6 tips for using jack stands
Working on cars requires a whole slew of relatively specialized tools. Often times we don’t even realize how unique those tools and practices are until we talk to someone new to the hobby. Or someone who is on the outside looking in. Just one example: How casually we discuss (and practice) the act of lifting our multi-thousand pound vehicles into the air and then supporting them with separate load-bearing apparatuses that allow us to work on, disassemble, or reach under the vehicles. It’s dangerous when done right, and deadly when done wrong.
That sounds scary, and to a point it should be. Being cautious when the risks are this high is not a bad thing. That’s why we created a quick list of tips for using jack stands: good for newbies, but it’s also a refresher for those experienced enough to have lifted up a vehicle many times, in many ways over the years.
Buy once, cry never
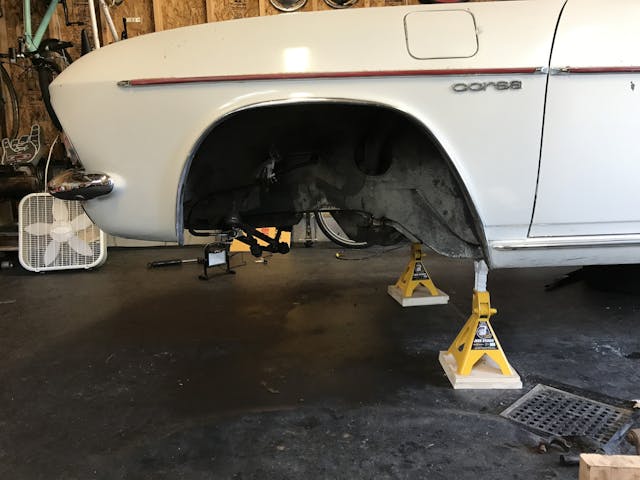
There are many factors in selecting jack stands, and price is one that many of us are forced to consider. While tools can and will be shopped based on price point, jack stands should not be one of them. These are critical safety items that should come from reputable and trustworthy sources. The Harbor Freight jack stand debacle of 2020 should be burned in our collective memory for a long time, as being crushed by your car is not the way to go. Cheaping out with jack stands is a fast track to a mere feeling of safety, rather than possessing actual safety.
Jack stands should be sturdy with a good wide base. A secondary method of locking them at the desired height is also a plus. Do not modify jack stands or otherwise compromise safety features in the name of convenience. Doing so is only making it easier to get hurt.
Size appropriately
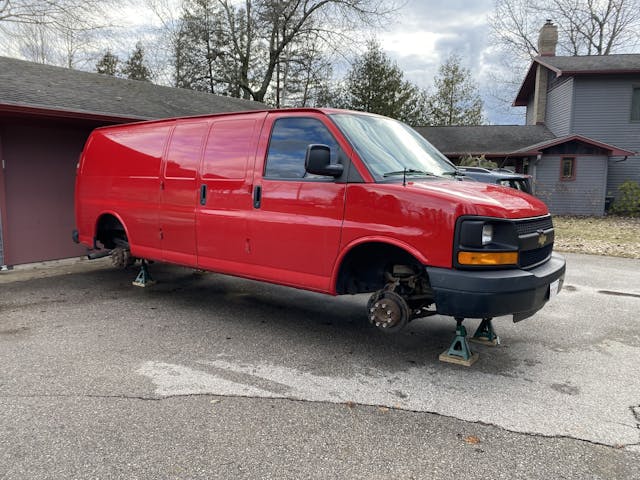
Jack stands produced after 2015 are rated as a pair. Which means if you find some at the local parts store that say they are “three-ton” jack stands, the ability to support the claimed 6000 pounds requires both stands. In reality, three-ton jack stands should be the smallest used in most home shops, as it gives a good safety margin when working on smaller cars, yet a set of four does have enough capability to hold a medium-sized truck or SUV in a pinch.
Remember that storing jack stands can be a hassle, so having one set that covers anything you’ll work on is the best way to go. That said, a small and large set of them is a nice luxury if you have the space. Inevitably something gets “stranded” on your one set of stands…and you’ll need another set shortly thereafter.
Trace the load path

Jack stand placement is as critical (if not more critical!) than proper sizing. The biggest jack stand in the world is useless if you place it in the wrong spot, letting the car fall down anyway. The service manual is the best place to look for jack points and jack stand placements. Even the owner’s manual in the glove box, a book that’s been shrinking over time and loaded with “please see dealer” language, likely still outlines the jack points for safe lifting. A quick internet search will likely reveal appropriate information too.
But sometimes that doesn’t work, or what you are doing is something the original engineer from decades past could have never imagined. That’s when a little bit of critical thinking goes a long way. Look under the car and locate a place that looks sturdy enough to place a jack stand, then follow what that is connected to. From there, imagine how it would support the load being placed on it. Supporting the rear of a car by placing stands under the rear differential makes sense because the entire weight of the car is normally supported by that part. Using a bumper or frame brace that doesn’t support and wasn’t designed for that load is a bad place to put a stand. If unsure, consult professionals.
Do the shake test

Now that your project is up in the air and supported by jack stands, there is one last step before you roll underneath: You gotta shake it. No, not the latest TikTok dance. Shake the car. Go to one of the corners and give it a good push and pull to make sure the car is stable and the stands are not going to move or shift while you are underneath. This is the same thing that mechanics in shops do when putting a car on a two post lift.
After all, now is the time to find that the ground isn’t really flat or the stands aren’t fully seated on their safety catch. Only after a good shake can you roll under the car with confidence that it will not be coming down on top of you.
Buddy system
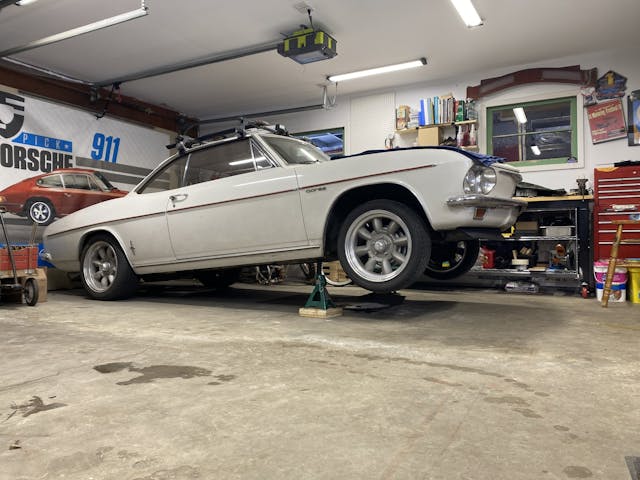
It feels strange to do when performing an innocuous task like adjusting a transmission shift cable or removing a driveshaft, but telling someone that you are working underneath a car with jack stands is a good practice. A text or call to a friend just to say “hey, I’m working on my project and am under the car for a bit” is enough of a heads up: if they don’t hear from you in awhile they know to check on your well being. Being pinned or injured under a car with no means to get help should be horrifying to you, and encourage you to whatever is necessary to prevent it.
Keeping a phone on your person is one option, as is using smart speakers or other items that require nothing more than yelling at them to activate them. I personally have a Google Home Mini above my workbench, which allows me to broadcast a message to another speaker inside my house by just yelling at it. This lets me feel safe-ish when I am working on projects while my wife is inside. (Presumably enjoying her time without me.) This practice isn’t for everyone, but it works for me. Find a system that works for you and use it.
Cribbing away that sinking feeling
Motorcyclists are familiar with the peril of asphalt: Ride somewhere on a warm day, set the bike on the kickstand, stop for a coffee, and the bike is laying on its side by the time you get back. Vandals? Inattentive drivers parking too-big SUVs? Nope. The asphalt did that.
Asphalt comes in a variety of flavors and mixtures, some of which isn’t nearly as solid as it feels under your feet. A heavy load concentrated on a small point can sink into asphalt. And the weight of that motorcycle leaning on the kickstand’s relatively small area can punch a hole into asphalt. Lo and behold, the kickstand sinks down enough that the motorcycle tilts and falls over. Bad news, but it points to a bigger problem.
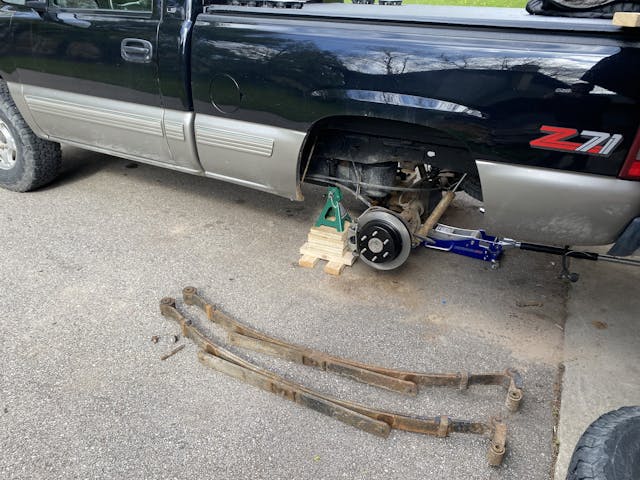
Now picture this kickstand is actually a jack stand under your project. With no warning, the car can shift as the asphalt gives way. Prevent this by using something like a chunk of wood to spread the load of the jack stand to a larger area. The same applies for any soft substrate like gravel or dirt. Cribbing is a common thing in heavy equipment transport/service, and by extension is a smart exercise to do when working on light duty vehicles as well.
Have another safety tip to add to the list? We’d love to hear it, as you can’t be too safe in these situations. So leave a comment below for everyone’s safety and well being.
***
Check out the Hagerty Media homepage so you don’t miss a single story, or better yet, bookmark it. To get our best stories delivered right to your inbox, subscribe to our newsletters.
My dad bought a home with a garage that had a grease pit. Being 16 years old at the time, I was able to make a lot of new friends. I believe there were a few Chevy and Ford transmission still down there when he sold the house.
Good information and one additional note is that your wooden base cribbing should be larger. The footprint of the square of plywood should be approximately twice the area of the base of the axle stand. $45 for a sheet of 23/32 plywood (DON’T use OSB) and a half hour with a skill saw will result in a lifetime supply of stand supports. The larger area increases surface friction when they are stacked and the axle stand won’t slip off the edge if something moves.
Be careful and use very good plywood. Roof decking plywood is not a good choice since there are empty pockets in the middle layers that could fail under the jack stand leg. I prefer to use solid wood such as hard maple over plywood. Tight grained wood is a must, cant use Oak or Pine since Oak grain will split and Pine will crush.
Agreed, that blue car in the article with multiple layers of wood looks like there is very little extra room for the jack stand placement. If the car shifts slightly for some reason one leg of the stand could easily slip off the plywood base. You’d also have to make sure the wood doesn’t get rotten or something over time & want to collapse with the weight being so close to the edge of the plywood. I cold see that possibly failing the “Shake test”.
Two questions and or points….
Not a fan of cribbing but if necessary it should exceed the footprint of the jackstand considerably in all directions to better ensure stability…..
Question….where do you place a jackstand when raising the car by jacking at a manufacturer approved jack point? In that instance you’re using the best location for the floorjack…
Particularly on a car with complete underbody cladding….
Answer….Jackpoint Jackstands;
https://jackpointjackstands.com
I’ve made platforms with strips of wood for chocks . They are made of 4x4s and 2x4s. It’s piece of mind and are great for long term use. I’m using them on a 62 Grand Prix being able to work front to back is great.
I have been teaching my grandson how to safely work on cars since I have been doing so for more than 45 years (unprofessionally). I have a 2 post lift and several sets of jack stands. EVERY time we lift a car, I make him prove to me that both the lift points and the stand points are proven to be the right location for the work. We use wheel chocks on both sides of the car, and on both sides of the tire when using a jack. He rolls his eyes at me every time. I also make him do a strong shake test when we use the lift and when we have the car on the stands. Still get the eye roll. I would NEVER allow him to use a cinder block as a lift hold, there are way too many cases where they fail. They are good to hold up the second story on your house when used in multiples, but single blocks fail. Most of the time when we use jack stands, I insist that we use 2 or leave the jack in place, but only after we released it to verify the stand holds, then lift the jack again just until it gets a small amount of load so it doesnt move if we bump it. Then again with the shake test. A thing that was missing in the article is to know how the weight of the car is going to shift when you do the work. If you are taking an engine out, then the weight shift is massive. If you are simply replacing brakes, then there is still a surprising amount of weight shift since modern wheels are heavy. when you take off both on one end of the car, along with rotors and calipers there is as real potential for an imbalance on your lift. Look online for the Chevy failures on the C8 Corvette by trained mechanics where they lifted one, took off the wheels, and it fell off the lift.
Last photo is not good practice. If you need that many blocks under the jack stand to get it high enough, get bigger stands. Don’t use stand up to their maximum height either>>get bigger stands. If blocks are needed to protect the floor or keep from sinking, better to use plywood as dimensional lumber can split along the grain. And use stands EVERY TIME you have a wheel off, even if just checking the brakes. Never rely on the jack hydraulics to not blow out.
Good article. I buy the highest rated stands I can get and still lay my wheels and tires underneath the car to catch it if something fails.
Jackpoint Jackstands are my favorite jackstands. You can jack and use stands on the same factory jack points. They’re strong yet light and very stable.
https://jackpointjackstands.com
John…very cool solution…thanks!
I’ve never seen that type before, are you able to adjust the height at all or is it just the one fixed height?
Jack stands and the jack together are how I do it (if there’s room for both). I made it a policy a long, long time ago, well before the Harbor Freight debacle, to never use anything from Harbor Freight that has to support weight.
Perhaps I’m showing my age, but the “Buy Once, Cry Never” section should have included a brief mention of the old three-legged, stamped metal jack stands once offered discount stores like K mart and Montgomery Ward. They still are around and are considered unstable and unsafe, especially if they are beginning to rust. I have a few I occasionally use as redundancy jack stands when using safe jack stands for the primary load. In truth, they should be thrown into the recycling bin and put out of circulation.
Absolutely!
I wanted to add to make sure you choose the right wood if you are using it for a base on asphalt. I’ve seen “jack base” wood split.
Excellent article!
I’ll add if you need to bring a car up high, do it in stages. Don’t lift the front end 2-3ft in the air, slap stands under it and then start lifting the rear. The odds of you sending those stands toppling sideways increases dramatically. Instead, bring them up a foot, then do the other end, then back & forth until you’re at height.
I always use stands and chocks when bringing my car up.
The one exception I have is my low profile floor jack. It has a very convenient feature. There’s a locking bar that slides through the mechanism and locks it at full height.
When I only need to work on one corner of a car at a time (example, I just swapped pads and pad sensors in my ’86 Benz), I put it under the jack pad, lift it and slide in the locking bar. With the other 3 wheels on the ground and a jack that can’t lower, I’m comfortable tackling jobs that don’t require me to actually get UNDER the car.
I have two sets of Jacks stands (different weight capacities) and use them frequently but I also throw a 6×6 under the car in case it does drop it wont completely crush me. If leaving the vehicle for any length of time, I will put 2×6 on top of the 6×6 to get it close to the jack height just in case some kid crawls under it while playing hide n seek.
“won’t completely crush me”…???? Really??? A “little” crushed is acceptable Barry???
The Harbor Freight jackstand recall is interesting because it was not a quality issue but a design issue. The teeth on the support post were small as compared to other stands. This was nice for making small adjustments but didn’t give a lot of grip for the ratchet mechanism. My new stands have large ratchet teeth and a locking bar.
I have a flat and level driveway made from asphalt millings. I always put a 12″ square piece of 3/4 plywood under each stand.