6 storage tips to optimize your garage space
Garages are multipurpose spaces, even if you don’t use yours primarily for DIY projects. There are things to store, some of which will be in storage forever and others that need to be readily accessed. Large swaths of floorspace must be clear or, at least, able to be made so on short notice. And we haven’t even gotten to the vehicles themselves.
Whether you run a full restoration shop or simply park your vintage ride inside day-to-day, these six storage tips will make your life easier.
Bin it
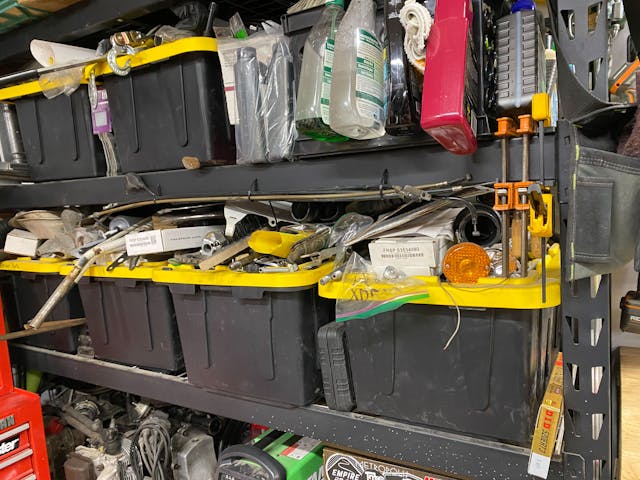
Garages are dirty places. Their large doors regularly admit dust and dirt, and these conspire to make everything inside a little more gross than the last time you touched it. Car parts are also vulnerable to sun and ozone exposure. Rubber ages much quicker when kept a room that has sun beaming in through a window plus a fridge, freezer, or compressor running in the corner. Ozone causes dry rot in tires and can harden spare rubber seals or gaskets to the point that they are unusable.
Keep degradation at bay by utilizing storage bins or containers to close things off from the sun and minimize ozone exposure.
Now actually bin it
You’ve decided to put everything in careful storage. Now it’s time to cull the parts stash and keep only the things that you need, recycling or selling everything else. Yours truly needs to hear this one, too: I have at least three pairs of “spare” cylinder heads for my Corvair, despite the fact I have no plans to rebuild that engine, and the heads that are in the car will be good for a long time. I should sell those.
As you do inventory, make sure your spares are actually worth keeping. At least once, I’ve dug into my stash only to find that what I thought was a solid spare was actually junk. That afternoon quickly turned frustrating, as I left the garage to go inside and start scrolling eBay.
Keep it together
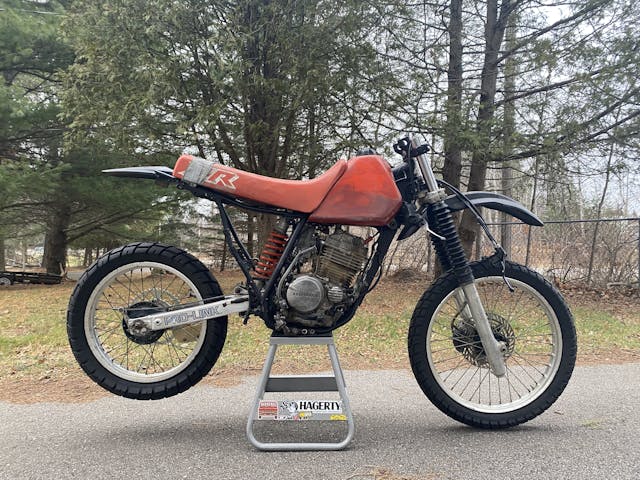
The easiest way to store a complicated arrangement of small parts is when those parts are assembled.
A friend of mine took a flathead V-8 Ford apart a few years ago as a winter project. For one reason or another, he got derailed. Before long, Ford engine bits became dirty, lost, or, at best, disorganized and scattered across his garage.
Once he decided to back-burner that rebuild, it would have been best to loosely re-assemble the V-8. That way, he could relocate it easily and store it as one large chunk of components. I’ve used this approach with a few transmissions and engines. Another upside? When you store the temporarily assembled project, you can write a tag recording what it needs and what you found when you began to tear it down.
Label, label, label
Speaking of tagging, have I hammered home the point that you should be labeling everything? Labeling things removes the index from your brain and frees up mental space for things that actually matter.
Wheels … all the wheels
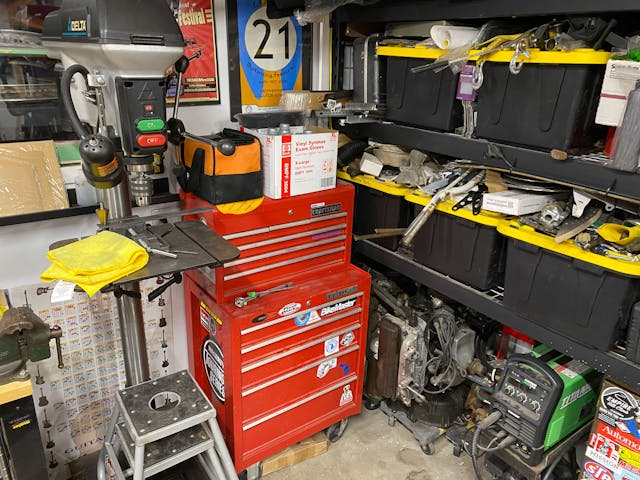
Have a heavy thing? Put it on wheels. Awkward-sized thing? Wheels. Tool chest? Wheels. Workbench? Most of the time, believe it or not, wheels.
It’s hard to overstate how nice it is to be able to rearrange your shop on a moment’s notice without breaking a sweat. Even better is the ability to “bury” things behind other things. For instance, in my shop I have few engines sitting under a shelf. I might pilfer one of the engines for a part once or twice a year. Usually, those engines are tucked into the corner, blocked by my drill press and a toolbox. Luckily, both the press and the toolbox are on wheels, so each is easily rolled away whenever I need to access the engines.
Combine functions if you can
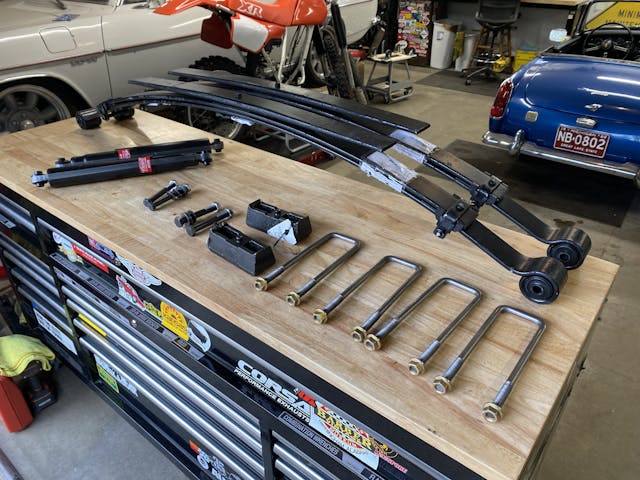
One of my favorite things in my personal shop is my 6-foot rolling toolbox. Sure, it has drawers aplenty, but most importantly, it has a worktop. This makes it the best of all workstations.
Not all dual-purpose tools work as nicely. Often, you’ll have to compromise. For example, the workbench on top of this tool chest is too thin for me to mount a vise to it. If this were my only workbench, that would be quite the challenge. The best advice is to think through all the pros and cons before putting big money into multipurpose shop equipment.
Check out the Hagerty Media homepage so you don’t miss a single story, or better yet, bookmark it.
I scored one of my favorite motorcycles many years ago from a guy who broke it, dismantled it, put the parts in boxes, tucked the boxes in the garage, and (per his story, for lack of funds and time), pretty much forgot about it. After about 15 years and two moves, he had not only lost interest and incentive, but wasn’t even sure if he had everything. In I walked, and made an offer – which his wife strongly encouraged him to accept. Thus came about my assembling adventure with a 1968 Triumph Bonneville 650. Parts to replace the damaged ones were easy enough to find (this was in the late ’70s), and a few brewskis got a local Triumph expert to give me some pointers. For less than a new set of tires for it would cost at today’s prices, I had me a really fun ride.
#1 when building a garage build it bigger than you plan.
#2 external storage barn. This is for non car related parts, tools and other things that can get in the way.
#3 cabinets. Shelving and drawers are your friend.
#4 make use of rafters. I enclosed a filled in mine with OSB boarding and folding stairs. Not only does it give me more storage but also it let me insulate and make for a warmer and cooler garage.
#5 Walls make use of every aspect. I have some man cave stuff like half the nose off Greg Picketts Jagbthst burned at Mid Ohio to the tailgate from Austin Dillions rookie Bass Pro truck tail gate. But I also have parts, tools and shelf’s with items for work.
#6 Ceiling use this for lights, air hoses and I even have my sons 3 soap box derby cars and his CR4 Corvette power wheels car tires up hanging on the ceiling. A good way to store large items and decorate at once.
I have had a number of people visit and others bring people to see the garage. It is part show place with a Corvette Billboard and big screen TV with Porsche seating and a Top Fuel short block coffee table. But it is also a place you tear down an engine, rebuild a tractor or weld a frame.
No matter how much storage make sure to clean up regularly and put away tools and parts. Clutter is the main issue most face.
Regarding “make use of rafters”: make sure that the garage roof construction is study enough to support what you put up there over time, especially any heavy stuff – you don’t want this to come down on your favorite ride when you get heavy snow on the roof
Regarding “I can’t do bins because I need to be able to see things”: place a piece of paper with a number (or a date, name etc.) in the open bin and take a picture of it, print and tape to the outside of the bin. Or write the date and number on the outside of the bin and refer to your stored phone pictures for reference
meaning: take a picture of the contents of each bin and tape on the outside of that bin, plus then you have an electronic record on your phone or computer
They also make bins that you can see through. They are not quite as strong, but make things easier to identify
As I’m only storing small motorcycle parts, I tend to use the shoe box size bins. They are translucent and easily marked with a Sharpie.
These small bins can be stacked on your shelves. Unfortunately the one with the part you want will always be on the bottom of the stack.
“Junk expands to fit the space allocated”, so build a small garage and throw the stuff out!
Do you have any pictures of your garage?
A great add on is to purchase some amazing American Made Post-Rack brackets! Cantilever steel brackets that extend 2’ from the 3-ply, 4-ply, or 6” x 6” post/column/beam of your pole barn/post-frame building. These brackets have an adjustable “grip” and hold extreme weight. FREE UP YOUR FLOOR! STORE UP THE WALL! Protect your projects with security! Build an industrial workbench, shelving, and storage spaces. Check ‘‘em out! They are AWESOME!
I can’t do bins because I need to be able to see things. An item in a bin is an item lost to time. I use a lot of shelves. The general issue I have with creating space is that every time I make space, I acquire things to put in it. Hyperv6’s suggestion to build bigger than you plan is dangerous, because car parts are a fluid and will fill every available space of their container. I have settled with rearranging clutter to accommodate projects.
@TG, That’s why you organize and group like things into bins and why you label them. Then, you can just look and see this bin is Harley stuff, that bin is Christmas stuff, etc.
I use the clear plastic bins made by Sterlite.
I’ve got 3 cars, 2 Olds 442s and a 928 ~ 84 Porsche in one bay of a 4 bay Metal space building. I have to move one car that’s not been running for 33 years to get to high storage shelf stuff, and although I’m a typically pretty neat, this bay is OUT OF CONTROL. I’m building two motors, both for Boats, and small projects for two out of three cars. I need physical help to get it back in shape. All my friends have shed their mortal coils. Two left, one in Naples Fla, & Braintree Ma. I need HELP!!!
With all the great stuff in your shop it should be easy to get some help from someone who just wants to hang out a learn stuff.
Better not get rid of those Corvair heads. They aren’t making them anymore. As long as you have the car, keep the parts, or at least one set of spares. I have a ’69 Firebird with OHC 6. I have a spare engine for it just in case. The engine in it supposedly was rebuilt in the past sometime, but the block has a crack and leaks a bit of antifreeze. Had the spare 20 years. I disassembled it and put back together without piston rings but with the bores greased. It had been stored improperly by the previous owner and had one lightly stuck piston (so now it needs overbored). If you put stuff in bins, inventory ALL the contents and put the inventory sheet inside AND on the front as well as number the bins and keep a copy on your computer. If you take stuff out, remove the item from the list.
Yup, labeled bins, wheels under heavy stuff, shelving, and an attic/mezzanine if you can. Likewise, having a separate location – shed or small building addition – for the non-automotive stuff keeps clutter & dirt down. I tend to group parts by which vehicle they belong with, as well as general electrical, plumbing, etc. I also like to keep stuff off the floor if possible to make sweeping easier. I find that the less clutter – physical or even visual – there is in the shop, the happier and more productive I am.
An economical solution to visible clutter on shelves is to buy second hand kitchen cupboards. They keep the dirt off stored items and once all are painted the same color, look just as good as expensive store-bought units. I’ve also used some of hyperv6’s other ideas too.
I have done all of the above…….still need space!!!!!! To much stuff?!?!?!?!?!?
I’m a firm believer in shelving and binning everything. Each bin, shelf, drawer, etc is numbered. Pretty much every very single part I own is logged onto an excel spreadsheet cross-referenced with location (bin, shelf, drawer + garage, basement, etc) as well as with car model if not a generic part. I never have a problem finding anything….but it does take a lot of self-discipline to remember to remove the part from the spreadsheet ‘inventory’ after it is found and put to use .
Also, a big plus to being organized is that it allows me to collect more without the wife noticing, lol 🙂
Re- purpose has been my solution.
I have converted a 60×60 calving barn into vehicle storage.
Now if I can only get my shop in line I hope to be able to actually get to work on my several projects.
Of course not right now as is is currently -15 f here in northern Alberta.
I use the two cars in the garage as shelves. As do many others. I’m just flat out of room!
I always buy the 3 drawer lateral file cabinets and use them in my shop. They are perfect height for a counter and they can handle heavy parts. I also have the storage bins that you showed but i get the clear ones the have the folding lids so i never loose the lid and i can see what is inside. the last thing is a store all the way to the ceiling with those bins and have a rolling ladder system in both my shops. the ladder pushes out of the way when not in use and rolls from one in of the shop to the other. In fact in one of my shops in turns a corner to get to the other side.
You say the top is too thin for a vise? Buy a butcher block panel from an outfit like Grizzly and make the top thicker.
Keep it accessible. Things you frequently need should be immediately visible and at hand. Oil filters, drain plug washers, fresh oil, nitrile gloves, combination wrenches, screwdrivers. Use wall space for cupboards, shelves and of course as big a roller cabinet and tool chest as you can fit. This will save a lot of time and frustration.
One must understand a principle of life. The more bins, shelves, cabinets, out buildings, decked attics, and rafter hangers that are added, they will ultimately be filled, and often not in an organized manner.
Labeling is good. Bag and tag is even better, especially for small parts. In addition to this, think about photographing things and even creating photo essays where you remind yourself about where something goes, how it’s attached, where it is stored and so forth. Presentation software (Keynote for macOS, PowerPoint for Windows) enable you to collect images and even videos with “speakers notes” attached to each slide. This is a great way to assemble an annotated photo/video essay that will help you manage the chaos that you created.