Polished to perfection: Behind the scenes of GDK Veneering

If GDK Veneering was a multinational company it would have plaques and posters on the walls at its global headquarters proclaiming its green credentials and boasts that it was single-handedly solving global warming. But GDK Veneering isn’t a multinational company and its global headquarters are behind a smart semi in a residential street in Crewe, U.K., Not that far from the Bentley factory. Flash it ain’t, but what could be greener or kinder to the planet than taking faded, cracked and aged wood from a classic car and making it like new again?
Years of fiddling with old cars has filled my address book with useful contacts for the many trades that are essential for the amateur fettler or restorer. Rusty bodyshell? No problem, I can point you in the direction of a company that can blast the rust off your E-Type’s monocoque using friendly media such as nut shells. MIG or TIG welding? Easy, I’ve got just the man for you. But woodwork and in particular work with veneers, I’m afraid I can’t help you. That’s changed after a morning with Ged Gollings, his son Daniel, and nephew Sean.
I’ve never visited an outfit quite like this before. Ged Gollings apologizes profusely and repeatedly for the rustic appearance of the workshop, but there’s no need because I’m used to seeing craftsmen working in cramped and untidy premises. Look more closely, however, and you see a perfectly managed and organized operation in which experience, lateral thinking, and sheer improvisation has created a perfect working environment.
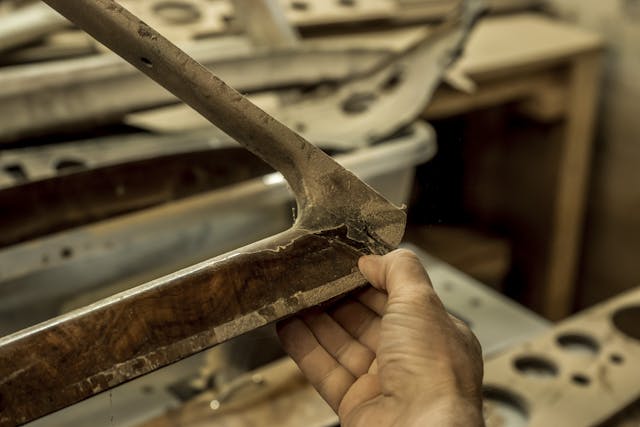
You’d expect from seeing his work that 52 year-old Ged had served an apprenticeship up the road at Rolls-Royce (which was in Crewe until BMW bought it) or Bentley. Not quite. Until redundancy struck he was working at his local B&Q. Gollings explains his unusual career path: “I then got a job at a company doing veneering that was run by a bloke who was at Rolls until he was also made redundant. I’ve never been massively into cars but as I soon as I started I fell in love with the job. When I started all I did was simple tasks like stripping off old material and removing brackets. Exactly the type of work that my nephew Sean does here.”
Unfortunately this company went to the wall when a large OEM pulled its work, and since it was the firm’s major customer, that was it. “We started GDK in 2013,” recounts Gollings, “and because I’d loved the work I’d paid attention and picked up a lot of the skills. I’m getting better at making things all the time and my skill level is improving.”
Looking at the work done here, that’s an understatement.

GDK Veneering is planning an imminent move into larger premises where everything will be done under one roof. For now there are three separate workshops. There’s the one at the back of the house where the intricate work is done, plus final polishing and then despatch of finished work; a small work shed on a small industrial estate is where Sean strips off brackets and strips off old lacquer; and then on the same estate there’s The Shack. From the outside The Shack looks like an old chicken shed but inside is a shed-within-a-shed. This is where final sanding and preparation takes place and where lacquer is sprayed onto parts. The Gollings have built an elaborate filter system so dust doesn’t get onto the wet surfaces.
Meanwhile, back at the home workshop Daniel Collings is working on some woodwork for a Mark II Jaguar. “It’s funny,” says Ged, “we seem to get runs of a particular car and then we go for ages without seeing another one.”

I’ve never seen veneering done before. It’s mesmerizing—a real art. Gollings Jr. is cutting small strips of veneer and then gluing them to the wood itself. Behind him is a fantastic example of Gollings ingenuity: a vacuum chamber made from plywood. It features a rubber sheet that is drawn down over, say a door capping, that has had its veneer glued on and now needs to cure. The sheet, drawn down onto the part by vacuum, holds the veneer in place until the glue has thoroughly dried. Smaller and more intricate parts that can’t be fitted into the vacuum curing box have to allowed to dry more slowly in the open air, with carefully applied tape holding the veneer in position.
The veneers themselves come in a multitude of different materials including the ever popular burr walnut. About four sheets of veneer are needed for a set of Jag Mark II woodwork, and they’ll cost around £250 ($336). I’d always assumed that the veneers come from the trunk of a tree, but that’s not the case. “No,” explains Gollings Sr., “the veneer comes from the tree’s bulb that’s below ground.”

Back at the satellite works Ged Gollings pulls out a box of wooden trim parts that are in an absolutely dreadful state. “This is about as bad as it gets,” says Gollings, “they’re from a 1960s Mercedes SL ‘Pagoda’. You can see how the lacquer has been in the sun for decades and has bubbled off. Also, the wood underneath the veneer has delaminated and looks as though it was made of some sort of cardboard rather than ply. This is going to be a complicated job as we’re going to have to make new bases for some of the parts before we can even think about the veneer. We’ll be charging about £1900 ($2555) to return this lot to perfect condition.’ Which seems extremely reasonable to me. Firstly, a perfectly restored Pagoda will be worth at least £100,000 ($134,500).
Once Daniel Gollings’ work has cured in the drying box it’s time for the parts to go to The Shack for spraying. “In the postwar period a polyurethane lacquer was commonly used,” says Ged Gollings, “but today we use a polyester lacquer. Pre-war material was more like a varnish.’
Pieces that have already been sprayed with lacquer are on drying shelves and I’m surprised at how thick the coating is. That’s explained as Ged takes me through the multiple sanding stages that go from the use of coarse 180 grit paper to finishing with 1200 grit. “It’s important,” he points out, “to use a good quality sand paper. We get through a lot of it.”
Back at the house we move to the polishing wheels. Again the Gollings’ imagination and improvisation skills have gone into making a really impressive polishing station. It’s miraculous to watch: with only a couple of passes along the spinning polishing wheel (to which Ged has applied one of several different types of polish that are used) a Mark II Jag door capping has gone from having a smoothly sanded but matte finish, to a high gloss part that looks as good as it would have done when came out of Browns Lane in the early ‘60s.
Speaking of Jaguar and its history, GDK was responsible for restoring the dashboard and wood parts for Sir William Lyons’ personal XJ6. Another set of XJ6 woodwork is currently going through the workshops. Unlike his father, Daniel Gollings is heavily into classic cars and is very knowledgeable. “Money no object I’d have a Jaguar XK-SS but on a more realistic level I’d like to get something like a Triumph Spitfire.” Presumably he wouldn’t be able to resist restoring its woodwork. “Those cheaper cars, like TRs and Cortinas, used cheap straight grain veneers together with cheap lacquers and animal glue. Not quite in the Bentley league.” Talking of Bentleys, Turbo R interiors are currently very popular. GDK also makes parts to keep in stock such as MGB wood kits.
“We make them if we get any spare time,” explains Ged Gollings, “which is rare. We currently have around an eight-month waiting list.” Gollings also tells us that customers are very precious about their car’s woodwork and often come and see work in progress. “We once had a Middle Eastern prince arrive to look at his car’s wood trim. He arrived in a Range Rover with heavily tinted windows and bodyguards, parked outside and came out back to check on progress.” I suspect he was surprised by the premises and awestruck by the quality of the work done within it.
Now my car restoration address book is complete, and I can point you in the direction of an outfit that can turn your classic’s sun-bleached, cracked, and discolored wood dashboard back into a thing of beauty.
Via Hagerty UK