State of the Art: The Present and Future of 3D Printing in Restoration
There’s never been a better time to be a steward of the obscure, rare, and obsolete. The steady rise of 3D printing seems to have followed an inverse path from the trickle-down of tech in decades past; while major automakers continue to utilize it on a relatively small scale, the democratization of the technology has led to a massive hobbyist community. Within this, automotive enthusiasts lead a collaborative, grassroots movement in spinning up all manner of tools and componentry for collector cars at every level.
Indeed, it’s the professional restorers, speed shops, and small-batch manufacturers who appear to benefit the most from 3D printing. In some ways, restoration and modification is the same as it ever was; metal fabrication and OE parts sourcing is as relevant as ever, but as cars once considered “modern” begin to slip deep into “classic” territory, a vast amount of plastic components—both vital and superficial—are only becoming more brittle and faded with each passing year.
And as much as we hoped modern production technology and OEM classic support from automakers like Porsche and Mercedes-Benz would guarantee an unbroken line of quality OEM replacement parts, a major European and Japanese parts shortage is brewing. And, when these parts reserves run out, some cars might be jerry-rigged lest they be permanently put on jackstands.

This is hardly a new phenomenon—dwindling support has required creative solutions from generations of enthusiasts, and while 3D printing has been around for a long time, in its early days it showed more promise than result. To wit, Steve Dibdin, co-owner of Additive Restoration (AR) and one of the foremost experts on 3D printing in the automotive space, has seen the technology evolve from the get-go. He’s used 3D printing since its relative adolescence in the mid-1990s, when he says the end product could only be used for prototyping. “The early ones were incredibly brittle, and very expensive. I remember working on a product, it was a small plastic part—about three inches by four inches by half an inch—and it cost [about $2,000] in the 1990s,” he laughs. “I remember putting it on the table, and it just shattered!”
The tech has come a long, long way in the decades since. One of his first projects under the banner of AR was a twin-spark rotor arm for an OSCA MT4, a component that leaned heavily on 3D printing for both prototyping and actual production. A week after the first rotor arm was installed, the recipient OSCA was shipped abroad for a successful 500-mile endurance rally.

AR still offers that OSCA rotor arm for sale on its website with a $750 tag. Hardly cheap, but as Dibdin explains, the alternative is your MT4 running poorly, or not at all, not to mention the actual production cost of the part is higher than you might think. OSCA built an estimated 72-79 MT4s between 1948 and 1956, and given these were hard-lived race prototypes, quite a few were lost to both time and tragedy. Prior to AR’s work, most OSCAs just “made do,” either with adapted off-the-shelf ignition or with time-consuming custom-fab parts. Dibdin says previous efforts from enterprising owners include a small batch of rotor arms hand-dremeled from a block of Bakelite.
With so few cars in existence and traditional means of parts production, it hardly made sense to produce even a limited run of production rotor arms. Economies of scale mean a minimum order for this part might have run into the hundreds, if not thousands of units, necessitating a unit price far, far beyond AR’s $750 ask. “We do a lot of one-offs, of course. But below between 1,000 or 2,000 parts, there’s this gray area that’s been difficult to make things efficiently, especially in plastics—until now.”
He holds up a small, blue plastic component on our video call, apparently a 3D-printed prototype for a carburetor linkage for a Sunbeam Tiger. As he tells it, the nylon doodad is likely stronger and will last longer than the original part while maintaining the same appearance. I ask him if that’s the case for many now-ancient plastic parts. “Absolutely! Take the column switch repair kit for [Ferrari 330s]. If you have one of those, there’s a good chance your indicator stalk is going to fall off at some point.” He mentions poor injection molding done in-period that that produced a plastic part that was weak, brittle, and full of inclusions.
“It was destined to self-destruct at some point. With 3D printing, we can make sure we don’t have those [imperfections], and I can predict exactly how something is going to fail,” he explains. “The technology we have both on the design side and the implementation of that is far advanced from where it was even 10 years ago.”
So, at the current state of the art, proper implementation of 3D printing produces components that are often better and far cheaper to produce than it was when it left the factory. For the smaller parts, is there still even a need for traditional restoration methods? “Machining still has its place,” he says. “What [3D printing] does is take out much of the man hours and required expertise of actual production. The design and development time is still the biggest expense.”

Shucks—I was rather hoping each hobbyist 3D printer came with a button marked “Press here for 1950s Maserati wheel cap,” but I digress. Of course, plastic isn’t always the answer. “If we’re doing something like suspension or brakes that’s safety critical, we’ll machine it from billet,” Dibdin explains. “We can get parts printed in 3D metal, and they’re very good. But, there are significant considerations.” He mentions post-processing is a large part of the current output of 3D printed metal, both aesthetically and structurally. And you’re limited in the material and application, whereas machining is settled science.
“When you machine something from metal, you know the material, you know the process, and the tolerances are far, far tighter,” Dibdin continues. “Though they can sometimes 3D print in metal or other material and then throw it on the CNC to finish it off.” The best of both worlds, then.
Still, even modern material cannot out-maneuver poor design. Dibdin mentions a previous project involving 3D printing a commonly failed part found in a Ferrari 550 seat. After a full development period, AR’s recreation part failed a short while after installation. “You have to know where the technology is appropriate and compatible. It’s the difference between getting a microwave-ready meal versus going out for a sitdown meal,” he laughs.
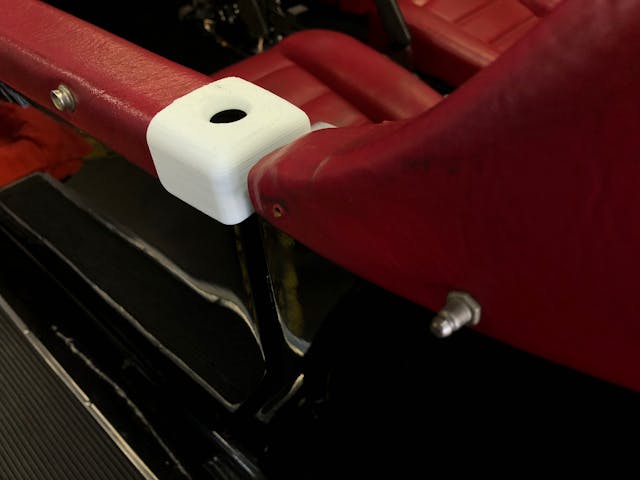
Dibdin was keen on stressing that 3D printing, no matter how advanced it may be, is still just another tool in your workshop. “It helps us get to a point, but it’s still very much about human interaction and understanding how things go together. It’s sort of sexy with lasers flying around, but to get to that point, someone spent time developing a product, going through iterations, prototyping it, testing it, and making sure it’s suitable,” he says. “At the end of the day, it’s just a fancy hammer.”
So, things are looking way, way up for micro-scale production of better-than-factory direct replacement components. But 3D printing has also irrevocably changed the aftermarket, especially when builds turn both restomod and big money.
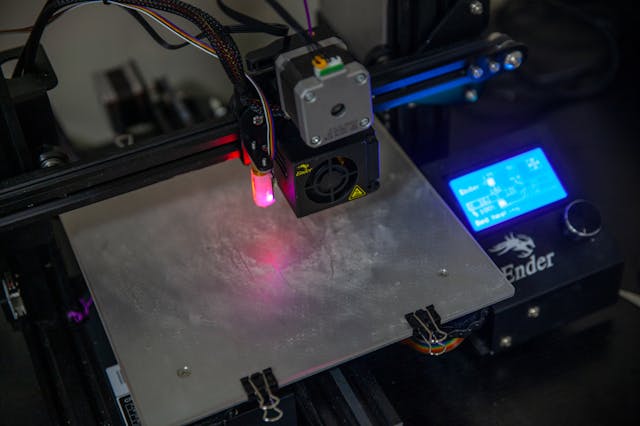


In a similar vein to Icon 4×4 and Gateway Bronco, Texas-based Vigilante 4×4 thoroughly modernizes and powers-up your choice of SJ-platform Jeeps, including ‘70s family truckster hotness like the OG Cherokee, Gladiator pickup, and Wagoneer. These are serious builds, and with a price tag starting at $300,000, each build is incredibly detail-rich, with little touches the Vigilante team says wouldn’t be possible without 3D printing.
Actually, the whole enterprise likely wouldn’t exist. “It’s important to say that it’s a very critical moment for us, as Vigilante is about modern technology, and we wouldn’t be able to do what we’re doing without 3D printing,” says co-owner Rachel van Doveren. “A lot of other vehicles can order [modern] parts straight from a catalog. Jeeps don’t have that luxury.”
Like most shops that utilize the tech, Vigilante primarily 3D prints test components as part of prototyping ahead of machining. “As of right now, we have an FTM printer in-house that we prototype everything from handles to brackets before we machine the metal part to make sure it looks right and fits correctly,” explains 3D printing specialist Nick Douglass. But, where there is no old part to restore or modify, and the component sits more-or-less behind the scenes, Vigilante will create something wholly new.

Jeep never installed rear air-conditioning ducts on any SJ-chassis vehicle, so some clever 3D printing ensures rear passengers are either frosty or toasty. Among Vigilante’s signature details are the repositioned (and modernized) air-conditioning controls, now made to look entirely original via careful post-processing. “We start with determining the need for the custom solution,” says Douglass. “We ask, ‘Are there factory parts we can restore and reuse?’ When there aren’t, we begin the process.”
It could be as complex as the A/C or as simple as a tiny bit of trim. “Take for example the clip that holds the sun visor in place. That’s not a complex piece. It just had to do its job and look good,” Douglass says. “Trying to get a factory piece sanded, repainted, and installing it with a screw without cracking that plastic can be a huge challenge.”
I ask Douglass about what developing 3D printing advancements he’s most looking forward to. He mentions metal printing, and material with integrated carbon fiber. Then, he pauses for a moment to reflect, thinking back on our discussion. “I wonder, personally, when it will become so hard to find a decent donor [body] panel, that the technology for sheetmetal reproduction will become more popular,” he muses. “There is a technology I’ve seen videos of, where a CNC-type machine uses a hammer-type object to form sheetmetal panels almost like a 3D printer, working a layer at a time. I wonder if that’s going to be the only option in the future.”
A fancy hammer, indeed.
***
Check out the Hagerty Media homepage so you don’t miss a single story, or better yet, bookmark it. To get our best stories delivered right to your inbox, subscribe to our newsletters.