When he’s not racing Pikes Peak, Dennis Palatov plans to revolutionize the battery industry

As memorable adventures do, this one came together in an unusual way. After a couple of brief emails, I found myself on a plane with the then-Infineon Raceway as my final destination. My assignment was a feature story for one of those famous British car magazines that would compare simulator driving with real-world action at this fast and intimidating circuit.
I’ve never refused a driving challenge, but this one caused me a little anxiety because I was meant to drive something I’d never heard of: a Palatov D4. It’s a stout little track car that looks like a sports racer of sorts and promised to be properly quick around Sonoma Racway. With the potent combination of a sub-1000-pound weight and a 180-hp Hayabusa motor, I expected that I was in for some serious lateral g-loads.

Walking me through the design of his car, Dennis Palatov spoke like a race engineer and it became apparent that this was no crudely constructed, home-built special. The D4 is a thoroughly considered track car intended to offer formidable on-track performance for a reasonable price with low running costs. The car’s most significant innovation is that the engine is placed not behind or in front of the driver but beside them, for optimal weight distribution. What wasn’t immediately apparent, though, that afternoon at Sonoma, was that Palatov is not a mechanical engineer.
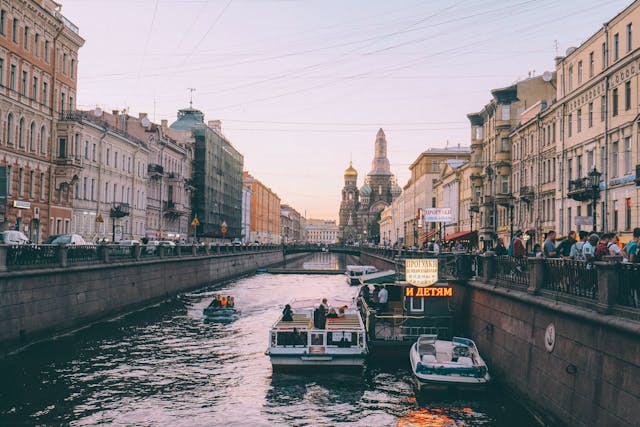
Growing up in St. Petersburg, Russia, Palatov always loved cars. In summer, he’d visit his grandmother near the Finnish border if only to catch a glimpse of a couple of foreign cars driving past. At age 15, he emigrated to the United States, breezed through highschool and finishing early, though he technically never graduated. Armed with the necessary AP courses and strong SAT scores, he was accepted to Cleveland’s Case Western Reserve University.
Palatov’s experience at Case was much the same as time in highschool, and he found himself with the credits necessary for graduation partway through his final year. After petitioning his professors, he got the necessary signatures, left Case, and didn’t bother to attend graduation. He later received his diploma in the mail.
“Some of the best engineers I worked with didn’t have degrees,” Palatov says, “but working with them taught me how to learn, and that somebody can teach you only what’s already known. If you want to discover something, that’s a whole different mindset and process–nobody can teach you something that they don’t know yet. I’ve made it my life’s work to figure out things that people don’t know yet.”
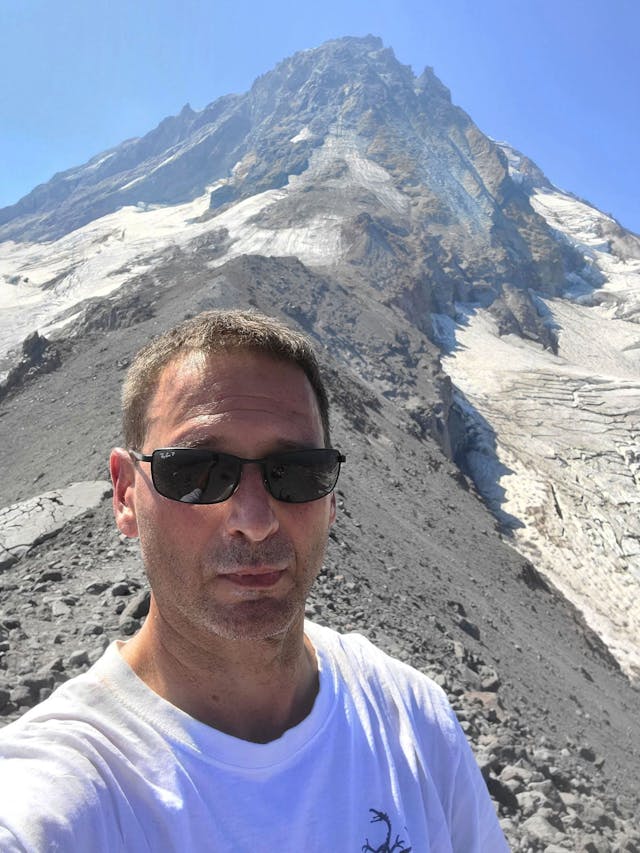
For many years, Palatov worked as a successful computer engineer and, along the way, scratched his performance-car itch with the purchase of a “clown shoe” BMW Z3M. When he discovered that Portland, Oregon was home to a city-owned racetrack, technically a park, he picked up and relocated. “I just always wanted to play with cars on track.”
If anything, Palatov is decidedly unconventional. From the cars that bear his name to his thoughts for the future of electric vehicles, he’s pursuing better and typically unorthodox ways to solve problems. I’m sure Palatov would shy away from this characterization, but if one can treat high school and college as a cakewalk, have a successful career in computer engineering, and transition to building serious track cars, there’s only one way to describe them: a polymath.
To date, Palatov Motorsports has turned out thirty remarkable performance cars, including the Hayabusa-powered D4 model that I drove many years ago; the D1, packing a compact, 3.0-liter Hartley V-8; the mid-engine D2; and several Pikes Peak racers. Palatov’s upcoming D8 coupe has been developed to accomodate both small-block Chevy and electric powertrains, and to my eyes, it’s the most attractive and appealing design the shop’s produced yet.
From their shop in Portland, Palatov and his team have already engineered some electric vehicles, specifically a pair of D2s for their partner, Cascadia Motion, the same firm with which Ford Performance partnered to built its Mustang Cobra Jet 1400 electric drag racer. Cascadia makes a slew of electric vehicle components, from motors and batteries to inverters and battery control systems. In the EV world, everyone likes to talk about battery size and motor output, but the real magic is found in the inverter engineering—and Cascadia builds some of the meanest.
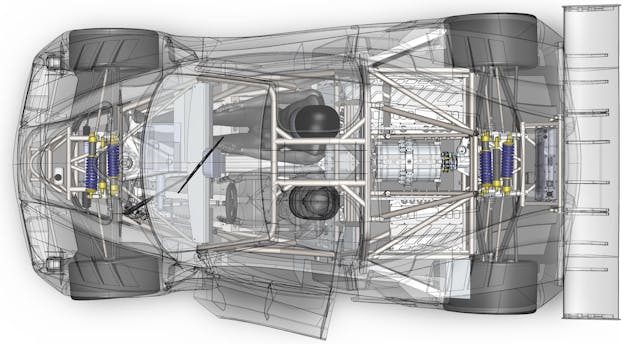
With his unique perspective for designing performance cars, I’m not surprised that Palatov has turned his attention to EV battery technology. Perhaps through the design and engineering process of the D2s, his approach to batteries is lightyears ahead of the industry.

“The problem is that there are not enough EVs that are retired yet,” he says. “Most of the EVs that have been recently manufactured are still in use and working just fine, until you have to recycle the battery. When you go to retire the vehicle, it’s a thousand pounds or so of battery that can still output ridiculous current. It requires big forklifts to remove from the car and the hazard of the residual energy in the battery is huge.
“Nobody really is thinking about that right now. They’re just pumping things out and all of the regulations that we have right now have been designed to overcome the biggest objection to EV adoption, which is range.”

If you look around, there’s not a single producer of electrified vehicles that doesn’t lead with the topic of range. However, as Palatov says, “If we’ve rated gas cars the same way, we would all be driving 5-mpg cars with 100-gallon fuel tanks, but that’s not a responsible way to treat a finite resource that has a big environmental and geopolitical impact.”
Palatov’s right. Each gasoline- and diesel-powered vehicle is rated and sold based on its incremental efficiency—on how many miles it can travel on one gallon of fuel. BEVs, on the other hand, have to overcome consumers’ anxieties about maximum range, so OEMs market them based on how far they can travel on the electric equivalent of a full tank. To EV pioneers, however, this logic is a bit simplistic: There’s arguably more ground to be gained by focusing on efficient consumption in specific use-cases than pursuing sheer maximum mileage—the electric equivalent of a bigger tank.
Instead of producing electrics with conventional, monolithic battery packs, Palatov is investigating a universal standard for a modular battery pack system that allows you to only carry what you need, reaping immediate benefits in weight-savings. The benefits are considerable, not just for the end-user, but also for the environment.

Palatov’s recently formed a company, Modular Battery Technologies, to facilitate this more circumspect approach. With governments incentivizing the manufacturing and adoption of EVs around the world, there’s no better time to tackle the challenges than right now. Modbatt thoroughly revolutionizes the way in which we look at EV batteries and is based around the concept of a smart, 3-kWh, modular cell that weighs in around 35 to 40 pounds for easy handling.
For the sake of argument, your typical 80-kWh automotive battery pack adds an easy 1000 pounds to the curb weight of an EV. Sure, it’s always positioned low in the chassis for optimal dynamics, but imagine if you weren’t lugging around those hundreds of additional pounds all of the time.
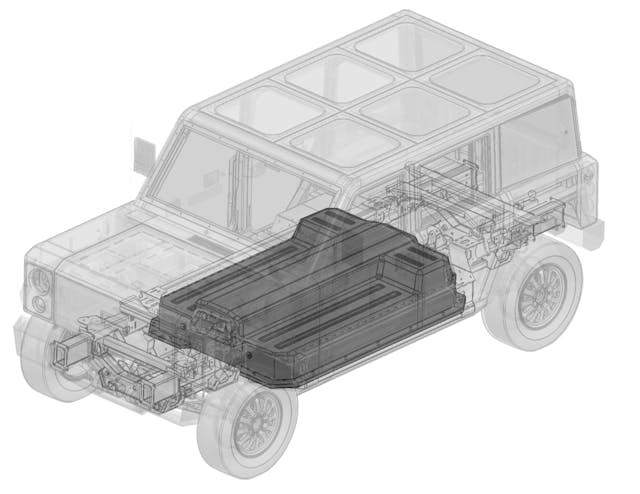
With a Modbatt-equipped EV, you’d only carry as much battery capacity as you’d require. I know from my EV driving experience that I’d like roughly 20 kilowatt-hours of battery onboard to satisfy my daily driving routine. That translates to a Modbatt setup of seven 3-kWh packs for a total of 21 kilowatt hours, with a combined weight of 280 pounds. Even with one additional pack for good luck, that puts my daily EV battery stash at 320 pounds.
Compared to the 1000-pound, more traditional storage system we sketched out, that’s 680 pounds that I don’t have to accelerate, brake, throw through corners, and generally haul around. Imagine two Dwayne Johnsons in your back seat every time you go for a drive! For those occasions when you need more range, you simply add in a few more battery modules.
Even with a two-ton vehicle, losing several hundred pounds from its curb weight imbues it with shorter braking distances, which is an undeniable improvement in safety. If it’s an EV with any sporting intention, the vehicle will be much more satisfying to drive. This modular approach gives EV designers the ability to place batteries anywhere they like in a chassis, allowing for the complete optimization of a key element of the vehicle’s weight.
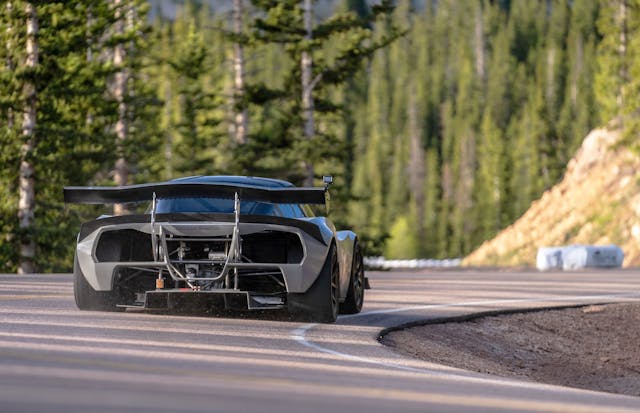
Since the the packs are self-monitoring, they have tremendous flexibility and safety. If, for example, a single pack goes bad for any reason, it can be switched off individually and the EV will continue to operate by drawing juice from the healthy modules.
Through a blockchain-based system, the battery modules can be securely authorized for use in a particular vehicle and are tracked from production to end-of-life. While all battery packs eventually become unusable in vehicles, that doesn’t mean true end-of-life. Once they no longer meet the performance standards for vehicle use, the Modbatt units can easily be upcycled into power packs for electric golf carts or for home-based power backups before final recycling is necessary.
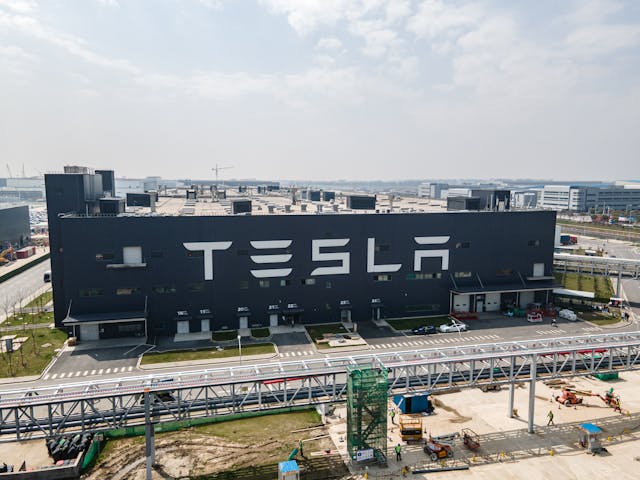
EV battery production is at a critical juncture. In 2020, electrics reached a milestone of 1.8 percent of U.S. vehicle market share, or roughly 1.7 million cars, and even now battery supply is a limiting factor. Making the electric future more daunting is that between legislative changes and various OEMs focusing on EV production, the supply of batteries will have to swell. Despite all of the wild promises, we won’t see the end of the internal combustion engine any time soon, as meta-forecasts suggest that the EV market share will increase to somewhere between 25 percent and 30 percent before the end of the decade.
Carmakers and suppliers have begun ramping up capacity, with 500 gigawatt-hours worth of battery production coming online for 2024, which will serve to satisfy some of the demand. However, if the average EV uses a 75-kWh battery pack, 500 GWh of annual production will satisfy less than seven million EVs, a fraction of the predicted market size.
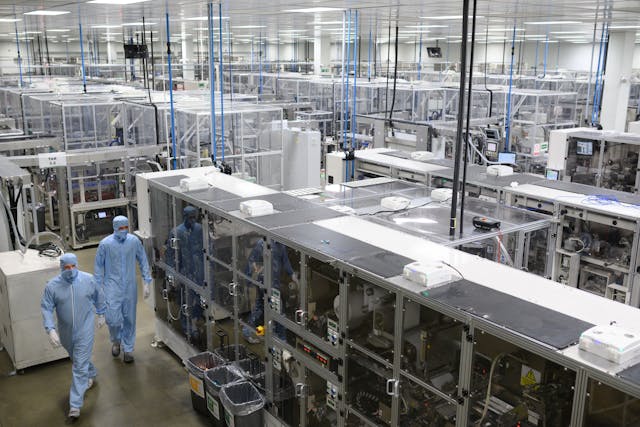
While demands may be greater, but even if the market is looking for even twenty million EVs, push will indeed come to shove. Palatov’s Modbatt not only permits vastly greater electric-vehicle production quantities, simply by virtue of those vehicles carrying the amount of batteries required by the users, but it’s a responsible and comprehensive production through end-of-life strategic approach.
In 2021, EV battery recycling has yet to become a problem, but it will in the near future. Consider that until now, and even for the foreseeable future, electric vehicles and their battery packs are a single, symbiotic unit. They way EVs continue to be manufactured means that you can’t have one without the other and separating the battery pack from the vehicle remains a costly, complex, and non-standardized process.
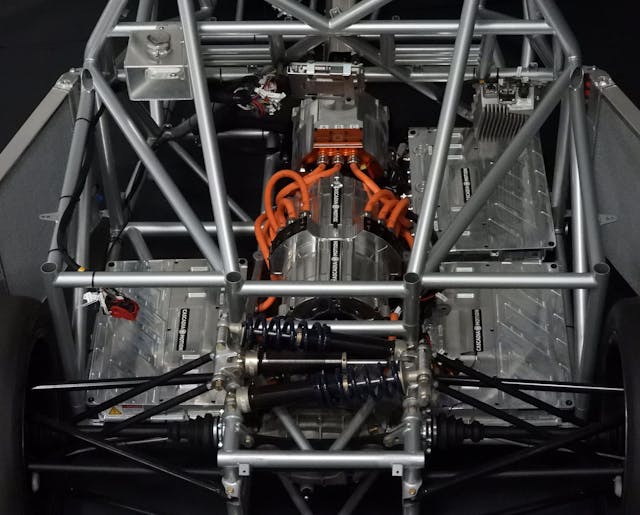
Modbatt solves that problem because each battery module can be easily decoupled from the vehicle and vice versa. Need a new battery pack? Just head on over to Pep Boys and pick up some fresh, fully charged units and recycle any aged-out packs at the same time. When end-of-life comes for the vehicle, recycling the entire vehicle is simplified because the battery pack and the car aren’t a single unit.
Without any EV battery lifecycle management standards in place, Modbatt’s approach is not only smart, but environmentally responsible, as well. What’s more, Modbatt’s modular design is meant to be an open standard and is available to any automaker or battery manufacturer.
Under the Modbatt model, EV batteries become a commodity at all stages in a module’s life cycle—production, delivery, storage, usage, repurposing, and final recycling—and their physical size means they can be handled by us humans while Elon’s robot people remain in their inevitable, perpetual development cycle.
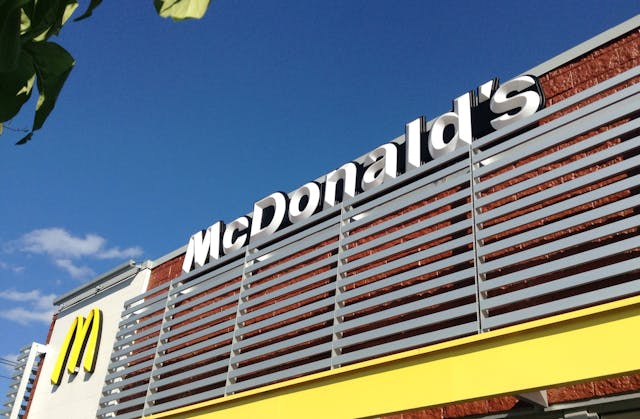
In the way that McDonald’s isn’t necessarily in the burger-slinging game, but rather heavily invested in real estate, Modbatt’s business model isn’t built around the production of battery modules. Manufacturing can be undertaken by any company by licensing Modbatt’s open standard on a royalty-free basis.
I’d like to avoid the digital currency rabbit hole at the moment, but in Modbatt’s case, blockchain and NFT technologies have some practical uses. According to Palatov, Modbatt “will charge small convenience fees on transactions like authentication, car-battery pairings, module ownership transfer, recycling certification, and we will also offer IT services and infrastructure to facilitate those transactions.”
The success of Palatov’s modular battery tech will require a major shift in regulatory thinking away from the myopic view of range, a completely different approach from manufacturers, as well as how vehicles are homologated.

In the meantime, Palatov thinks that commercial fleets may be the first adopters of their smart battery technology. “They’re being pushed towards going electric,” Palatov told me, “but when they buy an electric vehicle they have to choose the battery size together with the vehicle and sometimes they don’t even have a choice. If that battery is too large for the kinds of routes they’re going to run, then they’ve just overpaid for it and they’re using up their cargo capacity with battery weight that they don’t need.”
To me, Palatov’s modular, smart battery system makes a lot of sense. As a driver, I like the idea that I don’t necessarily need to carry hundreds of additional pounds worth of batteries every day, but not in terms of efficiency or safety. I want something that’s more enjoyable and, if I can use a Mazda MX-5 as an example, a lighter car is always more fun to drive.

Relative to today’s EV batteries, the economic and environmental advantages alone make Palatov’s Modbatt a no-brainer and I’d like to think the concept is rational enough to gain a foothold in electric vehicles of the near future. I just hope it’s not too rational for government regulators and carmakers.