5 bits of race-car flair to elevate any engine bay
There is something about the prioritization of function over form in the engine compartments of most race cars that turns the spaces into art. Any detail-loving person can appreciate them, but especially DIY and at-home mechanics: These engine bays are often the antithesis of what we usually get to work on. Race machines are built with service in mind, and that focus removes a lot of frustration for the mechanic. (If you’ve ever broken a dozen plastic clips opening the access panel to do an oil change, you know what I mean.)
In the engine bays of race cars, function becomes attractive. With that in mind, I took a look at a few projects around my garage and found some cool bits of flair that give off just the right motorsports-inspired look.
Tidy organization
Engine compartments can be busy, with hoses and cables going this way and that for various pumps and control modules. In race cars, engine bays are laid out system-by-system, and this arrangement lends itself to a more thoughtful installation that maximizes function while minimizing space. In short, the engine bay is all tidied up.
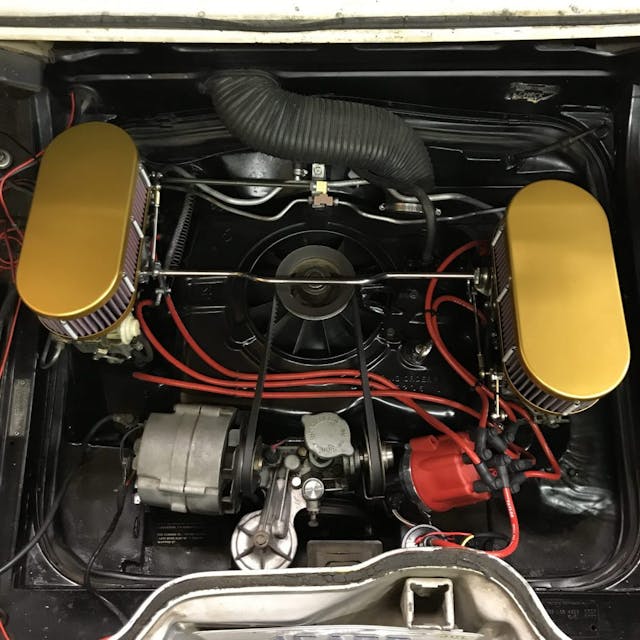
Organizing your car’s engine bay, whether or not it’s a race car, can be as simple as bundling wires into a proper loom or shortening unnecessarily long hoses. For my Corvair, tidying up meant removing the mechanical fuel pump and re-routing the fuel lines to remove clutter on top of the engine. This required very minimal fabrication: Though the four carbs might appear complex, they are mirrored side to side, allowing me to flip the stock fuel lines. Everything fits like it would from the Chevrolet factory, and I only had to put two 90-degree bends in a $10 generic steel pre-flared fuel line.
Safety wire
Since safety wire is the last step in any project—and one I am excited to do these days—just the presence of wire in the right place means a checkmark on my checklist. No need to rack my memory: If there’s no wire, the component is not ready —and I need to figure out why I left the job unfinished.
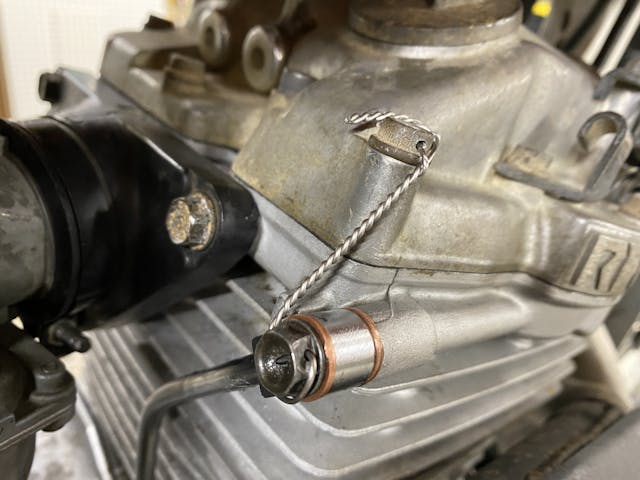
Science says a properly tensioned bolt will rarely loosen, but some positive retention of critical fasteners provides a warm security blanket to the mind of a detail-oriented gearhead: You know that piece of hardware is not going anywhere unless you let it. Safety wires entered my life when I first decided to try road racing and I’ve been breaking 1/16-inch drill bits putting them all kinds of places ever since.
With some attention to detail, the final product will be jewelry for your engine. Be sure to properly dress the cut ends, or your engine bay will hide a bunch of razor-sharp needles waiting to rip your hands open.
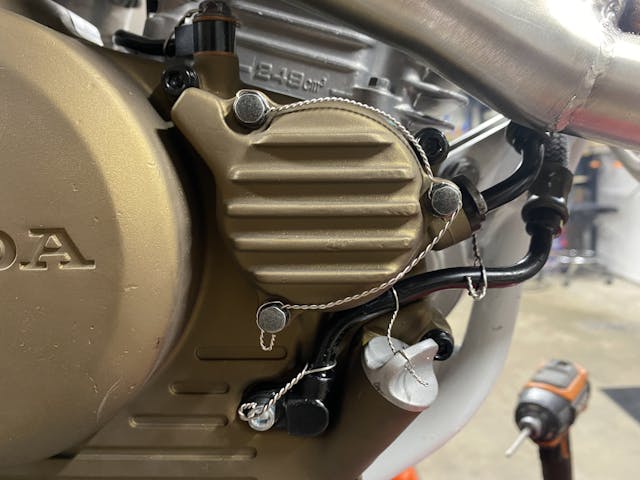
Labels or the lack thereof
For sponsored racers, brand names and logos matter. For the rest of us, they usually don’t, unless we are just bragging at the cruise-in. Between brand names and small labels identifying parts or need-to-know specifications, a race-engine bay can look either very cluttered or totally bare, devoid of any marketing whatsoever. Pick one look and try it out. Writing valve-lash specs on the valve covers or labeling fuel and oil lines all but guarantees correct assembly in any situation. They can be fun touches, too, especially if you enjoy silly easter eggs, like writing the solid-lifter valve adjustment specs on the valve covers that hide your hydraulic roller valvetrain. Posing? Yes, but also a harmless joke.
Breathers
Engines are all about airflow, and not just through the intake and exhaust. As the linear motion of the pistons is transferred into rotational motion by the crankshaft, pressure often builds inside the crankcase—pressure that is best relieved. Setting up appropriate breathers and ventilation can be easy and, if well thought-out, can still include modern crankcase-ventilation one-way valves.
Add some color

A little color contrast never hurt anything, and nothing makes a black-and-silver engine bay pop quite like a little gold—or whatever color you like. So many little details can be color-coded to make them disappear or become a feature. Valve covers and air cleaners are easy, but even hose ends, bits of wiring organization, and linkages can be snazzed up with subtle pops of color to really “bring the room together.” Be careful here though, as the look can get real gaudy real quick.
And just like that, you have an engine bay that is uniquely yours with a little race-car style mixed in—whether you need it or not.
***
Check out the Hagerty Media homepage so you don’t miss a single story, or better yet, bookmark it. To get our best stories delivered right to your inbox, subscribe to our newsletters.
I am not a fan of brands putting huge logos/graphics etc on their parts. I wish in those cases we at least had the option of neutral colors and low key branding so the parts fit within the environment we’ve created.
How did you beat hyperv6 to the first comment???????
Not engine related, but I’ve always thought that Hidden Hitch would be much closer to being hidden if it didn’t say HIDDEN HITCH in large white letters (on a black background).
Okay, this is something I had maybe noticed previously but will now bother me forever. Thanks for that.
I would leave the labels. The day that the plug gap or belt routing may come in handy.
Not only get things in place but leave the fluorescent convoluted tubing off. It is a fire hazard and just bad taste.
It is fine to use colors like red wires and stainless fasteners to bring some color to a drab compartment.
Finally just keep it race car clean. Most cars before a race is like new in presentation.
“Tidy Cables”…
My ex-wife once decided that the spark-plug cables in her car “looked messy”.
She re-routed them to look better, and discovered that the car wouldn’t start.
“Say Goodnight, Gracie.”
😂🤣😂🤣😆
Wow! My wife won’t even open the hood of her car, much less touch anything 😂
LMAO!!!
Your lock wire pattern should be reviewed on the round Honda cover at the 11 o’clock bolt, this is not secured as it is and also think of putting “spaghetti” plastic tubing on stainless steel wire close to a light alloy cover to avoid rubbing wear. Just a friendly advice from an aviation engineer !
Curious on the 11 o’clock bolt – I don’t see how it could come loose?
It will not. Splitting hairs a bit. Tubing where permitted is not a bad idea. Careful with your tie wraps though, they can and will cut through metal tubing. Ask me how I know.
Hey Claude, I take it you are not in the USA. A&P’s don’t get the “Engineer” designation here. In fact, until 30 or 40 years ago, we were classified as unskilled labor. I think now we have moved up to semi-skilled.
“Safety wire”?
I’m not sure why but the very thought of drilling 1/16” holes in all my critical bolt heads and inserting wires made the back of my brain hurt and it won’t go away……..
But seriously though, sometimes just doing a major CLEAN of the engine and engine bay does wonders!
Dad (not a car guy) used to wipe the valve covers and other sheet metal with a kerosene rag after each car wash. They were always clean and shiny.
On cars that I have bought new, after a car wash I take my wet towels and wipe everything I can touch under the hood. It goes a long long way keeping everything clean. Older cars it is a bit more messy.
After 40 years of being a commercial aircraft mechanic one of the things I know is safety wire. Safety wire your signature. Any mechanic who dives in to a job sees the safety wire job from the last guy. Some of those picture would be viewed as a hack job. What really stood out was loose pigtails and wire terminated around tubing. No Thank you. Not even on a car.
I learned how to safety wire from a US Air Force mechanic who had worked on 36 cylinder radial engines. 72 spark plugs all safety wired. He was pretty fast at it, and they always looked great. I never got that fast at it but mine do look pretty.
Where’s the STP sticker?
👍 The racers edge!
On the rear window where it belongs!
Agree with the above comments about “safety wire”, though the preferred term is “lock wire”. It will not prevent the bolt from coming loose, but will prevent it from falling out. Yes, please loop the free end back on itself so it doesn’t tear a hole in the top of your hand when you reach for something nearby.
So glad you didn’t add braided stainless hose all over the engine bay. That stuff just adds weight and acts like a hacksaw to anything it touches. Plus, there will always be one broken wire strand that finds its way into your hand or arm when you reach in…..
I did it all the time in the Air Force. Done properly, the bolt won’t turn to loosen. They are to be wired in the tightening direction, so any vibration will only allow loosening to the extent that the wire has slack. Part B: Why on a car engine?
Regarding Part B:
It’s required by many racing bodies for any drain hole. I see lots of aircraft guys talking about how to do it properly, and I don’t disagree with the observations, but the purpose in car racing applications is not to secure critical torques, but just to stop a drain port from opening up and dousing the track with oil.
That being the case, and being on the most frequently serviced fasteners, being easy & convenient usually wins out over being done “right”, so long as it prevents the plug from falling out of its hole.
If you talk to any aircraft mechanic, particularly military, it is called safety wire. And, if done properly, it will definitely keep a bolt from loosening. Got pretty damn good at it working on F-4’s during Viet Nam knowing it was subject to be checked by a QC inspector assuming they weren’t looking over your shoulder in the first place.
I’m guessing your military service branch was the U.S. Navy as was mine. 20 years as an Aviation Structural Mechanic from 1952 to 1972. My last command was as Aviation Maintenance Control Chief in VF-11 aboard the USS Forrestal flying F-4 B Phantom fighter jets. All we ever called it was safety wire even after I retired and worked in civilian aviation as support for the Army Aviation Reserve Unit flying the C23B. The sole purpose of a safety wire application was to keep bolts/fasteners from vibrating loose and causing a catastrophic failure and possible loss of an aircraft. I can agree with safety wire application on any and all fittings and drain plugs in the racing community where such loss could contribute to an unnecessary accident on the racetrack. Otherwise, it would be a waste of my time and effort, except in very special usage such as off-road racing or cross-country back woods driving. As for the quality of the workmanship in the article? As they say: “Don’t give up your day job”
Sure way to make any engine compartment look good is first to give it a real cleaning. The next is simply wax all painted surfaces (not matte ones or semi-gloss) then a bit of spray paint touch up and last add the fancy air cleaner or similar. Key is to keep it simple so that there is not a lot of things fighting for attention- the engine should be the center of attention so goofy stuff should be avoided
Is that a Lebowski joke at the end there?
I always use a #41 drill for safety wire. Easier than 1/16.
Interesting. I’ll have to source a couple. Once I switched to jobber bits and decent drill press everything got significantly easier. Hand drilling was a fools errand.
On the pic showing the 3 bolt cap on the Honda, the safety wire on the upper bolt would apply pressure in the counterclockwise direction, so unless that bolt has a left hand thread the wire should be repositioned so the twisted section is close to the uppermost hole. (Says your friendly aircraft inspector, pending his sign-off). Otherwise the safety wiring is very pretty:-)
Lol, I caught that too. Retired A&P.
Duly noted! Anytime a fellow racer complains about safety wire I just laugh having seen what you A&P folks have to deal with. We have it easy. There is some serious art to what you do!
I’ll add a nice helping of Adel clamps where needed to help keep hose/line routing neat and away from sharp edges and other undesired surfaces, along with judiciously applied T&B Ty-Raps (black only, please) to help keep routings neat. The small T&Bs can also be used to make really nice-looking spark plug separators.
Also – some extra pieces of split hose/tubing where needed (usually attached with T&B’s, of course) over hoses/lines as required where there might be chafing or rubbing.
Spend time prepping an off road racing vehicle with real pro and you’ll learn a lot of tricks that will serve you well in your vehicle prep endeavors.
The golden carb covers look good on the corvair.