6 storage tips to optimize your garage space
Garages are multipurpose spaces, even if you don’t use yours primarily for DIY projects. There are things to store, some of which will be in storage forever and others that need to be readily accessed. Large swaths of floorspace must be clear or, at least, able to be made so on short notice. And we haven’t even gotten to the vehicles themselves.
Whether you run a full restoration shop or simply park your vintage ride inside day-to-day, these six storage tips will make your life easier.
Bin it
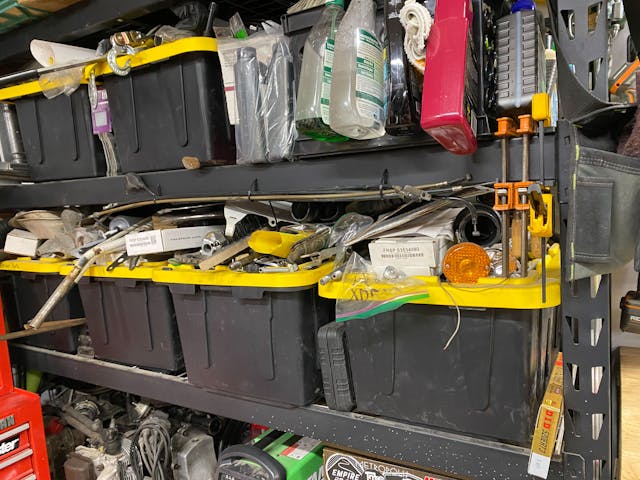
Garages are dirty places. Their large doors regularly admit dust and dirt, and these conspire to make everything inside a little more gross than the last time you touched it. Car parts are also vulnerable to sun and ozone exposure. Rubber ages much quicker when kept a room that has sun beaming in through a window plus a fridge, freezer, or compressor running in the corner. Ozone causes dry rot in tires and can harden spare rubber seals or gaskets to the point that they are unusable.
Keep degradation at bay by utilizing storage bins or containers to close things off from the sun and minimize ozone exposure.
Now actually bin it
You’ve decided to put everything in careful storage. Now it’s time to cull the parts stash and keep only the things that you need, recycling or selling everything else. Yours truly needs to hear this one, too: I have at least three pairs of “spare” cylinder heads for my Corvair, despite the fact I have no plans to rebuild that engine, and the heads that are in the car will be good for a long time. I should sell those.
As you do inventory, make sure your spares are actually worth keeping. At least once, I’ve dug into my stash only to find that what I thought was a solid spare was actually junk. That afternoon quickly turned frustrating, as I left the garage to go inside and start scrolling eBay.
Keep it together
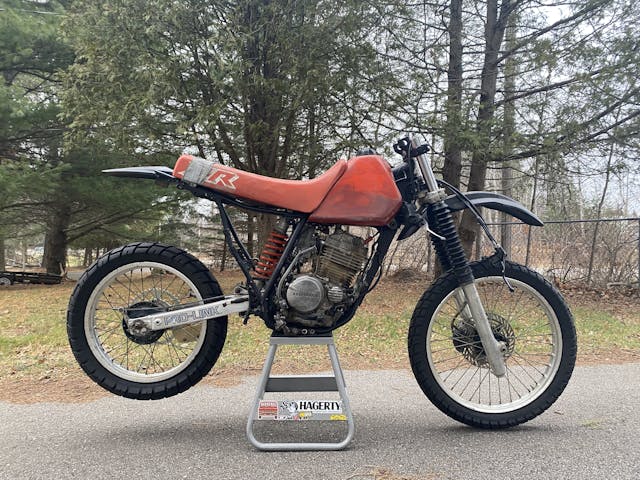
The easiest way to store a complicated arrangement of small parts is when those parts are assembled.
A friend of mine took a flathead V-8 Ford apart a few years ago as a winter project. For one reason or another, he got derailed. Before long, Ford engine bits became dirty, lost, or, at best, disorganized and scattered across his garage.
Once he decided to back-burner that rebuild, it would have been best to loosely re-assemble the V-8. That way, he could relocate it easily and store it as one large chunk of components. I’ve used this approach with a few transmissions and engines. Another upside? When you store the temporarily assembled project, you can write a tag recording what it needs and what you found when you began to tear it down.
Label, label, label
Speaking of tagging, have I hammered home the point that you should be labeling everything? Labeling things removes the index from your brain and frees up mental space for things that actually matter.
Wheels … all the wheels
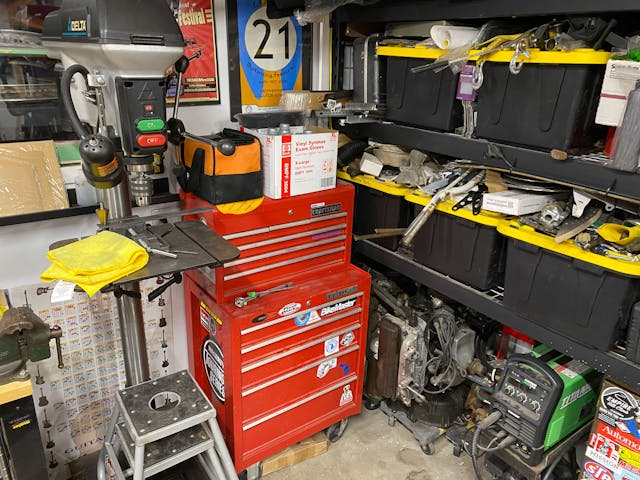
Have a heavy thing? Put it on wheels. Awkward-sized thing? Wheels. Tool chest? Wheels. Workbench? Most of the time, believe it or not, wheels.
It’s hard to overstate how nice it is to be able to rearrange your shop on a moment’s notice without breaking a sweat. Even better is the ability to “bury” things behind other things. For instance, in my shop I have few engines sitting under a shelf. I might pilfer one of the engines for a part once or twice a year. Usually, those engines are tucked into the corner, blocked by my drill press and a toolbox. Luckily, both the press and the toolbox are on wheels, so each is easily rolled away whenever I need to access the engines.
Combine functions if you can
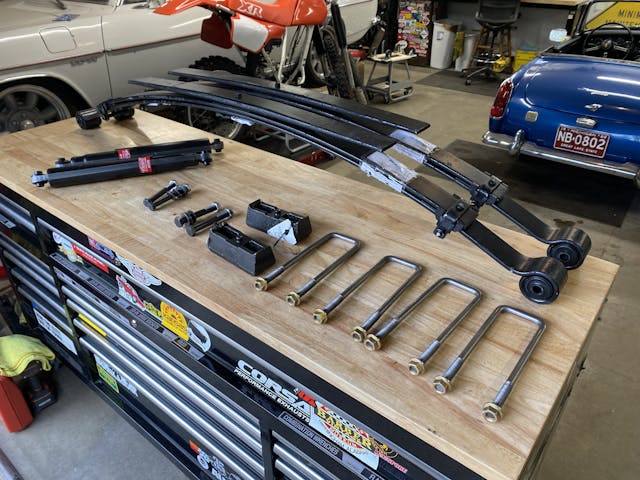
One of my favorite things in my personal shop is my 6-foot rolling toolbox. Sure, it has drawers aplenty, but most importantly, it has a worktop. This makes it the best of all workstations.
Not all dual-purpose tools work as nicely. Often, you’ll have to compromise. For example, the workbench on top of this tool chest is too thin for me to mount a vise to it. If this were my only workbench, that would be quite the challenge. The best advice is to think through all the pros and cons before putting big money into multipurpose shop equipment.
Check out the Hagerty Media homepage so you don’t miss a single story, or better yet, bookmark it.
An additional word or two on wheels: Many rolling cabinets have only two swiveling casters (lookin’ at you Harbor Freight). This forces one to drive it like a wheel barrow which is antithetical to effectively navigating cramped quarters. Replace those non-swiveling casters with swiveling casters and avoid the wheel barrow effect. Imagine being able to shove a big tool box or table into a just big enough space without having to move anything else. This is why a movers dolly will swivel at all four corners. BTW, you should have a bunch of movers dollys for those things that don’t come with their own wheels.
Bins for the win!
There are four categories… tools, generic parts (nuts, bolts, rivets etc.), consumables (oil, solvents, paint, fillers etc.) and parts both old and new. I see too many guys with parts in their tool boxes and various containers full of various bits and pieces. Kind of causes a waste of time when you are looking for stuff… The best advice I ever got and continue to give is “one project at a time”. There is nothing worse than mixing up parts from your ’59 and ’63 Corvettes! If you have tons of room and can segment everything, yeah go ahead. Most of us don’t have that luxury. Its also more rewarding to finish one two year project than looking at 2, 2 year projects not done after four years!
“Once he decided to back-burner that rebuild, it would have been best to loosely re-assemble the V-8…”
I don’t disagree, but in my experience there’s often no clear decision point to “back burner” a project. Other things keep taking priority, day by month by year. I have (sort of) learned to make some record or template of how things go together, and bag or container parts so that when the project inevitably drags on into months, I have some hope of reassembling at the end.
To Hyperv6. The garage I built is 30 x 36. I wanted 30 x 42 but my wife decide it would restrict our view behind the house. Anyway, I manage the space I have. An apartment building nearby was replacing cupboards in each apartment and was glad to get rid of the old ones. I took what I wanted and now I have storage galore. Nice and neat with everything hidden – nuts bolts, screws etc, light engine parts, lube,
electrical stuff, paint, power tools, things like that. It’s kinda like my man cave with a 48” tv, radio, small beer fridge, work bench and stools for me and any visitors. It’s well insulated so a small electric heater works fine.
I keep my boat alongside my 74 Grand Prix and other toys in there with room to work on the bench if I need to.
Livin’ the dream.
Build it and it will be filled!!!!
I just acquire more garages or build-on….so many toys and stuff. Problem solved!
You left out the basic rule: A place for everything and everything in its place. I have a hard time practicing this it seems, but it is very important to put everything back at the end of the day — or the session, be it a morning or whatever. If you don’t do this, you accumulate clutter and you don’t know where anything is after awhile. I worked in a shop in Ireland for awhile that specialized in Triumph Stags and Jags, and the owner, now my lifetime friend, drilled this into me. And sweep the floor before you leave! I didn’t even know how to use a push broom properly when I started with him. (Bang it on the floor after each stroke to knock the clingy junk out of it.)
I bought a Husky brand doublestack rolling toolchest, and made magnetic dry erase labels to match my needs, has been a great ‘tool’ for me to stay a bit more organized.
Cover the walls in pegboard and hang your hand tools on it. This allows you to find that wrench or other item you need at a glance and prevents you ordering duplicate tools on your next trip to Harbor Freight when you’ve forgotten that you already had three of the item in question stuck in the back of a drawer somewhere.
I got serious about labeling bins after watching an episode of Stacey David’s “Gearz” when he talked about sorting through an unfinished car project for a recently widowed woman. I figure if it fits in a tote, I don’t need an Excel sheet, but my wife or kids can pretty easily grab the tote of parts for each car if they need to sell it.
95% or what is in the garage is on wheels. I use 5-drawer horizontal filing cabinets and storage for tools, parts, and materials. The cabinets have a pair of HF moving dollies underneath- the dollies are cheaper than buying just casters and the cabinets would need a heavier plate added to the bottom to support the casters anyway.
We had to put a new roof on the garage this summer and we had the entire two car garage/shop emptied in less than two hours. It took as much time to take all the pegboard stuff down as it did to move all the equipment. And if something doesn’t fit in the garage, I can bring the tools to the project pretty easily.
Wow! Some good advice here, and timely. I have no garage at my house but plan to build one soon on the 2.5 wooded acres directly across the street. It needs to house my F150, Daimler V250, and 2 1970s era replicas (1901 curved dash Olds, and a Model T). Also must have a small apartment overhead (think guest room) and an 8×10 climate controlled storage room. Probably a work/storage lift and a high overhanging attached outside roof for boat and RV work. I’m thinking 32 x 32 or 30 x 40, but cannot wrap my head around a design. Any pointers on garage planning?
Oh, I’m in a flood zone and will get as much as 2 or 3 feet of water if a hurricane blows up the west coast of Florida.
5S is a good system for a clean shop
“SORT” “SHINE” “SET IN PLACE” “STANDARDIZE” “SUSTAIN”
The hardest of the bunch is sustain, we all clean up but how often and how many times do we let things go back to the way it was before we started. Everything has a place so put everything in its place, handle it once:-) easier said then done!
My brother-in-law’s quote, so I’m stealing: “nature abhors a vacuum”.
So true. As much as I try to fight that fact! Ha!
Helpful advice and ideas like these would be enhanced significantly if Hagerty.com included a way for us to post pictures. I put up 13 panels of pegboard in my garage and hang a LOT of things on it. Tool boxes eat up valuable floor space – best to be avoided. I bought a steel cabinet for power tools, etc. I made two vertical heavy duty bins from 4 X 4s, 2 X4s and 3/4 ply to store heavy spare parts (cylinder heads, starters, water pumps, bearings, intake manifolds, alternators – even blocks and transmissions). Floored the garage attic and store lighter parts up there that can take heat. Hung the original hood from my 1979 Corvette upside down from the ceiling on chains. Never going to use that hood again and should sell it. But it’s an interesting decoration. It’s not in the way and it’s value keeps going up.