weight of that motorcycle leaning on the kickstand’s relatively small area can punch a hole into asphalt. Lo and behold, the kickstand sinks down enough that the motorcycle tilts and falls over. Bad news, but it points to a bigger problem.
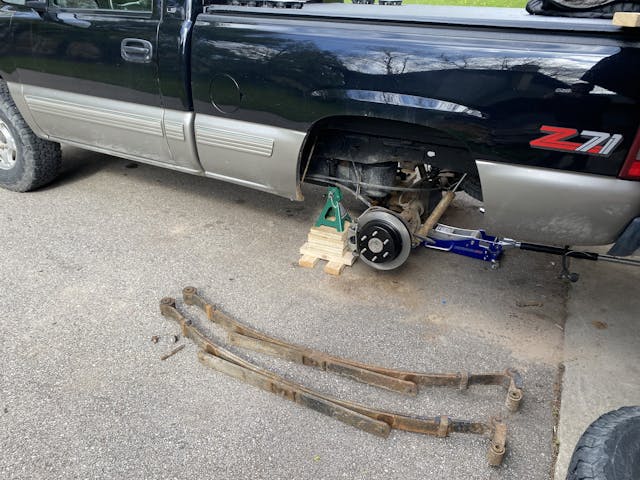
Now picture this kickstand is actually a jack stand under your project. With no warning, the car can shift as the asphalt gives way. Prevent this by using something like a chunk of wood to spread the load of the jack stand to a larger area. The same applies for any soft substrate like gravel or dirt. Cribbing is a common thing in heavy equipment transport/service, and by extension is a smart exercise to do when working on light duty vehicles as well.
Have another safety tip to add to the list? We’d love to hear it, as you can’t be too safe in these situations. So leave a comment below for everyone’s safety and well being.
***
Check out the Hagerty Media homepage so you don’t miss a single story, or better yet, bookmark it. To get our best stories delivered right to your inbox, subscribe to our newsletters.
I find jackstand ratings confusing then. I’ve used a single 3-ton stand to hold up one end of a rear deuce-and-a-half axle, which is a 2000 lb load with the truck empty. In my ignorance of this I’ve never had issues and there is no damage to the jackstand that I can discern. I always thought the rating was 3 tons per stand and not 3 tons per pair, which would mean 1.5 tons per stand!
To add more to this confusion, I’ve also used a 4-ton bottle jack to jack the truck up. Is that a rating for a pair of bottle jacks then? I’m concerned about how inconsistent ratings are between jackstands and jacks. If I can jack it up with a 4-ton jack, I better be able to hold it up with a 4-ton stand, not some 2-ton stand that needs a buddy on the other side to be considered a “4-ton jackstand”.
I consider myself lucky at this point and at the mercy of engineering safety factors that go into jackstand design. I guess I’ll be beefing up my stands. Maybe this rating discrepancy between equipment type is a manufacturer conspiracy to get us to spend more on bigger tools? I’d hope not but I’m somewhat a cynic.
1 ton is 2000 lbs. So 1.5 ton (or 1/2 of a 3 ton jack stand pair) is 3000 lbs. A bottle Jack of 4 tons can lift 8000 lbs. You are within safe working load of your Jack stands and bottle Jack.
Thanks – I got my math all screwed up!
Harold, also jack stands are normally sold in pairs so that’s why I assume they rate them in pairs. On the other hand a bottle jacks are sold individually, so the rating would be for 1.
Thank you for the safety article on jack stands. I have the Harbor Freight 6-ton jack stands subject to the recall. I had my 3150 pound car supported by them this summer. I crawled under the car numerous times. I had no idea they could be faulty. It’s time for a trip to my local Harbor Freight store. Thanks again.
I am reading about blocks, and stands, and lifts, and all sorts of other makeshift things. All my life there have been jack stands where I was working, dad had a set, my uncles had them, I own a pretty nice set, my friends had them. I use them and I do like them. All that said, when I was a kid we had a log at home that we just could not split no mater what we tried, that log was the go to primary safety stand for years, the routine was put the car on the jack stand and always jam the log under the side you are working on as a safety backup. The log made dad feel a lot better and it was a handy place to put tools, I honestly miss that log. Yes, the stand did once settle into the asphalt and was on the log at the end of the job, no one noticed until the log and stand couldn’t be moved to get the jack back under the car at the end of the job.
Great article! Your point on placement being important rang especially true for me. A few years ago, I agreed to help a friend (who had more enthusiasm than mechanical experience) convert his ’66 Mustang from drums to discs up front. I told him I would only help if we also went thru every wear piece in the front suspension and steering. He agreed. When I arrived on that first day, the car was positioned as I had suggested – with the nose toward the door to get the most natural light. I saw from the drive that he had already put the car on stands, removed the front wheels, and was underneath loosening something. Nice start! When I got to the front fender and could see into the wheel well, I practically screamed for him to get out from under it NOW! Instead of placing the stands under a nice flat part of the car, he had put them under the portion of the subframe that slopes upward toward the front to clear the suspension. If he had banged on anything or even applied torque in the wrong direction, the stands could have slipped, and the entire car would have fallen on him. I really don’t know how it was perched at an angle like that to begin with. Must have had a good coating of road grit to give it traction… We then had a lesson on the proper places to support a first gen Mustang. Seems like a no-brainer to most of us, but well worth the mention in your article. Well done!
Never be cheap and do it right. It’s simple to do.
I notice a few people mentioning chocking the wheels – hopefully they meant after the car was already up. With typical floor jacks, something has to roll as the car goes up. If the jack wheels are not free, the lift pad on the lack can slide. It only took having to replace one gas tank to figure that out – I’m a (sort of) fast learner
I had a jack stand slip out doing front brakes. I was sitting on the ground, facing the rotor. My legs in the wheel well. The rotor hit the ground, right in front of my nuts! A lesson well learned!
I was working on on one of my cars and had all 4 of my jack stands underneath it. I had to work on another one of my cars so I used a bunch of scrap 6″ X 6″, 4″ X 4″ and 2″ x 4″ cut into 16″ lengths as cribbing. I was able to have my car more than 18″ off the ground and safely do a complete brake job. My one neighbor came over and made fun of my cribbing, and I told him I would trust that cribbing more than I would any jack stand. To prove it I gave the car another shake test with him watching. The car, nor the cribbing moved.
I highly urge anyone who will be getting under a vehicle to disconnect the battery as Step One. You don’t want to be reaching around potentially live wires and hot connections (think starter terminals). A strong poke is one thing, but if you happen to cause the car to lurch when raised up, you could end up in a very bad way. Please disconnect first !!
Not sure if anyone has brought this up yet. Always make sure that when using only one pair of stands to choc the wheels still on the ground. Front and rear. Seems like common sense but I witnessed a gentleman using a bumper jack with no wheel chocs. I had to stop him and say something. Don’t know if I could have lived with myself if something had happened. When all the wheels are off the ground I get some 4×4’s or other wood to put under the tire areas so that if the jacks did fail the tires would catch some wood before the ground leaving me enough room to escape.
I use a jack as a backup to the stands.
use a jack as a backup to the stands.
Always. Good point!
Kyle clearly has a preferred method of cribbing, using pieces of wood barely larger than the base of the jack stand. The pictures look like examples of how to do it wrong, but I guess it seems to work for Kyle. I must use the wrong kind of wood because my steel jack stands dig into it in an unsettling way. I prefer using the aluminum stands with a big flat base. And the matching Schwaben jack pads that sit perfectly on top.
Surprised there was no mention of using properly constructed cribbing rather than jack stands if the wheels do not need to be removed. Not the best option for quick fix jobs, but the only way I’ll do any substantial work under a car if I don’t have to remove the wheels.
I might add that, if possible, leave your floor Jack in place in addition to your Jack stands. Those few seconds of backup support might spare you from a serious injury.