5 Torque Wrench Myths, Tested
Of all the tools in an entry-level DIY toolbox, the torque wrench is the most accurate and the most powerful. Should a torque wrench not do its job, your car could potentially fall apart; alternatively, it might never come back apart without a lot of force. We own a torque wrench so we can have confidence that our projects are assembled correctly. Since a torque wrench is so ubiquitous and important, there is a lot of passionate discussion about the proper care and feeding of this tool—and a lot of the talk is garbage.
There are seemingly endless myths about how a torque wrench works, how it is best used, and how it should be maintained. Some “rules” seem rooted in a deep desire to maximize the accuracy of the tool and minimize potential damage to it. Others simply reflect a misunderstanding of how the wrench works. We know this because Torque Test Channel on YouTube recently grabbed a few torque wrenches and set up a dynamometer to separate fact from fiction.
Torque Wrench Myth #1: A Smooth Swing Matters
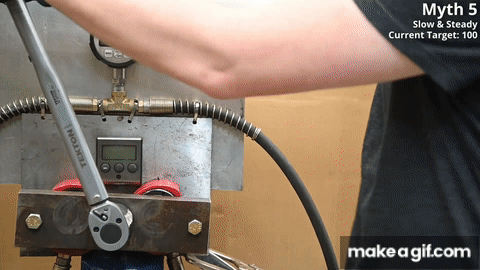
In the garage, many activities reward a smooth application of force. When using a torque wrench to put the final tension on a bolt, you are looking for an accurate measurement, and those rarely come with herky-jerky movements. Torque Channel‘s tests reveal that a long, smooth pull does seem to be the way to go, though the rule has its exceptions: While electronic torque wrenches demand a more regimented process, click-type torque wrenches can account for a fair amount of misuse.
Verdict: In general, a smooth swing does matter if your goal is accuracy—and, of course, it is. Otherwise, you’d be using a breaker bar.
Torque Wrench Myth #2: Always Double-Click

A long, smooth pull to final tension, and you let off the pressure. Why not give it a quick check to make sure? A double-click can’t add that much more torque.
The dynamometer tells us that, with a bolt at 100 foot-pounds, that additional click is worth about 1 additional foot-pound. Is that amount likely to make or break a project? Probably not, since a single foot-pound is within the accuracy range of the tool itself.
Takeaway: Since extra clicks can add up, the effect of a confirmation click is something to be aware of, but it is likely not a big deal.
Torque Wrench Myth #3: Recalibrate After Dropping

Use does not have to be synonymous with abuse when it comes to tools. Yes, tools wear out even when used as intended, but how delicate are torque wrenches, really? Torque Channel confirms that a brand-new wrench is working as advertised before subjecting it to a handful of “drops.” Then, the wrench’s calibration was checked—it was unaffected. The wrench was then submitted to additional abuse that honestly made me cringe a little. I’m sure someone has used a torque wrench as a makeshift hammer, but I doubt that person is concerned with the accuracy of the wrench if that is the kind of hackery they engage in.
The wrench was unaffected even by blatant abuse. Of course, this was a click-type wrench, the kind that tends to be more durable. (I would expect a digital wrench to be more fragile.)
Takeaway: If you drop your wrench, and you don’t trust it, there is no reason not to put your mind at ease and recalibrate—just know you probably don’t have to.
Torque Wrench Myth #4: The Warm-Up Period
This one was new to me. Some torque-wrench users use a torque wrench on something like a lug nut or socket clamped in a vise before they use it on the specific item to be final-torqued. The theory appears to be that you should confirm the mechanism is free and working properly, so you aren’t feeling for a click that never happens.
The benefit of this practice turns out to be peace of mind. All the wrenches tested on the dyno, and even those tested on a calibration rig, show that the change between the first and the 10th clicks is well within the tested spec of the wrench.
Takeaway: Not required, but I won’t judge if you keep doing this.
Torque Wrench Myth #5: Store It Slacked

Click-type torque wrenches are pretty simple at the core, with a spring and mechanism that shifts with a certain level of force. That spring is the key to calibration, so keeping it under tension has to be bad for the tool, right? Well, yes. Torque Channel examined a handful of wrenches of various sizes and sources that had been left set and under tension—for many years—and found that they all read slightly off. None, however, were off by a dangerous amount.
Takeaway: Best practice is to remove the tension, but don’t panic if you aren’t already doing it, or if you forget.
Torque Wrench Myth #6: Digital Torque Adapters Are Suitable Replacements

One of the gripes I have with torque wrenches is that I need at least four, and I am really not that far up the food chain, as far as DIY mechanics go. Given the funds I have tied up in my torque wrenches, it is easy to look down on the relatively affordable digital torque adapters. These can be attached to the end of a breaker bar or ratchet and use a transducer and display to show the torque input to the bolt.
Since digital adapters tended to be significantly cheaper than wrenches from known brands, it was only logical to discount their performance. Turns out, I was wrong. On the bolt dyno a $40 digital adapter performed similarly to a dedicated torque wrench. The former is especially helpful with a torque-to-yield bolt that requires both a torque spec and additional tightening by a certain number of degrees. The adapter used in this test was also good enough that it could be used to calibrate most home-use torque wrenches or, at least, confirm they are still working as expected.
Takeaway: True!
So maybe torque wrenches are a bit misunderstood. Hopefully Torque Test Channel put a few of your minds at ease. It also tests a few more myths than discussed here, so be sure to check out the full video if you want to see more fun torque-wrench testing.
***
Check out the Hagerty Media homepage so you don’t miss a single story, or better yet, bookmark it. To get our best stories delivered right to your inbox, subscribe to our newsletters.
My clicker that I splurged on some 40 years ago came with instructions that said to store it slack, and cycle it a few times before each use to circulate lubricant, so the myths are at least that old….TTC is a great channel for its unbiased testing and witty commentary. But Kyle: you are quite high on the DIY food chain. How many of us have knurled valve guides in our home shop?!?
Now I get it. If I post quickly and often enough, I no longer get the “you are posting too quickly” error.
I have a couple of beam torque wrenches and one clicker.
I “trust” the beam ones more, as you can tell by the reading if you are approaching the goal.
Also, maybe it is just me over thinking things, but I like to divide the torque by first tightening all the bolts on the assembly to 1/2 the goal, and then do them again to 3/4 goal and finally go the to the goal.
That’s the way I was taught – progressively / incrementally torque and follow a pattern to evenly distribute the force, ensure proper alignment and sealing, and keep from distorting the part. This is particularly important in light alloy parts with a lot of fasteners.
Common sense is important, too. A lot of factors can affect what the torque value should be, such as type and condition of threads, lubricated vs dry, material of the fastener, material of the parts involved, thermal factors, etc. Typically, if it doesn’t feel right, it isn’t. One of the older aircraft mechanics that I worked with used to refer to his “German torque wrench”, aka “Make it Gutentight.” Same guy also swore by his beam-type torque wrenches. He’d also dead-weight test his from time to time. Not totally precise, but fundamentally accurate. I haven’t calibrated / verified any of mine in a while – one of my employers had some nice Snap On wrench checking stations that we could use. We’d check the torque wrench or driver at several points in its range.
Also use the right size tool for the job and understand the tolerance limits for the tool. If it’s a 100 ft-lb torque wrench and it’s accurate to +/- 4% of full scale, that could mean 16 to 24 lb-ft on a fastener calling for a nominal 20 ft-lbs – big difference. Using a torque wrench with a 30 lb-ft range would be more appropriate.
Any tire shop worth its salt will use the progressive method described above (1/2, 3/4, full), PLUS they will ask you to drive around for a day or two, then stop back in for a re-torque of all the lugs. I thought that was overkill until the shop owner showed me a handful of “industry” photos on his computer of incidents where the techs had shortcut the practice.
In an area I couldn’t get my torque wrench into, carburetor base nuts, I used a box wrench, measured the length which was 9″ then divided 12″ x 9″ which came out to 1.33. With the recommended torque of 17 ft/lbs I multiplied 17 x 1.33 and used an accurate postal scale to pull of 22.6 lbs. at a right angle to the wrench.
I wholeheartedly disagree with the concept that the digital devices are perhaps fragile. From a 23 year career of being responsible for the calibration of the devices I ended up with a large collection of CDI digital devices from ounce-inches (& less) to 1000 ft-lb being used with a 3200 ft-lb Proto H6332 multiplier (& higher actually, but that’s the one I brought shear pins for).
The reason I standardized on those digital devices was that they simply worked and quite precisely with far greater reliability that any other style.
I concede that a Harbor Freight torque tool is a pretty impressive device for the price. And I will certainly use it for lug nuts. I do wish I could read the chrome on chrome divisions a bit more readily, but that’s just old eyes.
The device that is being pictured for calibration is by itself using digital technology. I just wonder if the general rule of checking a calibration of any device with another device of ten times greater accuracy is being followed with this article.