Wrenchin’ Wednesday: Using angle iron like a metal LEGO brick
The goal of Wrenchin’ Wednesday is to outline methods that allow someone to build a project without a massive set of tools or expensive machines. Many of these tricks are all about taking advantage of an object’s features to save fabrication steps that would either consume more time or require more costly tools, such as a welder, to accomplish. We’ll get to some tricky bits with the high-voltage metal glue-gun soon, but for now, staying low-tech means utilizing stock material in creative ways.
Flat metal has an obvious weakness to bending along its thinnest section. By adding extra dimensions to it, you can easily increase the rigidity of that flat part. You see this all the time with gusseting and dimple dies, and it’s the fundamental reason that angle iron is shaped the way it is. With this in mind, it becomes easy to see how we can manipulate this stock material to make all sorts of parts on a project.
As I round out the turbo project on my 1996 Chevy Suburban K2500, one of the last areas to address in the quest for cooler intake-air temps was the factory intake elbow, a cast-aluminum part that directs air into the intake manifold after it’s been compressed by the turbo. As a well-known bottleneck, this elbow is an easy part to swap out and replace with a larger diameter pipe, but with my Suburban’s routine off-roading (and stiff suspension), I was worried that it would eventually tear apart the silicone couplers from vibration unless it had support, so once the pieces finally arrived, I cut out a quick bracket.
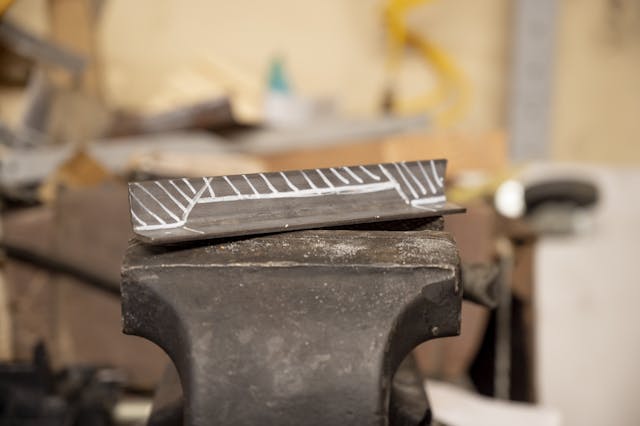

Take only what you don’t need, leave what you do. The diagonal sections clearly mark the areas that are getting chopped out, leaving behind a thin strip of the angle for our reinforced bracket.
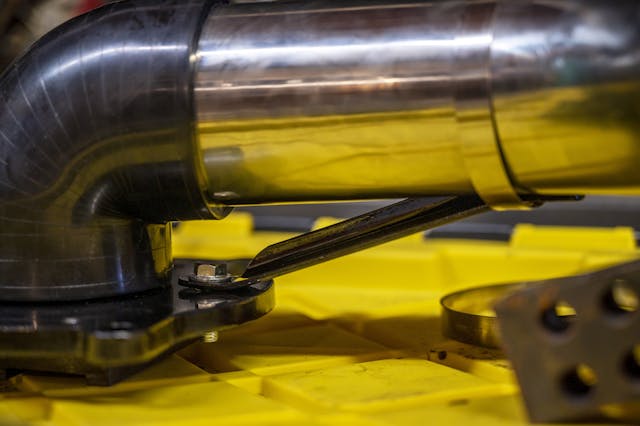
With the tabs bent and drilled, and a little appliance epoxy dusted onto the bracket, the support is finished in a half-hour. You could also build this out of flat stock, but adding the bend means more steps and thus more time. Of course, you could easily weld two strips together for the bracket, but that adds even more time to the project.
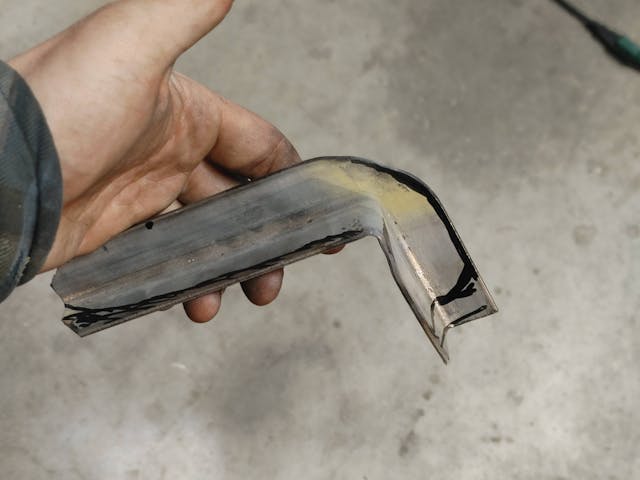

With a torch, it’s trivial to bend the angle iron while retaining the perpendicular face of the stock, a reinforcement which makes the wastegate strong enough to resist the constant spring pressure against it.
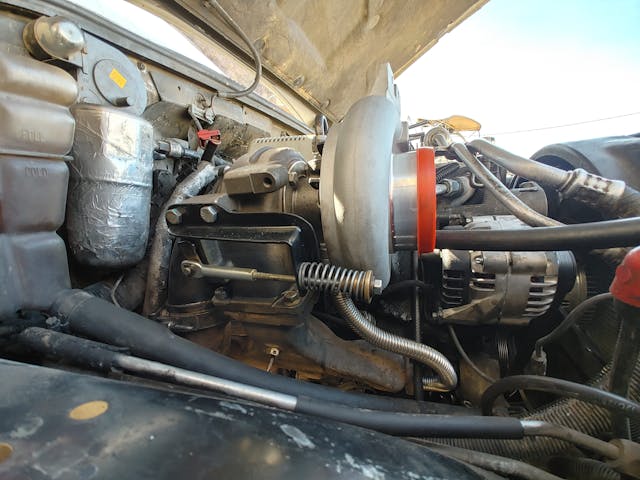
The options here are limitless—it’s just up to you to dream a solution. Don’t let the TV “pros” scare you away from custom projects; start bending these industrial LEGO bricks to your will.