4 Levels of Hardware Retention
Our beloved vehicles are massive assemblies of parts. Some of those parts are superfluous to the critical function of a car, so if they fell off we might get a bit of a chuckle at the situation. Other parts we want to stay tightened and torqued exactly how we set them, and that means some form of retention on all those nuts and bolts is imperative, lest our wheeled machines quite literally lose their wheels. Amazingly, this is all less complicated than you think.
Threaded hardware is all about friction. The threads are little more than long spiraling incline planes that wedge against one another, and the friction of the two surfaces is too great for the hardware to turn without outside assistance. Vibration and heat conspire against the smooth bond though, as differing materials could potentially expand at different rates and reduce or spike the load on the threads, allowing things to rotate even fractional amounts. Small, unnoticeable changes over time compound into catastrophic failures. Ever seen a loose wheel and tire rolling down the freeway? Terrifying. A drainplug that falls out and turns and engine into scrap metal? Nightmare fuel.
So how do our cars not fall apart? Well, it boils down to just a few types of retention. Here are the key ones:
Torque Spec
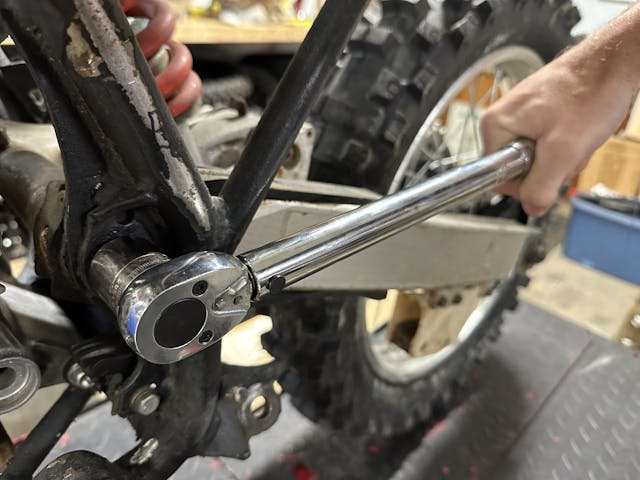
A proper torque specification uses the threads to stretch the hardware enough that it will not lose tension during its intended use. For a lot of common hardware, the torque spec is fairly low, enough to be done by hand with relatively small tools. Just the stretch of the hardware can be enough to keep things clamped tight for a long time.
The perfect example is torque-to-yield bolts that are tightened by degrees of rotation rather than torque. This more accurately sets the clamping load of the hardware, and with the proper number of threads it takes a lot of force to break those back loose. If you need more than that, start looking at . . .
Chemicals
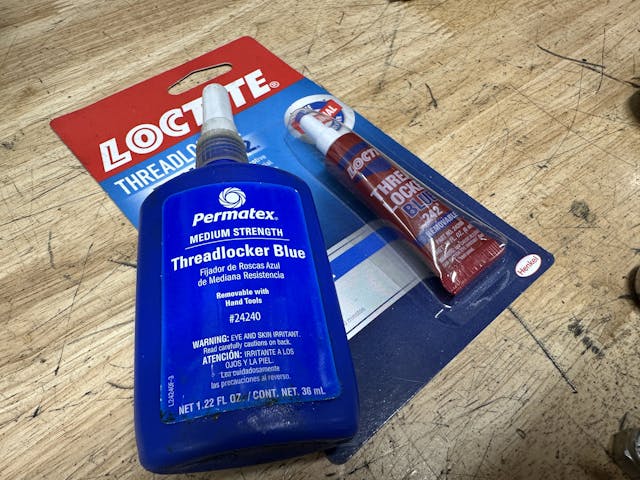
Fresh and clean assemblies might need just a little help to ensure everything stays tight, and one of the easy and cost-effective ways to do that is with liquid threadlocker chemicals. These are typically anaerobic-curing adhesives that essentially glue together a portion of the threads as they are final-assembled. The anaerobic part just means the formula cures without the need for oxygen, a good thing consider how tight the tolerance is on threaded hardware.
But threadlockers have limitations, like cure times and cleanliness standards, along with no visual indicator that it was actually applied—unless the installer makes a note. This can lead to frustration if higher-strength threadlocker is used in an area where it cannot easily be heated to help break its bond.
Additional Friction
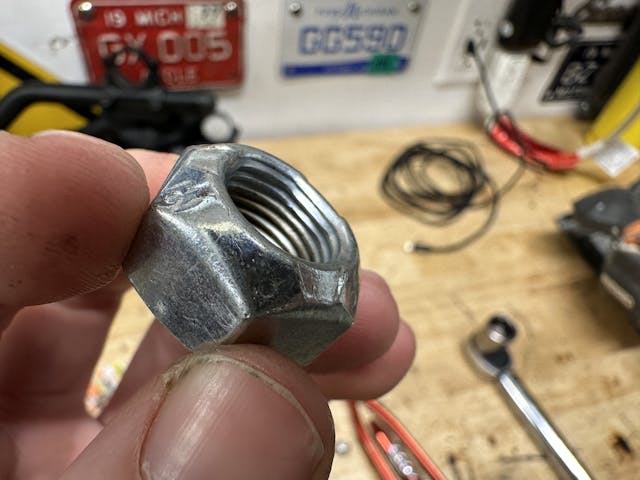
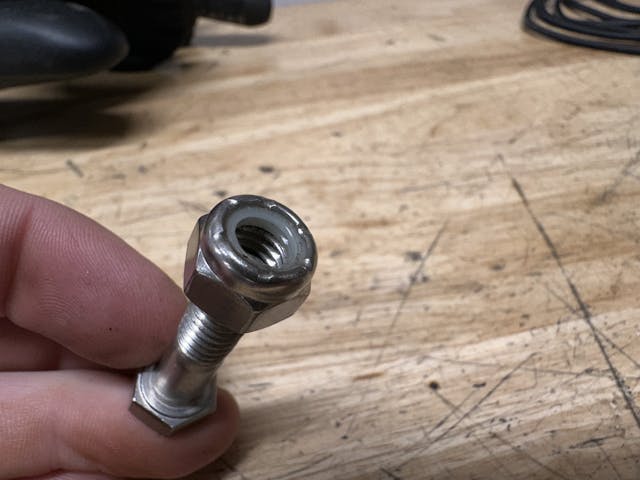
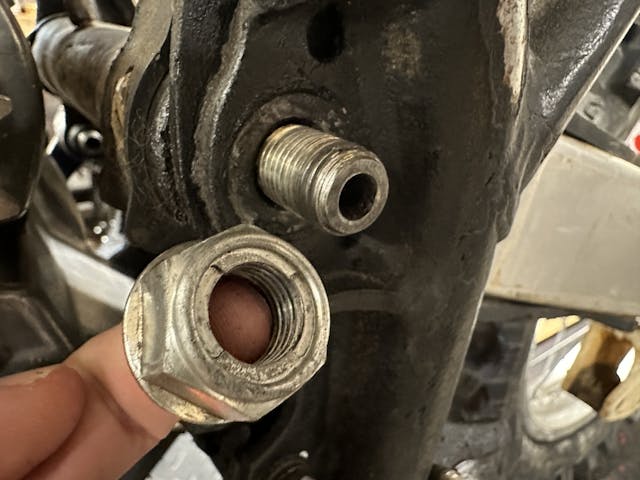
The threads might be one source of friction, but they don’t have to be the only source. Adding an additional feature or piece to the hardware that increases the amount of torque required to turn a fastener can be a solution when more clamping force is not needed but additional turning resistance is.
Two popular options for this are nylon-insert locknuts (aka nylock or nyloc) or metal washers, which are added to the back side of a nut to provide additional friction when the final tightening of the hardware is done. The nylon option does require temperature consideration in the final install. Nylock-style nuts are not the solution to header flanges that always loosen, as the nylon would be cooked off and gone after the first heat cycle.
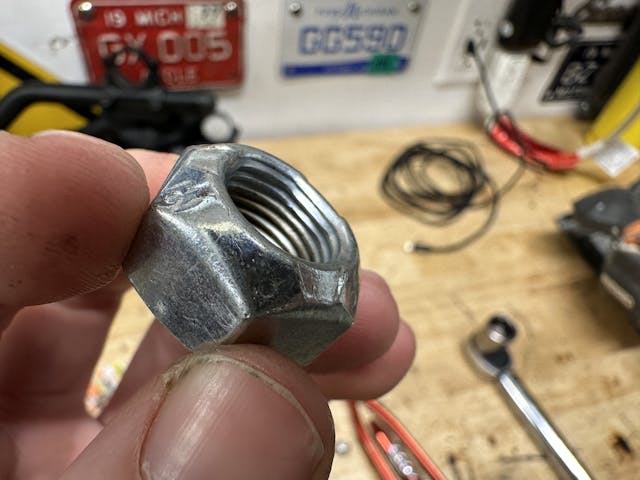
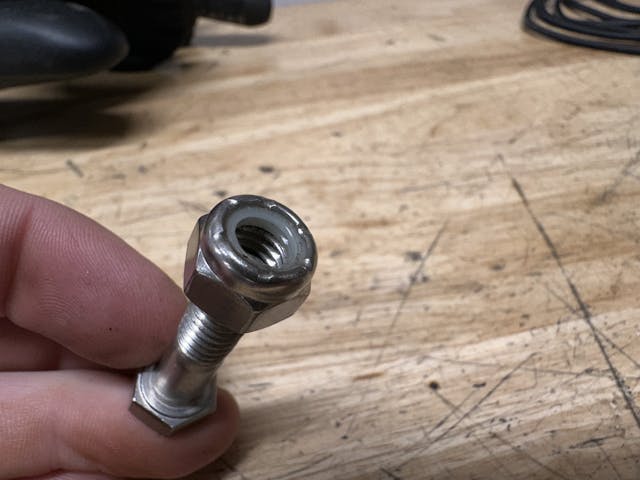
For something like that, it might be better to use a metal waster that deforms rather than the nylon. Another option for this is to have the final few threads of a nut be deformed just slightly. When using this type of hardware it should be factored into the final torque setting, if applicable, and most deforming hardware has limited ability for reuse, as each use lowers the performance of the specific part you are using it for. So if you need retention and serviceability, maybe it’s time to think about . . .
Positive Retention
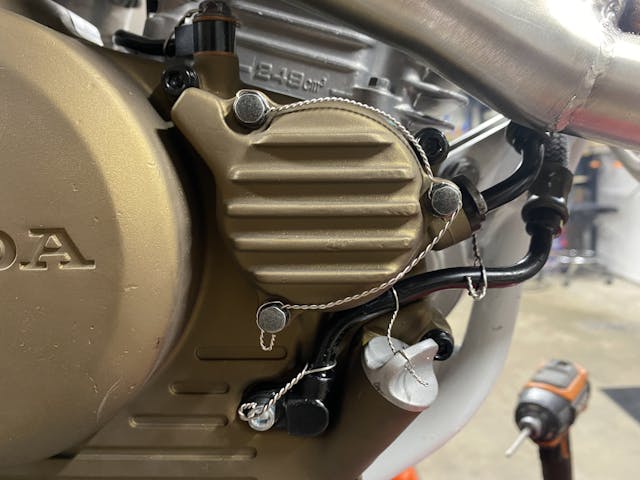
When you absolutely do not want things to start spinning on their own, you don’t leave the hard work to physics. You instead apply some type of physical retention as the final line of defense. This is the go-to for those with trust issues—and for people who fly airplanes. There is a fascinating art to tensioning and tying the strings of stainless wire between bits of hardware, carefully ensuring each pulls correctly on the next with properly minded ends.
I’m not an A&P (airframe and powerplant) guy, nor do I pretend to be, but even I can do safety wire that will retain hardware for the likes of my track motorcycles. I take comfort in knowing my oil lines will not be coming loose—although recently I did see a safety-wired line puking oil everywhere, but that’s because the banjo bolt broke. Which is a good reminder that the safety wire only prevents the hardware from turning, not from failing. Other styles that are easier on the hands include various types of lock washers that either dig into the materials or can be folded to prevent rotation. Of course, there is always the cotter pin and castle nut arrangement as well.
***
Even the simplest parts of our cars are hardly simple. Just keeping the thing together as it rolls down the road is a feat of engineering that I only scratched the surface of here. Any of us who choose to do our own work at home need to understand at least the basics of these items, though, so we can better understand appropriate reuse of parts and hardware, along with proper assembly. It’s the hardware that keeps us driving—best keep it together.
As a powerplant guy, I would tell you that safety wire is not intended to keep the fastener tight. It is intended to keep it in place and prevent it from becoming foreign material if it does come loose. I would not rely on it for tightness.
Good comment! Not coming out and staying tight are indeed two different things.